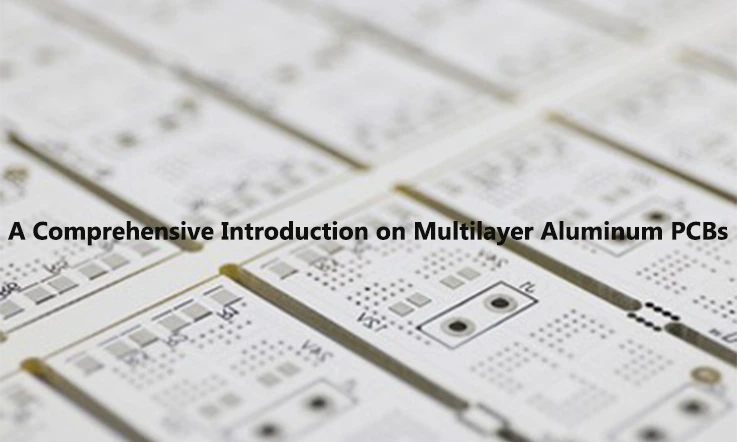
When it comes to high-power electronics, the efficiency and longevity of a system depend largely on how well heat is managed. Multilayer Aluminum PCBs have become a go-to solution in industries that require robust thermal management and compact designs. From high-voltage power systems to cutting-edge LED lighting, these circuit boards are providing a lifeline to complex designs by efficiently dissipating heat.
This guide delves into the essential aspects of multilayer aluminum PCB design, manufacturing, and emerging trends. It covers the latest advancements in thermal resistance, material selection, and sustainable manufacturing practices, providing insights into the future potential of these versatile boards. We’ll also explore the differences between multilayer aluminum PCBs, ceramic PCBs, and FR4 PCBs, shedding light on the advantages and limitations of each to help professionals make informed decisions in the design and manufacturing process.
What Is a Multilayer Aluminum PCB?
A Multilayer Aluminum PCB combines multiple layers of conductive copper with an aluminum base. The aluminum base excels at transferring heat away from sensitive components, ensuring that systems stay functional without overheating. This makes them particularly suitable for applications where high-power components generate a lot of heat, and controlling that heat is necessary to maintain performance and longevity.
The Basics of Multilayer Aluminum PCBs
A Multilayer Aluminum PCB is a type of printed circuit board that uses an aluminum base material in its design. Unlike traditional PCBs that rely on fiberglass or resin, the aluminum base offers superior thermal conductivity, ensuring heat is efficiently distributed away from the main components. These boards typically consist of multiple layers, including copper layers for signal pathways, a thermal insulating layer for electrical isolation, and the aluminum core for heat dissipation.
This unique construction makes Multilayer Aluminum PCBs ideal for applications that require both electrical reliability and thermal efficiency. They can handle larger currents and higher power without compromising performance, which is why they are widely used in electronics where heat dissipation is a concern, such as high-power LED systems and power modules.
Key Materials in Multilayer Aluminum PCBs-
Material | Role in Thermal Management |
Aluminum Base | Excellent heat conductor, prevents overheating |
Copper Layers | Conducts electrical signals while maintaining thermal efficiency |
Insulation Layer | Prevents electrical shorts, ensures safe current flow |
Thermal Vias | Direct heat away from the components to the aluminum base |
These materials are designed to withstand the conditions of high-power applications, providing both efficient power handling and reliable heat management.
Role of Aluminum Core in Heat Dissipation
The aluminum core is the cornerstone of Multilayer Aluminum PCBs’ ability to manage heat. Aluminum has a high thermal conductivity, meaning it can absorb and spread heat away from sensitive components faster than other materials commonly used in PCBs. This feature is essential when working with high-power electronics, as it prevents components from overheating and ensures they operate within their thermal limits.
When power components generate heat, the aluminum core serves as a heat sink, drawing excess heat away from the surface and distributing it throughout the board. This process ensures that heat is not localized, which could lead to the failure of components.
Why Aluminum-
●Aluminum is a highly effective material for heat conduction compared to traditional fiberglass.
●It’s lightweight, offering better design flexibility without adding bulk to the system.
●The material’s durability means it can withstand high temperatures without degrading, ensuring the PCB lasts longer.
With aluminum in place, the overall temperature of the board is regulated, helping the device maintain stable performance.
Key Advantages of Multilayer Aluminum PCBs in Thermal Solutions
When it comes to thermal management, Multilayer Aluminum PCBs offer numerous benefits that help in high-power applications. Here are some of the advantages these boards provide:
1. Efficient Heat Distribution-
A major advantage of Multilayer Aluminum PCBs is their ability to distribute heat uniformly across the board. As the components generate heat, the aluminum base layer transfers it quickly across the entire board. This prevents any area from becoming overheated, which could lead to potential system failures.
