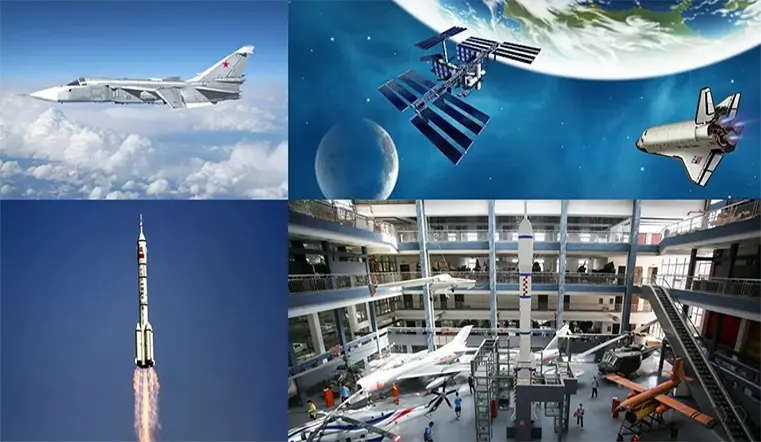
Welcome to the ultimate rundown on aerospace PCB manufacturing and assembly! In a world where precision is everything, this guide will take you through the nitty-gritty of what it takes to thrive in the aerospace sector. From design to procurement and collaboration, we’re diving deep to give you the lowdown on best practices that can skyrocket your efficiency and keep you ahead of the game. Whether you’re a seasoned pro or just getting your feet wet, buckle up as we explore the ins and outs of this high-flying industry.
Introduction to Aerospace PCB Manufacturing
Aerospace PCB Manufacturing specializes in creating printed circuit boards (PCBs) designed specifically for the aerospace industry. These PCBs support systems ranging from avionics to satellite communications. With technological advancements, the demands for performance and durability in aerospace PCBs continue to increase.
Importance of Aerospace PCB Manufacturing
In Aerospace PCB Manufacturing, recognizing its contributions is necessary for stakeholders. Aerospace PCBs serve as integral components in navigation, communication, and control systems. The design and production processes include comprehensive testing and adherence to standards, ensuring functionality in challenging environments.
●Reliability and Durability in Aerospace Applications
Reliability and durability are key in aerospace applications. PCBs must withstand extreme temperatures, vibrations, and electromagnetic interference. Manufacturers often use high-performance materials such as polyimide and specialized coatings that can endure these challenges.
For instance, when designing PCBs for commercial aircraft, engineers frequently choose multilayer configurations that enhance performance while reducing weight. This reflects the industry’s need to maximize efficiency and optimize space.
Key Reliability Factors:
Material Selection: Choosing materials that resist thermal expansion and maintain structural integrity under stress is necessary.
Testing Protocols: Rigorous methods like thermal cycling and vibration testing ensure that PCBs can handle the conditions of aerospace applications.
Reliability Factor | Description | Example Application |
Material Selection | High-performance materials resistant to thermal and mechanical stress | Avionics systems in commercial aircraft |
Testing Protocols | Procedures such as thermal cycling and vibration testing | PCBs in satellite communication systems |
●Compliance with Industry Standards in Manufacturing
Adhering to industry standards forms the foundation of Aerospace PCB Manufacturing. Various standards dictate specifications and testing protocols that ensure quality and safety. Key standards include IPC-6012 and MIL-PRF-31032, which outline requirements for performance and reliability in aerospace applications.
IPC-6012: This standard focuses on rigid printed boards, specifying qualification and performance criteria. Following IPC-6012 helps manufacturers maintain consistent quality throughout production. It acts as a guide that ensures every process is executed accurately.
MIL-PRF-31032: This military specification is necessary for military and aerospace applications, detailing extensive testing and qualification criteria. Compliance ensures that PCBs can endure extreme conditions, including radiation exposure and temperature fluctuations, which is necessary for maintaining safety.
Why Compliance Matters?
●Quality Assurance: Adhering to established guidelines supports high-quality production runs, reducing the chance of errors.
●Client Trust: Many aerospace clients require proof of compliance before considering suppliers, highlighting the necessity for adherence to standards.
Standard | Application | Testing Method |
IPC-6012 | Rigid PCBs for avionics systems | Automated Optical Inspection (AOI) |
MIL-PRF-31032 | Military communication systems | X-ray Inspection |
Case Study: A Leading Manufacturer’s Compliance Strategy
●Company: AeroPrecision Technologies
●Project: Development of robust PCBs for unmanned aerial vehicles (UAVs).
