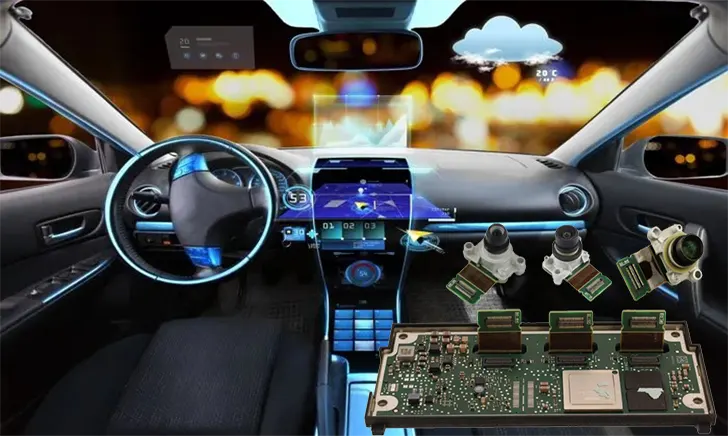
At JarnisTech, we bring a wealth of experience in crafting automotive PCBs. Our commitment to high-quality manufacturing ensures that you receive reliable products designed to stand the test of time. With ISO 9001:2008 and UL certifications under our belt, we’ve got the credentials that matter. From manufacturing to assembly, you’ll find everything you need right here in one convenient place.
We take pride in delivering exceptional products tailored to our customers’ needs. If you’ve got a design in mind, don’t hesitate to reach out! Send your specs and automotive PCB details to [email protected], and we’ll get you a free quote along with top-tier engineering services. Let’s make your next project a reality!
Automotive PCBs serve as the backbone of today’s vehicle electronics, powering everything from safety systems to infotainment features. As technology progresses, so does the demand for more advanced automotive PCBs. This article dives deep into the nitty-gritty of automotive PCB design, manufacturing, and assembly, offering a thorough guide for electronics manufacturers, OEMs, and engineers in the automotive sector.
Introduction to Automotive PCBs
Automotive Printed Circuit Boards (PCBs) form the backbone of modern vehicle electronics. They act as the wiring structure, connecting and supporting electronic components that range from basic lighting systems to advanced features like infotainment units and safety-critical systems, such as Advanced Driver Assistance Systems (ADAS) and electric vehicle (EV) battery management. Automotive PCBs aren’t just slapped together; they need to handle some seriously harsh environments, like temperature extremes, humidity, and continuous mechanical stress—all while providing consistent performance. If you’re in the auto game, whether as an OEM or in electronics manufacturing, understanding these boards is key to staying ahead in the race.
When we talk about Automotive PCB design, it’s not just about slapping components on a board. Engineers have to take heat dissipation, signal integrity, and the effects of mechanical vibrations into account. These aren’t your everyday electronics. Failures here can lead to massive recalls, not to mention safety risks.
Let’s break down a bit more: Automotive PCB manufacturing involves highly specialized processes and materials. You’re looking at high-temperature laminate materials like FR-4, and sometimes the stakes get higher with high-TG options to handle extreme conditions. Throw in heavy copper for better current handling, and you start seeing why the manufacturing side isn’t just about volume—it’s about doing it right.
The final piece? Automotive PCB assembly. This step involves placing the right components in exactly the right spot, but it also requires precision soldering techniques that stand up to vibrations and long-term wear. All this while ensuring a quick turnaround, because in this industry, timelines can make or break your success.
Automotive PCB Features & Specifications
Feature | Description |
High TG materials | Materials that provide stability under high temperatures, often exceeding 170°C. Necessary for powertrain and under-the-hood applications. |
Heavy copper | Increased copper thickness for greater current-carrying capacity. Commonly found in battery management systems and power electronics. |
Multiple layers | Multi-layered PCBs are used for more complex automotive applications, improving functionality without taking up much space. |
EMC Shielding | Essential for maintaining signal integrity in high-frequency automotive applications like radar sensors. |
Thermal Management | Methods such as heatsinks or thermal vias help dissipate heat effectively, preventing overheating in critical automotive systems. |
As we dive deeper, you’ll see how designing, manufacturing, and assembling PCBs isn’t just about hitting specs—it’s about ensuring safety, performance, and reliability in an industry that doesn’t allow for slip-ups.
Overview of Automotive PCB Design
Understanding Automotive PCB Design
When it comes to automotive electronics, PCBs form the foundation of just about every system inside a modern vehicle. These boards power everything from the infotainment setups that keep drivers on track, to the engine control units that regulate performance under the hood. But don’t be fooled—designing automotive PCBs isn’t just about linking parts together. It’s an intricate process that demands pinpoint accuracy and serious engineering know-how. Every trace, layer, and component placement on that board can make or break the functionality of advanced safety systems, power distribution, and overall vehicle efficiency. Whether it’s dealing with high temperatures, harsh vibrations, or electromagnetic interference, these boards need to hold up under some pretty tough conditions.