2. Increased Power Handling Capacity-
These PCBs can handle large currents and high-power applications without compromising the thermal management system. The multi-layer construction allows for higher current flow while ensuring that the heat generated is evenly dissipated, making them good for applications requiring significant power handling.
3. Extended Lifespan-
By preventing overheating and thermal stress, Multilayer Aluminum PCBs can help extend the operational lifespan of electronic components. The heat dissipation offered by the aluminum base reduces the risk of degradation, ensuring that the components remain operational for longer periods.
4. Compact and Lightweight Design-
Multilayer Aluminum PCBs provide excellent thermal performance in a compact form. This makes them highly suitable for industries like automotive and aerospace, where minimizing weight is a core factor without compromising on performance. The aluminum base helps us create systems that are both efficient and lightweight.
5. Sustainability-
Because aluminum is recyclable, its use in PCBs makes these boards a more eco-friendly option. This aspect is gaining attention in electronic design, especially with growing awareness of the environmental impact of electronic waste.
Design Considerations for Multilayer Aluminum PCBs
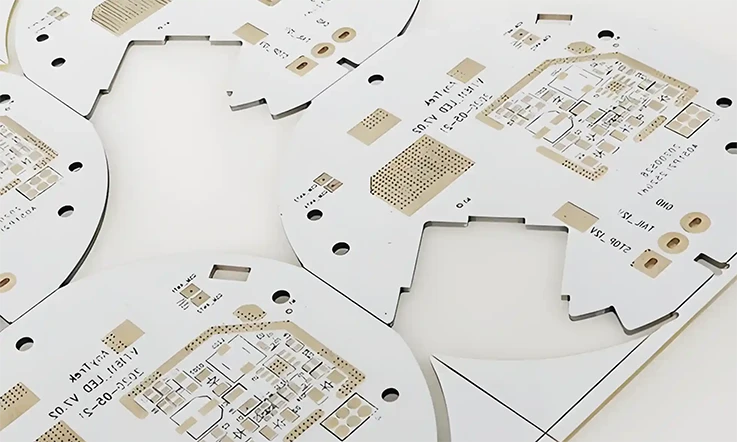
Designing Multilayer Aluminum PCBs requires a thorough understanding of both thermal management and electrical performance. As the demand for higher power applications, compact designs, and efficient heat dissipation continues to grow, the choices made during the design phase can significantly impact both the performance and durability of the final product.
The combination of material selection, layer construction, and electrical insulation ensures that the Multilayer Aluminum PCB operates effectively without overheating or encountering issues like short circuits. In this section, we’ll dive into the three most important factors—material selection, layer construction optimization, and electrical insulation—and how they play a role in the overall design of Multilayer Aluminum PCBs.
Material Selection for Multilayer Aluminum PCB Thermal Performance
When designing Multilayer Aluminum PCBs, selecting the right materials is the first step to ensuring thermal performance. Every layer of the PCB, from the aluminum core to the copper traces to the insulation materials, needs to be chosen with care to support both heat dissipation and electrical functionality.
Choosing the Right Aluminum Core Material-
The aluminum core in a Multilayer Aluminum PCB plays a central role in heat dissipation. The type of aluminum used affects the thermal conductivity of the PCB. Materials like 99.6% pure aluminum are often chosen to optimize heat dissipation. This allows the PCB to absorb and redirect heat, preventing it from affecting sensitive components.
The thickness of the aluminum core also has an impact. A thicker core can improve heat dissipation but might increase both the weight and cost of the board. On the other hand, a thinner core may offer a more budget-friendly option, though it could limit thermal efficiency in high-power applications.
Copper Traces and Their Role in Heat Transfer-
Copper remains the gold standard for electrical conductivity. In a Multilayer Aluminum PCB, the copper traces must be sized appropriately to handle the current without overheating. When working with high-power applications, it’s essential to ensure that the copper traces have sufficient width to accommodate higher currents, which will reduce the potential for thermal hotspots.
The copper foil used also impacts thermal conductivity. Some advanced copper-clad laminates feature high thermal conductivity properties to help heat move faster through the PCB and into the aluminum core, ensuring efficient heat dissipation.
Choosing Insulation Materials-
Selecting the right insulation goes hand in hand with choosing the metal components. While the aluminum core manages thermal conductivity, the insulation materials need to separate the layers electrically to prevent shorts and keep the circuit’s integrity intact.
For Multilayer Aluminum PCBs, materials like polyimide or FR4 are often used as insulation layers. These materials offer high dielectric strength and good thermal stability, meaning they can withstand both high temperatures and electrical stress. Additionally, advanced materials like ceramic-filled polymers are becoming more popular due to their excellent thermal performance and high thermal conductivity.