●Challenge: Ensure compliance with MIL-PRF-31032 while managing project timelines.
●Solution: Implemented a quality management system and conducted regular training sessions on compliance requirements.
●Outcome: Achieved compliance with zero defects during third-party audits, enhancing market reputation and attracting new clients.
Key Design Guidelines for Aerospace PCB Manufacturing
In the aerospace industry, PCB (Printed Circuit Board) design must adhere to specific guidelines to ensure functionality and reliability. These design guidelines help manufacturers optimize production processes, reduce defects, and enhance the performance of the final product.
Design for Manufacturability (DFM) in Aerospace PCBs
Design for Manufacturability (DFM) is a fundamental concept in the development of aerospace PCBs. The DFM approach considers manufacturing processes during the design phase, making PCB production and assembly more efficient.
Core Principles of DFM:
Design Simplification: Reducing the number of components can lower potential failure points and decrease production costs. Pursuing a simpler design aids in easier assembly.
Standardized Components: Utilizing off-the-shelf components whenever possible simplifies procurement and assembly processes, often leading to cost savings and shorter lead times.
Case Study: In a recent drone project, reducing the number of components in a complex PCB design led to a 30% reduction in assembly time, thereby accelerating deployment.
DFM Principle | Description | Benefits |
Design Simplification | Minimize component count | Reduce costs and assembly time |
Standardized Components | Use of common parts | Simplify procurement and inventory |
●Component Placement Best Practices for Aerospace Applications
Proper component placement is significant in enhancing aerospace PCB performance and reliability. A well-thought-out layout helps to minimize electromagnetic interference (EMI) and reduce thermal buildup.
Best Practices:
Strategic Placement: Grouping similar components can reduce signal interference. Keeping analog and digital circuits separate lowers crosstalk.
Thermal Management Design: Positioning heat sinks near heat-generating components improves heat dissipation and extends the lifespan of those components.
Placement Consideration | Description | Impact |
Strategic Placement | Group similar components | Reduce EMI and enhance performance |
Thermal Management Design | Incorporate heat sinks | Increase component durability |
●Thermal Management Considerations in PCB Manufacturing
Effective thermal management is fundamental to the reliability of aerospace PCBs. Proper thermal strategies are key to preventing failures caused by overheating, which enhances both performance and the longevity of the boards.
Thermal Management Techniques:
Heat Sinks and Thermal Vias: Integrating heat sinks or thermal vias in PCB designs effectively transfers heat away from critical components.
Material Selection: Choosing materials with good thermal conductivity helps improve heat distribution. For example, using aluminum or copper as layer materials enhances thermal performance.
Case Study: A leading aerospace company implemented a new thermal management strategy in its PCB designs. By using advanced heat sinks, overheating issues were reduced by 40%, increasing system reliability.
Thermal Management Technique | Description | Result |
Heat Sinks | Used to dissipate heat | Reduced component failure rates |
Material Selection | Utilize thermally conductive materials | Enhanced thermal performance |
Compliance with Military Specifications in Aerospace Manufacturing
In aerospace PCB manufacturing, adherence to military specifications ensures that products meet rigorous performance and safety standards. These standards apply to applications operating in extreme conditions.
●MIL-Spec PCB Standards
Military specification standards outline performance requirements for printed circuit boards used in aerospace applications. These standards cover everything from material selection to testing protocols, ensuring that PCBs can operate reliably in harsh environments.
MIL-PRF-31032: This specification describes performance standards for printed circuit boards intended for military and aerospace applications. Compliance requires extensive testing to ensure reliability under stress.
IPC-6012: This standard outlines requirements for rigid printed circuit boards, emphasizing the necessity for high-quality materials and manufacturing processes.
Importance of Standards:
Safety Assurance: Following MIL-Spec guidelines ensures that PCBs perform reliably under various conditions, protecting personnel and equipment.
Market Access: Many aerospace customers mandate compliance with MIL-Spec standards, making adherence a key factor for market entry.
Standard | Application | Key Requirements |
MIL-PRF-31032 | Military and aerospace applications | Comprehensive testing and validation |
IPC-6012 | Rigid PCBs for aerospace electronics | High-quality materials and processes |
●Testing and Validation Protocols in Aerospace PCB Manufacturing
Testing and validation are indispensable stages in the manufacturing process of aerospace PCBs. Ensuring that PCBs undergo rigorous testing to meet performance standards helps prevent operational failures.
Common Testing Methods:
Environmental Testing: Simulating real-world conditions to evaluate performance under temperature, humidity, and pressure variations.
