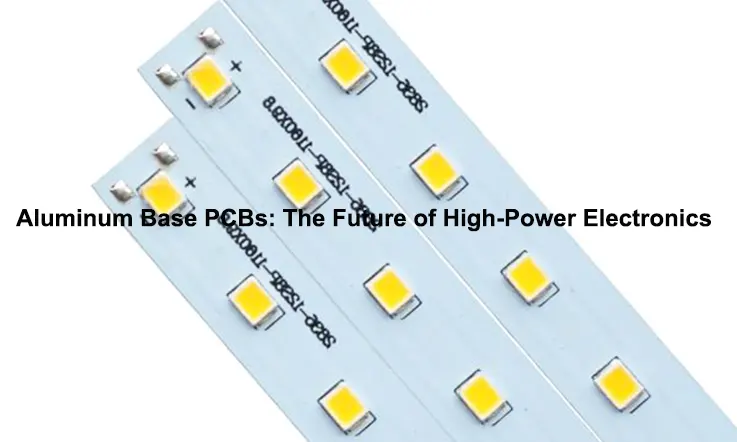
In the competitive landscape of electronics, the quest for efficiency and reliability is relentless. Among the materials that have emerged, aluminum base PCBs stand out for their remarkable ability to handle high-power applications. With technology advancing at breakneck speed, aluminum base PCBs have proven to be not just an option, but a necessity for high-performance electronic devices. This article dives deeper into their benefits, applications, and the promising future they hold, while incorporating the latest insights and trends in the industry.
Why Aluminum Base PCBs?
Aluminum base PCBs shine when it comes to handling heat. They offer superior thermal conductivity, making them a no-brainer for high-power applications like LED lighting and power amplifiers. By effectively dissipating heat, these boards keep devices running cool, ensuring longevity and reliability. It’s like having a trusty sidekick that’s always ready to take the heat!
Key Advantages:
Advantage | Description | Impact |
Superior Thermal Management | Aluminum conducts heat away from components efficiently | Reduces risk of overheating |
Enhanced Durability | The robust nature of aluminum stands up to tough environments | Prolongs lifespan of electronic devices |
Lightweight Design | Aluminum is lighter than many alternatives | Ideal for portable applications |
As we continue to unpack the benefits of aluminum base PCBs, it becomes clear that these boards offer a combination of performance and reliability that’s hard to beat. Whether it’s in renewable energy systems or the latest consumer electronics, aluminum base PCBs are paving the way for the future of high-power technology.
Types of Aluminum Base PCBs
There are several types of aluminum base PCBs that are popular in various applications, each tailored to meet specific needs. Let’s break down some of the most common types:
1. Single Layer Aluminum Base PCB
This type features a single layer of copper traces on one side of the aluminum core. It’s a solid choice for straightforward applications where effective heat dissipation is key. Think of it as your trusty workhorse—reliable and efficient.
2. Double Layer Aluminum Base PCB
Double layer aluminum base PCBs come with copper traces on both sides of the aluminum core. This design allows for more complex circuit layouts and higher component density, making it perfect for applications that need a little extra oomph.
3. Multilayer Aluminum Base PCB
Multilayer aluminum base PCBs consist of multiple layers of copper traces and dielectric material sandwiched between aluminum cores. These are the heavyweights of circuit design, used in applications requiring high density and intricate layouts.
4. Hybrid Aluminum Base PCB
Hybrid aluminum base PCBs mix aluminum cores with materials like FR4 or ceramic substrates. This combo gets you the best of both worlds—outstanding thermal management paired with strong electrical performance, ideal for demanding applications.
5. High Thermal Conductivity Aluminum Base PCB
These boards feature specially designed aluminum cores with enhanced thermal conductivity. They’re built for high-power applications that demand efficient heat dissipation, ensuring your devices run smoothly even under pressure.