Optimizing Layer Construction in Multilayer Aluminum PCB Design
The layer construction of a Multilayer Aluminum PCB dictates how effectively it handles heat and electrical signals. A well-planned layer stack-up can prevent heat from accumulating in any one area while also allowing for efficient signal routing.
Strategic Layer Placement for Better Heat Dissipation-
Optimizing the layer stack-up involves ensuring that the aluminum core is correctly positioned beneath the copper layers, which serves as the primary heat sink for the board. However, how the copper and insulating layers are arranged also impacts how well heat is dissipated. A well-designed layer stack-up ensures that the heat generated by high-power components moves efficiently through the PCB to the aluminum core.
For example, the power layers, which typically carry high currents and generate more heat, should be placed closer to the aluminum core. Meanwhile, the signal layers, which are more sensitive to heat, should be placed farther away from the core to minimize exposure to excessive temperatures.
Thickness of Copper and Insulation Layers-
Adjusting the thickness of the copper traces and insulation materials is another method of optimizing thermal performance. Thicker copper traces can carry more current and dissipate more heat, but this must be balanced with the space available on the PCB. Additionally, insulation materials should be optimized to prevent heat buildup while still maintaining electrical insulation between layers.
In certain high-power Multilayer Aluminum PCB applications, it may be necessary to use thicker insulation layers between the power and signal layers. This ensures that heat from the power components doesn’t interfere with the signal integrity of the sensitive circuits.
Ensuring Electrical Insulation in Multilayer Aluminum PCBs
Electrical insulation is just as necessary as thermal management in Multilayer Aluminum PCB design, particularly in high-power or high-voltage systems. Proper insulation helps electrical components work without interference from other layers or components and prevents short circuits caused by excessive heat buildup.
Selecting Insulation Materials for Safety-
Choosing the right insulation materials goes beyond just preventing short circuits—it’s about safety. For high-power Multilayer Aluminum PCBs, you’ll want materials that have a high dielectric strength to prevent electrical arcing between layers. Polyimide is often used because it offers excellent electrical insulation and thermal stability.
In addition, maintaining proper electrical insulation between the aluminum core and copper layers is necessary to avoid short circuits. Thermal pads are commonly used in this situation, as they offer both heat dissipation and electrical insulation, ensuring the board functions safely without heat-induced electrical issues.
Insulation Considerations for High-Voltage Systems-
When designing Multilayer Aluminum PCBs for high-voltage systems, the insulation requirements become even more stringent. A higher dielectric strength is needed to withstand the pressure of the voltage without breaking down. Materials such as ceramic-filled polymers or high-performance epoxy resins are commonly used for these applications to ensure that there is no risk of electrical breakdown.
How to Optimize Multilayer Aluminum PCB Designs for High Power Density?
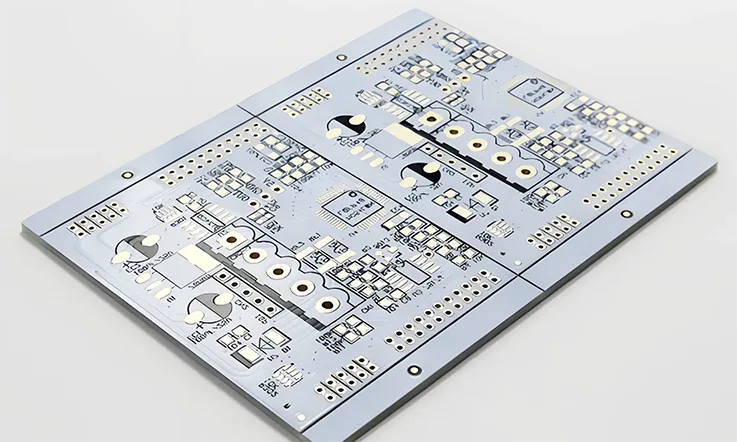
When designing Multilayer Aluminum PCBs for high power density applications, there’s no room for mistakes. The more power you pack into a smaller space, the harder it gets to manage the heat that inevitably comes with it. This is where thermal resistance and the smart design of Multilayer PCBs become indispensable. In this section, we will delve into the strategies that allow power electronics systems to thrive without overheating, ensuring maximum performance and reliability over time.
The focus here is not just on the materials but also on the thermal dissipation mechanisms embedded within the Multilayer PCB design. It’s about striking the perfect balance between high power density and efficient thermal management, so the device runs as expected, no matter how much power it handles.
Thermal Resistance: The Roadblock to High Power Density
In high power density designs, thermal resistance is one of the most challenging factors to manage. The more power your PCB handles, the more heat is generated, and if that heat isn’t efficiently dissipated, it can cause a multitude of performance and durability issues.