Electrical Testing: Verifying PCB functionality through techniques such as Automated Optical Inspection (AOI) and X-ray inspection.
Case Study: In a recent spacecraft project, environmental testing of PCBs revealed potential failure points, allowing for redesign before production, thus enhancing overall reliability.
Testing Method | Purpose | Result |
Environmental Testing | Simulate real-world conditions | Identify potential failure points |
Electrical Testing | Verify functionality | Ensure compliance with specifications |
Manufacturing Processes for Aerospace PCBs
Aerospace PCBs Manufacturing
The manufacturing processes for aerospace PCBs are designed to meet the stringent demands of the aerospace industry. These processes ensure that PCBs are reliable, efficient, and capable of operating under extreme conditions.
PCB Fabrication Techniques in Aerospace
PCB fabrication techniques include various methods designed to produce PCBs that fulfill specific aerospace requirements. These techniques involve multiple stages, each fundamental to ensuring the integrity and performance of the final product.
●Material Selection for Aerospace PCB Manufacturing
Material selection is fundamental in aerospace PCB manufacturing, as it directly affects the performance, weight, and thermal characteristics of the boards.
High-Frequency Laminates: Materials like Rogers or PTFE are preferred for high-frequency applications, as they provide superior dielectric properties.
Thermal Management Materials: Selecting materials with high thermal conductivity, like aluminum or copper, improves heat dissipation, which is fundamental to maintaining performance in high-power applications.
Material Type | Properties | Application |
High-Frequency Laminates | Low loss, high dielectric strength | Communication systems |
Thermal Management Materials | High thermal conductivity | Power electronics |
●Advanced Fabrication Technologies
Advancements in fabrication technologies have revolutionized aerospace PCB manufacturing, allowing for increased precision and reduced lead times.
Laser Direct Imaging (LDI): This technology enhances accuracy in patterning, reducing the risk of defects and improving yield rates.
Additive Manufacturing: Techniques like 3D printing enable the creation of complex geometries that traditional methods may not achieve, offering greater design flexibility.
Case Study: A recent initiative implemented LDI technology in PCB fabrication, resulting in a 25% increase in production efficiency and a significant decrease in waste.
Quality Control in Aerospace PCB Manufacturing
Quality control is a fundamental aspect of aerospace PCB manufacturing. Implementing rigorous quality measures ensures that each PCB meets the required specifications and standards.
●Quality Control Measures in PCB Fabrication
Quality control measures include a series of checks and balances throughout the manufacturing process.
Incoming Material Inspection: All materials are inspected for compliance with specifications before they enter the fabrication process.
In-Process Testing: Regular checks during fabrication help identify defects early, reducing rework and ensuring consistency.
Quality Control Measure | Description | Benefits |
Incoming Material Inspection | Verify material compliance | Prevent defects from the start |
In-Process Testing | Monitor quality during fabrication | Maintain consistent quality |
●Importance of Inspection in Aerospace PCB Manufacturing
Inspection protocols are fundamental in maintaining high standards in aerospace PCB manufacturing.
Final Inspection: A comprehensive review of the finished product ensures that all specifications have been met. This includes visual inspections and electrical testing.
Certification Processes: Adhering to industry standards, such as IPC and MIL-Spec, provides confidence in the reliability of the PCB.
Example: In a recent project, a thorough final inspection process identified a potential issue that could have led to operational failures, allowing for timely corrections.
Understanding Aerospace PCB Assembly Processes
The assembly processes for aerospace PCBs are designed to ensure reliability and performance under demanding conditions. A clear understanding of these processes is beneficial for manufacturers aiming to meet the rigorous standards of the aerospace industry.
Types of Aerospace PCB Assembly Techniques
Aerospace PCB assembly uses various techniques to meet the unique requirements of different applications. Each technique offers distinct advantages, and selecting the right one is important for achieving optimal results.
●Surface Mount Technology (SMT) for Aerospace PCBs
Surface Mount Technology (SMT) has gained traction in the aerospace sector due to its efficiency and compactness. This technique allows components to be mounted directly onto the surface of the PCB, minimizing space and enhancing performance.
Advantages of SMT:
High Density: SMT enables a higher component density on the PCB, which is beneficial for space-constrained applications.
Automated Assembly: This technique can be fully automated, leading to faster production times and consistent quality.
Example: A manufacturer implemented SMT in their satellite communication systems, resulting in a 30% reduction in PCB size while maintaining functionality.