Automotive PCBs aren’t just another circuit—they’re built to handle the rigors of the road. Engineers working on these boards are navigating a minefield of compliance regulations and thermal management concerns. You’ve got to hit the right balance between miniaturization and durability, all while making sure the design can handle the crazy heat and electrical stress under a vehicle’s hood. No shortcuts here—everything’s got to be on point.
So, next time you’re in your car adjusting the climate control or setting up your favorite playlist, remember there’s a whole team of engineers who’ve poured their expertise into that tiny but mighty PCB. Ready to up your game in the automotive PCB industry? Make sure you’ve got the right team, tools, and expertise to keep those wheels turning smoothly.
Design Calculations and Considerations
Let’s break this down: PCB design requires hitting some pretty exact numbers if you want things to work under the hood.
Trace Width Calculation: Ever tried stuffing a turkey on Thanksgiving? You can’t overdo it, or it’ll explode. Same deal with PCB traces—they need to be just the right width to handle the current load. The industry standard for figuring this out is IPC-2221, which helps designers calculate how wide a trace needs to be to safely carry current without overheating.
Impedance Control: If you’re working with high-frequency signals—like those needed for Advanced Driver Assistance Systems (ADAS)—you better make sure the impedance is on point. Any little hiccup in impedance can mess with your signal. Using simulation tools like HyperLynx or SiSoft during design ensures you don’t drop the ball when it comes to signal integrity.
Check out this table to break down the design factors:
Design Factor | Importance | Tool/Standard |
Trace Width | Prevents overheating | IPC-2221 |
Impedance Control | Maintains signal integrity | HyperLynx, SiSoft |
Thermal Management | Avoids heat-related failures | Ansys, COMSOL |
Automotive PCB Design Principles
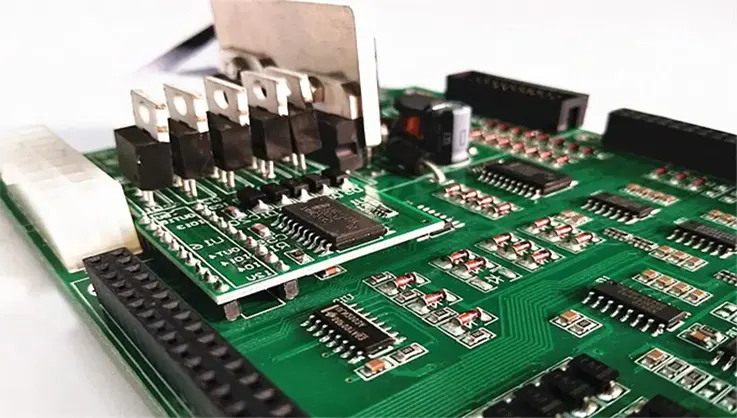
Designing for Performance
In the automotive sector, signal integrity is at the forefront of PCB design. As vehicles evolve with cutting-edge technologies, the need for high-speed data transfer skyrockets. Any signal degradation can throw a wrench in system performance, particularly in advanced driver-assistance systems (ADAS) and infotainment setups. Designers need to focus intently on aspects like trace width, spacing, and routing to ensure that signals remain clear over longer distances. Employing methods such as differential signaling and controlled impedance is common to bolster signal integrity.
Another key aspect is designing for electromagnetic compatibility (EMC). As vehicles integrate more electronic components, ensuring that these systems do not interfere with each other becomes increasingly important. Effective EMC design involves strategic placement of components, appropriate shielding, and the use of filtering techniques to minimize emissions. By considering these factors early in the design process, engineers can create PCBs that operate reliably in the electromagnetic environment of modern vehicles.
Advanced Design Techniques
In automotive electronics, multi-layer PCB designs have gained traction as a smart choice for enhancing performance. These setups enable a higher component density while keeping a compact footprint, which is a must in the tight quarters of modern vehicles. By stacking layers, engineers can efficiently route power and ground planes, cutting down on electromagnetic interference and boosting signal clarity.
The utilization of high-frequency materials is another advanced technique making waves in automotive PCB design. With the rise of technologies such as radar and LiDAR, PCBs need to handle higher frequencies without compromising performance. Materials like PTFE (polytetrafluoroethylene) and other low-loss substrates help minimize signal loss at high frequencies, ensuring robust communication between various vehicle systems.
Key Design Considerations
Design Aspect | Considerations |
Signal Integrity | Trace width, spacing, differential signaling, controlled impedance |
Electromagnetic Compatibility | Component placement, shielding, filtering techniques |
Multi-layer Designs | Layer stacking, power/gnd plane routing, thermal management |
High-frequency Materials | Low-loss substrates, PTFE usage, frequency response |
Embracing these design principles and techniques not only boosts the performance of automotive PCBs but also ensures they meet the evolving demands of the automotive industry. Whether you’re working on a new vehicle model or retrofitting an existing one, keeping these guidelines in mind will help you stay ahead of the curve.