What is Thermal Resistance in Multilayer Aluminum PCBs-
Simply put, thermal resistance is the measure of a material’s ability to resist the flow of heat. In a Multilayer Aluminum PCB, this concept applies to both the thermal conductivity of the materials used and the structural design of the layers. High thermal resistance means that heat is trapped within the PCB, causing hot spots that could lead to component failure or reduced performance.
When designing for high power density, managing thermal resistance begins with selecting materials that have low thermal resistance, such as high-conductivity copper and aluminum for the core. The aluminum core functions as a heat sink, effectively absorbing the heat produced by the active components and moving it away from the board.
Strategies to Minimize Thermal Resistance-
To ensure that thermal resistance does not hinder the performance of your Multilayer PCB, several strategies can be employed:
1.Optimize Layer Stack-Up: The design of your layer stack-up is essential in managing heat. Power layers should be placed closer to the aluminum core, as the core serves as the primary heat dissipation pathway.
2.Thermal Vias: These small, plated-through holes allow heat to transfer between layers. Placing thermal vias directly under high-power components ensures that heat doesn’t accumulate at one spot but instead moves quickly through the PCB toward the aluminum core.
3.Heat Spreading Materials: Materials like thermal pads or high-conductivity polymers can be used in between layers to assist in spreading the heat, ensuring uniform dissipation across the board.
High Power Density in Multilayer Aluminum PCBs: Balancing Performance and Heat Dissipation
As high power density designs become more common, we must take an integrated approach to thermal management and overall PCB design. Thermal dissipation cannot be an afterthought. It’s essential that the entire design process focuses on both the electrical conductivity and thermal management to create an efficient, reliable PCB.
Key Strategies for High Power Density Designs-
1.Use of Thermal Vias and Copper Planes Thermal vias are core components in the thermal management process of Multilayer Aluminum PCBs. These vias connect different layers of the PCB, allowing heat to travel quickly from the high-power components (like LEDs or power transistors) to the aluminum core. By using multiple thermal vias and copper planes, you can dramatically increase the thermal conductivity and spread the heat more evenly across the board.
This design approach enhances thermal dissipation and reduces thermal resistance within the system. Copper, with its excellent ability to conduct heat and electricity, helps optimize the heat flow efficiently.
2.Aluminum Core Selection and Thickness A thicker aluminum core helps dissipate heat more effectively by providing more material to absorb and spread heat away from sensitive components. For applications with high power density, choosing materials with higher thermal conductivity allows heat to move more quickly, reducing the likelihood of hot spots.
3.Thermal Pads and Advanced Materials Employing advanced materials like ceramic-filled polymers or graphene-based composites can significantly enhance heat dissipation. These materials often feature higher thermal conductivity and can be placed between the power components and the aluminum core to help manage heat more effectively.
Thermal pads are another go-to solution. They can be placed on the back of high-power components and help channel the heat directly into the aluminum core. Using these pads ensures that the heat is efficiently transferred and minimizes the chances of thermal hotspots.
Manufacturing Process for Multilayer Aluminum PCBs

The manufacturing process for Multilayer Aluminum PCBs consists of several stages that demand precision. As these boards are widely used in applications requiring efficient thermal management, each step of the fabrication process must be executed with careful attention to detail to guarantee the performance and durability of the finished product.
In this section, we explore the major stages in the PCB fabrication process, focusing on the unique aspects of manufacturing Multilayer Aluminum PCBs. We’ll also discuss the quality control steps necessary to ensure these PCBs meet the standards required in sectors like power electronics, automotive, and beyond.
Key Stages in Multilayer Aluminum PCB Fabrication
The production of Multilayer Aluminum PCBs involves multiple critical steps, beginning with material selection and continuing through etching, lamination, and final assembly.
1.Material Selection: The foundation of any Multilayer Aluminum PCB is the choice of materials. Typically, aluminum alloys are selected for the core material due to their ability to conduct heat. For the conductive layers, copper is typically used. The material choices directly influence the board’s overall thermal conductivity and electrical performance.
2.Copper Cladding and Etching: After selecting the base material, the aluminum core is cladded with copper. This copper layer will eventually carry the electrical signals. Etching removes unwanted copper, leaving behind traces that form the electrical connections of the PCB.
3.Layer Formation and Lamination: The lamination process involves stacking and bonding multiple layers of material to form the final PCB structure. At this stage, the copper and aluminum layers are fused under heat and pressure, creating a solid, durable board. Proper lamination is necessary to ensure that the layers bond securely and that no separation occurs during operation.
4.Via Drilling and Plating: After the layers are formed, thermal vias are drilled through the board. These vias create heat transfer pathways that allow heat to dissipate from the high-power components to the aluminum base. Once drilled, the vias are plated to create electrical connections between layers.
