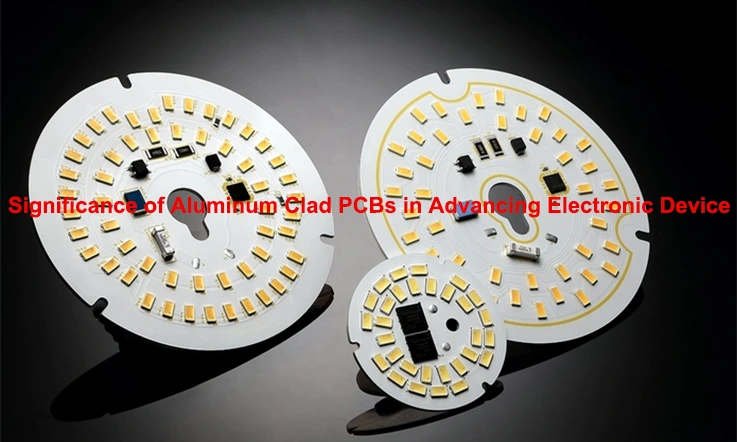
The design of modern electronic devices is a study in balancing conflicting demands: higher power density against stricter thermal limits, and increased functionality against shrinking physical footprints. In this context, the printed circuit board has evolved into a foundational component for thermal management. Aluminum-clad printed circuit boards (PCBs) represent a specialized solution engineered to address these challenges directly. By integrating an aluminum base, these boards provide a highly efficient mechanism for heat dissipation, supporting the development of more reliable and powerful electronics.
The Structure and Function of Aluminum-Clad PCBs
Aluminum-clad PCBs are engineered to address thermal management and structural integrity challenges in electronics. Their composite structure facilitates effective heat dissipation and provides mechanical robustness, offering a dependable platform for high-power applications.
Composition of an Aluminum-Clad PCB
A three-layer construction defines an aluminum-clad PCB. This layered assembly combines thermal transfer properties with electrical isolation to create a high-performance substrate.
●Base Layer (Aluminum): The substrate’s foundation is an aluminum alloy plate. It offers substantial structural support and functions as a heat spreader, efficiently drawing thermal energy away from active components for broader distribution and release.
●Dielectric Layer (Insulating): Positioned between the metal base and the copper foil, this thermally conductive dielectric layer electrically isolates the circuit while enabling efficient thermal transfer from the circuit layer to the aluminum plate.
●Circuitry Layer (Copper): The top layer consists of copper foil, which is etched to form the required circuit traces and pads. It carries electrical signals with minimal resistance, performing the function of a standard printed circuit board.
Performance Attributes and Benefits
This layered design delivers tangible benefits that overcome common engineering limitations, directly influencing the performance, lifespan, and overall cost of an electronic assembly.
●Effective Thermal Dissipation: The aluminum base excels at heat dissipation, maintaining component temperatures within safe operating limits and mitigating the risk of thermal failure. This attribute is especially beneficial for applications such as LED lighting systems and automotive power modules.
●Mechanical Durability: The aluminum substrate provides considerable mechanical strength, enhancing the board’s resilience to physical stress and vibration. This makes it a suitable choice for industrial machinery, aerospace systems, and other demanding operational environments.
●Cost-Effectiveness: By incorporating thermal management directly into the board’s structure, the requirement for separate cooling hardware, such as bulky heat sinks or fans, is often diminished or eliminated. This design simplification can lead to reduced manufacturing and assembly expenses.
●Design Versatility: The construction of aluminum-clad PCBs allows for a high degree of customization. This adaptability supports the development of compact and innovative product forms without the cost escalations associated with specialized thermal management solutions.
Comparative Review of PCB Substrates: Aluminum and Its Alternatives
The selection of a PCB substrate directly influences a product’s thermal behavior, mechanical durability, and overall cost. A direct comparison between aluminum and other common substrate materials clarifies its specific applications and benefits in product design.
vs. Standard FR-4 PCB
FR-4 is composed of a woven fiberglass cloth with an epoxy resin binder and is the most widely used PCB material.
●Thermal Performance: FR-4 acts as a thermal barrier, making it unsuited for high-power designs without secondary cooling measures. In contrast, aluminum is a thermal conductor, actively channeling heat away from components.
●Mechanical Properties: Aluminum offers superior strength, rigidity, and dimensional stability when compared to FR-4.
