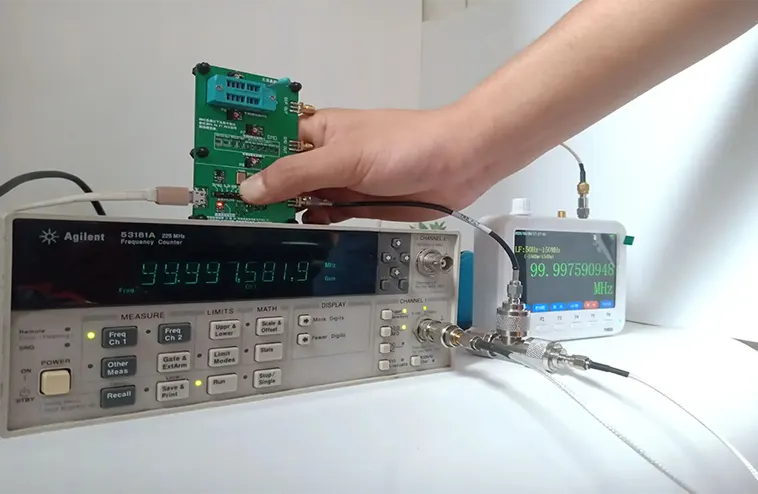
The journey of medical PCBs from design to assembly is complex and multifaceted. Each phase—design, manufacturing, and assembly—requires a deep understanding of the specific challenges and technologies involved. As we embrace the future, innovations in connectivity, sustainability, and automation will drive the evolution of medical devices, enhancing their capabilities and expanding their applications. In this article, we’ll explore the Medical PCB design, manufacturing, and assembly processes that ensure these devices perform reliably in critical situations.
Primary PCB Types Used in the Medical Industry
Choosing the right printed circuit board (PCB) for medical devices is a crucial step in ensuring performance and reliability. Medical equipment requires various types of PCBs to meet different mechanical, electrical, and environmental demands. Below is a detailed breakdown of the most common PCB types used across medical applications, along with factors that make them ideal for certain use cases.
1.Flexible PCBs: Adaptable Solutions for Compact Spaces
Flexible PCBs (Flex PCBs) are widely used in medical devices where space is limited, or components need to be folded, wrapped, or bent during use. Their ability to conform to non-traditional shapes makes them a top choice for wearables and portable medical instruments.
Common Applications:
●Pacemakers
●Blood glucose monitors
●Imaging equipment
●Flexible endoscopes
These PCBs excel in applications that involve movement, reducing the chance of connection failures caused by stress or vibration. Their ability to minimize space and weight makes them ideal for wearable health tech and devices designed for continuous patient monitoring.
2.Flexible Aluminum PCBs: Built for Power and Durability
While Flex PCBs offer unmatched flexibility, certain high-power medical devices require boards with enhanced heat dissipation. This is where flexible aluminum PCBs step in. The aluminum substrate efficiently transfers heat, making these boards the go-to option for high-intensity applications, such as surgical lighting or MRI machines.
Features of Flexible Aluminum PCBs | Benefits in Medical Devices |
Superior heat dissipation | Prevents overheating in high-power devices |
Lightweight and durable | Ensures longevity with frequent use |
Chemical resistance | Suitable for use in sterilized environments |
3.PCB Microcircuits: Tiny Yet Mighty
When working with miniaturized medical devices, PCB microcircuits are the preferred solution. These circuits combine the flexibility of regular Flex PCBs with advanced miniaturization capabilities, providing high performance in small form factors.
Applications:
●Hearing aids
●Wearable sensors
●Portable diagnostic tools
The malleability of these circuits allows manufacturers to fit complex functionalities into compact devices, meeting the growing demand for discreet medical solutions like in-ear hearing aids and continuous glucose monitors.
4.Polyimide PCBs: Strong and Stable Under Pressure
Medical devices that operate in harsh environments require boards with exceptional mechanical strength. Polyimide PCBs stand out due to their thermal stability, chemical resistance, and tensile strength.
Use Cases:
●Prosthetics
●Implanted devices like defibrillators
●Devices exposed to sterilization processes
These boards offer stability across a wide temperature range, making them suitable for both implantable solutions and devices that undergo frequent autoclaving.
5.Ceramic PCBs: Precision for High-Performance Applications
Ceramic PCBs are known for their thermal conductivity and ability to perform under extreme temperatures. With a low coefficient of thermal expansion, they can maintain functionality without warping, making them ideal for high-frequency, high-performance medical devices.
Applications:
●Ultrasonic equipment
●Implantable stimulators
●Lab diagnostic tools
Ceramic PCBs also offer resistance to chemical erosion, ensuring durability in chemically exposed environments like laboratories and operating rooms.
6.Rigid-Flex PCBs: The Best of Both Worlds
Rigid-flex PCBs offer a combination of flexibility and durability by integrating flexible layers with rigid sections. This hybrid design enables engineers to reduce the number of connections between components, minimizing points of failure while adding structural stability.
Applications:
●Imaging equipment
●Portable infusion pumps
●Wearable ECG monitors
These boards are ideal for complex assemblies where reliability and precision are top priorities, such as devices requiring multi-layer circuits within tight enclosures.
Why It All Matters for Medical Devices?
Selecting the right PCB isn’t just about technical specs—it’s about delivering healthcare solutions that improve patient outcomes. Whether you’re developing an implantable device, portable diagnostic tool, or high-powered surgical equipment, each type of PCB has a distinct role in supporting medical innovation.
