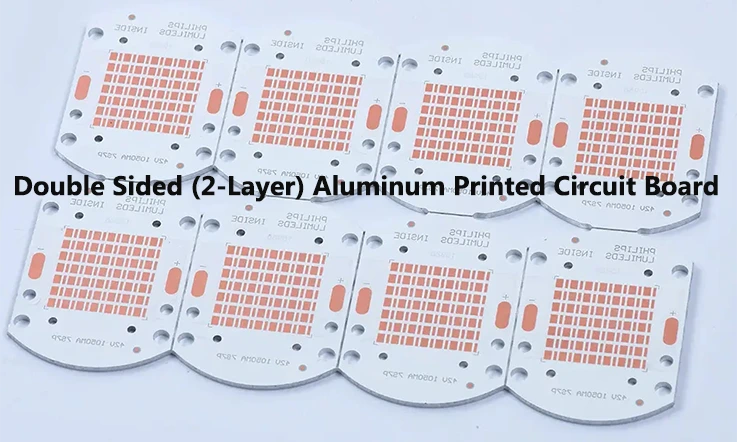
The contemporary electronics industry has an increasing need for highly durable and adaptable printed circuit board (PCB) solutions. In recent times, there has been a growing interest in the advancement of aluminum substrate technologies, which offer several advantages over traditional board materials like FR-4. This article delves into the emerging field of double-sided aluminum PCBs, which incorporate active components on both sides of an aluminum core. We will elucidate the primary benefits of this PCB variant and explore initial applications that are pushing the limits of what can be achieved.
What is 2 Layer Aluminum PCB (Double-Sided Alu PCB)?
The construction of a 2-layer aluminum substrate is typically more intricate and comprises five Structural: the layer, dielectric layer, aluminum base layer, dielectric layer, and circuit layer.
The aluminum material utilized in the aluminum base layer of the PCB possesses excellent thermal conductivity and lends itself well to conventional processing methods such as drilling, punching, and copper application.
Referred to as a double-sided aluminum PCB, the 2-layer aluminum PCB allows for the inclusion of LEDs on both sides of the substrate, in contrast to single-sided aluminum substrates that accommodate only one LED and a single layer trace. Consequently, the production of double-sided aluminum substrates involves the incorporation of two layers of traces, necessitating additional stamping and electroplating processes compared to single-sided aluminum PCBs. Consequently, the cost of double-sided aluminum boards is higher.
Due to the increased complexity of the 2-layer aluminum manufacturing process, it requires the drilling of holes twice, as it is challenging to directly plate copper onto the aluminum base material.
Types of Double Sided Aluminum PCB
The market offers a variety of double-sided aluminum substrates, each catering to specific application requirements. Here are some of the most prevalent types available:
Standard Double-Sided Aluminum Substrate:
This type of substrate features aluminum layers on both sides of the board, making it a popular choice for LED applications.
Thermal Conductive Double-Sided Aluminum Substrate:
Designed for applications demanding efficient heat dissipation, this substrate exhibits significantly higher thermal conductivity compared to the standard variant.
High-Frequency Double-Sided Aluminum Substrate:
Tailored for high-frequency applications, this substrate possesses a low dielectric constant, contributing to reduced signal loss and improved performance.
Flexible Double-Sided Aluminum Substrate:
Constructed from flexible materials, this substrate incorporates aluminum layers on both sides. It finds utility in applications requiring flexibility, such as wearable electronics.
Hybrid Double-Sided Aluminum Substrate:
This substrate combines the advantages of different materials, such as aluminum and ceramic. By leveraging this hybrid construction, it delivers enhanced thermal conductivity and superior electrical performance.
These diverse types of double-sided aluminum substrates cater to the evolving needs of the electronics industry, providing solutions for a wide range of applications.
Properties of 2 Layer Aluminum PCB
The 2-layer aluminum circuit board possesses distinct properties that contribute to its exceptional performance, setting it apart from single-sided aluminum PCBs.
Thermal Dissipation:
An outstanding characteristic of the aluminum PCB is its superior thermal dissipation capability. Unlike insulated metal substrates such as CEM3 and FR4, which exhibit poor thermal conductivity, aluminum is renowned for its excellent heat dissipation properties. Effective heat dissipation is crucial in preventing electronic component failure.
High Dimensional Stability:
Aluminum exhibits remarkable dimensional stability, meaning it experiences minimal expansion when subjected to heat. This inherent stability makes the aluminum PCB particularly well-suited for applications requiring high thermal performance.