●Cost Considerations: For standard, low-power electronics, FR-4 presents the lowest material expense. Aluminum boards have a higher initial outlay but can lower the total system cost by obviating the need for separate heat sinks and streamlining assembly.
●Application Focus: FR-4 is designated for general-purpose electronics. Aluminum is specified for designs where heat dissipation is a primary operational requirement.
vs. Ceramic PCB
Ceramic substrates are based on materials like Alumina (Al₂O₃) or Aluminum Nitride (AlN) and are noted for their thermal characteristics.
●Thermal Performance: High-purity ceramics like AlN can exhibit thermal conductivity superior to aluminum, but standard Alumina is often comparable. The main thermal advantage of ceramics is their operational stability at extreme temperatures.
●Mechanical Properties: Ceramics are exceptionally hard and dimensionally stable, yet they are brittle and prone to fracture from shock or vibration. Aluminum is robust and ductile, providing better resistance to impacts.
●Manufacturing Cost: Manufacturing costs for ceramic PCBs are considerably higher than for aluminum due to material and processing expenses.
●Application Focus: Ceramics are reserved for high-temperature, high-frequency, or hermetically sealed applications, such as specialized aerospace or sensor technologies. Aluminum presents a more cost-effective and durable solution for most commercial and industrial high-power designs.
vs. Flexible PCB (Flex PCB)
Flexible PCBs are built on pliable polymer films, such as polyimide, that permit the circuit to be bent or folded.
●Thermal Performance: Standard flex materials are thermal barriers, similar to FR-4, with limited heat dissipation capability.
●Mechanical Properties: The distinction here is one of function. Flex PCBs are selected for their ability to conform to non-planar enclosures and endure dynamic bending. Aluminum PCBs are selected for their absolute rigidity and structural strength.
●Application Focus: Flex PCBs enable three-dimensional product forms found in wearables, cameras, and compact medical instruments. Aluminum is for planar applications that demand a strong, heat-dissipating foundation.
vs. Copper Core PCB
Copper core boards are the closest technological counterparts to aluminum-clad PCBs, utilizing a copper base instead of aluminum.
●Thermal Performance: Copper’s thermal conductivity (~400 W/mK) is nearly double that of aluminum (~220 W/mK), providing the maximum level of heat transfer in a metal-core PCB.
●Physical Properties: Both metals are strong, but copper is substantially denser and heavier than aluminum.
●Cost Factor: The material cost of copper is markedly higher than that of aluminum, positioning copper core PCBs as a premium solution.
●Application Focus: Copper core is designated for the most demanding thermal challenges where cost and weight are secondary considerations. For the majority of designs, aluminum achieves an optimal balance of high thermal performance, low weight, and cost-effectiveness.
Substrate Comparison Summary:
Substrate Type | Thermal Conductivity (W/mK) | Relative Cost | Mechanical Profile |
Aluminum | ~220 | Medium | High (Rigid) |
FR-4 | ~0.3 | Low | Medium |
Ceramic | 20-170+ | High | Very High (Brittle) |
Flexible (FPC) | ~0.3 | Medium-High | Low (Flexible) |
Copper | ~400 | Very High | High (Heavy) |
Advanced Architectures: Multilayer and Hybrid Aluminum PCBs
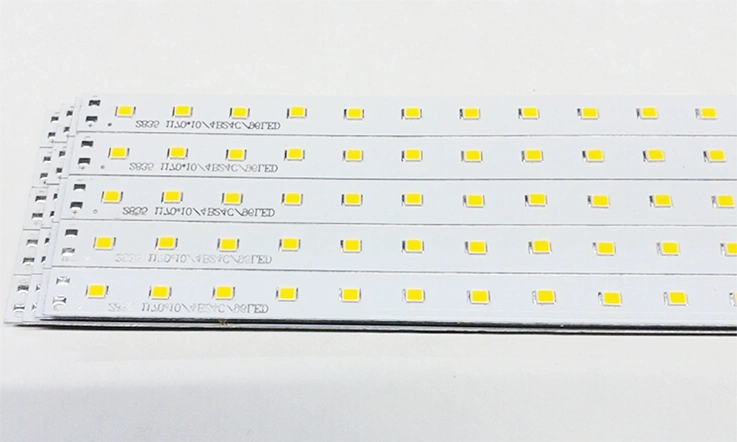
To meet the demand for higher circuit density, aluminum-clad PCB technology has expanded to include sophisticated multilayer and hybrid architectures. These structures apply the thermal management properties of an aluminum core to complex designs, enabling greater system integration.