Medical PCB Design: Creating Precision Circuits for Complex Medical Applications
Designing medical PCBs requires a unique blend of engineering prowess and an understanding of the stringent demands of healthcare devices. As technology progresses, the complexity of these circuits also grows. This evolution necessitates innovative approaches to ensure that medical devices perform reliably and accurately, especially in life-critical applications.
1.High-Frequency Medical PCB Design for Diagnostic Equipment
When designing diagnostic equipment like MRI machines or ultrasound systems, precision and accuracy are non-negotiable. High-frequency medical PCBs ensure these devices operate smoothly by maintaining signal integrity and reducing interference. For example, MRI machines rely on radio frequency (RF) signals to generate highly detailed images of the body. Even a slight disruption in the signal path can degrade the image, making it harder for healthcare professionals to provide an accurate diagnosis.
To tackle this challenge, engineers utilize sophisticated simulation tools like ANSYS HFSS or Keysight ADS. These platforms allow them to model the electromagnetic behavior of circuits, ensuring that signal integrity is maintained throughout the PCB. By identifying potential interference sources during the design phase, engineers can implement strategies like differential signaling or impedance matching to keep signals crisp.
Here’s a breakdown of the key elements in high-frequency medical PCB design:
Aspect | Description |
Signal Integrity | Maintaining clear signals to ensure accurate diagnostics |
Electromagnetic Simulation | Tools to model and predict circuit behavior |
Component Selection | Choosing components that support high-frequency operation |
2.Designing Miniaturized Medical PCBs for Wearables and Implants
The push towards smaller, more efficient medical devices has never been stronger, particularly in the realm of wearables and implants. As healthcare shifts towards more personalized solutions, the demand for compact yet powerful medical PCBs continues to rise.
Take, for example, a wearable heart rate monitor. It needs to be lightweight and comfortable while still gathering accurate data. This is where innovative solutions like rigid-flex PCB technology come into play. By combining rigid and flexible circuit designs, manufacturers can fit complex circuitry into tight spaces without sacrificing functionality.
The following table illustrates some common approaches to miniaturization in medical PCB design:
Method | Benefit |
Rigid-Flex Technology | Combines rigid and flexible PCBs for compact designs |
3D PCB Design | Utilizes three-dimensional structures for space-saving |
Advanced Material Usage | Employs lightweight, durable materials for longevity |
As these technologies evolve, they open the door for groundbreaking applications in patient monitoring and personalized healthcare. Imagine a tiny implant that continuously monitors vital signs and transmits data to a healthcare provider in real time. That’s not just a dream anymore; it’s becoming a reality thanks to advancements in medical PCB design.
3.Power Management in Medical PCB Design
In today’s high-tech medical devices, managing power consumption is a fundamental aspect of PCB design. With the increasing complexity of devices, from handheld diagnostics to implantable technologies, engineers are challenged to optimize power distribution effectively.
For instance, consider a portable blood glucose monitor. It must deliver accurate readings while ensuring battery life is maximized. Engineers tackle this challenge by incorporating advanced power management techniques, such as dynamic voltage scaling and power gating. These strategies help to minimize energy consumption without compromising performance.
Here’s a snapshot of effective power management strategies in medical PCB design:
Technique | Application |
Dynamic Voltage Scaling | Adjusts power usage based on operational demands |
Power Gating | Disables unused components to conserve energy |
Battery Management Systems | Optimizes charging cycles and prolongs battery life |
Materials and Technologies Driving Advanced Medical PCB Manufacturing
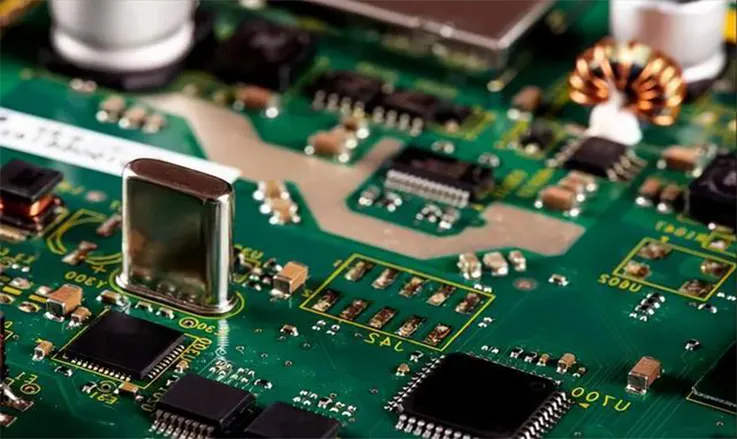
When it comes to whipping up reliable medical devices, the right materials and technologies are like the secret sauce. Picking the right components can make the difference between a device that rocks and one that flops. Let’s dive into the nitty-gritty of material selection, HDI tech, and compliance so you can stay ahead of the game.
1.Selecting Materials for Medical PCB Manufacturing
Choosing materials for medical PCB manufacturing is no small potatoes. It’s all about hitting that sweet spot where performance meets reliability. Here are some key players in the material game:
FR-4: This fiberglass-reinforced epoxy laminate is the bread and butter of PCB materials. It’s versatile and easy on the wallet, making it a top choice for many applications, from basic devices to more complex systems.
Rogers Materials: When you’re dealing with high-frequency applications, Rogers materials are the big guns. They’ve got stellar dielectric properties that ensure your signals stay crisp and clear, especially in devices like MRI machines and ultrasound equipment.