5.Layer Registration and Alignment: To ensure precision, layer registration is performed. This step ensures the layers are perfectly aligned, minimizing the risk of defects that could interfere with circuit functionality or heat dissipation.
Layer Stacking and Soldering Techniques for Multilayer Aluminum PCBs
Layer stacking is a main part of Multilayer Aluminum PCB design, as each layer in the stack has a specific role—whether it’s for power, ground, or signal. Proper stacking helps achieve desired thermal dissipation and electrical performance.
1.Stack-Up Design: The way the layers are arranged can impact electrical performance and thermal management. The signal layers are typically placed between power and ground layers, which can help reduce electromagnetic interference (EMI) and enhance signal integrity. The aluminum core is placed at the bottom of the stack for effective heat dissipation.
2.Soldering Techniques: Once the layers are stacked, soldering bonds the components to the PCB traces. Different soldering techniques are employed, including wave soldering for through-hole components and reflow soldering for surface-mount components. The chosen method depends on the design complexity and the type of components being used.
●Wave soldering is often used for through-hole components, while reflow soldering is more commonly applied to SMT components. Both techniques ensure a reliable connection between the components and the board.
3.Thermal Management During Soldering: During the soldering process, excess heat can become an issue. That’s where thermal pads and heat sinks come into play. These elements help absorb heat during the soldering process, ensuring the integrity of the Multilayer Aluminum PCB isn’t compromised during assembly.
PCB Testing and Quality Control in Multilayer Aluminum PCBs
Once the Multilayer Aluminum PCB is fabricated, it undergoes a series of tests to ensure it functions as intended. Rigorous testing checks the thermal conductivity, electrical integrity, and mechanical durability of the board, making sure it meets the high demands of its intended application.
1.Electrical Testing: After fabrication, electrical tests are conducted to check for continuity, impedance, and other electrical properties. Continuity tests ensure there are no shorts or open circuits, while impedance tests check for any issues in signal integrity that could impact performance.
2.Thermal Testing: Since Multilayer Aluminum PCBs are commonly used in high-power applications, thermal testing is an essential part of the process. Thermal imaging can be used to identify hot spots and ensure that heat dissipation is occurring effectively through the aluminum core.
3.Mechanical Stress Testing: To simulate real-world usage, the PCB undergoes mechanical testing. This includes tests for vibration, bending, and thermal cycling, which ensures the PCB can withstand the conditions it will face during operation.
4.Quality Control Standards: Every Multilayer Aluminum PCB must pass a series of inspections and adhere to industry standards. Visual inspection and X-ray inspection are common methods used to detect defects such as misalignment or improper solder joints.
5.Final Inspection and Packaging: Once the PCB passes all tests, it undergoes a final inspection to ensure it meets aesthetic and functional standards. The board is then carefully packaged to prevent damage during shipping, often using anti-static materials to safeguard against static discharge.
Multilayer Aluminum PCBs vs. Ceramic PCBs, Flexible PCBs, and FR4 PCBs
When designing advanced electronics, choosing the right type of PCB is more than just about performance; it’s also about durability, heat management, and the ability to handle complex circuitry. Each material offers distinct advantages depending on the application’s requirements. In this section, we’ll compare multilayer aluminum PCBs, multilayer ceramic PCBs, multilayer flexible PCBs, and multilayer FR4 PCBs to highlight their characteristics and best-use scenarios. Let’s dive into the specifics of each and explore how these materials measure up in various design applications.
Multilayer Aluminum PCBs vs. Multilayer Ceramic PCBs
Both multilayer aluminum PCBs and multilayer ceramic PCBs excel in heat dissipation, but they do so in different ways. Aluminum, being a great conductor of heat, makes aluminum PCBs ideal for applications requiring efficient thermal management, such as power electronics, LED lighting, and automotive systems. The aluminum core serves as a natural heat sink, helping to dissipate heat away from sensitive components.
On the other hand, ceramic PCBs are often chosen for their superior electrical insulation and high thermal conductivity. They can handle high temperatures better than aluminum in some situations and are typically used in applications like high-frequency RF circuits, medical devices, and aerospace technology. However, ceramic PCBs can be more brittle, making them less durable under mechanical stress compared to aluminum-based solutions.
Here’s how they compare in a nutshell:
Property | Multilayer Aluminum PCB | Multilayer Ceramic PCB |
Thermal Conductivity | High | Very High |
Mechanical Strength | Strong, but less than ceramic | Brittle, more prone to cracking |
Electrical Insulation | Good, but not as high as ceramic | Excellent, better than aluminum |
Cost | Lower | Higher |
Applications | Power, LED, automotive | Aerospace, medical, high-frequency RF |
As shown in the table, multilayer aluminum PCBs offer a balanced performance in terms of thermal dissipation and electrical insulation, while multilayer ceramic PCBs excel in applications that require high-frequency performance and durability under extreme temperatures.