Dual-Sided and Multilayer Constructions
●Dual-Sided PCBs: This design features copper circuitry on both the top and bottom surfaces of a central aluminum core. A layer of dielectric material is applied to each side for electrical isolation, doubling the available routing area compared to a single-layer board.
●Multilayer PCBs: These constructions expand on the dual-sided format by laminating additional layers of circuitry and dielectric material. The result can be four, six, or more layers of routing paths, all mechanically anchored to the central aluminum core.
●Insulated Via Technology: Layer-to-layer connections are achieved using insulated plated through-holes (vias). Because these must pass through the conductive aluminum core, a specialized process is employed: an oversized hole is drilled, filled with non-conductive resin, and then a standard-sized via is re-drilled through the resin before plating. This method ensures reliable inter-layer connections without shorting to the metal base.
Hybrid Constructions for Mixed-Signal Applications
In fields like high-frequency telecommunications, a single dielectric material may not satisfy all performance needs. Hybrid constructions address this by combining different materials in one stack-up to optimize for varied requirements.
●Targeted Performance: This approach permits the use of a high-performance, low-loss RF dielectric material (e.g., a PTFE-based laminate) for a specific board section dedicated to sensitive radio frequency circuits, thereby preserving signal integrity.
●Integrated Structure: This RF-optimized section is then laminated with a standard thermally conductive dielectric and the aluminum base. The outcome is a single, monolithic PCB that provides exceptional RF performance in one area and robust heat dissipation for other components, like power amplifiers, on the same board.
●System Miniaturization: This technique eliminates the need for multiple interconnected boards, allowing for more compact and highly integrated assemblies in complex communication modules and transceivers.
Embedded Coin Technology for Concentrated Heat Sources
For intense thermal challenges from a highly concentrated heat source, embedded copper coin technology provides a direct thermal shunt to manage localized “hot spots.”
●Direct Thermal Path: This advanced process involves machining a cavity into the aluminum base and press-fitting a solid cylindrical copper “coin” into it. The coin is positioned so its top surface is flush with the surrounding dielectric layer.
●Superior Conductivity: The heat-generating device (such as a laser diode or high-power GaN component) is mounted directly onto this copper coin. As copper’s thermal conductivity is nearly double that of aluminum, this creates a continuous, low-resistance thermal path from the device die straight to the metal core.
●Performance Maximization: This technique delivers an exceptional level of thermal management for the most demanding components, enabling them to operate at their highest capacity without thermal throttling or premature failure. It represents a sophisticated fusion of mechanical and PCB processing.
Mechanical and Thermal Properties
The physical properties of an aluminum-clad PCB’s composite structure directly govern the reliability and lifespan of the electronic assemblies built upon it.
Mechanical Strength and Operational Reliability
The rigidity of the aluminum core provides exceptional physical robustness. This inherent strength prevents the board from flexing, warping, or fracturing under shock and vibration, making it suitable for applications exposed to mechanical stress.
●Vibration Damping: The metal core effectively dampens mechanical vibrations, protecting delicate components and their solder joints from fatigue and failure. This attribute is highly beneficial in automotive, aerospace, and industrial environments.
●Impact Resistance: Compared to brittle substrates like ceramic or standard FR-4, the inherent strength of aluminum offers superior resistance to physical impact, enhancing the overall durability of the end product.
●Stable Component Mounting: The rigid platform ensures that large or heavy components remain securely mounted without placing undue stress on their electrical connections, which contributes to long-term operational reliability.
Table 1: Comparison of Mechanical Properties
Property | Aluminum Core PCB | Standard FR-4 | Ceramic Substrate |
Flexural Strength (MPa) | 300 – 400 | 350 – 450 | 150 – 250 |
Impact Resistance | High | Moderate | Low |
Vibration Damping | Excellent | Moderate | Poor |
Warpage Under Load | Minimal | Moderate | Low |
Thermal Stability and Dimensional Control
An assembly’s ability to remain stable through temperature fluctuations is fundamental to its integrity. The aluminum core offers superior dimensional control, which directly enhances long-term reliability.
●Low Coefficient of Thermal Expansion (CTE): The aluminum base possesses a much lower CTE than conventional FR-4 substrates. This means that as the board undergoes thermal cycling, it expands and contracts substantially less, reducing the mechanical stress exerted on all attached components.
