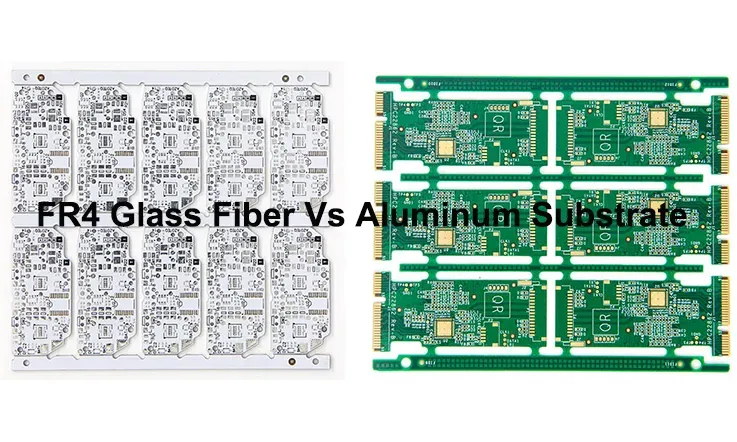
When you’re working with printed circuit boards (PCBs), it’s not just about connecting circuits—choosing the right materials is half the battle. In the world of PCB design and manufacturing, Aluminum Substrates and FR4 Glass Fiber Boards are two of the most common materials. But how do you decide which one’s the right pick for your project? Let’s dive into the nitty-gritty and look at what makes these materials tick, from thermal management to cost efficiency and everything in between.
Understanding the Basics of Aluminum Substrate and FR4 PCB Materials
Choosing between Aluminum Substrates and FR4 Glass Fiber Boards requires a solid understanding of what each material brings to the table. These aren’t just fancy names; the material selection could make or break your next big project. Whether you’re dealing with a high-power device or just trying to keep costs in check, each option comes with its own set of strengths and weaknesses.
What is an Aluminum Substrate?
When we talk about aluminum substrates, we’re essentially looking at a material that’s all about managing heat. These PCBs are built with an aluminum base, which helps them handle the intense thermal load that comes with powering high-output devices like LED lighting systems or industrial power supplies. This isn’t your everyday PCB material; it’s designed to move heat away from critical components, keeping your board from burning out when things get hot.
Key Properties of Aluminum Substrates
The standout feature of aluminum PCBs is their thermal conductivity. Aluminum acts as a heat sink, dissipating heat much faster than FR4 can. This keeps components cooler, which in turn extends their lifespan. These boards are also known for their mechanical strength, making them an ideal choice when durability is key. You don’t want your board warping or breaking down under stress, and aluminum is sturdy enough to handle that pressure.
Applications of Aluminum PCBs in Power Electronics
Thanks to their heat dissipation capabilities, aluminum PCBs shine in high-temperature environments. They’re commonly used in power electronics, especially in devices like LED lights, where thermal performance is a must. LED lighting systems can generate a lot of heat, and without proper thermal management, they’ll flicker out faster than you can say “burnout.” Aluminum substrates ensure these devices can handle the heat—literally.
Case Study 1: Automotive Electronics
An automotive manufacturer faced overheating issues with ECU boards made from FR4. The components were exposed to high temperatures near the engine, leading to frequent failures. By switching to aluminum substrate PCBs, the manufacturer observed a temperature reduction of 20°C during peak operations. This upgrade not only enhanced the reliability of the ECUs but also reduced maintenance costs by 30%.
Case Study 2: LED Lighting Systems
A company producing high-powered LED panels struggled with heat dissipation, resulting in frequent LED failures. Using FR4 boards, they found that the heat generated exceeded what the material could handle. Transitioning to aluminum substrates allowed for efficient heat dissipation, resulting in longer LED life and improved product performance. This shift reduced customer returns by 25%, demonstrating the value of selecting the right PCB material.
What is FR4 Glass Fiber Board?
Now, onto the more traditional side of things: FR4. FR4 is a composite material made from woven fiberglass cloth and epoxy resin. It’s the go-to for standard PCBs, offering a great balance of electrical insulation, mechanical strength, and affordability. You’ll see FR4 used across a wide range of applications, from consumer electronics to telecommunications. Think of it as the workhorse of the PCB world.