Material | Key Features | Common Applications |
FR-4 | Cost-effective, versatile | General-purpose medical devices |
Rogers | High-frequency performance | MRI machines, ultrasound equipment |
Polyimide | Flexible and durable | Wearable medical devices, implants |
2.Implementing HDI Technology in Medical PCB Manufacturing
High-Density Interconnect (HDI) technology is the real deal when it comes to PCB manufacturing. This tech lets you create smaller, more intricate circuit boards that don’t compromise on performance. Here’s what you need to know:
Compact Design: HDI techniques enable designers to cram more capabilities into a tighter space, which is a major plus for portable medical devices that need to be both lightweight and high-performing. This compactness allows for more sophisticated features without adding bulk, making these devices easier to handle and transport.
Improved Signal Integrity: HDI designs use finer traces and smaller vias to ensure signals flow smoothly without distortion or interference. These compact structures reduce electrical noise and minimize crosstalk, making them a solid fit for applications that demand precise data transmission. By optimizing signal paths and keeping everything tight, HDI PCBs deliver reliable performance even in high-frequency environments.
Benefit | Description |
Space Efficiency | Smaller boards fit into compact devices |
Higher Performance | Better signal integrity and lower power consumption |
Enhanced Functionality | More components in a limited area without compromises |
3.Ensuring Compliance During Medical PCB Manufacturing
In the medical field, compliance isn’t just a formality; it’s the lifeblood of your operations. Staying on top of industry regulations is a must to ensure both patient safety and device efficacy. Here’s how to keep your ducks in a row:
Quality Control Processes: Implementing strict quality control measures throughout the manufacturing process is a must. This could be as simple as regular visual inspections or as complex as advanced testing techniques.
Thorough Documentation: Keeping accurate records isn’t just a best practice; it’s necessary to show that you’re following the rules. This includes everything from material specs to test results.
Compliance Aspect | Importance |
Regulatory Standards | Ensures safety and efficacy of medical devices |
Quality Assurance | Prevents defects and enhances device reliability |
Traceability | Allows tracking of materials and processes |
Medical PCB Assembly Techniques: Meeting Stringent Quality Requirements
In the medical device manufacturing, the assembly process can make or break your product. The techniques used in medical PCB assembly must not only meet strict quality standards but also adapt to the evolving needs of healthcare. Let’s explore the nitty-gritty of assembly techniques, from SMT and THT to turnkey solutions and quality control practices.
1.SMT vs. THT for Medical PCB Assembly
When it comes to choosing the right assembly method, manufacturers often find themselves at a crossroads: Surface Mount Technology (SMT) or Through-Hole Technology (THT)? Each has its own set of perks and drawbacks, making the decision a key consideration in the design process.
Surface Mount Technology (SMT): SMT is like the cool kid on the block. It’s sleek, space-efficient, and offers enhanced electrical performance, making it the go-to choice for modern medical devices. By mounting components directly onto the surface of the PCB, SMT allows for more compact designs and faster production speeds. For example, in the realm of portable medical devices, where every millimeter counts, SMT shines brightly.
Through-Hole Technology (THT): On the other hand, Through-Hole Technology (THT) is your go-to solution when you need reliability. It’s been a staple in the industry for years, especially suited for applications that require strength, like military and rugged medical devices. THT involves placing component leads through holes in the PCB and soldering them on the opposite side, creating a robust connection. This method shines in scenarios where devices face significant physical stress or demand high durability, such as surgical instruments. It’s a dependable choice for those tough jobs!
Technology | Advantages | Best Use Cases |
SMT | Space-saving, faster production | Portable medical devices, wearables |
THT | Robust connections, high durability | Surgical tools, military equipment |
2.Turnkey Medical PCB Assembly for Rapid Product Launches
The pressure to launch medical devices at lightning speed is real, and that’s where turnkey assembly services come into play. Think of turnkey assembly as the one-stop shop for getting your product out the door—fast.
Comprehensive Solutions: Turnkey providers handle everything from design to assembly, which means you can kick back while they take care of the heavy lifting. This integrated approach helps streamline the entire supply chain, reducing lead times and minimizing hiccups along the way. For instance, when a new diagnostic tool needs to hit the market quickly, relying on a turnkey solution can mean the difference between leading the charge and lagging behind.
Innovation Focus: By offloading assembly logistics, manufacturers can focus on what really matters—innovation. You get to spend more time brainstorming the next big thing instead of sweating the small stuff. With turnkey services, it’s like having your cake and eating it too; you get quality and speed all wrapped up in one neat package.
Benefit | Description |
Speed to Market | Quick turnaround from design to production |
Cost Efficiency | Reduces overhead by streamlining processes |
Enhanced Collaboration | Better communication between teams |
Adopting turnkey solutions in your assembly process is a savvy move that can lead to better market positioning.
3.Quality Control Practices in PCB Assembly
Quality control goes beyond a mere checklist; it’s the foundation of effective medical PCB assembly. By putting strong quality assurance practices in place, you can ensure that each assembly meets the rigorous standards necessary for medical applications. This attention to detail not only safeguards patient safety but also boosts the overall reliability of your devices. So, make quality a top priority and watch your assembly process thrive!
Automated Optical Inspection (AOI): Think of AOI as the watchful eye in your assembly line. This tech inspects the assembled PCBs for defects in real time, catching issues before they escalate. It’s like having a safety net that helps ensure that every device that rolls out is up to snuff.