Thermal Expansion:
The use of multiple materials in traditional PCBs can lead to thermal contraction and expansion issues. However, employing aluminum boards can mitigate these problems, thereby enhancing the reliability and durability of electronic devices. Additionally, aluminum PCBs offer effective solutions for managing thermal expansion concerns in surface mount technology (SMT) applications.
Additional Performance Benefits:
Beyond the aforementioned characteristics, the 2-layer aluminum PCB provides a shielding effect, enhancing electromagnetic compatibility. Moreover, it demonstrates excellent resistance to high temperatures, further bolstering its suitability for demanding environments. This circuit board exhibits superior electrical and thermal performance, contributing to the overall reliability and efficiency of electronic systems.
What Are the Benefits of the 2 Layer Aluminum PCB?
The utilization of Aluminum PCBs offers several key benefits:
Cost-Effectiveness:
Aluminum, being a widely available metal, exhibits low mining and refining costs compared to other metals. Consequently, the manufacturing process using aluminum is more economical, making Aluminum PCBs a cost-effective choice.
Environmental Friendly:
Aluminum is both recyclable and non-toxic, making it an environmentally friendly option. The ease of assembling aluminum PCBs contributes to energy conservation, while the use of this metal base by printed circuit board suppliers promotes the overall health of the planet.
Heat Dissipation:
Effective heat dissipation is crucial to prevent damage to electronic components. Aluminum plays a significant role in heat transfer, efficiently dissipating heat from vital components. This capability of Aluminum PCBs ensures reduced adverse effects on the printed circuit board, making them highly effective in heat dissipation.
Enhanced Durability:
The 2-layer Aluminum circuit board offers superior durability and strength compared to bases made of fiberglass or ceramic. The robust nature of Aluminum material reduces the likelihood of accidental breakage during handling, manufacturing processes, and everyday use, contributing to the longevity of products.
The combination of cost-effectiveness, environmental friendliness, excellent heat dissipation, and enhanced durability makes Aluminum PCBs a favorable choice for a wide range of electronic applications.
Construction and Design for Double Sided Aluminum PCB
Layer Structure:
Double-sided aluminum PCBs consist of two layers of aluminum, with a dielectric layer sandwiched in between.
The outer layers of aluminum act as conductive traces, allowing for component placement and interconnection on both sides of the board.
The dielectric layer provides electrical insulation between the top and bottom conductive layers.
Dielectric Material:
The dielectric material used in double-sided aluminum PCBs is typically a thermally conductive material with good electrical insulation properties.
Common dielectric materials include epoxy resin-based thermoset materials, such as FR-4, FR-5, or polyimide (PI).
The dielectric material plays a crucial role in maintaining electrical isolation between the conductive layers and providing thermal management.
Circuit Traces and Component Integration:
The conductive traces on double-sided aluminum PCBs are etched or deposited on the outer layers of aluminum using techniques like chemical etching or screen printing.
Both sides of the PCB can accommodate components, allowing for higher component density and increased circuit complexity.
Surface mount technology (SMT) components are commonly used for efficient component integration.
Vias, which are conductive pathways connecting the top and bottom layers, are utilized for electrical continuity and signal routing between the layers.
Soldermask and Silkscreen:
Soldermask is applied to the outer layers of the PCB to protect the conductive traces and prevent solder bridges during component soldering.
Silkscreen printing is used to add component designators, logos, and other markings for reference and identification purposes.
Thermal Management Considerations:
Double-sided aluminum PCBs are known for their excellent thermal dissipation properties.
Thermal vias can be strategically placed to enhance heat transfer from components to the aluminum layers, facilitating efficient heat dissipation.
Thermal pads or metal-core vias can be used to enhance thermal conductivity in critical areas.
Design Rules and Manufacturing Considerations:
Design guidelines for double-sided aluminum PCBs include considerations for trace width, spacing, and clearance to ensure proper electrical performance and manufacturability.
The design should account for thermal expansion and contraction during operation to prevent stress on the board and components.
Careful attention should be given to the choice of materials, stack-up configuration, and fabrication techniques to optimize performance and reliability.
By employing suitable construction techniques and following design principles specific to double-sided aluminum PCBs, manufacturers can produce robust and efficient boards capable of meeting the requirements of various applications.
