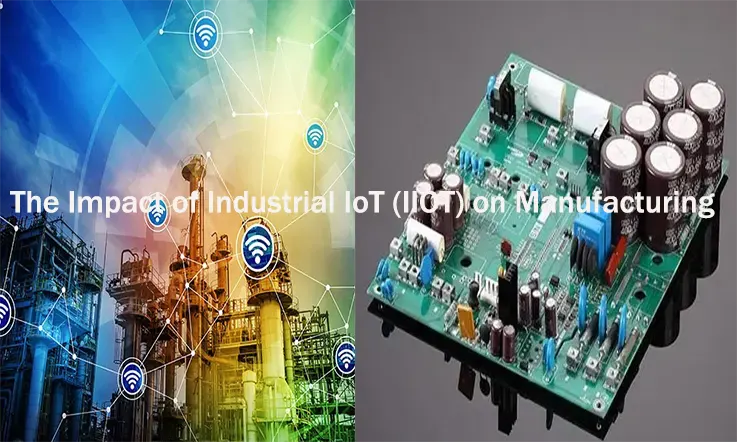
Industrial IoT (IIoT) is the use of interconnected devices and sensors in industrial settings to collect and analyze data, optimize processes, and improve efficiency. It offers benefits such as increased productivity, improved quality control, and enhanced worker safety. However, IIoT also presents challenges such as cybersecurity risks and data management. Overall, IIoT is transforming the industrial sector and enabling businesses to become more efficient, productive, and sustainable.
What is IIoT ?
The Industrial Internet of Things (IIoT) encompasses the integration of actuators and smart sensors within manufacturing processes, commonly referred to as Industry 4.0. This convergence leverages the capabilities of intelligent machines to provide advantages that traditional machines could not deliver in industrial settings over the years.
IIoT proponents assert that smart machines outperform humans in real-time data acquisition and analysis while effectively communicating crucial information for informed business decision-making.
Furthermore, actuators and connected sensors facilitate the identification and resolution of issues and inefficiencies, resulting in cost and time savings and supporting business intelligence initiatives. IIoT significantly contributes to manufacturing by unlocking potential gains in supply chain efficiency, quality control, and supply chain traceability, as well as enabling key processes such as asset tracking, predictive maintenance, and energy management.
Integration of machine learning, big data, and machine-to-machine (M2M) communication in IIoT fosters enhanced reliability and operational efficiency across industries and businesses. This encompasses the pervasive connectivity of physical devices and consumer devices.
The impact of IIoT is transformative, revolutionizing daily business operations. Its applications extend from detecting corrosion in refinery pipes to providing real-time data revealing untapped capacity in plants. Smart machines are instrumental in driving IIoT due to their real-time data capture, analysis capabilities, and rapid dissemination of findings.
IIoT finds extensive adoption across diverse sectors, including oil and gas, aviation, logistics, energy, manufacturing, and others. Its primary focus lies in optimizing operations, particularly through process automation.
Components of IIoT
Industrial IoT (IIoT) systems are composed of several components that work together to collect, transmit, analyze, and act on data. Here are some of the key components of IIoT:
Sensors and Actuators: These are devices that capture data from the physical world and convert it into digital signals that can be processed by computers. Sensors can measure various parameters such as temperature, pressure, vibration, and humidity, while actuators can control physical processes such as motors, valves, and switches.
Communication Networks: IIoT systems rely on various communication technologies to transmit data between devices and systems. These can include wired and wireless networks such as Ethernet, Wi-Fi, Bluetooth, and cellular networks.
Edge Computing: This is a computing model that processes data closer to the source of the data, rather than sending it to a centralized cloud server. Edge computing devices, such as gateways and routers, can perform data filtering, aggregation, and analysis, and can also take autonomous actions based on the data.
Cloud Computing: IIoT systems also use cloud-based services to store and process large volumes of data. Cloud platforms can provide scalability, flexibility, and advanced analytics capabilities to handle the massive amounts of data generated by IIoT devices.
Analytics and Machine Learning: IIoT systems generate vast amounts of data that need to be processed and analyzed to extract valuable insights. Analytics tools and machine learning algorithms can help identify patterns, anomalies, and trends in the data, and can also provide predictive and prescriptive insights for decision-making.
These components work together to create a comprehensive IIoT system that enables real-time monitoring, control, and optimization of industrial processes.