Summary Table of Aluminum Base PCB Types
Type | Description | Application Examples |
Single Layer Aluminum Base PCB | One layer of copper traces | Basic LED lighting |
Double Layer Aluminum Base PCB | Copper traces on both sides | Complex power amplifiers |
Multilayer Aluminum Base PCB | Multiple layers for high density | Advanced communication systems |
Hybrid Aluminum Base PCB | Combines aluminum with FR4 or ceramic | Automotive electronics |
High Thermal Conductivity PCB | Enhanced thermal properties | High-power LED systems |
Choosing the right type of aluminum base PCB hinges on the specific requirements of your application—whether it’s power handling, thermal management, or circuit complexity. Each type offers unique benefits, making aluminum base PCBs a versatile option for modern electronics.
Key Benefits of Aluminum Base PCBs
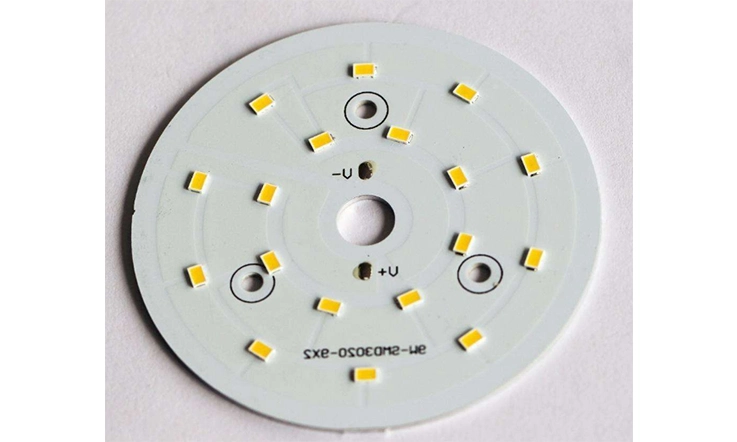
Superior Thermal Management
Aluminum base PCBs bring exceptional thermal management capabilities that are hard to ignore. In high-power applications, excess heat can cause significant performance hiccups or even lead to component failure. With thermal conductivity ranging from 1 to 9 W/mK, aluminum efficiently dissipates heat, keeping devices operating within safe temperature limits.
Take a look at a case study involving a major telecommunications company that adopted aluminum base PCBs for their new line of power amplifiers. These amplifiers, built to handle high-frequency signals, faced overheating issues with traditional FR-4 boards. After switching to aluminum base PCBs, the company noted a 30% reduction in thermal resistance, which led to a 25% boost in performance stability and a 15% drop in energy consumption. This move not only extended the amplifiers’ lifespan but also ramped up customer satisfaction by delivering reliable performance when it mattered.
Thermal Management Summary:
Metric | Before Transition | After Transition | Improvement |
Thermal Resistance | High | 30% lower | Reduced overheating |
Performance Stability | Moderate | 25% higher | More reliable output |
Energy Consumption | Baseline | 15% lower | Cost savings |
Cost-Effectiveness and Reliability
Manufacturers are always on the hunt for ways to cut costs while keeping quality in check. Aluminum base PCBs excel in this regard. Their durability means they can handle tougher conditions compared to other materials. Fewer failures lead to lower warranty claims and happier customers.
For instance, a leading LED manufacturer dealt with frequent failures in their lighting systems, which resulted in costly recalls and unhappy clients. After making the switch to aluminum base PCBs, they saw a whopping 40% decrease in failure rates over two years. Thanks to enhanced thermal management, their LED systems operated more efficiently, cutting energy consumption by around 20%. This shift not only brought significant cost savings but also boosted their reputation in the market.
Cost-Effectiveness Summary:
Metric | Before Transition | After Transition | Improvement |
Failure Rate | High | 40% lower | Increased reliability |
Energy Consumption | Baseline | 20% lower | Reduced operational costs |
Customer Satisfaction | Moderate | Significantly higher | Enhanced market reputation |
So, aluminum base PCBs deliver both thermal management and cost-effectiveness, making them a smart choice for manufacturers looking to elevate their products. When it comes to keeping the heat down and the performance up, these boards are definitely worth their weight in gold!
