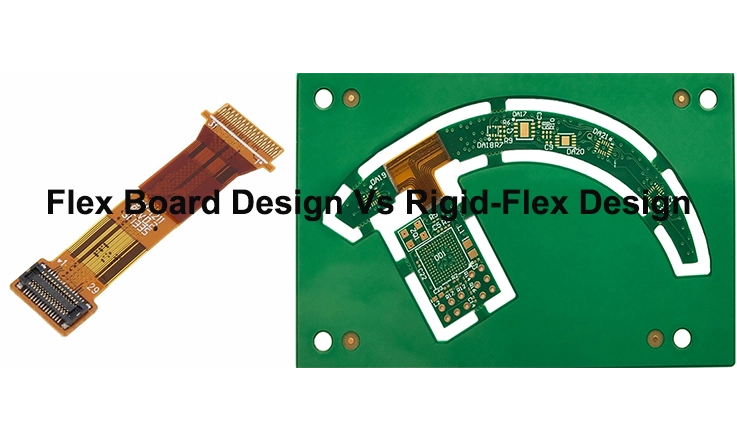
Flex PCB and rigid-flex PCB represent two separate design structures providing distinct merits and considerations. Apprehending the disparities between these two pcb types is crucial for successful PCB design. This composition probes into the basics of flex PCB design alongside the merits of rigid-flex PCB design, offering guidelines on determining the suitable choice amongst the two.
Definition of Flex Board Design
Flex board design refers to the process of designing and production flexible printed circuit boards. Stand out from traditional rigid PCB, flex boards are conceived from pliable materials, empowering them to flex, contort, and adapt to distinct forms and outlines.
Flex boards are primarily utilized in scenarios where space is at a premium and necessitate the circuit board’s ability to bend or flex. They provide numerous superiorities over rigid PCB, like enhanced dependability, diminished weight, and augmented durability. Flex boards are routinely encountered in items such as smartphones, wearable technology, medical equipment, aerospace mechanisms, and automotive electronics.
The design process for flex boards calls for evaluation of the distinct mechanical and electrical attributes of pliable materials. Engineers must factor in elements such as the bend radius, Base material thickness, as well as the arrangement of components to guarantee dependability and operational efficiency of the circuit. Specialized design software and tools are used to create the layout and routing of the flexible circuit traces.
The production of flex boards involves a fusion of conventional PCB manufacturing methods and specific procedures for managing pliable materials. The flexible substrate usually comprises polyimide or polyester film, which gets draped with a conductive material layer like copper. The circuit pattern is then etched onto the conductive layer, and additional layers may be added for multi-layer flex boards.
The design of flex boards necessitates proficiency in both electrical and mechanical engineering, complemented with a profound comprehension of the characteristics and constraints of flexible materials. It is an exclusive domain that persists in progressing as novel technologies and materials are formulated.
What is a Rigid-Flex Board Design?
A hybrid design of rigid-flex boards amalgamates the aspects of both rigid and flexible printed circuit boards, intertwining them intricately into an integral circuit. It inherits the benefits of rigid as well as flexible PCB, making way for intricate and space-efficient designs that stay resilient to mechanical pressures while ensuring dependable electrical linkages.
In a rigid-flex board design, the circuit is segmented into several divisions, with certain portions consisting of rigid substrate materials, while others are composed of flexible materials. The rigid sections typically contain components that require a solid mounting surface, while the flexible sections allow for bending and conforming to fit the desired shape or enclosure.
The segments that are rigid and those that are flexible are united utilizing techniques such as plated through-holes, vias, or flexible connectors. TThese interconnections provide electrical continuity between the rigid and flexible portions of the circuit. The pliable segments can be architectured to flex or twist, allowing the board to fit into tight spaces or conform to the shape of the product.
Employing rigid-flex board designs presents numerous advantages. They diminish the requirement for connectors and cables, leading to streamlined assembly processes and enhanced dependability. They also conserve weight and spatial dimensions, making them an apt preference for condensed and light electronic apparatuses. Instances of rigid-flex boards are predominantly found in applications marked by limited space, elevated vibrations or shocks, or instances demanding recurrent flexing.