Benefit of IIoT
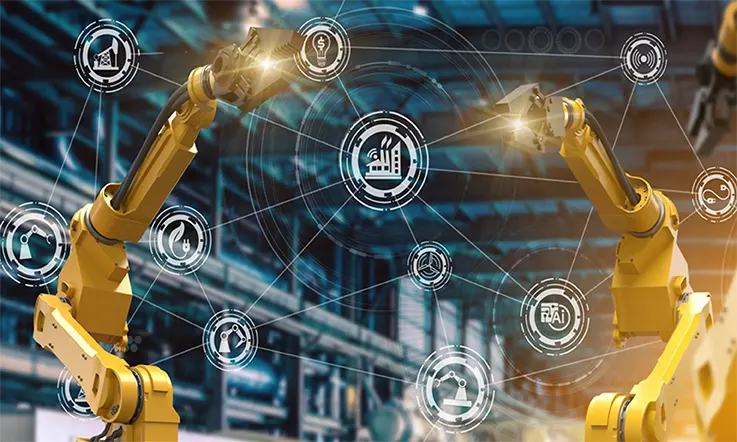
One of the prominent advantages of deploying IIoT devices in the manufacturing industry is their ability to enable predictive maintenance. Real-time data generated by IIoT systems allows organizations to anticipate when equipment will require servicing, enabling proactive maintenance to mitigate the risk of failures. This is particularly valuable in production lines, where machine failures can result in costly work stoppages. By addressing maintenance needs ahead of time, organizations can achieve improved operational efficiency.
Another benefit is the optimization of field service operations. IIoT technologies empower field service technicians to identify potential equipment issues before they escalate, enabling them to address problems proactively and prevent inconvenience for customers. These technologies can provide technicians with information about the required parts for a repair, ensuring they have the necessary equipment on hand during service calls.
Asset tracking is facilitated by IIoT, offering significant advantages throughout the supply chain. Suppliers, manufacturers, and customers can utilize asset management systems to track the location, status, and condition of products. Instant alerts are sent to stakeholders if goods are damaged or at risk, empowering them to take immediate or preventive action to mitigate the situation.
IIoT also contributes to enhanced customer satisfaction. When products are connected to the Internet of Things, manufacturers can collect and analyze data on customer product usage. This valuable information enables manufacturers and product designers to develop more customer-centric product roadmaps, resulting in improved customer experiences.
Furthermore, IIoT improves facility management by monitoring the factors that can impact the performance of manufacturing equipment. Sensors are employed to track vibrations, temperature, and other relevant parameters that may lead to suboptimal operating conditions. Identifying and addressing these factors promptly can optimize facility performance and prolong the lifespan of equipment.
Major considerations for adopting IIoT
When considering the adoption of IIoT (Industrial Internet of Things), several key factors should be taken into account:
Business Objectives: Clearly define the goals and targets that the organization aims to achieve through IIoT adoption. Identify specific areas where IIoT can bring value, such as improving operational efficiency, reducing costs, enhancing product quality, or enabling new revenue streams.
Infrastructure Readiness: Assess the existing infrastructure and determine if it can support the implementation of IIoT solutions. Consider factors such as network connectivity, scalability, data storage, and security. Evaluate whether upgrades or modifications are necessary to ensure seamless integration and optimal performance.
Data Governance and Security: Establish robust data governance and security protocols to protect sensitive information and ensure regulatory compliance. Implement measures to safeguard data confidentiality, integrity, and availability throughout the IIoT ecosystem, including devices, networks, and cloud platforms.
Interoperability and Standards: Consider interoperability requirements, as IIoT involves integrating various devices, systems, and technologies from different vendors or suppliers. Emphasize the adherence to industry standards and protocols to enable seamless data exchange and compatibility between different components of the IIoT ecosystem.
Scalability and Flexibility: Plan for future growth and scalability by selecting IIoT solutions that can accommodate increasing data volumes and expanding requirements. Ensure that the chosen technologies can adapt to evolving business needs and integrate with new devices or systems as the IIoT landscape evolves.
Return on Investment (ROI): Conduct a thorough cost-benefit analysis to assess the potential ROI of implementing IIoT solutions. Consider the upfront and ongoing costs, such as device procurement, installation, maintenance, and data management. Evaluate the potential benefits, such as improved operational efficiency, reduced downtime, enhanced product quality, and increased revenue.