Applications of Aluminum Base PCBs
High-Power Electronics
Aluminum base PCBs are the go-to choice for high-power applications like LED lighting and power supply systems. In LED technology, these boards shine by effectively managing the heat generated, which helps extend the lifespan of the bulbs and keeps their brightness intact. Think of aluminum base PCBs as a reliable sidekick—always there to keep things cool when the heat is on!
Benefits in LED Applications:
Metric | Traditional PCB | Aluminum Base PCB | Improvement |
Heat Management | Limited | Superior | Prolonged lifespan |
Brightness Stability | Fluctuates | Consistent | Enhanced performance |
Lifespan of Bulbs | Shorter | Longer | Reduced replacement costs |
Custom Solutions for Diverse Industries
The versatility of aluminum PCBs allows manufacturers to tailor designs for a wide range of applications, whether it’s for automotive, telecommunications, or consumer electronics. Custom solutions enable companies to meet unique demands without sacrificing quality. In this ever-evolving market, being able to adapt quickly is key—like a chameleon blending into its surroundings!
Customization Examples:
Industry | Application | Custom Solution |
Automotive | Power distribution systems | Specialized thermal management designs |
Telecommunications | Signal amplifiers | Compact, high-efficiency layouts |
Consumer Electronics | Smart devices | Lightweight, flexible designs |
Aluminum base PCBs not only provide essential thermal management but also offer the flexibility that modern industries need. By customizing solutions, manufacturers can stay ahead of the curve, ensuring their products meet the demands of today’s dynamic market.
Comparison: Aluminum Base PCBs vs. Copper Core PCBs
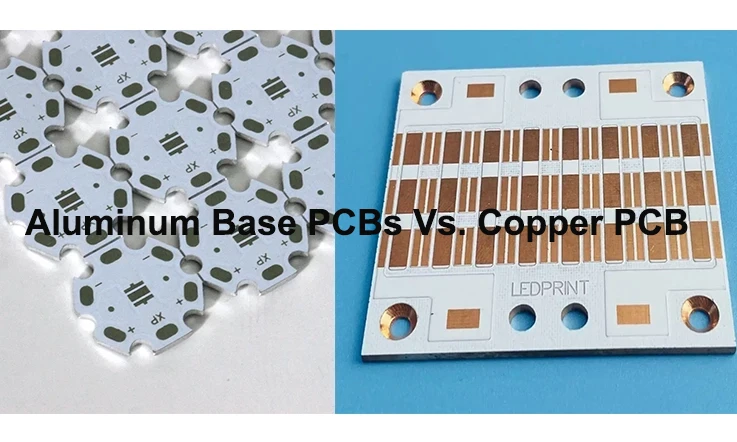
Thermal Performance Analysis
When comparing aluminum PCBs to copper PCBs, thermal performance is often a key consideration. While copper has long been revered for its conductivity, aluminum often shines in high-load scenarios, providing better heat management.
A recent study conducted by an industry research group found that aluminum PCBs exhibited a thermal cycling capability that surpassed copper boards by 25%. In practical terms, this means that devices utilizing aluminum base PCBs can withstand more rigorous thermal fluctuations, reducing the risk of component failure.
Weight Considerations
Another advantage of aluminum PCBs is their weight. Aluminum is significantly lighter than copper, which is a critical factor in applications like aerospace and automotive industries where weight reduction is paramount. This lightweight property helps improve fuel efficiency in vehicles and reduces operational costs in various applications.
Thermal Performance Comparison of Aluminum PCBs vs. Traditional Materials
Property | Aluminum PCB | Copper PCB |
Thermal Conductivity (W/mK) | 1 – 9 | 390 |
Thermal Cycling Capability | 25% Higher than Copper | / |
Operating Temperature Range (°C) | -40 to 85 | -40 to 125 |
Cost Effectiveness | High (Low Failure Rate) | Medium (Moderate Failure Rate) |
Weight | Lighter | Heavier |
Design Considerations
From a design perspective, aluminum base PCBs offer more flexibility than traditional materials. The unique properties of aluminum allow for innovative layouts that maximize both performance and space.