●Solder Joint Reliability: This dimensional stability has a pronounced effect on the reliability of solder joints. By minimizing the CTE mismatch between the PCB and its components (especially large ceramic devices or ICs), it mitigates a primary cause of solder joint fatigue and failure over the product’s lifespan.
●Prevention of Warpage: The inherent rigidity of the aluminum prevents the board from warping or bowing during high-temperature assembly processes like reflow soldering or during operation, ensuring a flat, stable surface for components.
Table 2: Thermal and Dimensional Stability Comparison
Property | Aluminum Core PCB | Standard FR-4 | Ceramic Substrate |
Coefficient of Thermal Expansion (ppm/°C) | 17 – 23 | 70 – 90 | 6 – 8 |
Max Operating Temperature (°C) | 130 – 150 | 110 – 130 | 200+ |
Thermal Conductivity (W/m·K) | 1.0 – 3.0 | 0.3 – 0.4 | 20 – 200 |
Warpage During Reflow | Minimal | Moderate | Low |
Electrical Performance Characteristics
The construction of an aluminum-clad PCB directly enhances its electrical performance, influencing its capacity for high-current applications and its effect on signal integrity.
High-Current Handling and Voltage Drop Minimization
The option to use heavier copper weights enables aluminum-clad PCBs to manage high currents effectively. This capability supports high-power applications by preventing trace overheating and minimizing voltage drops that would otherwise diminish device efficiency.
●Enhanced Ampacity: Because the board rapidly dissipates heat from the copper traces, the traces can sustain higher currents (ampacity) for a given cross-sectional area compared to those on a thermally insulating FR-4 substrate.
●Stable Power Delivery: By minimizing voltage drops along high-current paths, the board helps ensure that components receive a stable supply voltage, which permits smooth operation in power conversion and motor drive applications.
●Design for Power Density: This high-current capability makes it possible to create more compact power circuits, as wider traces or additional copper planes may become unnecessary, contributing to overall system miniaturization.
Signal Integrity and EMI Shielding
When connected to the system ground, the aluminum base functions as an effective ground plane and electromagnetic shield—a valuable, integrated feature for many electronic designs.
●EMI Suppression: The grounded metal core helps to contain electromagnetic emissions from high-frequency circuits, reducing interference with nearby electronics and aiding in efforts to meet regulatory EMI standards.
●Improved Noise Immunity: The shield also protects sensitive analog or digital circuits on the board from external sources of electromagnetic noise, resulting in a cleaner signal environment and an improved signal-to-noise ratio.
●Low-Inductance Ground Path: The large, solid aluminum plate provides a low-inductance ground reference, which benefits high-speed digital circuits by minimizing ground bounce and other signal integrity disruptions.
Advanced Fabrication and Manufacturing Processes
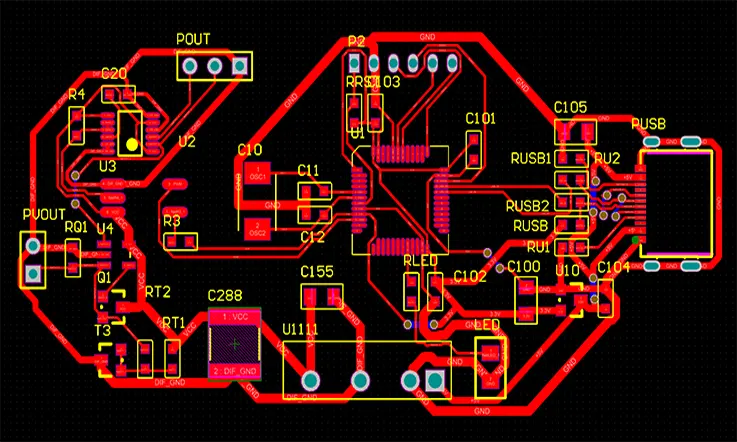
The fabrication of aluminum-clad PCBs combines precision machining with chemical processing. This requires process controls more stringent than those for standard FR-4 boards to ensure the final product meets its performance specifications.
Overview of the Manufacturing Sequence
●Material Preparation: The process begins with cutting the aluminum sheet to panel size and subjecting it to chemical cleaning and surface roughening treatments. This ensures optimal adhesion between the aluminum and the dielectric layer.
●Precision Lamination: In a lamination press, the dielectric layer and copper foil are bonded to the prepared aluminum base under precisely controlled heat and pressure. This process requires uniform pressure and temperature to achieve a void-free, durable bond.