Automotive PCB Manufacturing: Taking It from Design to Reality
When you’re building PCBs for cars, you’re working with precision parts that need to withstand everything from scorching engine heat to bone-rattling vibrations. It’s not just about slapping a circuit on a board—it’s about creating a durable, long-lasting foundation for the tech that drives our cars, from ADAS to engine control units. The manufacturing process here is on a whole different level, so buckle up as we dive into the nitty-gritty.
Material Selection for Automotive PCBs
When it comes to selecting materials for PCBs, it’s all about ensuring durability. Your PCB needs to withstand extreme temperatures, relentless road vibrations, and even the occasional splash of water. Here’s a quick overview of materials that make the cut for automotive applications:
FR-4 Variants: Your good ol’ trusty FR-4 is a solid choice, but for automotive, you need a high-temp version. Why? Because the last thing you want is your circuit warping under engine heat.
Polyimide: This is where flexibility comes in. For systems that need a bit of bend—think dashboard wiring or seat sensors—polyimide is your go-to. It can take a beating and still keep the current flowing.
Types of Automotive PCBs
In the automotive world, one PCB definitely doesn’t fit all. Depending on where and how it’s used, you’ll find different types of PCBs, each with its own strengths:
Rigid PCBs: These are the dependable, workhorse PCBs you’ll find in high-power systems like the engine control unit (ECU) or alternators. They’re sturdy and can handle high currents without flinching.
Flexible PCBs: Flex circuits, on the other hand, are like the Swiss Army knives of the PCB world. Need a circuit to squeeze into a tight spot? These are your answer. Think about areas like door locks, sensors, or even seat controls, where space is tight but reliability is still critical.
Rigid-Flex PCBs: Sometimes you need a mix of both—a board that’s strong in some areas but flexible in others. Rigid-flex PCBs get used in systems where you need components spread out over different areas, like airbags or modern entertainment systems.
High-TG boards refer to PCBs made from materials with a high glass transition temperature. These materials can withstand higher thermal stress without losing their structural integrity. In automotive applications, where components can experience significant temperature fluctuations, high-TG boards are often preferred for their reliability. They are particularly effective in areas like power electronics and LED lighting, where heat dissipation is a concern.
Heavy copper boards are another specialty within the automotive sector. These boards incorporate thicker copper layers, typically greater than 3 ounces per square foot, which is crucial for applications requiring high current carrying capacity. Heavy copper PCBs are frequently used in power distribution, electric vehicle (EV) battery management systems, and motor control circuits. The additional copper not only helps manage heat more effectively but also contributes to improved conductivity, ensuring that power flows smoothly through the system.
●Comparison of PCB Types
PCB Type | Advantages | Common Applications |
Rigid PCBs | Durability, thermal stability | Engine controls, safety systems |
Flexible PCBs | Lightweight, space-saving, 3D configurations | Sensor assemblies, displays |
High-TG Boards | Higher thermal resistance, reliable performance | Power electronics, LED lighting |
Heavy Copper Boards | Enhanced current capacity, improved heat management | Power distribution, EV battery systems |
PCB Fabrication Process: Where It All Begins
The first steps of automotive PCB manufacturing are a lot like building a house. You’ve got to start with a solid foundation—here’s how it all gets rolling.
Material Preparation: Think of this as the base layer of your cake. Choosing the right substrate—whether it’s FR-4 for general use or polyimide for those flexible circuits—sets the stage for everything else. The material is prepped according to the specs and needs of the car’s electronics. For high-power EV systems, you’d go for heavy copper PCBs to handle the power load.
Layering and Etching: Here’s where the magic happens. You take multiple layers and laminate them together. Then, through a process called etching, the circuit pathways are carefully carved out, sort of like chiseling a path for electricity to flow through.
Drilling and Plating: Once the layers are done, it’s time to drill those vias (holes) where components like capacitors and resistors will live. After the drilling, the holes are plated with copper to ensure smooth electrical conductivity between layers. Think of it as adding doorways in your multi-story house.
Fabrication Step | Description | Purpose |
Material Preparation | Substrate selection and treatment | Ensures the right base for the application |
Layering & Etching | Laminating and etching circuit paths | Creates the circuit design on the board |
Drilling & Plating | Drilling and copper-plating holes for component insertion | Enables interconnectivity across layers |
Quality Control: Keeping It Tight
No cutting corners here—quality control in the auto world is like getting an inspection sticker before you hit the highway. If a PCB fails under the hood, it could lead to some serious problems, so manufacturers use the most advanced tech to make sure every board meets the standards.
Automated Optical Inspection (AOI): Imagine having a high-tech scanner that combs through every inch of the PCB, looking for the tiniest defect in the circuit patterns. AOI does just that. This is like having a pair of eagle eyes to catch any issues before the assembly stage, ensuring that what goes into your car works flawlessly.
Functional Testing: This is the big test. Once the board is built, manufacturers run it through a series of functional tests to make sure it can handle whatever gets thrown at it—whether that’s managing the power system of an electric car or helping to guide the autonomous driving sensors. If it can’t hack it in testing, it won’t make it to your dashboard.