Feature | Description | Benefits |
High Component Density | Allows for more components in less space | Optimizes PCB real estate |
Automated Assembly | Reduces human error and increases efficiency | Streamlines production processes |
●Through-Hole Technology (THT) in Aerospace Assembly
Through-Hole Technology (THT) remains relevant in aerospace assembly, particularly for components that require enhanced mechanical strength.
Applications of THT:
Heavy Components: THT is ideal for larger components, such as connectors and relays, that need robust connections to withstand vibrations.
Repairability: The design of THT allows for easier repairs, which can be advantageous for maintenance in aerospace applications.
Case Study: A company specializing in aircraft instrumentation found that using THT for critical connectors improved the longevity of their systems, significantly reducing maintenance intervals.
Feature | Description | Benefits |
Mechanical Strength | Provides a stronger connection for heavy components | Reduces the likelihood of connection failures |
Enhanced Repairability | Facilitates easier maintenance and repair | Cuts down on downtime and costs |
Specialized Tools and Equipment for Aerospace PCB Assembly
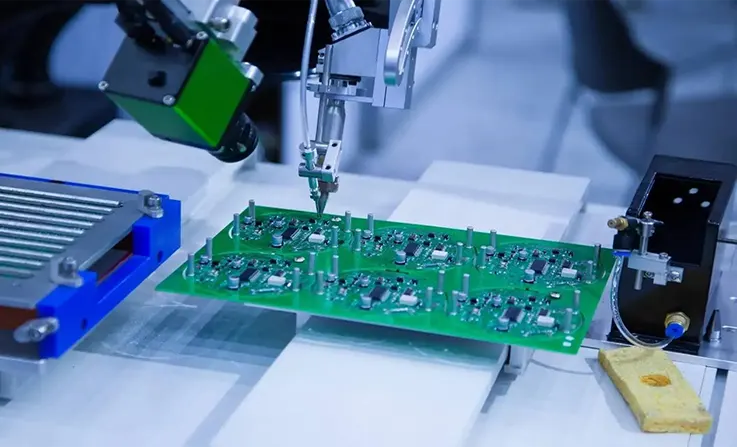
In aerospace PCB assembly, utilizing specialized tools and equipment guarantees precision and reliability. These tools are tailored to meet the unique demands of the aerospace industry, contributing to successful assembly processes.
Essential Assembly Tools for Aerospace PCBs
The choice of assembly tools can significantly impact the quality and efficiency of aerospace PCBs. Here are some of the key tools that facilitate high-quality assembly.
●Soldering Stations
Soldering stations are fundamental in the assembly of aerospace PCBs. They allow for precise application of solder, ensuring secure connections between components.
Types of Soldering Stations:
Digital Soldering Stations: Equipped with temperature control and programmable settings, these stations enhance accuracy in soldering tasks.
Desoldering Tools: Essential for reworking PCBs, these tools help in removing and replacing components without damaging the board.
Example: A manufacturer of avionics equipment utilized advanced digital soldering stations, resulting in a 25% increase in assembly efficiency while maintaining the quality of solder joints.
Feature | Description | Benefits |
Temperature Control | Ensures consistent soldering temperature | Reduces the risk of overheating |
Programmable Settings | Allows customization for different components | Enhances accuracy and repeatability |
●Automated Pick-and-Place Machines for Aerospace Applications
Automated pick-and-place machines are integral to modern aerospace PCB assembly. These machines rapidly and accurately position components onto the PCB, significantly reducing assembly time.
Benefits of Automated Systems:
Speed: High-speed operation allows for the rapid assembly of complex PCBs.
Precision: Automated machines minimize human error, ensuring that components are placed exactly where they need to be.
Case Study: An aerospace manufacturer integrated a state-of-the-art pick-and-place system, leading to a 40% reduction in assembly time for their latest satellite communication boards.
Feature | Description | Benefits |
High-Speed Operation | Quickly places components on PCBs | Increases throughput |
Error Reduction | Reduces chances of misalignment | Enhances overall assembly quality |
Testing Equipment for Aerospace PCB Assembly
Testing is a critical component of aerospace PCB assembly, ensuring that all systems function correctly before deployment. Various testing equipment is used to verify the integrity and performance of assembled boards.
●Optical Inspection Systems
Optical inspection systems are utilized to examine the quality of solder joints and component placement on PCBs. These systems employ cameras and imaging software to detect any anomalies.
Advantages of Optical Inspection:
Real-Time Analysis: Allows for immediate identification of defects, enabling quick adjustments.
Non-Destructive Testing: Maintains the integrity of the board while checking for quality.