Applications of Double Sided Aluminum PCB
Automotive Industry:
Engine control units (ECUs)
LED lighting systems
Powertrain systems
Battery management systems (BMS)
Vehicle navigation systems
Aerospace Industry:
Avionics and flight control systems
Satellite communication systems
Radar systems
Instrumentation and control panels
On-board entertainment systems
Industrial Sector:
Power supplies and inverters
Industrial automation and control systems
Motor drives and controllers
HVAC systems
Robotics and machinery control
LED Lighting:
LED modules and fixtures
Street lighting systems
Display panels and signage
Architectural lighting
Stage and event lighting
Consumer Electronics:
Wearable devices
Smart home automation systems
Audio amplifiers
Portable electronic devices
Gaming consoles and peripherals
Renewable Energy:
Solar power inverters
Wind turbine control systems
Energy storage systems
Smart grid infrastructure
Electric vehicle charging stations
Telecommunications:
Base station equipment
Network switches and routers
Wireless communication systems
Optical transceivers
Data center infrastructure
Medical Devices:
Patient monitoring systems
Imaging equipment
Diagnostic devices
Surgical instruments
Portable medical devices
Industrial Lighting:
High-intensity discharge (HID) lighting
Industrial process lighting
Hazardous area lighting
Outdoor and area lighting
Mining and construction lighting
Double Sided Aluminum PCBs find extensive use in these and various other industries due to their excellent thermal dissipation, dimensional stability, durability, and high-density component integration capabilities.
Future Trends and Innovations For Double Sided Aluminum PCB
Improved Substrate Materials:
Advancements in substrate materials for double-sided aluminum PCBs will focus on enhancing thermal conductivity, electrical insulation, and dimensional stability.
New materials with higher thermal conductivity, lower dielectric loss, and improved mechanical properties will enable better heat dissipation and electrical performance.
Miniaturization and Advanced Chip-Scale Packages:
Continued miniaturization of electronic components and the development of advanced chip-scale packages will drive the demand for more compact and densely integrated double-sided aluminum PCBs.
Shrinking component sizes and increased functionality in smaller packages will require optimized PCB designs to accommodate these advancements.
Advanced Manufacturing Techniques:
Further refinement of manufacturing processes, such as precision etching, laser drilling, and advanced surface finishing techniques, will enable the production of highly precise and reliable double-sided aluminum PCBs.
Additive manufacturing technologies, such as 3D printing with aluminum, may also find applications in the fabrication of double-sided aluminum PCBs.
Flexible Double-Sided Aluminum PCBs:
The development of flexible double-sided aluminum PCBs will open up new possibilities for applications that require bending or conforming to curved surfaces.
Flexible substrates combined with double-sided aluminum construction will provide flexibility, light weight, and excellent thermal management in a single package.
Increased Integration of Smart Features:
Double-sided aluminum PCBs will incorporate smart features, such as embedded sensors, wireless communication modules, and advanced signal processing capabilities.
Integration of these smart features will enable enhanced functionality, communication, and data processing, catering to the needs of IoT (Internet of Things) and smart device applications.
Advanced Thermal Management Solutions:
Ongoing research and development will focus on improving thermal management solutions for double-sided aluminum PCBs.
Integration of advanced heat sinks, heat pipes, phase change materials, and active cooling techniques will further enhance heat dissipation capabilities, enabling the PCBs to handle higher power densities.
Design Optimization for High-Frequency Applications:
As high-frequency applications continue to expand, there will be a focus on optimizing the design of double-sided aluminum PCBs to minimize signal loss, impedance mismatch, and electromagnetic interference (EMI).
Careful consideration of trace routing, controlled impedance, and grounding techniques will be crucial for achieving high-performance RF (radio frequency) and microwave applications.
These future trends and innovations will shape the evolution of double-sided aluminum PCBs, enabling them to meet the demands of emerging technologies and applications in a wide range of industries.
Conclusion
Double-sided aluminum PCBs represent a cutting-edge technology poised to make a significant impact across various industries. With their combination of strength, lightweight properties, and the capability for high-density component integration, these boards are exceptionally well-suited for demanding applications in sectors such as automotive, aerospace, and industrial.
The continuous refinement of substrates, along with advancements in microscopic deposition and the miniaturization of chip-scale packages, are expanding the possibilities for sophisticated aluminum PCB system designs. This ongoing progress enables the development of increasingly advanced and intricate aluminum PCB solutions.
It is crucial to note that double-sided aluminum PCBs differ from single-layer aluminum PCBs in terms of their design and capabilities. The unique characteristics of double-sided aluminum PCBs make them ideal for specific use cases that require enhanced performance and functionality.
If you require a reliable PCB manufacturer for top-quality 2-layer aluminum PCBs, we invite you to contact us at JarnisTech. We are dedicated to delivering exceptional products and services, and we assure you that choosing us will be a decision you won’t regret.