Advanced Manufacturing Technologies: Welcome to the Future
These days, PCB manufacturing is getting a major facelift, thanks to cutting-edge tech that’s changing the way we think about production.
Additive Manufacturing: We’re talking 3D printing for PCBs. Instead of traditional subtractive methods (removing material), this tech builds the circuit from the ground up, layer by layer. It’s especially useful for rapid prototyping and custom designs. Got a crazy new idea for a compact automotive sensor? 3D printing might just be the way to bring it to life faster than you can say “ignition.”
Smart Manufacturing: With IoT integration, manufacturers are bringing intelligence into their production lines. Think of it like having smart sensors embedded in every step of the manufacturing process, so any issue gets flagged in real-time. This system can monitor temperature, pressure, and even the quality of the materials being used, all without missing a beat.
Automotive PCB Assembly: Getting Down to the Nuts and Bolts
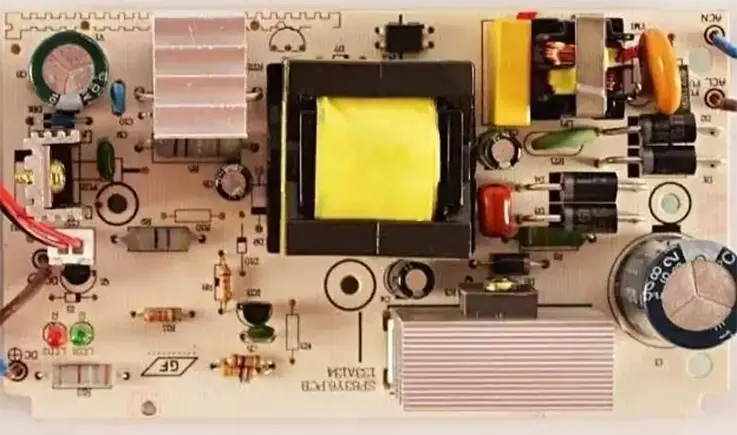
When it comes to automotive PCB assembly, you’re talking about techniques that can handle the wear and tear of rough roads, high heat, and extreme vibration. It’s not just about piecing parts together—it’s about making sure those connections stay strong, no matter how tough the ride gets.
Assembly Techniques: Two Ways to Make it Stick
PCB assembly in the automotive world demands reliability, efficiency, and longevity. Let’s break down the two primary techniques used in this process, each serving different purposes:
Surface Mount Technology (SMT): This method is the workhorse of PCB assembly, especially in the automotive sector. It’s all about efficiency—components are mounted directly onto the surface of the PCB, making the design compact and saving space. In applications like adaptive cruise control or advanced driver-assistance systems (ADAS), where size matters, SMT gets the job done. Plus, automated machines handle most of the work, speeding up production while maintaining precision.
Through-Hole Technology (THT): For those moments when durability is non-negotiable, Through-Hole Technology (THT) is the way to go. This technique involves inserting components through pre-drilled holes and soldering them on the opposite side, creating robust mechanical bonds. In automotive applications, where PCBs face mechanical stress and high-power loads, this method shines. Think about parts like connectors and large capacitors that must endure the bumps and vibrations of the road. THT ensures these components stay secure and reliable, ready to perform no matter the conditions.
Assembly Technique | Description | Ideal Application |
Surface Mount Technology | Mounts components directly on the PCB surface; fast and compact | Compact systems like ADAS or infotainment |
Through-Hole Technology | Components go through holes and are soldered for stronger connections | High-power or mechanically stressed components |
Reliability Testing for Automotive PCBs: Testing Like a Pro
In automotive applications, reliability isn’t negotiable. You wouldn’t want your dashboard to glitch out during a long road trip, or worse—an engine control failure. That’s why reliability testing is a huge part of the assembly process, with manufacturers pushing their PCBs to the limit to ensure they can take the heat (literally) and still perform.
Thermal Cycling Tests: Cars operate in wildly varying environments, from freezing temperatures in the mountains to the heat of desert highways. To make sure automotive PCBs can handle these extremes, they’re subjected to thermal cycling tests, where they are repeatedly exposed to drastic temperature changes. This process ensures the PCB won’t warp, crack, or short out when temperatures swing from one extreme to the other.
Vibration Testing: Imagine your car’s circuit board constantly being shaken by potholes, speed bumps, and uneven terrain. Now, multiply that stress over years of driving. Vibration testing is designed to simulate this kind of wear and tear, ensuring that all connections remain solid and the PCB continues to function without failure.
Case Study: Real-World Application—Electric Vehicle Battery Management System (BMS)
Let’s look at how a leading EV manufacturer tackled the challenge of improving the performance of its battery management system (BMS). The BMS is like the brains behind the battery—it monitors temperature, voltage, and current to ensure the car’s battery operates efficiently and safely. To keep things cool under pressure, they turned to high-TG (glass transition temperature) materials and advanced thermal management techniques. These materials withstand the high temperatures associated with charging and discharging the battery, helping reduce the risk of thermal runaway (a chain reaction that can lead to fires in extreme cases).