Example: A company specializing in military-grade electronics implemented optical inspection systems, resulting in a 30% decrease in assembly errors.
Feature | Description | Benefits |
Real-Time Monitoring | Detects issues during assembly | Facilitates immediate corrective action |
High-Resolution Imaging | Provides detailed images of solder joints | Enhances defect detection capabilities |
●X-Ray Inspection Techniques for Aerospace Assemblies
X-ray inspection is employed to examine hidden solder joints and internal components of aerospace PCBs. This technique is particularly useful for validating connections that are not visible through standard inspection methods.
Applications of X-Ray Inspection:
Hidden Component Verification: Ensures that all internal connections are secure and correctly assembled.
Void Detection: Identifies air pockets within solder joints that could compromise performance.
Case Study: An aerospace firm adopted X-ray inspection technology for their PCB assemblies, which allowed for comprehensive analysis of internal connections, ultimately increasing reliability in their systems.
Feature | Description | Benefits |
Non-Destructive Testing | Allows for thorough inspection without damaging the PCB | Ensures component integrity |
Internal Connection Verification | Confirms that all connections are properly made | Enhances overall system reliability |
Quality Control in Aerospace PCB Assembly
Quality control is a fundamental aspect of aerospace PCB assembly, ensuring that each component meets stringent industry standards. This involves a series of protocols and inspections designed to detect and mitigate any potential issues throughout the assembly process.
Implementing Quality Assurance Protocols in Aerospace Assembly
Establishing robust quality assurance protocols is essential for maintaining high standards in aerospace assembly. These protocols encompass a variety of strategies aimed at ensuring that every stage of production is monitored and evaluated.
●In-Process Inspection Techniques for PCB Assembly
In-process inspection techniques are utilized to identify defects during the assembly process. These methods help catch issues early, minimizing rework and ensuring adherence to specifications.
Types of In-Process Inspections:
Visual Inspections: Technicians conduct routine visual checks to ensure components are correctly placed and soldered.
Automated Optical Inspection (AOI): This technology uses cameras to detect defects such as misaligned components or insufficient solder.
Example: A leading aerospace manufacturer integrated AOI systems, which led to a 20% reduction in errors during assembly, saving time and costs.
Inspection Method | Description | Benefits |
Visual Inspections | Manual checks by trained technicians | Quick identification of obvious defects |
Automated Optical Inspection (AOI) | Uses cameras to detect assembly issues | Enhances accuracy and consistency |
●Final Product Testing Standards in Aerospace Assembly
Final product testing is the last line of defense before an aerospace PCB is deployed. Adhering to established testing standards ensures that products meet the required operational criteria.
Testing Methods:
Functional Testing: Validates that the PCB operates as intended under simulated conditions.
Environmental Testing: Assesses performance under various environmental conditions, such as temperature extremes and humidity.
Case Study: A firm specializing in aerospace communications systems adopted rigorous final testing protocols, resulting in a significant improvement in product reliability and customer satisfaction.
Testing Type | Description | Benefits |
Functional Testing | Tests operational performance | Verifies that all specifications are met |
Environmental Testing | Simulates extreme conditions | Ensures durability and reliability |
Failure Analysis and Troubleshooting in Aerospace PCB Assembly
Even with thorough quality control measures, failures can still happen. Learning how to effectively analyze and troubleshoot these failures supports continuous improvement efforts.
●Common Assembly Defects in Aerospace PCBs
Identifying common defects in aerospace PCBs helps in developing strategies to mitigate them. Typical defects include:
Solder Bridges: Unintentional connections between adjacent pads that can cause short circuits.
Cold Solder Joints: Poorly soldered connections that can lead to intermittent failures.
Example: An aerospace contractor experienced a series of failures due to cold solder joints. By implementing more rigorous soldering training and procedures, they reduced these defects by over 30%.
Defect Type | Description | Causes |
Solder Bridges | Unwanted connections between pads | Excess solder or incorrect placement |
Cold Solder Joints | Weak or insufficient solder connections | Inadequate heating or movement during cooling |
●Root Cause Analysis Methods
Effective root cause analysis is crucial for resolving issues in aerospace PCB assembly. Several methods can be employed:
Fishbone Diagram: A visual tool that helps identify potential causes of a problem by categorizing them into different areas.
5 Whys Technique: A straightforward approach that involves asking “why” multiple times to drill down to the root cause.
Case Study: A company faced repeated failures in their PCB assemblies. By utilizing the 5 Whys technique, they traced the issue back to inadequate training and revised their training programs accordingly.