Key Properties of FR4 PCBs
FR4 PCBs excel in providing electrical insulation and mechanical durability. While they don’t manage heat as efficiently as aluminum substrates, they’re still plenty strong. The fiberglass core adds mechanical resilience, making it resistant to warping or flexing under stress. The big win here, though, is in cost—FR4 boards are generally more affordable than their aluminum counterparts, making them the popular choice for consumer electronics.
Applications of FR4 PCBs in Consumer Electronics
FR4’s low cost and reliable mechanical properties make it the material of choice in products like smartphones, computers, and other consumer electronics. These devices don’t generate the same heat levels as industrial power supplies or LED systems, so FR4 is more than capable of handling the job. It’s a solid choice for anyone looking to keep costs down without sacrificing too much on performance.
Process Differences Between Aluminum Substrate and FR4 Glass Fiber Board
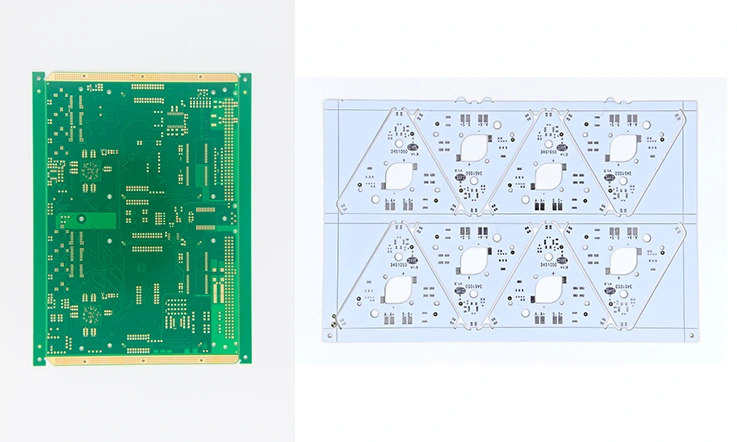
The manufacturing process for both aluminum PCBs and FR4 PCBs involves some key differences that can affect your final decision. If you’re a PCB designer or a manufacturer, these details are worth knowing because the production line isn’t quite the same for both materials.
Manufacturing Process of Aluminum PCBs
Creating an aluminum PCB is a little more involved than making your typical FR4 board. The aluminum base is paired with an insulating layer (usually ceramic polymer) that separates the conductive layer from the base metal. This structure not only helps with thermal management but also adds extra steps in the production process. As a result, aluminum PCBs tend to be more expensive to produce, but they pay off when you’re working with high-power devices that need top-notch heat dissipation.
Manufacturing Process of FR4 PCBs
In contrast, FR4 PCB manufacturing is pretty straightforward. The fiberglass and epoxy combination is easy to work with, and the manufacturing techniques for FR4 have been refined over decades. This makes FR4 PCBs much quicker and cheaper to produce compared to aluminum boards. If you’re cranking out consumer electronics where the focus is more on keeping costs low, FR4’s simplicity is a clear advantage.
Technical Comparison: Aluminum Substrate vs. FR4 Glass Fiber PCB
Performance Comparison: Thermal Management and Heat Dissipation
Now, let’s talk about thermal management—one of the biggest differentiators between aluminum substrates and FR4 glass fiber boards. When it comes to keeping your PCB cool, these two materials are worlds apart.
Thermal Conductivity of Aluminum Substrates
If heat is your main concern, aluminum substrates are the way to go. With their superior thermal conductivity, aluminum boards can disperse heat at a much faster rate than FR4. This makes them an excellent choice for high-power applications, where keeping the system cool can mean the difference between smooth sailing and catastrophic failure. Heat dissipation is the name of the game here, and aluminum plays it well.
Heat Management in FR4 Glass Fiber Boards
On the flip side, FR4 PCBs don’t quite measure up when it comes to heat management. They’re perfectly fine for low-power applications, but if your project is generating a lot of heat, FR4 isn’t going to cut it. That said, not every project requires industrial-grade thermal performance, so unless you’re dealing with LEDs or power electronics, FR4 might still be a good fit.