This move didn’t just boost safety—it also cranked up the overall efficiency of the EV, allowing for longer driving ranges without overheating concerns. Now, that’s what we call future-proofing your ride!
Why So Importance of IATF 16949 in Automotive PCB Manufacturing and Assembly?
When it comes to automotive PCB manufacturing and assembly, adhering to IATF 16949 standards can make a world of difference. This international standard focuses on quality management systems specifically tailored for the automotive sector, ensuring that manufacturers meet stringent requirements for quality and reliability.
Key Benefits of IATF 16949 in Automotive PCBs
Enhanced Quality Assurance: By implementing IATF 16949, companies can establish robust quality management processes. This leads to fewer defects and higher reliability in PCBs, which is critical for automotive applications where performance is non-negotiable.
Improved Customer Satisfaction: Meeting IATF standards signals to customers that your organization is committed to quality. This trust can lead to long-term partnerships and repeat business. For example, a manufacturer that consistently delivers defect-free products is likely to gain favor with major automotive OEMs.
Streamlined Processes: The framework encourages continuous improvement and efficient processes. Companies often see reduced waste and better resource management, which not only saves money but also supports sustainability efforts.
Risk Management: IATF 16949 promotes identifying and mitigating risks throughout the production process. This proactive approach can prevent costly recalls and safety issues, safeguarding both manufacturers and consumers.
Example of Implementation:
Consider a PCB manufacturer that recently adopted IATF 16949. Before the transition, they faced high defect rates and customer complaints. After implementing the standard, they reduced defects by 30% in the first year. This not only improved their reputation but also led to a significant increase in orders from automotive clients seeking reliability in their suppliers.
Aspect | Before IATF 16949 | After IATF 16949 | Improvement |
Defect Rate | 15% | 10.5% | 30% Reduction |
Customer Complaints | 50 per month | 25 per month | 50% Reduction |
Order Volume | 100 units | 150 units | 50% Increase |
Implementing IATF 16949 in your automotive PCB manufacturing process is more than just a compliance checklist; it’s about building a culture of quality that resonates with customers and sets you apart in a competitive landscape. Ready to take the leap? Please contact us today, let’s talk with your automotive PCB project detail!
Challenges in Automotive PCB Design and Manufacturing
Addressing Supply Chain Issues
In the automotive PCB sector, supply chain disruptions can significantly impact production timelines and overall project viability. The pandemic and geopolitical tensions have underscored vulnerabilities in sourcing materials and components.
●Managing Supply Chain Risks in PCB Production:
To tackle these challenges, companies need to develop robust supply chain management strategies. This includes:
Diversifying Suppliers: Engaging multiple suppliers across different regions can mitigate the risk of delays. For example, if one supplier faces production issues, others can step in to fulfill orders.
Establishing Strong Relationships: Building solid relationships with suppliers ensures that manufacturers receive priority in supply allocation during shortages.
Implementing Inventory Management Solutions: Companies can adopt just-in-time inventory systems, balancing the need for materials without overstocking, which can lead to increased costs.
Strategies for Sourcing Reliable Materials
Finding top-notch materials is key to ensuring the performance and reliability of automotive PCBs. When you choose the right components, you’re not just filling a spec; you’re building a foundation that can withstand the rigors of the road. Quality materials help prevent failures and extend the life of your boards, making them a smart investment for any automotive application.
Strategy | Description |
Material Certification | Ensuring that materials meet industry standards such as ISO and UL certifications is crucial for reliability. |
Local Sourcing | Sourcing materials from local suppliers to reduce transportation costs and lead times, enhancing flexibility in production. |
Supplier Audits | Regular audits help manufacturers ensure compliance with quality standards and identify potential issues before they escalate. |
Compliance with Industry Standards
Adhering to industry standards is not just about legal compliance; it’s also about ensuring product safety and reliability.
●Overview of Automotive Industry Regulations:
Automotive electronics must comply with various regulations that govern design and manufacturing practices. Key standards include:
ISO 26262: Focuses on functional safety in automotive systems to prevent faults that could compromise safety-critical functions.
RoHS Compliance: Restricts the use of specific hazardous materials in electronic components, ensuring environmentally friendly practices.
●Ensuring Adherence to Environmental and Safety Standards:
Manufacturers should:
Stay Updated on Regulations: Regularly review and update processes to align with evolving standards. Engaging with regulatory bodies can provide insights into upcoming changes.
Training and Awareness: Conduct training sessions for staff on compliance requirements ensures that everyone involved in the design and manufacturing process understands their responsibilities.
Compliance Strategy | Description |
Regular Updates | Regularly review and update processes to stay aligned with evolving regulations. |
Staff Training | Conduct training sessions for staff on compliance requirements to ensure understanding of responsibilities. |
Automotive PCB Performance Requirements: What’s Under the Hood?