Analysis Method | Description | Benefits |
Fishbone Diagram | Categorizes potential causes | Provides a structured approach to problem-solving |
5 Whys Technique | Digs deeper into root causes | Simple and effective for identifying underlying issues |
Challenges and Limitations of Aerospace PCB Manufacturing and Assembly
Aerospace PCB Circuit Board Assemblty
Aerospace PCB manufacturing and assembly encounter various challenges that can affect production efficiency, product quality, and compliance with industry standards. Recognizing these challenges is significant for professionals in the field.
Technical Challenges in Aerospace PCB Manufacturing
Aerospace designs often present unique technical challenges that require specialized solutions.
●Managing Complexity in Aerospace Designs
Aerospace PCBs often involve complex designs with densely packed components and intricate circuitry. This complexity can lead to difficulties in manufacturing and assembly, making it essential to adopt advanced design techniques.
Example: In multi-layer PCBs, managing layer stack-up and minimizing signal cross-talk can be tricky. Utilizing advanced CAD tools can help visualize and manage this complexity more effectively.
Challenge | Description | Solution |
Complex Designs | High density and intricate layouts | Use advanced CAD software for visualization |
Layer Stack-Up Management | Ensuring proper signal integrity | Employ simulation tools to predict behavior |
●Addressing Signal Integrity Issues
Signal integrity is a significant concern in aerospace applications, where even minor disturbances can lead to performance degradation. Factors such as electromagnetic interference (EMI) and parasitic capacitance can impact signal quality.
Mitigation Strategies:
Controlled Impedance: Designing PCBs with controlled impedance paths helps maintain signal quality.
Shielding Techniques: Implementing shielding strategies can minimize EMI effects.
Regulatory Limitations in Aerospace Manufacturing
Compliance with aerospace standards is non-negotiable in the manufacturing process. Regulatory limitations can pose challenges for manufacturers aiming to meet these standards.
●Compliance with Aerospace Standards
Manufacturers must adhere to various aerospace standards, such as AS9100 and ISO 9001. These standards set rigorous quality management systems that must be followed.
Example: A manufacturer facing challenges in meeting AS9100 certification implemented a comprehensive quality management system, which streamlined processes and ensured adherence to the required standards.
Standard | Description | Impact |
AS9100 | Quality management for aerospace | Ensures compliance and enhances reliability |
ISO 9001 | General quality management systems | Provides a framework for continuous improvement |
●Impact of Regulatory Changes on Aerospace PCB Manufacturing
Changes in regulations can have significant implications for aerospace PCB manufacturing. Manufacturers need to stay informed about these changes and adapt their processes accordingly.
Example: When new environmental regulations were introduced, a manufacturer had to revise its material sourcing strategies to comply with new standards.
Supply Chain Constraints for Aerospace PCBs
The supply chain for aerospace PCBs is often subject to various constraints that can affect production timelines and material quality.
●Sourcing High-Quality Materials
High-quality materials are indispensable in aerospace applications, as they significantly influence performance and safety. However, sourcing these materials can be challenging due to market fluctuations and supplier limitations.
Solution: Establishing strong relationships with reliable suppliers can mitigate risks associated with material shortages.
Constraint | Description | Strategy |
Material Quality | Need for high-performance materials | Build partnerships with trusted suppliers |
Market Fluctuations | Variability in material availability | Diversify sourcing options to manage risk |
●Ensuring Timely Delivery in Aerospace Manufacturing
Timely delivery is necessary in aerospace manufacturing, as delays can cause major project setbacks. Working closely with suppliers and optimizing logistics can help manage these challenges.
Example: A manufacturer implemented a just-in-time (JIT) inventory system to reduce lead times and improve delivery schedules.
Delivery Challenge | Description | Solution |
Lead Times | Delays in material supply | Implement JIT inventory management |
Logistics Coordination | Managing transportation logistics | Use logistics software for better planning |
Best Practices for Quality Assurance in Aerospace PCB Manufacturing
Quality assurance in aerospace PCB manufacturing is imperative for ensuring that products meet strict performance and safety standards. Adopting best practices in this area can greatly improve reliability and customer satisfaction.
Testing and Inspection Techniques for Aerospace PCBs
Effective testing and inspection methods are the backbone of quality assurance in aerospace PCBs. These techniques help identify defects and ensure that the final products perform as expected.
●Functional Testing Methods
Functional testing verifies that the PCB performs its intended functions under operational conditions. This can include:
In-Circuit Testing (ICT): This method checks for electrical shorts, opens, and correct component placement. ICT is typically performed after assembly but before final encapsulation.