Property | Aluminum Substrate | FR4 Glass Fiber |
Thermal Conductivity | High (1.0W/mK – 9.0W/mK) | Low (0.3W/mK) |
Heat Tolerance | Excellent | Moderate |
Operating Temperature Range | -40°C to 150°C | -40°C to 140°C |
Heat dissipation is one of the critical factors that differentiate aluminum substrate PCBs from FR4 PCBs. Aluminum substrates can handle high heat loads and are preferred in applications where heat buildup could damage components, such as high-power LEDs and solar panels. In contrast, FR4 PCBs can handle moderate heat but require additional cooling systems like heat sinks or fans for high-power applications.
Mechanical and Electrical Properties: Which Is More Durable?
Beyond thermal performance, you’ll also need to consider the mechanical properties of your PCB. Durability and electrical performance play a huge role in ensuring your board can handle the stresses of its working environment.
Mechanical Strength of Aluminum PCBs
Aluminum substrates are tough. They’re not just good at handling heat—they’re also incredibly strong, offering mechanical durability that keeps the board from bending or cracking under pressure. This makes them a solid choice for industrial electronics, where durability is just as important as thermal management.
Mechanical Strength of FR4 PCBs
While not as strong as aluminum, FR4 boards still provide decent mechanical strength thanks to the fiberglass core. They’re more than capable of withstanding the rigors of most consumer electronics, but if you’re working in an industrial environment where things can get rough, aluminum PCBs are the better choice.
Cost Efficiency: Aluminum PCB vs FR4 PCB
When it comes down to it, the cost efficiency of your PCB is going to be a major factor. Whether you’re designing a PCB for a high-power application or for mass production in consumer electronics, price matters.
Is Aluminum PCB Cost-Effective for High-Power Applications?
In high-power environments where thermal management is critical, the extra cost of aluminum PCBs can be justified. Sure, they’re more expensive than FR4 boards, but the fact that they handle heat so well makes them worth the investment in the right scenarios. You’ll save yourself from expensive component failures and downtime, making aluminum a solid pick if you need serious heat dissipation.
Comparing the Cost of FR4 PCBs for Consumer Applications
If cost is your primary concern and you’re not dealing with high-heat environments, FR4 PCBs are the way to go. They’re much cheaper to produce and perform just fine in most consumer applications. If you’re building devices like smartphones or tablets, FR4 will do the job without burning a hole in your pocket.
More Detailed Technical Insights
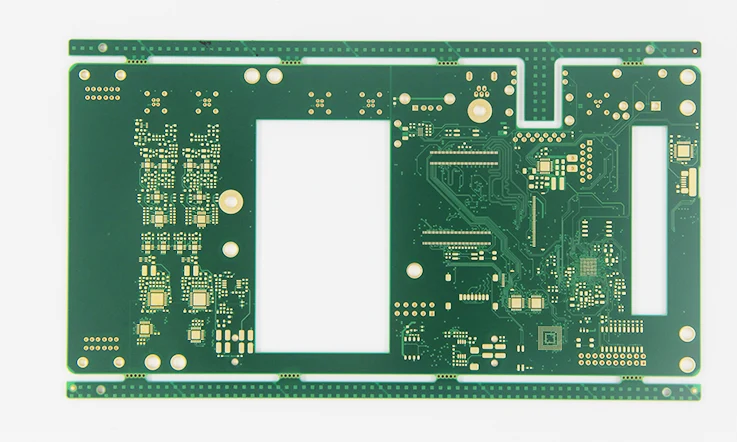
To dive deeper into the technical specifics of both aluminum substrate and FR4 glass fiber PCBs, we’ll explore their material properties, focusing on thermal conductivity, electrical insulation, and mechanical strength.
Aluminum Substrate PCB Technical Breakdown
Aluminum substrate PCBs are well-known for their superior heat dissipation capabilities, which come from the inherent properties of aluminum as a metal. The thermal conductivity of aluminum can range from 1.0 to 9.0 W/mK, significantly higher than FR4’s average of 0.3 W/mK. This allows aluminum PCBs to maintain lower operational temperatures, thereby extending the lifespan of components. For instance, in high-power LED applications, aluminum substrates can help prevent thermal runaway, a scenario where excessive heat damages components, leading to cascading failures. In the automotive industry, these substrates are often chosen due to their ability to handle heat-heavy environments, ensuring consistent performance in engine control units (ECUs).