Change Management: Recognize that IIoT implementation may require changes to existing processes, workflows, and organizational structures. Develop a change management plan that includes communication, training, and support for employees to ensure smooth adoption and alignment with the new IIoT-enabled operations.
Data Analytics and Insights: Determine how the collected data will be analyzed, interpreted, and turned into actionable insights. Explore advanced analytics techniques, such as machine learning and artificial intelligence, to derive meaningful insights from the raw IIoT data. Identify the key performance indicators (KPIs) and metrics that will drive decision-making and continuous improvement.
Vendor Selection: Evaluate different vendors and solution providers based on their expertise, experience, reliability, and support capabilities. Consider factors such as compatibility with existing systems, scalability, long-term partnership potential, and their ability to meet specific industry requirements.
Regulatory and Compliance Considerations: Stay abreast of relevant regulations and compliance requirements that impact IIoT implementation, especially regarding data privacy, security, and industry-specific regulations. Ensure that the chosen IIoT solutions align with these regulations and can support compliance efforts.
By thoroughly considering these factors, organizations can make informed decisions and successfully adopt IIoT solutions that align with their strategic objectives and deliver tangible benefits.
How does IIoT work ?
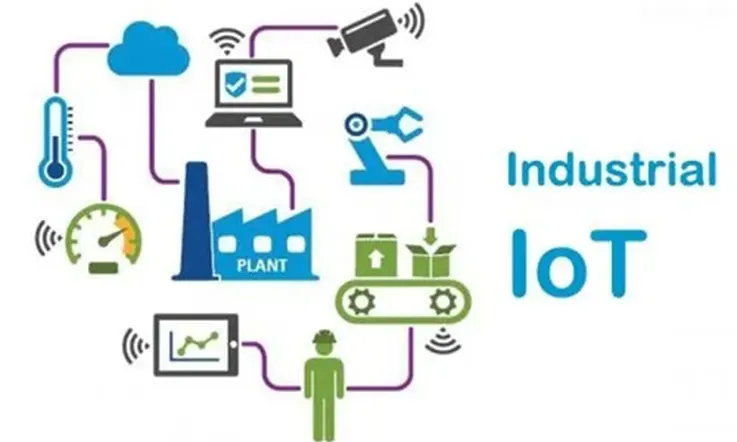
IIoT, as a subset of IoT, is revolutionizing how businesses establish connections, monitor operations, analyze data, and take action in the industrial sector, leading to cost reduction and enabling growth.
The term “industrial internet” was first coined by General Electric, one of the founding members of the Industry IoT Consortium.
IIoT leverages the data generated by traditional industrial devices over the years, which were previously considered “dumb.” Smart machines on assembly lines not only have the capability to capture and analyze data at higher speeds but also excel at communicating critical information, enabling faster and more precise decision-making.
The convergence of information technology (IT) and operational technology (OT) is the driving force behind IIoT. It involves a network matrix that connects devices and equipment, collects data through sensor technologies, analyzes it, and seamlessly integrates it into platform-as-a-service solutions. IIoT opens up new possibilities for industrial use cases, presenting significant opportunities for economic expansion.
IIoT efficiently gathers vast quantities of field data from the factory floor, transmits it through connection nodes, performs analysis on dedicated servers, and transforms the information into actionable insights on cloud platforms. This empowers businesses to make informed decisions tailored to their specific markets and target audiences. Essentially, IIoT establishes a system that interconnects edge devices such as actuators, sensors, controllers, connection switches, gateways, and industrial personal computers (IPC) with the cloud.
How is industrial IoT different from other types of IoT ?
Industrial IoT (IIoT) and other types of IoT share many similarities, but they also have some key differences.
The main difference between IIoT and other types of IoT is the context in which they are deployed. IIoT is focused on the use of IoT technologies in industrial settings, such as manufacturing, energy, transportation, and logistics. In contrast, other types of IoT are typically used in consumer or commercial settings, such as smart homes, wearables, and retail.
Another key difference is the scale and complexity of the systems involved. IIoT systems often involve large-scale deployments of sensors, devices, and equipment, and require sophisticated data analytics and machine learning algorithms to extract insights and optimize processes. These systems are typically highly integrated with existing industrial control systems and require a high degree of reliability and security.
Finally, IIoT systems often have different requirements for connectivity and data management than other types of IoT. For example, IIoT systems may require low-latency, high-bandwidth connections to support real-time control and monitoring of industrial processes. They may also require specialized data storage and analysis tools that are optimized for industrial data formats and protocols.