Designing rigid-flex boards requires specialized knowledge and expertise. Designers need to consider factors such as the bend radius, material properties, and mechanical stress during the design process. They also need to ensure proper electrical connections and signal integrity across the rigid and flexible sections.
The manufacturing process for rigid-flex boards involves a combination of traditional PCB fabrication techniques and specialized processes for handling flexible materials. The rigid and flexible sections are typically manufactured separately and then laminated together to form the final board.
Collectively, designs incorporating rigid-flex boards proffer a adaptable and dependable resolution for electronic merchandise necessitating a meld of rigid and flexible circuits. They enable the creation of compact, durable, and high-performance devices in various industries, including aerospace, medical, automotive and consumer electronics.
Guidelines of Flex PCB and Rigid-Flex PCB Design
In today’s evolving landscape of PCB design, engineers are necessitated to harbor an extensive cognition of both flex and rigid-flex PCB designs. The era of sole dependence on rigid printed circuit boards has unmistakably passed. To guarantee success in crafting an apt printed circuit board for a particular application, comprehending the complexities and primary distinguishing characteristics of each design methodology is absolutely critical.
If you find yourself at the crossroads of deciding whether to design a flexible PCB or a rigid-flex PCB, adhering to these directions becomes paramount to facilitate a proficient navigation through the procedure:
Guidelines for Flex PCB Design
Initiating a project focused on flex PCB design necessitates the adherence to critical guidelines to ascertain triumphant results. Consider the following guidelines to navigate the flex PCB design process effectively:
1.Understand Flex PCB Fundamentals:
Acquaint yourself with the rudimentary principles of flex PCB design. Equip yourself with knowledge about the properties and features of flexible materials such as polyimide or polyester film and their influence on the design process. Develop your understanding regarding the capabilities and limitations of flex circuits, taking into account elements like bend radius, flexibility and durability.
2.Define Application Requirements:
Make sure to outline the needs of your particular project. Take into account factors like space limitations, temperature variations, electrical functionality and environmental surroundings. These criteria will guide your decisions when designing helping you pick the suitable materials and design techniques.
3.Select Suitable Materials:
Choose the right materials for your flex PCB design. Consider the flexibility, thermal stability, dielectric properties, and compatibility with your application’s requirements. Ensure that the chosen materials can withstand the expected mechanical stress, temperature variations and chemical exposure.
4.Optimize Component Placement:
Carefully plan and optimize the placement of components on the flex PCB. Consider the mechanical stress and strain that components may experience during bending or flexing. Place components strategically to minimize stress concentration and ensure reliable electrical connections.
5.Route Traces and Conductors:
Exercise meticulous care when routing traces and conductors on the flex PCB. Employ suitable trace widths, spacing, and impedance control to uphold signal integrity. Keep the usage of vias and acute bends to a minimum to decrease stress on the flex circuit. Adhere to the design directives and norms provided by the manufacturer or as per industry standards.
6.Provide Adequate Reinforcement:
Reinforce areas of the flex PCB that may experience higher stress, such as connectors or areas where components are mounted. Use additional adhesive or stiffeners to enhance mechanical stability and prevent flex circuit damage during assembly or operation.
7.Perform Thorough Design Verification:
Before manufacturing the flex PCB, conduct thorough design verification. Use design rule checks (DRC) and electrical rule checks (ERC) to ensure the design meets the required specifications. Simulate and analyze the design for signal integrity, thermal performance, and reliability using appropriate software tools.
8.Collaborate with Fabrication Experts:
Work closely with experienced flex PCB manufacturers or fabricators. Consult them during the design process to ensure manufacturability and to address any specific requirements or constraints. Leverage their expertise to optimize the design for production and assembly.
9.Test and Validate the Design:
Once the flex PCB is manufactured, perform rigorous testing and validation. Verify electrical connectivity, functionality, and performance under expected operating conditions. Conduct environmental and reliability tests to ensure the design meets the desired standards and specifications.