Aluminum substrates also offer mechanical strength, making them ideal for environments that face physical stress, such as automotive electronics. The dielectric layer between the copper and the aluminum base provides insulation and heat transfer, ensuring that the electrical performance remains uncompromised even at elevated temperatures.
FR4 Glass Fiber PCB Technical Breakdown
FR4 glass fiber boards, while not designed for heavy thermal loads, are prized for their electrical insulation and mechanical durability. With a dielectric strength of about 20kV/mm, FR4 is a go-to material for applications that require reliable electrical insulation, such as consumer electronics and communication devices.
In terms of material composition, FR4 consists of woven glass fibers that are embedded in an epoxy resin matrix. This unique composition allows it to maintain dimensional stability and offers resistance to moisture, making it suitable for environments where humidity or water exposure is a concern. Moreover, FR4 boards are versatile, handling both single-layer and multi-layer PCB designs, providing flexibility for more complex circuit configurations.
In-Depth Comparison with Competing Materials
For a more holistic understanding, we’ll now compare aluminum substrates and FR4 glass fiber with other alternative materials commonly used in PCB manufacturing, such as ceramic and flexible PCBs.
Ceramic Substrates vs Aluminum PCBs
Ceramic substrates, like aluminum, are known for their excellent thermal conductivity, often exceeding 150 W/mK. They are typically used in high-end RF and microwave applications where high-frequency stability is a requirement. However, ceramic PCBs are significantly more expensive and brittle, making them prone to mechanical failure in high-vibration environments, unlike the more robust aluminum substrates.
For applications where extreme heat and high-frequency signals are the primary concerns, ceramic PCBs might be the ideal choice, but they lack the cost-effectiveness and mechanical durability that aluminum substrates provide, particularly in automotive and industrial electronics.
Flexible PCBs vs FR4
Flexible PCBs, made from materials like polyimide, provide versatility that neither aluminum nor FR4 can match. They are ideal for applications requiring bending and flexing, such as wearable electronics or medical devices. However, they cannot dissipate heat as effectively as aluminum substrates, nor do they offer the electrical insulation and stiffness of FR4 boards.
In contrast, FR4 glass fiber boards are more suited for rigid, multi-layer designs in environments where physical flexibility is not a priority, but dimensional stability and cost efficiency are crucial factors.
Comparative Analysis Table
To help visualize the differences among these materials, here’s a comparison table highlighting their key features:
Material | Thermal Conductivity (W/mK) | Electrical Insulation | Mechanical Strength | Cost | Best For |
Aluminum Substrate | 1.0 – 9.0 | Moderate | High | Moderate | High-power applications (LEDs, automotive) |
FR4 Glass Fiber | 0.3 – 0.4 | High | Moderate | Low | Consumer electronics, communication devices |
Ceramic | 150+ | High | Low (Brittle) | High | High-frequency RF, microwave applications |
Flexible PCB | 0.3 | Moderate | Low | Moderate | Wearables, medical devices |
How Choosing Between Aluminum Substrate and FR4 PCB?
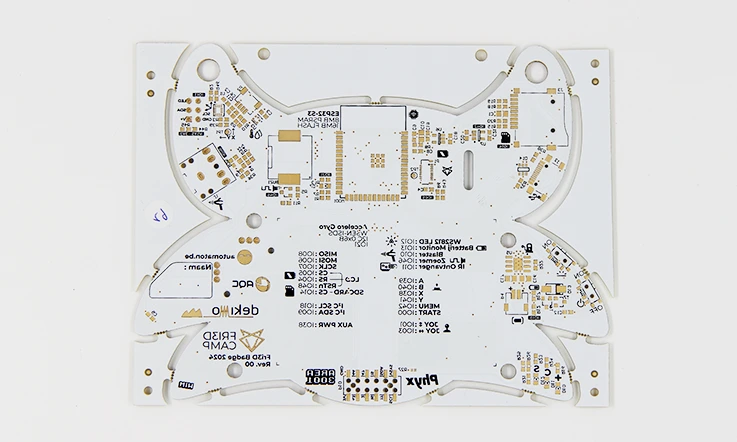
So, how do you choose between an aluminum substrate and an FR4 glass fiber board for your next PCB project? Well, it all depends on what you’re building.