●Circuitization and Finishing: Following lamination, the panel undergoes processes like circuit imaging and etching, but with parameters modified for the metal base. The final steps include applying a solder mask, a surface finish (e.g., ENIG, HASL), electrical testing, and final routing or V-scoring for depanelization.
Table 1: Key Parameters in Manufacturing Stages
Process Stage | Key Parameters | Typical Values |
Surface Treatment | Surface Roughness (Ra) | 0.3 – 0.8 µm |
Lamination | Temperature / Pressure | 170–200 °C / 15–25 kg/cm² |
Imaging & Etching | Etch Factor | 2:1 – 3:1 |
Surface Finishing | Common Finishes | ENIG, HASL, OSP |
Final Routing | V-Scoring Depth / Width Tolerance | ±0.05 mm |
Best Practices for High-Yield Fabrication
High-yield fabrication and dependable product quality depend on adherence to established best practices. These methods control the numerous variables found in processing composite materials.
●Process Control: Implementing Statistical Process Control (SPC) for designated manufacturing variables, such as lamination pressure and drilling speeds, ensures product uniformity across production runs and delivers a stable, repeatable performance to the customer.
●Specialized Tooling: Utilizing drill bits and router bits specifically designed for metal-laminate composites is necessary. This produces clean holes and edges, free from burrs or delamination that could compromise the product’s long-term reliability.
●Automated Inspection: Employing Automated Optical Inspection (AOI) after etching and Automated X-ray Inspection (AXI) for multilayer boards helps to identify defects early. This is a quality assurance measure that prevents flawed boards from reaching the customer and improves overall product integrity.
Table 2: Process Control and Quality Assurance Metrics
Parameter / Method | Best Practice Value / Range | Purpose |
Lamination Pressure SPC | ±1.5 kg/cm² | Ensures bond quality and consistency |
Drilling Speed | 80–120 m/min (Al-based materials) | Minimizes delamination, burrs |
Tool Wear Monitoring | Tool life ≤ 500 hits | Prevents edge chipping |
AOI Defect Detection | ≥ 95% detection rate | Early detection of shorts/opens |
AXI Accuracy (µm) | ±10 µm for BGA/SMD joints | High precision defect verification |
Have a complex multilayer design? Our advanced manufacturing processes can bring your vision to life with precision. Upload your Gerber files now for an instant quote and DFM analysis.
Common Challenges and Innovative Solutions in Production
The material composition of aluminum-clad PCBs presents distinct manufacturing hurdles. Addressing these effectively requires experienced process engineering and specialized equipment.
Navigating Common Manufacturing Hurdles
Several hurdles are inherent to the production process, demanding precise control and expert knowledge to mitigate.
●Delamination Risk: Establishing a robust, permanent bond between the smooth, non-porous aluminum surface and the polymer-based dielectric is a primary difficulty, requiring meticulous surface preparation and lamination control.
●Drilling Complications: Drilling through the dissimilar materials of aluminum and FR-4-like dielectrics can cause issues like resin smear on inner layers or burrs on the aluminum surface. If not managed properly, both situations can compromise via reliability.
●Dimensional Tolerance Control: During the high-temperature lamination cycle, managing the different rates of thermal expansion between the aluminum, copper, and dielectric layers is necessary to prevent built-in stress and maintain tight dimensional tolerances.
Leveraging Innovation for Process Optimization
Advanced manufacturing techniques are employed to address these specific hurdles, streamlining production and enhancing final product quality.
●Advanced Surface Preparation: Directly countering the risk of delamination, techniques like plasma etching or advanced chemical etching create a micro-roughened surface on the aluminum. This dramatically increases the surface area for mechanical bonding with the dielectric, improving adhesion reliability.
●Plasma De-smear and Hole Cleaning: In response to drilling complications, a plasma treatment process is often used to clean newly drilled holes. This removes any resin residue (smear) from inner-layer copper pads and ensures a reliable electrical connection after plating.
●Laser Direct Imaging (LDI): Using LDI instead of traditional phototools for circuit imaging allows for much finer feature resolution and tighter registration accuracy. This enables the production of more complex circuit designs and aids in maintaining strict dimensional control.
Strategic Design and Assembly (DFM/DFA) Considerations
The performance of a system using an aluminum-clad PCB extends beyond the board itself, encompassing component selection and the assembly process. Optimizing a design for both manufacturing and assembly (DFM/DFA) is the direct path to a more reliable and cost-effective final product.