Multilayer Aluminum PCBs vs. Multilayer Flexible PCBs
Next, let’s take a look at how multilayer aluminum PCBs compare to multilayer flexible PCBs. While both offer high-performance capabilities, they serve very different needs.
Multilayer flexible PCBs are designed for applications where flexibility and a lightweight structure are needed, such as in wearable devices, portable electronics, and tight spaces that rigid PCBs can’t accommodate. Flexible PCBs can bend and conform to the required shapes, allowing for compact, lightweight designs that are often used in consumer electronics like smartphones and tablets. However, flexible PCBs often have less robust thermal dissipation properties than aluminum-based PCBs.
In contrast, multilayer aluminum PCBs are excellent at managing heat in high-power applications but lack the flexibility that multilayer flexible PCBs offer. They are best suited for applications where thermal management is a higher priority than flexibility.
Property | Multilayer Aluminum PCB | Multilayer Flexible PCB |
Thermal Conductivity | High | Low |
Flexibility | Rigid | Flexible |
Durability | High, but rigid | Less durable, but flexible |
Cost | Moderate | Higher |
Applications | Power electronics, LED, automotive | Wearables, medical devices, consumer electronics |
As seen, multilayer flexible PCBs might be more suitable for compact designs but may not offer the same level of heat management as multilayer aluminum PCBs. The choice between these materials depends heavily on whether the priority is thermal performance or the need for flexibility in design.
Multilayer Aluminum PCBs vs. Multilayer FR4 PCBs
Finally, let’s explore how multilayer aluminum PCBs compare to multilayer FR4 PCBs, a more commonly used material in the PCB industry.
Multilayer FR4 PCBs are widely used in consumer electronics, telecommunications, and industrial equipment due to their relatively low cost and reliable electrical performance. However, while they offer a solid base for general-purpose electronics, they fall short when it comes to thermal management compared to aluminum-based PCBs. FR4 is a composite material made of woven glass fiber and epoxy resin, making it a durable and stable solution for many applications, but it doesn’t conduct heat as efficiently as aluminum.
For applications where thermal dissipation is a priority, such as power supplies or high-power LED systems, multilayer aluminum PCBs are preferred. FR4, being a good dielectric material, is better suited for general applications where high temperature or heat dissipation is not a major concern.
Here’s a comparison between the two:
Property | Multilayer Aluminum PCB | Multilayer FR4 PCB |
Thermal Conductivity | High | Low to Moderate |
Electrical Insulation | Good | Very Good |
Mechanical Strength | Strong | Strong |
Cost | Higher than FR4 | Lower |
Applications | Power electronics, LED lighting | Consumer electronics, industrial |
The Future of Multilayer Aluminum PCBs
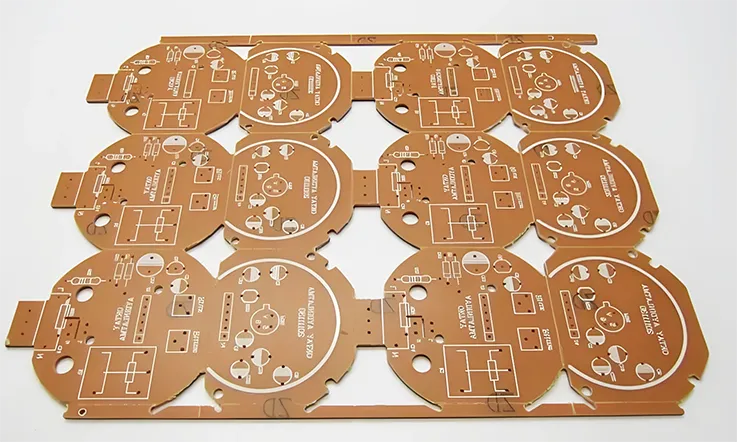
The demand for multilayer aluminum PCBs is steadily increasing as industries such as automotive, LED lighting, telecommunications, and power electronics continue to require advanced thermal management solutions. Aluminum’s unique properties, such as its excellent thermal conductivity, make it a go-to material for high-performance electronics. However, as technology evolves, new challenges arise in multilayer PCB design and manufacturing processes. Additionally, with growing environmental concerns, sustainability is becoming a top priority for us. In this section, we’ll explore the emerging trends, the sustainability of design and manufacturing, and how new materials are shaping the future of multilayer aluminum PCBs.