Factors to Consider When Selecting PCB Materials
If your project involves high-power electronics or systems that generate a lot of heat, like LED lighting or automotive components, then an aluminum PCB is probably your best bet. The extra cost of aluminum substrates is more than worth it for the enhanced thermal management and mechanical strength they provide. On the flip side, if you’re working on something like a smartphone, tablet, or another consumer electronics device, FR4 PCBs will do the trick. They’re affordable, reliable, and can easily handle the demands of low to moderate heat environments.
Final Thoughts on Aluminum vs FR4 for Different Applications
To sum it up, both aluminum substrates and FR4 boards have their strengths. Aluminum PCBs are your go-to for heavy-duty, heat-generating applications where thermal management and durability are non-negotiable. FR4 PCBs, on the other hand, shine in consumer electronics, offering a low-cost solution for devices that don’t need the heavy-duty heat dissipation that aluminum provides. So, next time you’re designing a PCB, think about what you need: is it a tank that can handle heat, or a reliable workhorse for everyday tech?
In either case, choosing the right material could be the difference between smooth sailing and running into headaches down the road. And hey, no one wants to be the person who picks the wrong board and ends up with a system meltdown.
Make the Smart Choice for Your Next Project
Choosing the right PCB material can drastically impact the performance and longevity of your product. Whether you need the high thermal conductivity and durability of Aluminum PCBs or the cost efficiency and versatility of FR4 PCBs, the key is aligning your selection with your project’s specific needs.
Don’t let thermal issues or cost overruns derail your project—contact a reliable PCB supplier today to discuss the best solution for your next design. If you’re still unsure about which material is right for you, feel free to consult with PCB experts who can guide you through the decision-making process.
Ready to take your design to the next level? Get a free quote from our expert PCB prototype services and ensure that your next project is optimized for performance, reliability, and cost-efficiency. Click here to start your journey to better PCB design!
FAQs About Aluminum Substrate and FR4 PCBs
Just before we wrap things up, here are a few quick FAQs to help clarify any lingering questions you might have about aluminum substrates and FR4 glass fiber boards.
How do aluminum PCBs manage heat better than FR4 PCBs?
Aluminum PCBs excel at heat dissipation thanks to their metal core, which acts as a heat sink to pull heat away from components. FR4 PCBs, with their fiberglass-epoxy mix, don’t handle heat nearly as well and are better suited to low-power applications.
Are aluminum PCBs more expensive than FR4 PCBs?
Yes, aluminum PCBs are generally more expensive than FR4 PCBs because of their material costs and the extra steps involved in their manufacturing process. However, the extra cost is justified for high-power, heat-sensitive applications.
Which PCB material is more durable?
Aluminum PCBs are more durable than FR4 PCBs when it comes to mechanical strength. They can handle tougher environments and are less likely to warp or break under stress. FR4 PCBs, while still durable, are more suited to consumer products that don’t face extreme conditions.
What’s the best choice for consumer electronics?
For most consumer electronics, FR4 PCBs are the best choice because they are affordable and provide sufficient electrical insulation and mechanical strength for devices like smartphones, computers, and household gadgets.
Can I use a combination of aluminum and FR4 in the same project?
Yes, some advanced designs integrate both aluminum and FR4 layers to achieve a balance between thermal management and cost efficiency. This hybrid approach can offer the best of both worlds, especially in devices that need localized heat dissipation alongside low-cost PCB layers.
With this complete breakdown, hopefully, you’re feeling more confident about the differences between aluminum substrates and FR4 glass fiber boards. Whether you’re designing for power or affordability, picking the right PCB material can help you avoid a lot of headaches—and maybe even make you the hero of your next project! So, whether you’re aiming for efficiency, cost, or just making sure your board doesn’t go up in flames, the right choice is out there.