Component Layout for Optimal Thermal Pathways
Component placement on an aluminum-clad PCB is a thermal design task. The objective is to engineer the shortest, most efficient thermal path from any heat source to the aluminum base.
●Prioritize Heat Sources: Identify and position the main heat-generating components first. Ensure their thermal pads are sufficiently large and provide a direct, low-resistance path to the underlying copper plane.
●Utilize Thermal Vias: For surface-mount components, place an array of small, conductive vias directly in their thermal pads. These vias act like pillars, efficiently conducting heat through the dielectric layer to the aluminum core, which enhances component lifespan and system stability.
●Avoid Thermal Crowding: Distribute heat-generating components across the board’s surface rather than clustering them. This allows the aluminum base to spread heat more effectively and prevents the formation of a single, intense hot spot.
Planning for Efficient and Reliable Assembly
Anticipating the physical characteristics of aluminum-clad PCBs during the design phase leads to more efficient and reliable assembly.
●Reflow Profile Adjustment: The board’s high thermal mass requires a carefully tuned reflow soldering profile. The preheating stage must be long enough for the entire board, including the aluminum core, to reach a uniform temperature. This prevents components from experiencing thermal shock and ensures all solder joints reflow properly.
●Depanelization Method: The rigidity of the aluminum makes V-scored lines difficult to break and can stress nearby components. For high-reliability applications, routing (milling) boards out of the panel is often the preferred method for a cleaner, stress-free edge.
●Fiducial and Tooling Hole Placement: The correct placement of fiducial markers for optical alignment by pick-and-place machines, along with tooling holes for securing the panel in fixtures, provides the foundation for a smooth and accurate automated assembly process.
Facing thermal or assembly challenges with your design? Our engineering team offers a complimentary DFM (Design for Manufacturability) assessment to help you optimize your design, reduce costs, and enhance reliability.
Procurement Strategy and Total Cost of Ownership
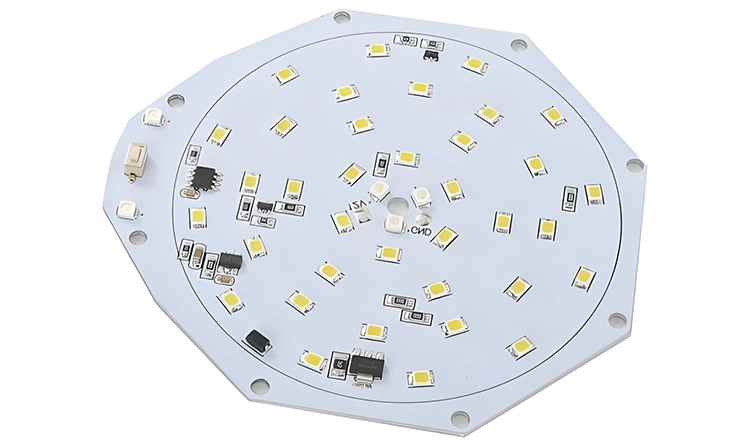
An informed procurement decision for aluminum-clad PCBs looks beyond per-unit price to the total cost of ownership (TCO). This strategic approach evaluates a supplier’s capabilities against the product’s entire lifecycle.
Selecting a Qualified Supplier
Identifying a suitable supplier requires an evaluation that extends beyond price to assess technical capability, quality systems, and service responsiveness.
●Technical Capability Audit: Assess the supplier’s verified ability to handle the specific technologies a design requires. This includes their range of available dielectric materials, proven experience with multilayer constructions, and published tolerance capabilities.
●Quality System Verification: Confirm the supplier holds relevant industry certifications, such as ISO 9001 and the stringent IATF 16949 for the automotive supply chain. These serve as objective evidence of robust and repeatable process controls.
●Service and Support Responsiveness: Evaluate the supplier’s customer service and technical support. A responsive, knowledgeable supply source can accelerate problem-solving, reduce project risks, and prevent costly errors.
Cost-Benefit Analysis and Long-Term Advantages
A comprehensive analysis reveals the true economics of aluminum-clad PCBs. Although the initial board cost may be higher than for conventional substrates, the long-term savings are often substantial.
●System-Level Cost Reduction: The integrated thermal management of an aluminum-clad PCB can reduce or eliminate the need for other components like fans, large heat sinks, and thermal interface materials, along with their associated assembly labor, thus lowering the total bill of materials (BOM).