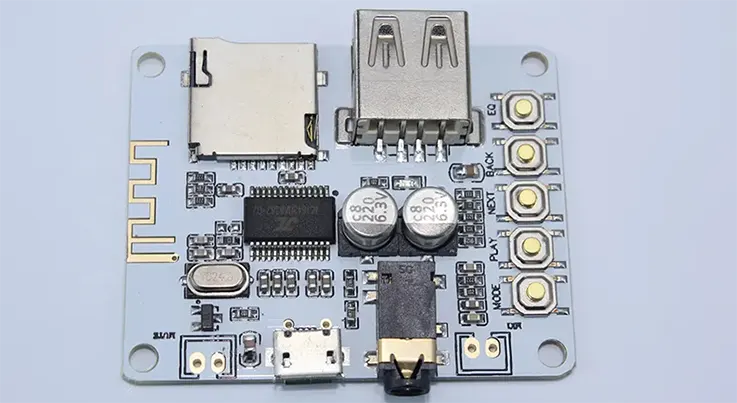
When it comes to automotive PCBs, the performance bar is set high. These PCBs are tasked with handling rugged conditions like high heat, vibration, and electrical loads in everything from EV power systems to advanced infotainment. If you’re going to keep these PCBs firing on all cylinders, you’ll need to stay laser-focused on two big areas: signal integrity and thermal management. Let’s break these down.
Key Performance Metrics: No Room for Error
●Signal Integrity
Signal integrity is the name of the game when it comes to high-speed data transmission in modern automotive systems. Whether it’s radar, ADAS, or infotainment systems, the data must be clean and reliable. Any noise or signal degradation can lead to serious performance issues.
Real-world example: Imagine a radar system in a self-driving car misreading its environment due to poor signal integrity—definitely not a situation you want on the highway.
Solutions: To maintain signal integrity, designers often work with controlled impedance and shielded PCB layers. Plus, using advanced materials that minimize dielectric losses keeps the data streams tight.
●Thermal Management
Heat is the enemy, especially in automotive environments. From the engine control unit (ECU) to the battery management system (BMS) in EVs, PCBs are put to the test in terms of heat tolerance. Without effective heat dissipation, components can fail, leading to major problems.
How it’s handled: Designers use materials with excellent thermal conductivity, such as ceramic-filled pre-preg or thermal vias. Heat sinks and thermal pads also play a big role, preventing hotspots and ensuring a long life for the components.
Practical Example: A PCB in an electric vehicle’s inverter might use heavy copper layers and thermal vias to direct heat away from critical components, ensuring it stays within safe operating temperatures even during fast acceleration.
Performance Metric | Description | Techniques Used |
Signal Integrity | Ensuring clear, high-quality data transmission | Impedance control, low-loss materials, shielding |
Thermal Management | Effective heat dissipation to prevent failure | Heavy copper, thermal vias, heat sinks |
Why Automotive PCBs Lean on High TG and Heavy Copper Materials?
In today’s automotive landscape, where cars are more like computers on wheels, the choice of materials for PCBs is absolutely no joke. Two standout features are high TG materials and heavy copper. Here’s why:
●High TG (Glass Transition Temperature)
High TG materials offer increased thermal stability. They’re the workhorses of the automotive PCB world, keeping everything together when temperatures start to soar. Automotive environments—think engine compartments or high-power applications—often subject PCBs to temperatures that would have ordinary materials warping, delaminating, or straight-up frying the board.
Example: A high-TG laminate in a power control module ensures that the board doesn’t buckle under high operational temperatures, providing consistent performance even when things heat up.
●Heavy Copper
Heavy copper layers beef up a PCB’s current-carrying capacity. These are particularly useful in high-power applications like EVs and hybrid vehicles, where managing large currents is part of the daily grind. Heavy copper not only carries more current but also spreads the heat more effectively, reducing stress on individual components.
Example: In an electric vehicle’s charging system, heavy copper traces allow for fast charging without overheating, enabling both durability and safety over the long haul.
Material | Benefit | Use Case |
High TG Materials | Offers stability at higher temperatures | Engine control units, power management systems |
Heavy Copper | Enhances current capacity and heat dissipation | Electric vehicle charging systems, power converters |
Current Trends and Innovations in Automotive PCB Technology
As the automotive industry speeds toward electrification, self-driving systems, and IoT integration, automotive PCB technology is evolving at breakneck speed. Let’s explore some of the cutting-edge trends driving this shift.
Advancements in Materials: A New Age for PCB Manufacturing
The growing focus on electric vehicles (EVs) and autonomous cars has amped up the need for materials that can handle more power, higher temperatures, and offer better sustainability. Here are some advancements making waves:
●Bio-based Substrates
There’s a push for environmentally friendly materials in PCB manufacturing, and bio-based substrates are leading that charge. These substrates use renewable resources, reducing reliance on traditional petrochemicals. They’re perfect for companies aiming to improve their green footprint without sacrificing performance.
Example: Companies working on sustainability initiatives in their PCB production are using bio-based materials like polylactic acid (PLA) for their substrates, reducing carbon emissions and waste.