X-ray Inspection: When it comes to those hard-to-reach areas, X-ray inspection is the go-to technique. This approach digs into the PCB layers, ensuring that all hidden components are soldered properly and that there are no sneaky defects hiding out of sight. This process is especially necessary for intricate assemblies with tightly packed components. Keep those hidden issues at bay—utilize X-ray inspection to maintain top-notch quality!
Quality Control Technique | Advantages |
AOI | Real-time defect detection |
X-ray Inspection | Thorough internal checks for complex assemblies |
Medical PCB Traceability: Tracking Every Step with Precision
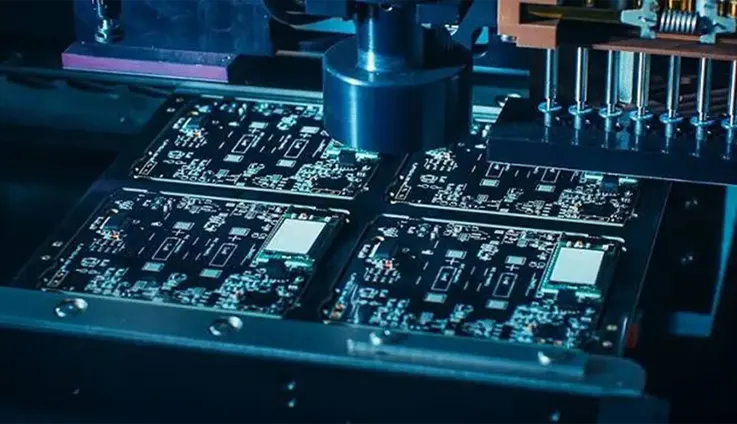
In the manufacturing of medical devices, traceability acts as a safeguard to ensure transparency, quality control, and accountability throughout the product’s lifecycle. It’s the practice of documenting every step—from raw materials to final production—so that manufacturers can track components and processes in real time. Let’s break down what traceability means in the context of printed circuit board assemblies (PCBA) and its significance to the medical industry.
1.What is PCB Traceability?
In simple terms, traceability in electronics manufacturing is the ability to follow and document every component, process, and material used to build a circuit board. Every part, from resistors to microprocessors, is tracked through product serial numbers, lot codes, and equipment usage logs. This data allows manufacturers to review past practices, spot any inconsistencies, and take proactive steps to avoid issues before they affect the final product.
2.Core Elements of Traceability in Medical PCBs
Quality Management-
Medical device manufacturers must meet strict quality control standards—and ISO 13485 is the gold standard. This international certification mandates suppliers to maintain rigorous control over their processes and ensure traceability at every stage. Components, raw materials, and even third-party suppliers involved in the chain must align with the same high standards.
Example: If a defect is found in a pacemaker, traceability records enable manufacturers to identify the faulty batch and quickly issue a targeted recall, rather than pulling the entire product line.
Process Agility and Risk Management-
By tracking the entire production process, manufacturers can respond flexibly to risks and adjust operations as needed. Adopting ISO 14971, an internationally recognized framework for risk management, ensures manufacturers take a methodical approach to hazard identification and mitigation strategies.
Common tools used for this purpose include:
●Preliminary Hazard Analysis (PHA): Helps detect risks early in the design phase.
●Hazard and Operability Studies (HAZOP): Focuses on potential operational failures.
●Failure Mode and Effect Analysis (FMEA): Pinpoints weak spots that might impact product reliability.
Agility Example: If one batch of materials is delayed or rejected, traceability systems allow manufacturers to pivot quickly, minimizing downtime while maintaining compliance.
Legal Compliance and Accountability-
Traceability is a key component of legal compliance. When problems arise that may threaten patient safety, being able to demonstrate that your processes adhere to regulatory standards can help avert lawsuits and lead to faster resolutions. Lacking proper documentation, companies expose themselves to the risk of substantial fines, penalties, or legal disputes resulting from product defects or recalls. Keeping meticulous records is not just a wise move; it’s a savvy way to manage legal challenges!
Case Example: Imagine a medical device causes unexpected harm to a patient. With traceability in place, the manufacturer can produce records demonstrating adherence to quality standards and isolate the issue—whether it’s with the design, material, or production.
3.How Traceability Enhances Medical PCB Manufacturing?
Traceability isn’t just about following rules—it’s about making smarter decisions and building trust with customers. Below are a few real-world advantages:
Benefit | How It Helps in Medical PCB Manufacturing |
Faster Problem Resolution | Easily pinpoint defective batches for targeted recalls. |
Improved Quality Control | Monitor supplier performance and make data-backed improvements. |
Compliance Assurance | Stay aligned with ISO standards and avoid penalties. |
Optimized Risk Management | Quickly adapt to changes with full visibility into production processes. |
Why Traceability Matters More Now Than Ever?
With medical devices becoming more advanced and interconnected, the stakes have never been higher. Whether it’s implantable devices or wearable tech, manufacturers can’t afford to cut corners. Traceability ensures not only that devices work as intended but also boosts customer confidence. Patients and healthcare providers alike need assurance that the products they rely on meet the highest possible standards.
Testing and Quality Control in Medical PCB Production
Testing and quality control are where the rubber meets the road in medical PCB production. Every board has to go through its paces to prove it’s fit for the job, especially since lives depend on these devices working right, every time. From reliability testing to environmental stress screening, these processes ensure that the final product will stand up to the wear and tear of real-world conditions.
1.Advanced Testing for Medical PCB Reliability
Medical PCBs are the nerve centers of many healthcare devices, and they have to handle everything from daily wear to unexpected extremes. Engineers put these boards through a series of rigorous tests to ensure they can handle whatever comes their way—think of it as a bootcamp for circuits.