For example, in a project involving a compact drone, engineers faced challenges in fitting all components while maintaining thermal efficiency. By employing aluminum base PCBs with a custom layout, they successfully minimized the board’s footprint while optimizing heat dissipation. This innovative approach not only enhanced the drone’s performance but also improved battery life by 15%, providing a significant edge in a competitive market.
Manufacturing Processes for Aluminum Base PCBs
Fabrication Techniques
The manufacturing of aluminum base PCBs involves several intricate steps that are key to achieving top-notch performance. From substrate preparation to etching and lamination, precision is the name of the game at every turn. For instance, the surface finish applied to aluminum PCBs can greatly influence their thermal and electrical performance. Techniques like anodizing or plating enhance both durability and conductivity, which is essential for high-performance applications.
Key Fabrication Techniques:
Technique | Description | Benefits |
Anodizing | An electrochemical process that thickens the aluminum oxide layer | Increases corrosion resistance, enhances insulation |
Plating | Applying a layer of metal onto the surface for improved conductivity | Boosts electrical performance, enhances durability |
Surface Finishing | Various methods to smooth and protect the surface | Ensures optimal thermal transfer, prolongs lifespan |
Manufacturers are often all in when it comes to investing in advanced equipment. By embracing automation and precision engineering, they can crank out aluminum PCBs that meet the rigorous demands of today’s market. This isn’t just about keeping up; it’s about setting the pace for what’s next.
IPC Standards and Quality Control
Sticking to IPC standards is non-negotiable in aluminum PCB production. These guidelines act like a roadmap, ensuring that products hit specific reliability and performance benchmarks. Rigorous quality control measures throughout the manufacturing process help guarantee that each board can withstand real-world challenges.
Think of IPC standards as the playbook for high-quality manufacturing—making sure that every PCB produced is ready to roll when it’s put to the test. Whether it’s through visual inspections, thermal performance testing, or automated checks, manufacturers are leaving no stone unturned to deliver boards that don’t just meet expectations but knock them out of the park.
Quality Control Measures:
Measure | Description | Purpose |
Visual Inspection | Manual checks to identify defects | Catches surface-level issues early |
Thermal Performance Testing | Evaluating how well boards handle heat | Ensures thermal efficiency and reliability |
Automated Checks | Using machines to monitor production | Increases efficiency and accuracy |
Therefore, the manufacturing processes for aluminum base PCBs are a blend of art and science. With the right techniques and adherence to quality standards, manufacturers are well-equipped to deliver products that perform reliably in demanding applications. The future is looking bright for those who are willing to put in the work!
Challenges and Solutions in Aluminum Base PCB Manufacturing
While aluminum base PCBs come with a host of benefits, they also present their share of hurdles during manufacturing. Let’s dive into the nitty-gritty of these challenges and how savvy manufacturers are tackling them head-on.
Thermal Expansion Woes
One of the biggest headaches in aluminum PCB manufacturing is thermal expansion. Aluminum tends to expand more than traditional materials like FR-4 when temperatures rise. If engineers don’t keep a close eye on this during the design phase, it could lead to warping or misalignment, making for a rough ride in the assembly process.
Smart Solutions: To tackle this issue, many manufacturers are using advanced simulation techniques to predict how their designs will behave under various thermal conditions. This proactive approach allows them to tweak their designs early on, ensuring everything stays snug as a bug in a rug when things heat up. By incorporating strategies like multi-layer construction or using thermal vias, they can enhance stability and keep those boards in tip-top shape.
Lamination Quality
Another sticky situation comes from achieving consistent lamination quality. Aluminum base PCBs require a precise bonding process to ensure the copper traces and aluminum substrate adhere well. Any slip-up here can lead to reliability issues down the line. It’s like building a house on a shaky foundation; it just won’t hold up!
Keeping It Tight: To ensure solid lamination, manufacturers are investing in top-notch equipment and quality control processes. Many are implementing automated inspection systems that monitor the lamination process in real-time. This way, they can catch any potential problems before they escalate, ensuring the final product meets all the high standards that customers expect.
Cost Management
Cost is always a hot topic in PCB manufacturing. Aluminum base PCBs can be pricier to produce than traditional options due to the specialized materials and processes involved. However, savvy manufacturers know that cutting corners isn’t the way to go. Instead, they focus on streamlining production to keep costs manageable.