●Thermally Conductive Polymers
As electric vehicles (EVs) ramp up their power demands, managing heat becomes a major concern. That’s where thermally conductive polymers step in. These materials excel at dissipating heat efficiently while keeping weight to a minimum—a major win for automotive applications where both thermal management and fuel efficiency are on the line.
Case in Point: High-performance EV manufacturers have already begun integrating thermally conductive materials in battery management systems (BMS) to ensure long-term reliability and prevent overheating during fast-charging scenarios.
Material Innovation | Benefit | Application |
Bio-based Substrates | Eco-friendly, sustainable | Green manufacturing initiatives |
Thermally Conductive Polymers | Efficient heat dissipation | Battery management, high-power electronics |
The Role of AI and Machine Learning: Smarter Design and Production
Incorporating artificial intelligence (AI) and machine learning (ML) into PCB design and manufacturing is no longer just a trend—it’s transforming the industry. Here’s how:
●AI-Driven Predictive Maintenance
AI systems can now anticipate potential PCB failures before they happen. With predictive analytics, manufacturers can monitor equipment in real-time, catching problems early and reducing costly downtime. This is especially handy in automotive electronics, where reliability isn’t just appreciated—it’s expected.
Practical Example: A manufacturer using AI to track solder joint wear-and-tear can schedule preventive maintenance on their machinery, dodging production halts and saving big on repair costs.
●Quality Control Powered by Machine Learning
ML algorithms are now being used to enhance quality control processes. These systems can detect even the tiniest flaws during PCB fabrication, which might otherwise slip through human inspections. ML-based systems “learn” over time, improving accuracy and driving efficiency.
Example: A PCB factory deploying ML for automated optical inspection (AOI) has seen defect detection accuracy shoot through the roof, cutting rework times and boosting yield.
AI/ML Innovation | Benefit | Use Case |
AI-Driven Predictive Maintenance | Reduced downtime, optimized maintenance | Equipment monitoring, preventive actions |
ML in Quality Control | Higher defect detection accuracy | Automated optical inspection, defect elimination |
Why Choose Us – Top Automotive PCBs Manufacturer – JarnisTech!
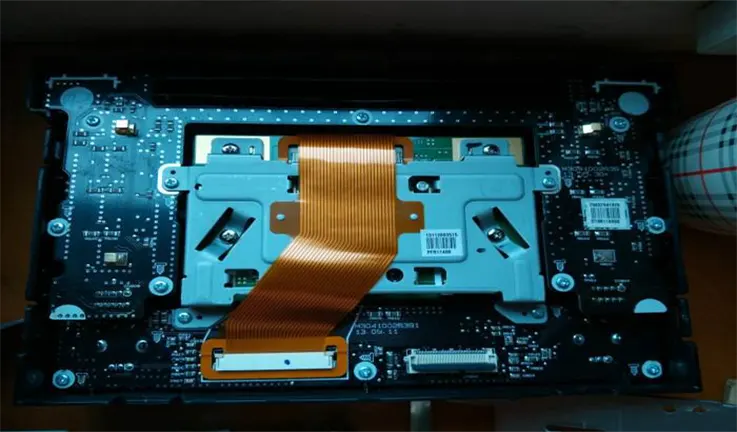
At JarnisTech, we don’t just manufacture circuit boards; we engineer the indispensable neural network for the future of mobility. We specialize in pioneering high-performance automotive Printed Circuit Boards (PCBs), architecting the electronic heart of safety, efficiency, and intelligence for the world’s most forward-thinking automotive innovators.
1. The Core Technology Driving the Next Automotive Revolution
Choosing JarnisTech means empowering your automotive electronic systems with unparalleled performance in these critical areas:
●Precision Vehicle Control & Diagnostics: Our PCBs form the bedrock of the vehicle’s “brain” and central nervous system, ensuring every command is executed with instantaneous and flawless accuracy.
●Proactive Safety & Collision Avoidance: We deliver maximum-reliability circuit solutions for mission-critical safety systems, safeguarding every journey.
●Ultimate Energy Efficiency: Through superior circuit design and fabrication, we significantly reduce power consumption, directly enhancing fuel efficiency and extending electric vehicle range.
●Cutting-Edge In-Cabin Experience: From high-definition infotainment to seamless connectivity, we help create the responsive, feature-rich, and immersive environments that define modern luxury and utility.
2. Pioneers and Problem-Solvers in LiDAR PCB Technology
We are recognized experts in the manufacturing of PCBs for AI-driven LiDAR (Light Detection and Ranging) systems. As the “eyes” of autonomous driving, LiDAR PCBs demand absolute reliability under the most extreme operating conditions.
We are more than a manufacturer; we are a dedicated technology partner. When a global leader in 3D sensing was developing its next-generation AI-driven LiDAR platform, they faced a challenge that other suppliers couldn’t overcome: a critical wire-bondable gold issue that compromised long-term reliability.