Functional Testing: This test is the bread and butter. It checks that every component on the board does exactly what it’s supposed to. Imagine a blood glucose meter giving a faulty reading—it could throw a patient’s health plan off course. Functional testing verifies that readings are accurate, sensors respond correctly, and communication modules sync up smoothly.
Stress Testing: Now, this is where things get intense. Engineers simulate harsh conditions—like rapid temperature swings, vibrations, and humidity—similar to what the device might experience in the real world. For example, stress testing might reveal that a monitoring device used in ambulances doesn’t hold up under constant motion. Spotting these weaknesses early means fewer headaches—and recalls—down the line.
Test Type | Purpose | Example |
Functional Testing | Verifies component performance | ECG sensors functioning properly |
Stress Testing | Simulates harsh conditions | Vibration tests on portable diagnostic tools |
2.Lifecycle Testing and Environmental Stress Screening (ESS)
When you’re building devices meant to last, lifecycle testing and ESS are your secret weapons. It’s all about predicting how your device will hold up over time without waiting years to find out.
Lifecycle Testing: In this process, engineers simulate months or even years of wear in a matter of days. Medical devices like pacemakers or ventilators need to work reliably for extended periods, so lifecycle testing helps catch potential breakdowns early. Imagine if a critical component in an implant were to wear out unexpectedly—it’s these tests that ensure that doesn’t happen.
Environmental Stress Screening (ESS): ESS is the equivalent of taking a PCB for a spin under extreme conditions—overheating, freezing, high humidity—you name it. The goal is to flush out any weak components before they cause trouble in the field. For instance, a medical sensor used in outdoor health monitors might need to withstand both freezing winters and scorching summers. If it can’t, ESS will bring that flaw to light during production.
Testing Method | Goal | Use Case Example |
Lifecycle Testing | Predicts long-term reliability | Assessing the lifespan of pacemakers |
Environmental Stress Screening (ESS) | Identifies potential failures early | Outdoor patient monitors in extreme weather |
3.Compliance Testing and Certification
Compliance testing is the final boss before any medical PCB can be put to work. Devices need to meet strict guidelines to ensure they’re safe for patients and pass the muster with regulatory bodies like the FDA, CE, or ISO.
Staying Current with Regulations: The rulebook for medical devices changes frequently. From updates in electrical safety standards to stricter EMI (electromagnetic interference) limits, manufacturers need to stay on their toes. For example, the growing use of wireless communication in medical devices has led to new regulations around signal interference. Staying ahead of these changes is non-negotiable to avoid production delays.
Certification and Documentation: Certification isn’t just about slapping on a fancy label—it’s about proving that every part of the device meets regulatory benchmarks. From materials used to production methods, every step must be documented. This paperwork not only satisfies regulators but also gives patients peace of mind knowing the devices they rely on meet safety standards. Miss a single step, and your product risks getting yanked off the shelves.
Certification Type | Purpose | Example |
FDA (USA) | Ensures safety and effectiveness | Approval for Class II devices (e.g., glucose meters) |
ISO 13485 | Sets quality standards for manufacturing | Compliance in international markets |
Ensuring Global Compliance with Medical PCB Standards
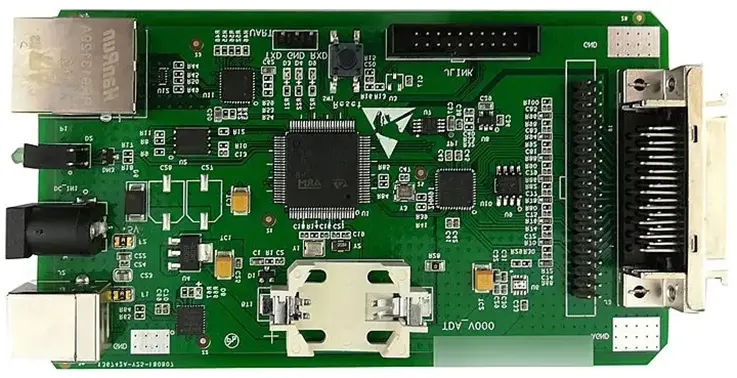
Navigating the labyrinth of global compliance standards is no walk in the park for medical device manufacturers. Ensuring PCBs meet the latest regulatory benchmarks is like threading a needle—it demands precise documentation, ongoing validation, and flexibility to keep up with evolving requirements. Let’s break down the must-hit compliance targets and how manufacturers can stay ahead of the game.
1.FDA and ISO 13485 Certification for Medical PCB Products
Securing FDA approval and ISO 13485 certification isn’t just about ticking boxes—it’s about building trust and proving that your products meet the high bar set by the industry. Here’s what it takes to stay on track:
Thorough Documentation: Every step of the production process—from design to delivery—needs to be documented. This isn’t just for internal use; auditors will want to see the full paper trail to ensure nothing slips through the cracks.
Process Validation: Manufacturers need to validate each production step to confirm it consistently delivers quality results. For example, if a PCB is used in heart monitors, every batch must undergo the same rigorous testing to guarantee consistency.
Continuous Monitoring: Certification isn’t a one-and-done deal. Companies must monitor production processes regularly to stay compliant with FDA updates and ISO 13485 standards. Tools like automated reporting systems can help teams spot red flags before they become compliance headaches.