Guidelines for Rigid-Flex PCB Design
Designing a rigid-flex PCB necessitates deliberate contemplation of both rigid and flexible sections to ascertain a prosperous result. Adhere to these directives to proficiently steer the course of the rigid-flex PCB design progression.
1.Understand Rigid-Flex PCB Fundamentals:
Acquaint yourself with the elementary theories of rigid-flex PCB design. Absorb knowledge about the integration of rigid and flexible sections in a solitary circuit, which permits compact and intricate designs. To learn the strengths and constraints of rigid-flex PCB, encompassing their mechanical steadfastness, dependability and flexibility.
2.Define Application Requirements:
Clearly define the requirements of your specific application. Consider factors such as space constraints, mechanical stress, temperature range, electrical performance and environmental conditions. These requirements will steer your design judgments and enable you to opt for the suitable materials and design techniques for both the the rigid and flexible sections.
3.Plan the Rigid-Flex Configuration:
Determine the optimal configuration for the rigid and flexible sections of the PCB. Consider the mechanical stress and strain that the PCB may experience during operation or assembly. Identify areas where rigid sections are necessary for component mounting or connector interfaces, and plan flexible sections where bending or flexing is required.
4.Select Suitable Materials:
Choose materials that are suitable for both the rigid and flexible sections of the PCB. Take into account the mechanical resilience, thermal constancy, dielectric traits and compatibility with your application’s stipulations. Ensure that the elected materials possess the durability to bear the anticipated mechanical strain, temperature fluctuations, and chemical vulnerability in both sturdy and pliable regions.
5.Optimize Component Placement:
Carefully plan and optimize the placement of components on the rigid-flex PCB. Consider the mechanical stress and strain that components may experience during bending or flexing. Place components strategically to minimize stress concentration and ensure reliable electrical connections in both the rigid and flexible sections.
6.Route Traces and Conductors:
One ought to strictly scrutinize the routing of traces and conductors in both the sturdy and pliable segments of the PCB. Implement fitting trace widths, spacing, and impedance supervision to preserve signal integrity. Truncate the utilization of vias and acute bends in the malleable areas to dodge imposing strain on the flex circuit. Adhere to the design norms and directives furnished by the manufacturer or by industry benchmarks.
7.Provide Adequate Reinforcement:
Reinforce areas of the rigid-flex PCB that may experience higher stress, such as connectors or areas where components are mounted. Use additional adhesive or stiffeners to enhance mechanical stability and prevent flex circuit damage during assembly or operation.
8.Perform Thorough Design Verification:
Before manufacturing the rigid-flex PCB, conduct thorough design verification. Use design rule checks (DRC) and electrical rule checks (ERC) to ensure the design meets the required specifications. Simulate and analyze the design for signal integrity, thermal performance, and reliability using appropriate software tools.
9.Collaborate with Fabrication Experts:
Work closely with experienced rigid-flex PCB manufacturers or fabricators. Consult them during the design process to ensure manufacturability and to address any specific requirements or constraints. Leverage their expertise to optimize the design for production and assembly.
10.Test and Validate the Design:
Once the rigid-flex PCB is manufactured, perform rigorous testing and validation. Verify electrical connectivity, functionality, and performance under expected operating conditions. Conduct environmental and reliability tests to ensure the design meets the desired standards and specifications.
Key Differences Between Flex PCB and Rigid-Flex PCB Designs
Flex PCB and rigid-flex PCB are two distinct design architectures with several key differences:
1. Board Materials:
●Flex PCB exclusively use flexible dielectric films like polyimide.
●Rigid-flex PCB incorporate both rigid laminates (such as FR-4 or polyimide) and flex films.
2. Layer Stack-up:
●Flex PCB typically have single or double-sided conductor layers.
●Rigid-flex PCB have more complex layer structures with 4-30+ conductive layers.
3. Circuit Complexity:
●Flex PCB support simple wiring with low component counts.
●Rigid portions on rigid-flex boards allow for high-density ICs, fine lines, and small via structures.