Automated Test Equipment (ATE): Using specialized equipment, manufacturers can automate the testing process, allowing for more extensive testing coverage and quicker results.
Testing Method | Description | Benefits |
In-Circuit Testing | Checks electrical connections | Detects faults before assembly is completed |
Automated Test Equipment | Automates functional tests | Increases efficiency and accuracy |
●Reliability Testing Standards
Reliability testing is imperative in aerospace applications, where failure can result in serious consequences.Common reliability tests include:
Thermal Cycling: This test subjects the PCB to extreme temperature changes to evaluate its performance under stress.
Vibration Testing: By simulating the conditions experienced during flight, this test assesses the mechanical robustness of the assembly.
Reliability Test | Description | Purpose |
Thermal Cycling | Subjecting PCBs to temperature extremes | Assesses thermal stability |
Vibration Testing | Simulating operational vibrations | Evaluates mechanical resilience |
Documentation and Traceability in Aerospace Manufacturing
Comprehensive documentation and traceability contribute significantly to maintaining quality assurance in aerospace manufacturing. They provide a transparent record of processes and materials used throughout production.
●Maintaining Comprehensive Records
Keeping detailed records of every step in the manufacturing process aids in quality control and ensures accountability. This includes:
Material Certifications: Documenting the origin and specifications of materials helps verify compliance with standards.
Production Logs: Detailed logs of the manufacturing process enable manufacturers to trace back through each phase of production if issues arise.
Documentation Type | Purpose | Example |
Material Certifications | Verifies material compliance | Certificates from suppliers |
Production Logs | Tracks manufacturing steps | Daily logs detailing production metrics |
●Importance of Compliance Audits
Regular compliance audits ensure that manufacturing practices align with industry standards and regulations. These audits can help identify areas for improvement and enforce accountability.
Internal Audits: Conducting regular internal audits allows manufacturers to assess their processes and implement corrective actions proactively.
External Audits: Engaging third-party auditors can provide an objective evaluation of compliance with aerospace standards.
Audit Type | Description | Frequency |
Internal Audits | Self-assessment of quality practices | Quarterly or semi-annually |
External Audits | Independent evaluation of processes | Annually or as required by certification standards |
Procurement Strategies for Aerospace PCB Manufacturing and Assembly
Developing effective procurement strategies is central to ensuring that aerospace PCB manufacturing meets quality and reliability standards. This includes evaluating suppliers, negotiating contracts, and understanding market dynamics.
Evaluating PCB Suppliers for Aerospace Applications
Choosing the right supplier is a pivotal step in aerospace PCB manufacturing. A thorough evaluation process ensures that selected suppliers meet the industry’s high standards.
●Key Criteria for Supplier Selection
When selecting suppliers for aerospace PCBs, several criteria should be considered:
Technical Capability: Reviewing a supplier’s capability to produce PCBs that fulfill specific design requirements involves assessing their technology and equipment thoroughly.
Quality Assurance Practices: Suppliers should have established quality management systems in place. This can be verified through their certifications, such as ISO 9001 or AS9100.
Delivery Performance: On-time delivery is a must in aerospace applications. Reviewing a supplier’s history of meeting deadlines helps avoid project setbacks.
Selection Criteria | Description | Evaluation Method |
Technical Capability | Ability to meet design requirements | Equipment audits, capability assessments |
Quality Assurance | Robust quality management systems | Review of certifications and audit results |
Delivery Performance | Consistency in meeting delivery schedules | Historical performance analysis |
●Importance of Certifications and Standards in Aerospace PCB Manufacturing
Certifications and adherence to industry standards are fundamental in ensuring the reliability of aerospace PCBs. Suppliers should hold relevant certifications that confirm compliance with aerospace-specific standards.
AS9100 Certification: This standard focuses on quality management systems specific to aerospace manufacturing, ensuring that processes are aligned with industry best practices.
IPC Standards: The Institute of Printed Circuits (IPC) provides guidelines that cover the quality and reliability of PCB manufacturing processes.
Certification | Description | Benefits |
AS9100 | Quality management for aerospace | Ensures adherence to aerospace requirements |
IPC Standards | Guidelines for PCB quality | Enhances product reliability |
Negotiating Contracts and Pricing for Aerospace PCB Procurement
Effective negotiation strategies are central to achieving favorable terms in contracts and pricing.
●Understanding Cost Drivers
Recognizing the factors that influence costs can help in negotiations. Key cost drivers include:
Material Costs: Fluctuations in raw material prices can significantly impact overall costs. Staying informed about market trends allows for more strategic negotiations.