Certification | Purpose | Example Application |
FDA Approval | Ensures safety and performance for U.S. markets | Glucose monitoring systems |
ISO 13485 | Sets standards for global manufacturing quality | Ventilators and ECG machines |
Without these certifications, breaking into certain markets—like the U.S. and EU—is practically impossible. So, the message is clear: Don’t skip the fine print.
2.Meeting IPC and RoHS Standards in Medical PCB Production
If you’re not up to snuff with IPC standards and RoHS compliance, you’ll find yourself dead in the water pretty quickly. Here’s why these standards matter:
IPC Standards: These guidelines ensure the structural and electrical integrity of PCBs. Engineers following IPC Class 3 standards, for example, are producing boards built to withstand mission-critical tasks. Think about surgical robots—there’s no room for failure when precision is everything.
RoHS Compliance: RoHS restricts the use of hazardous materials like lead and mercury in electronics. Compliance not only meets environmental regulations but also safeguards patient health. Devices worn or implanted in patients, like insulin pumps, need to be RoHS-compliant to avoid exposing users to toxic substances.
The best manufacturers put systems in place to monitor compliance at every stage. Digital compliance management platforms can track production data, alerting teams when something falls out of spec. It’s not just about playing it safe—it’s about building consumer trust from the ground up.
3.Maintaining Compliance During Production Changes
When it comes to medical manufacturing, change is the only constant. Whether it’s a new material, supplier, or process tweak, manufacturers need to stay nimble while keeping compliance airtight.
Adapting to New Materials or Technologies: Switching to a new PCB substrate, for example, might improve performance, but it could also introduce new compliance challenges. Regular internal audits ensure new materials don’t throw off established processes.
Training and Documentation: The entire production team—from engineers to assembly line workers—needs to stay in the loop. Continuous training sessions make sure everyone understands new compliance rules as soon as they hit the books.
Using Compliance Management Tools: Automated tools help manufacturers keep tabs on changing regulations. For instance, if new RoHS guidelines tighten restrictions on certain chemicals, the system will flag affected product lines and suggest alternatives.
Compliance Focus | Challenge | Solution |
Material Substitution | New materials may introduce risks | Regular internal audits |
Process Tweaks | Maintaining certification with new processes | Training and compliance management tools |
Prototyping and Small-Batch Manufacturing for Medical PCBs
Navigating the process of prototyping and small-batch production in the medical PCB space requires a fine-tuned balance of speed, precision, and adaptability. Let’s dive into how manufacturers can stay agile while meeting industry expectations.
1.Rapid Prototyping for Medical PCB Design Validation
Rapid prototyping is like having a sneak peek at the final product—except you can tweak, test, and rework it as many times as needed without the hefty price tag of mass production. By using 3D printing, CNC machining, and fast PCB fabrication methods, engineers can experiment with various designs in real-time.
Shorter Iteration Cycles: In just days, companies can build functional prototypes to validate concepts like sensor accuracy or PCB form factors. Imagine developing a wearable heart monitor—rapid prototyping lets teams confirm fit and connectivity long before the final launch.
Failure-Friendly Process: Prototypes act as a playground for uncovering flaws early. For example, if a PCB’s heat management design doesn’t cut it during a thermal test, the team can quickly revise the layout and print a new board.
Practical Applications: Prototypes aren’t just for show—they’re increasingly functional. Engineers can stress-test these models with real-world scenarios, making sure that the final product will perform as expected under clinical conditions.
This approach not only reduces time-to-market but also slashes the chances of expensive production errors down the line.
2.Small-Batch Manufacturing for Custom Medical PCB Assembly
As healthcare shifts towards personalized solutions, the need for flexible, small-batch production has surged. In contrast to large-scale runs, small-batch manufacturing allows companies to cater to niche markets and unique customer demands with precision.
Custom Configurations: This process allows for the assembly of specialized devices, such as tailored implants or portable diagnostic tools, without the overhead of mass production. Think of a startup producing custom neurostimulation devices—small batches let them stay nimble and pivot as needed based on patient feedback.
Lower Risk, Higher Flexibility: Small runs mean manufacturers can make quick changes mid-production if a design improvement is identified. No need to worry about wasting thousands of units already in stock. This approach also aligns with lean manufacturing principles, focusing on waste reduction and just-in-time production.
Responsive to Market Trends: Small-batch production helps companies test new ideas on a smaller scale before committing to full-scale manufacturing. For example, they might introduce an updated ECG monitor in small quantities to gauge market response before ramping up.
3.Cost Considerations in Prototyping and Small-Batch Manufacturing
While small-batch manufacturing and prototyping have their perks, the financial side needs careful planning. Here’s how manufacturers can stay on top of the numbers without compromising on quality:
Cost of Materials vs. Flexibility: Prototypes often rely on specialized materials or expedited manufacturing processes, which come with higher upfront costs. However, these expenses pay off by preventing costly production errors in large-scale runs.
Technology Investment: Investing in in-house rapid prototyping tools like CNC machines can be expensive but might save companies money over time. Alternatively, outsourcing can provide access to cutting-edge technologies without the capital investment.
Method | Benefit | Cost Consideration |
3D Printing | Fast iterations, complex designs | Material costs (resin/filament) |
CNC Machining | Precision for metal PCBs | High setup and tooling fees |
Outsourcing Prototyping | Access to advanced tech | Vendor lead times and shipping fees |
Batch Size and Unit Pricing: The smaller the batch, the higher the per-unit cost—but small runs reduce the financial impact if changes are needed.Striking a balance between batch size and pricing is key to staying competitive while catering to specific client requirements. It’s all about being adaptable and ready to pivot when necessary to keep those customers satisfied!