●Reliability and Warranty Savings: A lower field failure rate, attributable to better thermal management, translates directly into reduced warranty claims and repair costs, and serves to protect brand reputation.
●Performance-Enabled Value: In many cases, the superior performance enabled by an aluminum-clad PCB (e.g., brighter LEDs, more powerful motor drives) allows the final product to command a higher price or capture greater market share, providing a direct return on the investment in the advanced substrate.
Applications Across High-Technology Sectors and Future Trajectory
The practical benefits of aluminum-clad PCBs have established them in numerous demanding industries. Their application is expanding, driven by the overarching technological trends of increased efficiency and power density.
Established Industrial Use Cases
In many sectors, aluminum-clad PCBs have transitioned from a niche choice to a standard solution for addressing thermal and reliability requirements.
●Automotive Systems: These boards are a component of modern vehicle operation, found in high-power systems like LED headlights, electric power steering controllers, and the complex power electronics within electric vehicle (EV) battery management systems and motor inverters.
●Industrial Power and Automation: In factory settings, they provide a robust platform for variable frequency motor drives, high-power welding equipment, and uninterruptible power supplies (UPS), applications that demand reliable performance under heavy electrical and thermal loads.
●Solid-State Lighting: The high-power LED lighting industry, from architectural lighting to horticultural applications, is built upon aluminum-clad PCBs. They function to extract heat from the LED dies, which sustains brightness, efficiency, and long operational life.
Emerging Market Trends
The market for aluminum-clad PCBs is expanding, propelled by global movements toward energy efficiency and electrification. This growth fuels further innovation and creates new applications for the technology.
●Widespread Electrification: Beyond EVs, the electrification of systems in aerospace, heavy machinery, and other sectors is creating new demand for compact, reliable, and thermally efficient power conversion electronics—an ideal application space for aluminum-clad PCBs.
●Wide-Bandgap Semiconductors: The increasing adoption of Gallium Nitride (GaN) and Silicon Carbide (SiC) power devices creates more concentrated heat loads. This makes advanced thermal solutions, such as the previously discussed aluminum boards with embedded copper coins, an enabling technology for the next generation of power electronics.
●Telecommunications Infrastructure: The rollout of 5G and future wireless technologies requires base stations with more powerful and densely packed amplifiers. The hybrid aluminum-clad PCBs detailed earlier, which manage intense heat while preserving RF signal integrity, are a growing part of this sector.
Conclusion: A Substrate for Advanced Electronics
As electronic systems advance toward higher performance within more compact forms, aluminum-clad PCBs provide a distinct advantage. Their capacity to manage thermal energy, combined with their mechanical robustness, allows for the design of more reliable and powerful devices. This makes them a feature in applications ranging from electric vehicles and 5G infrastructure to advanced lighting and renewable energy systems.
However, realizing these benefits is not inherent to the material alone. As this article has detailed, achieving superior outcomes hinges on an integrated approach that encompasses thoughtful design, advanced fabrication techniques, and strategic procurement. A manufacturing supplier who demonstrates mastery of this entire ecosystem is the final element in unlocking the full potential of this versatile technology.
Ready to elevate your product’s performance? Contact us today. Our team of experts will partner with you to begin your high-performance aluminum-clad PCB customization journey, building a solid foundation for your exceptional products.
The Hallmarks of a Strategic Manufacturing Partner
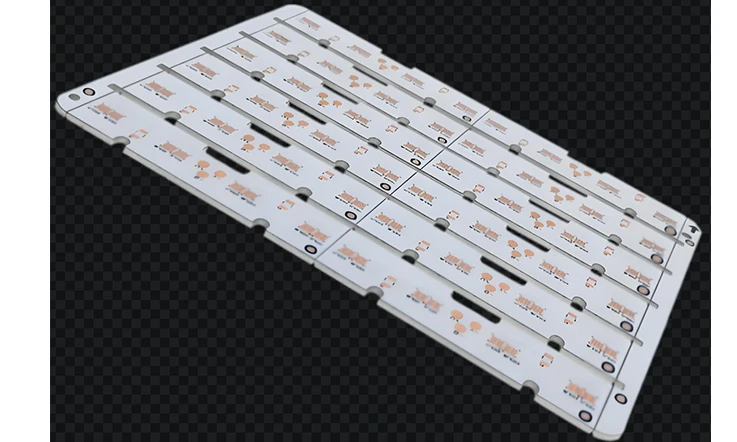
Understanding the complexities of aluminum-clad PCBs is the first step; selecting a manufacturer with the proven capability to produce them to the highest standards is the next. A strategic manufacturing relationship is defined by tangible strengths that translate directly into project success.