All in All, while IIoT and other types of IoT share many similarities, IIoT is focused on the use of IoT technologies in industrial settings, which requires a different set of tools, technologies, and approaches to connectivity, data management, and analytics.
How the IIoT powers digital transformation ?
Industrial IoT (IIoT) has a significant impact on digital transformation by enabling organizations to collect and analyze vast amounts of data from connected devices and systems. This data can then be used to optimize processes, increase efficiency, reduce costs, and create new business models.
Here are some of the ways in which IIoT powers digital transformation:
Real-time monitoring and control: IIoT allows organizations to monitor and control industrial processes in real-time. This enables them to identify and address issues as they happen, and make adjustments to optimize performance and improve efficiency.
Predictive maintenance: IIoT sensors can be used to monitor the condition of equipment and predict when maintenance is needed. This helps organizations to reduce downtime, extend the life of their equipment, and avoid costly repairs.
Data analytics: IIoT generates vast amounts of data that can be analyzed to identify patterns and insights that would be difficult to detect manually. This data can be used to optimize processes, reduce waste, and improve quality.
Supply chain optimization: IIoT sensors can be used to track goods and materials throughout the supply chain, enabling organizations to optimize logistics, reduce costs, and improve customer satisfaction.
New business models: IIoT can enable organizations to create new business models by offering new services or products that were previously not feasible. For example, manufacturers can use IIoT to offer predictive maintenance services to their customers, or to create new revenue streams by selling data insights to third parties.
In a words, IIoT powers digital transformation by enabling organizations to collect and analyze data from connected devices and systems, which can be used to optimize processes, reduce costs, and create new business models.
Risks and Challenges of Industrial IoT ?
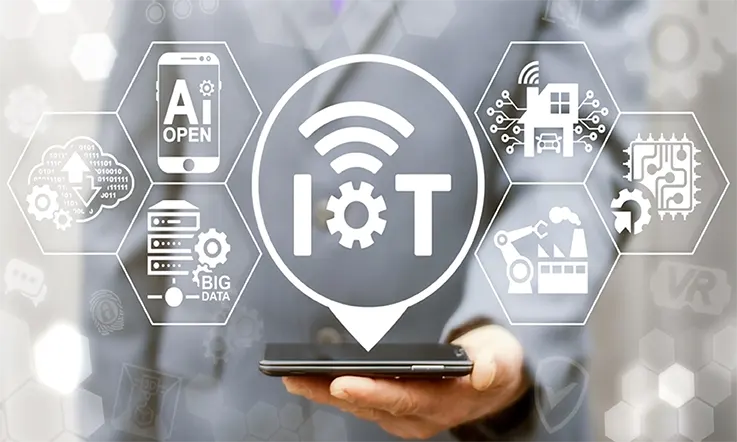
The Industrial Internet of Things (IIoT) has the potential to revolutionize the way we manufacture goods, manage supply chains, and operate industrial facilities. However, like any new technology, it also poses certain risks and challenges that need to be addressed for successful adoption and implementation. Here are some of the main risks and challenges associated with IIoT:
Security risks: One of the biggest concerns with IIoT is the security of industrial systems and data. As more devices are connected to the internet, there is a higher risk of cyber attacks and data breaches. IIoT devices and networks need to be properly secured to prevent unauthorized access, data theft, and other malicious activities.
Compatibility issues: IIoT involves integrating different devices and systems from different vendors, which can lead to compatibility issues and interoperability problems. This can make it difficult to integrate new IIoT devices into existing systems, and can limit the ability to share data across devices and systems.
Complexity and cost: Implementing IIoT can be complex and expensive, as it involves integrating hardware, software, and networking technologies. It can also require significant investments in infrastructure and training. This can be a barrier to adoption for many organizations.
Data management and analysis: IIoT generates vast amounts of data, which can be overwhelming for organizations to manage and analyze. To fully realize the benefits of IIoT, companies need to be able to effectively collect, store, and analyze data in real-time.
Privacy concerns: IIoT can collect sensitive information about employees, customers, and operations. Companies need to be transparent about the data they collect, and implement policies and procedures to protect the privacy of individuals and comply with legal and regulatory requirements.
Maintenance and downtime: IIoT devices require maintenance and updates, which can cause downtime and disruptions to industrial processes. It is important to have robust maintenance and support procedures in place to minimize downtime and ensure that IIoT devices are functioning correctly.