The Role of IoT and AI in Medical PCB Innovation
The medical industry is experiencing a shift towards smarter, more connected devices powered by Internet of Things (IoT) and Artificial Intelligence (AI). These innovations offer enhanced patient care, real-time data insights, and new opportunities for personalized healthcare. However, with these advancements come new challenges related to security, design, and scalability. Let’s break it down.
1.IoT-Enabled Medical Devices for Remote Healthcare
IoT is turning healthcare on its head by enabling remote monitoring and data exchange between patients and providers in real time. Medical PCBs designed for IoT need to be fine-tuned for connectivity, power efficiency, and reliability to ensure devices like insulin pumps, smart inhalers, and cardiac monitors keep doing their thing without a hitch. It’s all about making sure these gadgets are up to snuff, so they can deliver the care patients need, right when they need it!
24/7 Monitoring and Alerts: Imagine a patient using a wearable ECG patch—data flows from the device to a cloud server, where physicians can track heart activity remotely. This setup reduces the need for frequent hospital visits and allows early detection of complications.
Connectivity Matters: For these devices to work smoothly, PCBs must support wireless protocols like Bluetooth Low Energy (BLE), Wi-Fi, and NB-IoT (Narrowband IoT). A dropped signal during critical moments can’t happen, which makes reliable connectivity hardware a top priority.
Case Study: The rise of telehealth platforms has made it easier for elderly patients to receive care from home. IoT-enabled glucose monitors now send blood sugar levels directly to apps, giving caregivers the ability to intervene before problems escalate.
2.AI Integration in Medical PCB Design
Artificial intelligence is leveling up the PCB design process, creating smarter workflows and improving the reliability of medical devices. Instead of relying solely on manual design processes, engineers use AI algorithms to automate PCB layout generation and anticipate design flaws.
Predictive Design Tools: AI-based software can run simulations to predict thermal performance, signal integrity, and power distribution issues, allowing engineers to tweak designs before manufacturing even begins.
Faster Troubleshooting: When devices hit production snags, AI systems can analyze manufacturing data to detect the root cause faster than manual inspections. This saves both time and resources, especially in high-stakes environments where delays aren’t an option.
Example of AI in Action: Consider a smart ventilator with adaptive algorithms that adjust oxygen levels based on patient data. The PCB powering such a device must be designed to support AI modules that learn over time, refining performance in response to individual needs.
3.Data Security Concerns with IoT Medical Devices
With connected devices comes the challenge of keeping sensitive patient data safe from prying eyes. Medical IoT devices are attractive targets for cyberattacks, and any breach could compromise both patient safety and privacy.
●Encryption is a Must: Every data exchange—whether between a glucose monitor and a smartphone or a remote heart monitor and a hospital server—must be protected using strong encryption protocols. This ensures that only authorized individuals can access the data.
●Regulatory Compliance and Standards: IoT medical devices need to comply with HIPAA (Health Insurance Portability and Accountability Act) in the U.S. and GDPR in Europe, ensuring that personal health information is protected at all times.
Security Measure | Purpose |
End-to-End Encryption | Secures data during transmission and storage |
Two-Factor Authentication | Prevents unauthorized access to devices |
Regular Software Updates | Fixes vulnerabilities and strengthens defenses |
Real-World Example: In 2017, the FDA recalled a series of pacemakers due to potential security vulnerabilities that could have allowed hackers to alter device settings remotely. This incident underscores the need for robust security practices throughout the product lifecycle.
Why Choose JarnisTech for Your Medical Device PCB Manufacturing Needs?
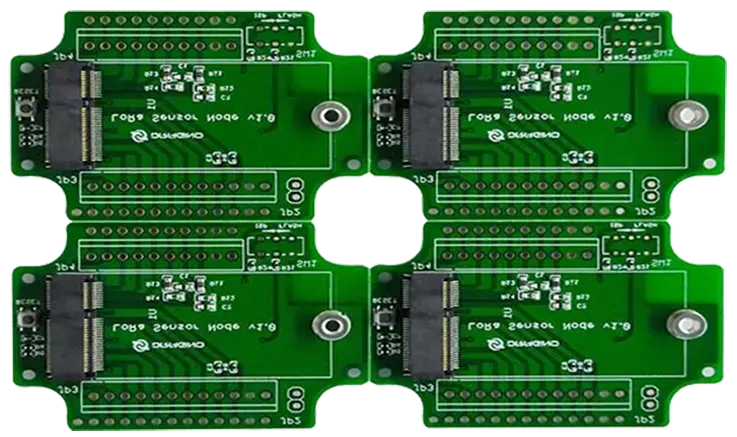
Picking the right partner for PCB manufacturing is no easy feat, particularly in the medical device sector, where precision, dependability, and quick turnaround can set you apart. With over two decades of expertise, JarnisTech, based in Shenzhen, China, excels in turnkey PCB assembly and specializes in high-frequency, high-density designs. Here’s what differentiates us in a crowded market:
1.Comprehensive PCB Manufacturing Capabilities
At JarnisTech, we offer more than just assembly; we deliver comprehensive services tailored to support engineering teams and medical device manufacturers throughout the entire development process. Whether you’re working on prototypes or scaling up for full production, we make sure each phase flows without a hitch.
●Surface Mount Technology (SMT) Assembly: Efficient for high-volume production with compact components.
●Through-Hole Technology (THT): Ideal for components needing stronger connections and durability.