A Systematic Approach to Quality
Quality is not a final goal, but a system embedded in every step. Each board produced is the output of a rigorously controlled process designed for predictable and reliable outcomes, ensuring the final product performs as expected in the field.
●Certified Processes: Operations are certified under stringent industry standards, including ISO 9001 for quality management and IATF 16949 for the demanding automotive sector, providing objective evidence of disciplined process controls.
●Advanced Inspection: A suite of advanced inspection technologies is employed, from Automated Optical Inspection (AOI) for circuit accuracy to cross-section analysis and thermal shock testing to validate structural integrity and long-term reliability.
●Material Traceability: Complete traceability is maintained for all raw materials, from the specific batch of aluminum alloy to the dielectric and copper foil, providing an unbroken chain of quality assurance.
Focus on Total Cost of Ownership (TCO)
A forward-thinking pricing philosophy centers on delivering superior value and fostering long-term supply chain stability, with a focus on optimizing the Total Cost of Ownership (TCO), not just the upfront unit price.
●Process Efficiency: Investment in modern, efficient manufacturing processes minimizes waste and reduces operational overhead, allowing for competitive pricing.
●Value-Added DFM: Proactive Design for Manufacturability (DFM) analysis helps identify and correct potential design issues before production begins, preventing costly delays and redesigns.
●Transparent Quotations: Clear, detailed quotations with no hidden fees enable fully informed procurement decisions.
Dependable and Punctual Delivery
In today’s market, on-time delivery is non-negotiable. A production system geared towards predictability and dependability is a requirement for any serious supply chain.
●Intelligent Scheduling: An intelligent production scheduling system provides realistic lead times and optimizes workflow, ensuring projects stay on track.
●Robust Supply Chain: Strong relationships with a network of pre-qualified material suppliers mitigate the risk of delays caused by raw material shortages.
●Proactive Communication: From order confirmation to shipment, regular status updates provide a clear view of a project’s progress.
Expert-Led, Proactive Service
Superior service extends beyond simple order fulfillment to include accessible expertise and proactive support throughout a project’s lifecycle.
●Dedicated Engineering Support: An accessible team of experienced engineers can provide timely and accurate assistance for pre-sale technical queries or post-delivery support.
●Streamlined Onboarding: A refined process for new projects, from Gerber file analysis to final confirmation, is designed to be as smooth and efficient as possible.
●Responsive Problem Solving: Should any challenges arise, they are addressed with urgency and transparency, with a focus on collaborative work to find the optimal solution.
Comprehensive Manufacturing Capabilities
A facility should be equipped to handle the full spectrum of aluminum-clad PCB technologies, from standard single-layer boards to the most complex constructions.
●Multilayer and Hybrid Expertise: There should be proven, high-yield capabilities in manufacturing complex multilayer boards with insulated vias, as well as hybrid constructions that combine different dielectric materials.
●Advanced Thermal Solutions: Hands-on experience with advanced thermal management techniques, including the precision manufacturing of boards with embedded copper coins, is a sign of a top-tier fabricator.
●Material Versatility: The ability to work with a wide array of thermally conductive dielectric materials and source specific substrates meets the unique performance requirements of any application.
Frequently Asked Questions (FAQs)
1.What distinguishes Aluminum-Clad PCBs from other types?
They feature an integrated aluminum base that provides superior heat dissipation and mechanical strength, unlike standard FR-4 boards which are thermally insulating and less rigid.
2.How do aluminum-clad PCBs improve thermal performance?
The aluminum core rapidly draws heat away from critical components and spreads it across the board’s surface. This prevents dangerous overheating, allowing components to run cooler and more reliably.
3.Are aluminum-clad PCBs suitable for designs with high component density?
Yes, particularly multilayer versions. They allow for dense, complex circuit layouts while using the central aluminum core for effective heat management, making them ideal for compact, high-power designs.
4.What should be considered when designing a circuit on an aluminum-clad PCB?
The top consideration is thermal layout: place hot components to ensure a direct heat path to the aluminum base. Also, the assembly reflow profile must be adjusted to account for the board’s high thermal mass.