Emerging Trends in Multilayer Aluminum PCB Technology
The advancement of multilayer aluminum PCB technology continues to evolve with new techniques and materials pushing the boundaries of thermal management and electrical performance. A few noteworthy trends include:
1.Miniaturization and Higher Density: As devices become more compact, the need for high-density multilayer aluminum PCBs increases. This has led to a focus on finer trace designs, thinner copper layers, and more precise soldering techniques. Smaller, more powerful components demand multilayer PCB designs that can handle significant power loads while maintaining heat dissipation efficiency.
2.Integration with Smart Systems: With the increasing demand for connected devices, multilayer aluminum PCBs are being integrated into IoT devices, smart homes, and even automotive electronics. As these systems require more complex designs, there’s a trend toward incorporating multilayer aluminum PCBs with sensors, microprocessors, and wireless communication modules.
3.Improved Thermal Dissipation Techniques: New developments in thermal vias, heat sinks, and thermal pads have been instrumental in advancing thermal conductivity. Emerging micro-channel cooling techniques allow for better heat management, making it possible to design higher-performance systems without overheating.
4.Flexible and Rigid-Flexible Designs: While rigid aluminum PCBs are widely used for their structural stability, the demand for flexible designs is growing in areas like wearable devices and automotive electronics. By incorporating flexible aluminum PCBs, we can provide more adaptable and space-efficient designs.
Trend | Description |
Miniaturization | Smaller, denser designs with advanced thermal management |
Integration with Smart Systems | Embedded with IoT, sensors, and wireless tech |
Enhanced Thermal Management | Improved vias, heat sinks, and micro-channel cooling |
Flexible Designs | More demand for flexible and rigid-flexible solutions |
Sustainable Design and Manufacturing of Multilayer Aluminum PCBs
As industries shift towards more sustainable practices, multilayer aluminum PCB manufacturing must adapt. The production processes involved, such as etching, lamination, and soldering, often generate waste and emissions. Manufacturers are turning to more environmentally conscious alternatives to minimize the environmental impact:
1.Eco-Friendly Materials: The industry is exploring alternative substrates and components that reduce reliance on toxic chemicals and heavy metals. For instance, lead-free soldering processes are gaining momentum as part of the RoHS compliance trend.
2.Energy-Efficient Manufacturing: Incorporating more energy-efficient processes into the production of multilayer aluminum PCBs can reduce both operational costs and carbon emissions. A lot Companies are utilizing automated technologies and improving factory layouts to minimize energy consumption.
3.Recyclable and Reusable Materials: Sustainable design doesn’t just stop at production; it extends to the end of a product’s life cycle. Multilayer aluminum PCBs are increasingly being designed with recyclability in mind. Aluminum itself is highly recyclable, and some manufacturers are incorporating recycled materials into the PCB manufacturing process.
4.Closed-Loop Systems: Advances in closed-loop recycling systems have begun to be integrated into PCB manufacturing, allowing for the recovery of valuable metals from used boards. This reduces waste and promotes the circular economy.
Sustainability Factor | Impact on Multilayer Aluminum PCBs |
Eco-Friendly Materials | Use of lead-free, non-toxic materials and components |
Energy Efficiency | Energy-saving production techniques and factory automation |
Recyclability | Designing for easy material recovery and reuse |
Closed-Loop Systems | Reduction in waste and improved resource efficiency |
The Impact of New Materials on Multilayer Aluminum PCB Performance
The evolution of materials science is reshaping how multilayer aluminum PCBs perform in high-demand applications. New composite materials, conductive polymers, and nanomaterials are becoming increasingly relevant to the future of PCB design. These developments are opening up new avenues for performance enhancement:
1.High-Temperature Resins: New resins and laminates are being developed that can withstand higher operating temperatures, which can improve the performance of multilayer aluminum PCBs in environments such as power electronics or automotive applications. These high-temperature resins extend the lifespan and reliability of the boards, making them more suitable for harsh environments.
2.Nano-Enhanced Materials: Nanotechnology is being explored for its ability to enhance the electrical and thermal properties of PCBs. Nanomaterials can be incorporated into the resin or coating layers, significantly improving thermal conductivity and electrical insulation without adding bulk to the PCB.
3.Copper Clad Aluminum (CCA): Copper-clad aluminum is being studied as an alternative to traditional copper-based PCBs. This material offers a balance between cost-efficiency and thermal management, with the added benefit of a lighter weight compared to pure copper alternatives.
4.Flexible Substrates: Advances in flexible substrate materials, such as polyimide and PET (polyethylene terephthalate), are expanding the possibilities for multilayer aluminum PCBs. These materials allow for more flexibility in design, opening up new applications in wearable devices, healthcare tech, and automotive systems.