●Box Build Assembly: We handle the entire device—beyond PCBs—with final assembly solutions, including cable harnessing and packaging.
●Testing and Inspection Services: Our in-house testing guarantees your products meet industry standards and function properly before leaving the factory.
Our ISO 9001 certification reflects our commitment to strict quality control protocols that are scalable and transparent. This means customers benefit from streamlined processes with complete visibility at every stage.
2.From Concept to Market—Your Innovation Partner
Prototyping for Rapid Design Iterations-
Creating a new medical device means navigating multiple rounds of testing, and speedy feedback is where it’s at. At JarnisTech, we specialize in rapid prototyping, enabling clients to confirm their designs and catch any issues early on, long before they hit the production stage. Whether you’re launching a fresh concept or revamping existing tech, our prototyping services streamline lead times and minimize risks. Let’s turn your ideas into reality without the headaches!
●Case Example: A startup developing a wearable heart monitor used our prototyping services to refine sensor placement. With our design-for-manufacturability (DFM) insights, they caught a potential thermal issue that could’ve caused malfunctions under heavy usage.
Engineering Support That Goes the Extra Mile-
At JarnisTech, we think consultations should go beyond mere formalities. Our engineers collaborate closely with your team to ensure that designs meet both budget constraints and functional needs. Here’s a look at what we bring to the table:
●Design Rule Checks (DRC): Ensuring every design meets industry standards.
●Laminate and Material Consulting: Helping you choose the right substrates and finishes for high-frequency boards.
●Cost Optimization Strategies: We guide you on how to balance performance with budget constraints, ensuring your product hits the market without delays or surprise expenses.
Engineering Services | What It Does |
Design Rule Check (DRC) | Identifies potential design errors before production. |
Surface Finish Consulting | Ensures optimal surface selection for functionality and longevity. |
Stack-Up Design | Improves signal integrity by arranging PCB layers effectively. |
3.Reliable Manufacturing with Global Partnerships
One of the most challenging parts of medical device production is overseeing fabrication—especially when components come from multiple suppliers. JarnisTech simplifies this process through long-term relationships with both domestic and international PCB facilities, ensuring high-quality output at competitive prices.
We inspect every board before shipment and offer lifecycle support to help you troubleshoot post-production issues. Our goal is to stay with you through the entire product lifecycle, ensuring your device remains functional and reliable from prototype to final release and beyond.
4.Support for the Long Haul—Lifecycle Services That Matter
Even after your PCBs are fabricated, we don’t just hand off the product and walk away. JarnisTech provides lifecycle support that includes continuous monitoring, routine maintenance advice, and failure analysis if issues arise.
●Example: One client experienced unexpected electromagnetic interference (EMI) in their medical diagnostic equipment post-production. Our engineers stepped in, conducted a root-cause analysis, and suggested layout adjustments to prevent future disruptions.
5.JarnisTehc Medical PCB Manufacturing Capabilities
Item | Capability / Description |
PCB Thickness | 0.4 mm to 8.2 mm (custom options available) |
Copper Weight | Inner layers: 0.5–12 oz; Outer layers: up to 40 oz |
Layer Count | 2 to 46 layers |
Applications | Imaging, Monitoring, Robotic Surgery, Radiation Therapy |
Testing Methods | AOI (2D/3D), Solderability, Flying Probe, TDR, X-ray, Micro-section |
Quality Standards | IPC-6012 Class 2/3, ISO 13485, IEC 60601-1/-2, UL 94V-0 |
Traceability | Full records: CoC, material specs, AOI report, FAI, ionic test report |
Design Support | DFM & DFA checks, IPC Class 3 compliance, engineering consultation |
Production Model | Fabrication + Assembly under one roof for speed and accuracy |
Why Work with JarnisTech?
We recognize that getting products to market quickly and maintaining quality are top priorities for medical device manufacturers. With our extensive experience and state-of-the-art facilities, we deliver flexible and scalable solutions tailored to your specific needs. Our dedicated team is ready to provide personalized assistance, whether it’s through engineering consultations, rapid prototyping, or lifecycle management. Let’s work together to kick your projects into high gear!
Call us today at 0086-0755-23034656 or visit our contact page to learn how we can help your next project succeed. At JarnisTech, we don’t just build PCBs—we build trust, one board at a time.
Frequently Asked Questions (FAQ)
What is a Medical PCB?
A Medical PCB (Printed Circuit Board) is a critical component in medical devices, providing the necessary electrical connections and pathways for various functions. These boards must meet strict regulatory standards due to their application in health-related technologies.
How do I choose the right materials for Medical PCB manufacturing?
Selecting materials for Medical PCB manufacturing depends on several factors, including the specific application, required durability, and environmental conditions. Common materials include FR-4 for general applications, Rogers for high-frequency needs, and ceramic for specialized requirements.
What are the key design considerations for Medical PCBs?
Key design considerations for Medical PCBs include signal integrity, power management, component placement, and biocompatibility. Designers also need to consider the size constraints, especially for wearable and implantable devices.
How is the manufacturing process for Medical PCBs different from standard PCBs?
Medical PCBs require higher reliability, regulatory compliance, and stringent testing protocols compared to standard PCBs. The manufacturing process often involves specialized equipment and adherence to standards like ISO 13485 and FDA regulations.
What testing methods are used for Medical PCBs?
Testing methods for Medical PCBs include functional testing, flying probe testing, X-ray inspection, and environmental stress screening. These tests ensure that the boards perform reliably under various conditions and meet safety standards.