Innovative Approaches: By adopting lean manufacturing principles and investing in automation, companies can boost efficiency and trim unnecessary expenses. Plus, using recycled aluminum not only helps keep costs in check but also appeals to eco-conscious customers. It’s a win-win situation!
Future Trends in Aluminum Base PCB Technology
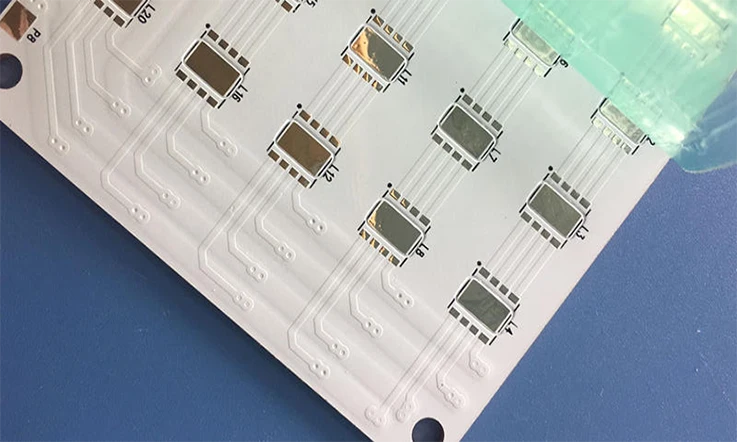
The future of aluminum base PCB technology is shining bright, with a wave of innovations on the horizon. As engineers roll up their sleeves and dive into new materials and techniques, aluminum PCBs are set to break the mold in exciting ways.
Innovations in Design and Materials
Advancements in materials are at the forefront of this transformation. Think about integrating new composites or hybrid structures—these innovations promise to take aluminum PCBs to the next level. For example, engineers are exploring novel thermal management techniques like embedded heat sinks and advanced coatings. These enhancements are designed to push the limits of performance, ensuring that aluminum PCBs can handle even the toughest high-power applications.
Key Innovations:
Innovation Type | Description | Potential Benefits |
New Composites | Hybrid materials that combine aluminum with other elements for enhanced performance | Better thermal conductivity, weight reduction |
Embedded Heat Sinks | Heat sinks integrated directly into the PCB design for efficient heat dissipation | Improved thermal management, space-saving |
Advanced Coatings | Innovative surface treatments to protect against environmental factors | Increased durability, reduced wear |
Expanding Market Opportunities
The demand for aluminum base PCBs keeps climbing as industries wake up to their many perks. Sectors like renewable energy, electric vehicles, and smart technology are set to make aluminum PCBs key players in the electronics game.
Manufacturers who jump on this trend are bound to find new markets and opportunities, turning challenges into success stories. It’s all about seizing the moment and harnessing aluminum’s unique properties to drive innovation forward. Those who adapt quickly will be riding the wave of progress while others are still trying to catch up.
Wrapping Up: Why Aluminum Base PCBs Are the Future
As we navigate the ever-evolving landscape of electronics, aluminum base PCBs are not just a trend—they’re here to stay. Their unmatched thermal management, cost-effectiveness, and adaptability position them at the forefront of high-power applications. Whether you’re a PCB designer, an electronic manufacturer, or just starting in the industry, embracing aluminum base technology is a savvy move.
So, what are you waiting for? Dive into the world of aluminum base PCBs and discover how they can elevate your projects to new heights. The future is bright, and aluminum base PCBs are leading the way!
Frequently Asked Questions (FAQs)
What are the primary advantages of aluminum PCBs?
Aluminum PCBs offer superior thermal management, cost-effectiveness, and reliability, making them ideal for high-power applications.
How do aluminum PCBs compare to traditional materials?
Compared to copper PCBs, aluminum provides better thermal performance and design flexibility, enhancing overall efficiency.
What industries benefit the most from aluminum base PCBs?
Industries such as automotive, telecommunications, and consumer electronics benefit greatly from aluminum base PCBs due to their tailored applications and efficiency.