JarnisTech not only delivered high-speed multilayer boards that met their stringent requirements for vibration and thermal shock resistance, but our materials science and process engineering expertise also allowed us to definitively solve their wire-bonding technical bottleneck. This success stands as a testament to our deep technical capabilities and our ability to resolve complex manufacturing challenges where others have failed.
3. Powering the Frontier of Automotive Applications
We collaborate side-by-side with industry innovators, providing custom PCB solutions for a wide spectrum of advanced applications:
●L4/L5 Autonomous Cars and Trucks
●Automated Guided Vehicles (AGVs)
●Advanced Driver-Assistance Systems (ADAS) & Pre-Crash Systems
●Vehicle-to-Everything (V2X) & Connected Car Systems
●Vehicle Performance Enhancement Utilities
4. Forged by the Industry’s Most Stringent Standards
Our promise of quality is built on a foundation of rigorously adhering to and exceeding the industry’s highest standards. We don’t just follow guidelines; we internalize them into every stage of our production DNA.
●IPC-6012DA / IPC-6012DA-S: The gold standard for automotive-grade PCBs, ensuring elite reliability under extreme heat and vibration.
●AEC-Q Series (AEC-Q100, Q101, Q102, Q104, Q200): Full compliance with the Automotive Electronics Council’s stress test qualifications for every component, from integrated circuits to discrete semiconductors.
●UL 94V-0: All our advanced boards meet the highest flammability rating, providing an essential layer of safety.
5. Absolute Traceability: Our Commitment to High-Reliability, Delivered
We understand that in automotive electronics, reliability is non-negotiable. By strictly implementing IPC-6012 Class 2 and Class 3 standards and maintaining a comprehensive traceability system, JarnisTech ensures that every PCB we ship is engineered for perfection.
With your first articles and every production order, we provide a Comprehensive Quality Dossier, which includes:
●Certificate of Conformance (CofC)
●Material Specifications and Provenance
●First Article Inspection (FAI) Report
●Reflow Profile Data
●Automated Optical Inspection (AOI) or Visual Inspection Report
●Flying Probe or In-Circuit Testing (ICT) Report
●Ionic Cleanliness Test Report
6. Our Automotive PCB Manufacturing:
Category | Standard Technology | Advanced Technology |
Layer Count | 1 – 18 | 20 – 60 |
Quick Turn Time | 24–48 hrs (1–8 layers)3–7 days (10–26 layers) | 8 – 25 Working days |
Board Thickness | Min:2L – 0.010”4L – 0.020”6L/8L/10L/12L – 0.062”Max:2L – 0.125”3–12L – 0.200” | Min:2L – 0.005”4L – 0.010”6L – 0.031”8L – 0.040”Max:0.250”–0.500” |
Board Size (Max) | 16” × 22”, 12” × 21” | 10” × 16”, 16” × 22”, 12” × 21” |
Copper Thickness | 0.5 oz – 20 oz | 21 oz – 40 oz |
Mechanical Limits | Hole Aspect Ratio: 8:1Min Hole Size: 0.008”Min Trace/Space: 0.006”/0.006”Min Drill-to-Copper: 0.010”Min BGA Pitch: 1 mm | Aspect Ratio: 12:1Hole: 0.004”Trace/Space: 0.002”/0.002”Drill-Copper: 0.005”Pitch: 0.3 mm |
Quality Standards | IPC 6012 Class 2, 100% Netlist, TDR, Electrical Test | IPC 6012 Class 3, 100% Netlist, TDR, MIL-SPEC 31032 / 55110 / 50884 |
Special Capabilities | / | Blind/Buried Vias, Laser/Mechanical Microvias, Metal Core, Burn-in, Rigid-Flex, Flex, RF PCBs |
This dossier is your guarantee of quality and our solemn promise to uphold a zero-defect manufacturing philosophy.
FAQ About Automotive PCBs
How does the automotive industry’s shift to electric vehicles impact PCB design?
The shift to electric vehicles (EVs) increases the demand for high-performance PCBs that can handle higher currents and voltages. This necessitates innovations in materials, designs, and thermal management to support advanced functionalities like battery management systems and electric drive controls.
What are some common applications of automotive PCBs?
●Advanced Driver Assistance Systems (ADAS)
●Engine control units (ECUs)
●Infotainment systems
●Battery management systems
●Safety systems like airbag control
How can manufacturers ensure signal integrity in automotive PCBs?
●Using controlled impedance traces
●Implementing proper grounding techniques
●Minimizing trace lengths and ensuring correct routing
●Utilizing differential signaling for high-speed communication
What is the significance of UL certification for automotive PCBs?
UL certification signifies that the PCB meets safety standards established by Underwriters Laboratories, ensuring it can withstand specific environmental and electrical conditions. This certification enhances product credibility and can be a selling point for OEMs.
What future trends should be watched in automotive PCB technology?
Future trends include the integration of more advanced materials (like flexible electronics), the use of artificial intelligence for design optimization, increased miniaturization of components, and advancements in 5G technology to enhance vehicle connectivity.