4. Conductor Thickness:
●Flex PCB conductors are usually 12-35 microns thick.
●Rigid-flex boards use 1 oz (35 microns) copper or thicker, up to 3 oz (105 microns).
5. Outline and Form Factor:
●Flex PCB can be fabricated in any 2D shape and fit confined spaces when folded.
●Rigid-flex PCB fold into complex 3D structures but cannot freely flex over their entire length.
6. Dynamic Flexing:
●Flex PCB can bend repeatedly to conform to contours and motions.
●Rigid-flex PCB only flex at discrete points determined in the design.
7. Cost:
●Simple flex PCB are relatively low cost and suitable for basic applications.
●Rigid-flex PCB entail higher fabrication and assembly costs.
8. Reliability Factors:
●Flex PCB require robust strain relief mechanisms to handle dynamic bending.
●Rigid-flex boards need careful pad layouts to avoid cracks and ensure reliability.
It is imperative to comprehend these disparities when choosing between flex PCB and rigid-flex PCB for a particular application. Each pcb types has its unique merits and factors to ponder, and the selection of the suitable design transpires based on the requirements of the scheme.
Frequently Asked Questions (FAQs) on Flex PCB and Rigid-flex PCB Design
Q1. When should a flex PCB be chosen over a rigid-flex PCB?
Flex PCB is the optimal choice when the design requirements involve simple wiring in a confined space, the circuit needs to flex dynamically during operation, there is a need for an extremely lightweight or low-profile solution, or when project budgets are limited. Under these situations, flex PCB yields a more economically viable and fitting resolution in contrast to a rigid-flex PCB, which might introduce unnecessary complexity.
Q2. When should a rigid-flex PCB be selected over a flex PCB?
A rigid-flex PCB turns out to be the suitable pick when the design commands high component populations, multiple strata, and elaborate circuitry. It outperforms in applications requiring interlinking PCB across different forms or when static and dynamic flex zones need to merge on the same board. The adaptability of a rigid-flex PCB accommodates the inclusion of complex ICs and the achievement of various form factors.
Q3. What are some typical applications suited for flex PCB?
Flex PCB technology is employed across numerous sectors, encompassing wearable technology, medical catheters, robotics, consumer electronics cabling, print heads, and military antennas. These specific applications capitalize on the innate flexibility of flex circuits that fulfill dynamic bending and comply with precise design stipulations.
Q4. What types of products typically use rigid-flex PCB?
Rigid-flex PCB technology is widely exploited in items like mobile electronics, aerospace systems, server backplanes, laptops, vehicle cameras, machine automation regulators, and sophisticated medical apparatus. These products implore the amalgamation of highly intricate ICs across various form factors and configurations, thus compelling the utilization of rigid-flex PCB to secure the sought after functionality and dependability.
Q5. Does rigid-flex PCB technology completely replace the need for flex PCB?
Absolutely not, rigid-flex PCBs haven’t fully substituted the requirement for flex PCBs. While rigid-flex PCB offer a hybrid solution that combines the benefits of both rigid and flex PCB, self-standing flex PCBs continue to take up their spot in certain use-cases. For straightforward flex circuitry that predominantly encompasses wiring liasons, minus the sophistication ushered in by rigid-flex design, exclusive flex panels are frequently more appropriate and economically efficient.
The selection between flex PCB and rigid-flex PCB depends on careful consideration of factors such as flexibility requirements, circuit complexity, component density, and cost considerations. Striking the right balance among these factors ensures the optimal choice for a given product’s design and functionality.
Conclusion
Flexible PCB layout and rigid-flex PCB design extend unique benefits and contemplations. Flex PCB confer suppleness, lightweight infrastructure and cost efficiency, thereby fitting for utilization with uncomplicated wiring and confined spaces. Concurrently, rigid-flex PCB tender the capacity to integrate complex circuits and various form factors, thus appropriate for projects demanding high component concentration and diverse forms. By comprehending these distinctions and assessing project prerequisites, engineers are empowered to make educated choices to guarantee fruitful PCB designs.