Labor Costs: The skill level of workers and the labor market conditions can affect pricing. Evaluating suppliers based on their workforce can provide insights into potential costs.
Cost Driver | Description | Impact on Pricing |
Material Costs | Variability in raw material prices | Directly influences overall procurement costs |
Labor Costs | Skill level and availability of workforce | Affects manufacturing efficiency and pricing |
●Long-Term Partnerships vs. One-Time Purchases in Aerospace Procurement
Establishing long-term partnerships with suppliers can yield several benefits compared to one-time purchases.
Stability: Long-term relationships often lead to better pricing and consistent quality, as suppliers are more invested in maintaining a strong partnership.
Collaboration: Working closely with suppliers can facilitate innovation and improvements in design and manufacturing processes.
Procurement Strategy | Description | Advantages |
Long-Term Partnerships | Ongoing supplier relationships | Stability, better pricing, and collaboration |
One-Time Purchases | Single transactions for specific needs | Flexibility, but may lead to higher costs |
Collaboration with Aerospace OEMs
Aerospace PCB Boards
Collaborating with Original Equipment Manufacturers (OEMs) is a strategic aspect of aerospace PCB manufacturing. Understanding and responding to OEM requirements fosters strong partnerships and enhances product development.
Understanding OEM Requirements for Aerospace PCB Manufacturing
Aerospace OEMs have specific needs that must be met for successful collaboration. Engaging with these requirements helps in developing tailored solutions.
●Tailoring Solutions for Specific Needs
Each aerospace project presents unique challenges and requirements. Customizing PCB designs to align with these needs can improve performance and reliability.
Design Specifications: Different aerospace applications demand specific design attributes. Understanding these specifications allows manufacturers to create PCBs that fit seamlessly into the OEM’s overall system.
Material Selection: Tailoring the choice of materials based on the application’s environment—like temperature extremes or exposure to chemicals—ensures that the PCB will perform reliably over its lifespan.
Specific Need | Tailored Solution | Benefits |
Design Specifications | Custom PCB layout and component placement | Enhanced compatibility with OEM systems |
Material Selection | Use of high-temperature or corrosion-resistant materials | Improved reliability in harsh environments |
●Importance of Early Engagement
Engaging with OEMs early in the design process can lead to smoother project execution and better end products.
Design Feedback: Early collaboration allows for continuous feedback from OEMs, helping to refine design parameters and manufacturing processes.
Risk Mitigation: Identifying potential issues early can lead to timely adjustments, reducing the likelihood of costly rework later in the project.
Engagement Stage | Activities Involved | Outcomes |
Early Design Phase | Collaborative design meetings | Enhanced alignment on project goals |
Prototyping | Sharing prototypes for evaluation | Early identification of design flaws |
Building Long-Term Partnerships in Aerospace PCB Supply Chain
Long-term partnerships with OEMs contribute to a more resilient and efficient supply chain. Nurturing these relationships can yield mutual benefits.
●Communication and Feedback Loops
Establishing clear communication channels enhances collaboration and responsiveness.
Regular Check-ins: Scheduled meetings to discuss progress, challenges, and feedback can strengthen the partnership and keep projects on track.
Real-Time Data Sharing: Utilizing technology to share data and updates can streamline processes and facilitate quicker decision-making.
Communication Method | Purpose | Benefits |
Scheduled Meetings | Discuss progress and challenges | Maintains alignment and addresses issues |
Real-Time Updates | Share project status and data | Increases responsiveness and efficiency |
●Joint Development Initiatives
Collaborative development efforts can lead to innovative solutions and improved product offerings.
Co-Innovation Projects: Working together on new technologies or products can lead to breakthroughs that benefit both parties.
Shared Resources: Pooling resources for research and development can enhance capabilities and reduce costs.
Initiative Type | Description | Advantages |
Co-Innovation Projects | Jointly developing new technologies | Accelerates innovation and market readiness |
Shared R&D Resources | Collaborative use of facilities and tools | Reduces overall development costs |
Wrapping Up
The Ultimate Guide to Aerospace PCB Manufacturing and Assembly Excellence
As we wrap up this comprehensive exploration of aerospace PCB manufacturing and assembly, it’s clear that excellence doesn’t just happen—it’s built through continuous improvement and a commitment to quality. By adhering to best practices, leveraging advanced technologies, and fostering strong partnerships, you can navigate the complexities of the aerospace landscape with confidence. Remember, it’s all about staying sharp and adapting to change. Keep pushing the envelope, and your aerospace PCBs will not only meet expectations but soar beyond them!