New Material | Effect on Multilayer Aluminum PCBs |
High-Temperature Resins | Improves performance in extreme environments |
Nano-Enhanced Materials | Enhances thermal and electrical properties |
Copper Clad Aluminum (CCA) | Cost-effective, lighter, and improved thermal performance |
Flexible Substrates | Enables flexible designs for compact applications |
Why Choose JarnisTech for Multilayer Aluminum PCBs?
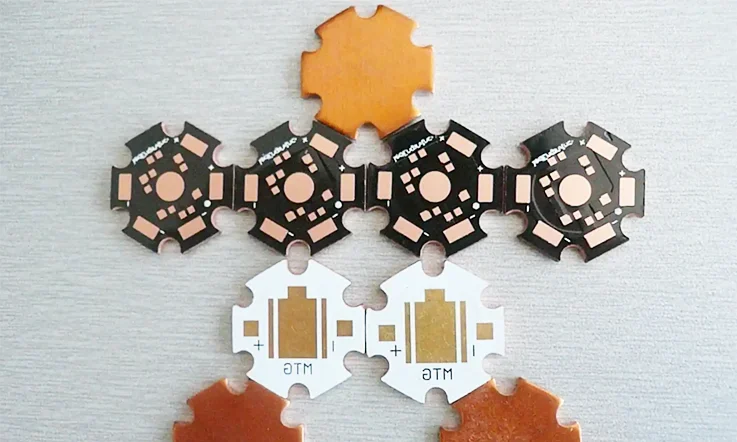
At JarnisTech, we specialize in delivering high-performance multilayer aluminum PCBs designed to meet the toughest demands of modern electronics. With years of experience and a dedicated team of professionals, we bring a wealth of knowledge to every project, ensuring that our products meet the highest standards of quality and precision. Whether you’re designing for automotive, medical, or consumer electronics, our expertise ensures your PCB will be up to the task.
1.Our Commitment to Quality and Precision
JarnisTech stands out in the PCB manufacturing space because of our commitment to providing high-quality, reliable products that exceed customer expectations. We use state-of-the-art equipment and the latest technologies to ensure that each multilayer aluminum PCB we produce performs consistently across its lifecycle.
Our design and fabrication process involves close collaboration with clients, ensuring that all specifications are met with exacting precision. From the initial design phase through to assembly, our comprehensive approach guarantees that every PCB we produce adheres to industry standards and is optimized for thermal management, electrical performance, and mechanical stability.
2.Experience You Can Trust
With a proven track record in producing multilayer aluminum PCBs, we are trusted by a wide range of industries. We understand that each project has its own set of challenges, whether it’s high-density component layout, heat dissipation, or ensuring electrical insulation. Our team is always ready to tackle the complexities of custom designs, ensuring that your PCB meets all functional and environmental requirements.
3.Delivering Beyond Expectations
When you partner with JarnisTech, you’re not just getting a product—you’re getting a reliable, long-term partner who will help you through every step of the design and manufacturing process. From high-power electronics to low-profile consumer devices, our team is committed to delivering exceptional PCBs that perform under pressure.
We don’t just stop at manufacturing. Our customer service team is there to guide you through every phase, offering solutions that fit your unique needs. Whether you’re working with high-frequency circuits, power electronics, or demanding mechanical environments, we’ve got you covered.
4.Why JarnisTech?
Advanced Technology: We leverage cutting-edge machinery to ensure precision at every step of the PCB production process.
●Custom Designs: Whether it’s multilayer or specialized configurations, we work closely with you to tailor solutions for your specific application.
●Thermal Performance: With an in-depth understanding of heat dissipation, we focus on selecting materials and designs that keep your products running efficiently.
●Full-Service Manufacturing: From concept to assembly, JarnisTech offers end-to-end solutions for all your PCB needs.
Let JarnisTech help you achieve your product goals with our top-tier multilayer aluminum PCBs. Reach out today to discuss your next project—we’re ready to bring your designs to life!
FAQs: Multilayer Aluminum PCBs
1.What materials are used for the base layer in multilayer aluminum PCBs?
The base layer is typically made of aluminum, which offers superior heat conductivity compared to other PCB base materials.
2.What is the typical range of PCB thickness for multilayer aluminum PCBs?
The thickness can vary based on the application, but most multilayer aluminum PCBs range from 1.6mm to 3.2mm in total thickness.
3.What role does the dielectric material play in multilayer aluminum PCBs?
The dielectric material between the aluminum base and copper layers acts as an insulator, helping to prevent electrical shorts while enhancing heat dissipation.
4.What are the limitations of multilayer aluminum PCBs?
One limitation is their rigidity, which makes them less suitable for applications requiring flexible designs. They can also be more difficult to fabricate than other PCB types.
5.How does the manufacturing process of multilayer aluminum PCBs differ from standard FR4 PCBs?
The main difference lies in the aluminum base layer, which requires specialized processes such as bonding and thermal management techniques.