Overall, IIoT presents both opportunities and challenges for organizations. By addressing these risks and challenges, companies can successfully implement IIoT and reap the benefits of improved efficiency, productivity, and competitiveness.
How Can Businesses Secure Industrial Internet of Things (IIoT) ?
Securing Industrial Internet of Things (IIoT) is critical for businesses to protect their assets, data, and operations from cyber threats. Here are some best practices businesses can follow to secure their IIoT networks:
Conduct a risk assessment: Businesses should conduct a thorough risk assessment to identify potential vulnerabilities and threats in the IIoT network. This will help businesses to prioritize their security efforts and allocate resources effectively.
Implement physical security measures: IIoT devices should be physically secured to prevent unauthorized access. This may include measures such as secure enclosures, locks, and access control systems.
Use strong authentication and access controls: Businesses should implement strong authentication and access controls to ensure that only authorized users and devices can access the IIoT network. This may include measures such as multi-factor authentication, role-based access control, and password policies.
Encrypt data in transit and at rest: IIoT devices should use encryption to protect data both in transit and at rest. This will prevent unauthorized access and ensure that data cannot be intercepted or tampered with.
Monitor the network for threats: Businesses should implement monitoring and alerting systems to detect and respond to potential threats in real-time. This may include intrusion detection and prevention systems, security information and event management (SIEM) systems, and threat intelligence feeds.
Update software and firmware regularly: Businesses should ensure that IIoT devices are running the latest software and firmware versions to ensure that any known vulnerabilities are patched.
Train employees on security best practices: Employees should be trained on security best practices, including how to identify and report potential security threats and how to use IIoT devices securely.
By following these best practices, businesses can improve the security of their IIoT networks and reduce the risk of cyber threats. It is important to note that IIoT security is an ongoing process, and businesses should regularly review and update their security measures to stay ahead of emerging threats.
Future of IIoT
The future of IIoT looks promising as more and more industries are embracing the technology to improve their operations and gain a competitive advantage. Some potential developments and trends in the future of IIoT include:

Edge Computing: The use of edge computing, which involves processing data closer to the source, is expected to increase in IIoT applications. This can help reduce latency and improve real-time decision-making.
5G Networks: The rollout of 5G networks is expected to facilitate faster and more reliable communication between IIoT devices, leading to increased efficiency and productivity.
Artificial Intelligence and Machine Learning: The use of AI and machine learning in IIoT applications is expected to increase, enabling better predictive maintenance, quality control, and supply chain management.
Increased Security Measures: With the increasing number of connected devices, IIoT security measures will need to be strengthened to prevent cyber attacks and ensure data privacy.
Integration with Legacy Systems: As more companies adopt IIoT, integration with legacy systems will become more important. This will require the development of standardized protocols and interfaces to enable seamless communication between different systems.
As a result, the future of IIoT is likely to be characterized by greater connectivity, increased automation, and more intelligent decision-making based on real-time data analysis.
Conclusion
The Industrial Internet of Things (IIoT) is revolutionizing the manufacturing industry by enabling real-time visibility, control, and optimization of industrial processes. IIoT systems comprise various components, including sensors, actuators, communication networks, edge and cloud computing, and analytics and machine learning. These systems have numerous applications in areas such as predictive maintenance, quality control, supply chain management, asset tracking, and energy management. Implementing IIoT brings substantial benefits, including improved efficiency, cost reduction, enhanced safety, increased productivity, and better decision-making.
IIoT plays a crucial role in shaping the manufacturing process and driving digital transformation across industries. Its systems ensure the safe and secure handling of industrial data, contributing to improved customer satisfaction. Integrating internet-connected devices into production processes facilitates faster and easier data acquisition.
However, IIoT also faces challenges, such as cybersecurity risks, interoperability issues, data privacy concerns, legacy system integration, and a scarcity of skilled workers. As technology advances and new use cases emerge, IIoT is expected to assume an increasingly significant role in the manufacturing industry, presenting opportunities for innovation and growth.
We are currently experiencing the fourth industrial revolution, commonly known as Industry 4.0. Its focus lies in integrating connected devices, particularly those of IIoT, into industrial operations. IIoT devices will have a substantial impact on digital transformations as companies strive to digitize their supply chains and production lines. By leveraging IIoT, businesses can achieve maximum efficiency by increasing productivity.