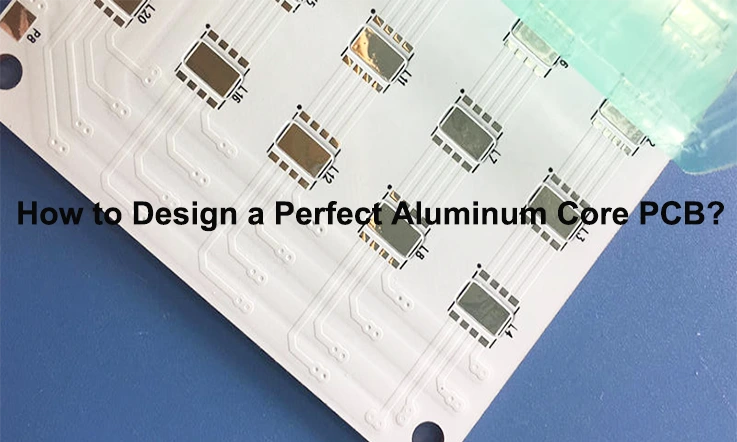
Aluminum Core PCBs are really shaking things up in the design scene, providing a savvy solution for thermal management and signal integrity. With stellar thermal conductivity, aluminum Core PCB help keep components chill, preventing overheating during operation. Take LED lighting applications, for instance; when heat can be a real hassle, aluminum Core PCB substrates are like your trusty sidekick, making sure everything stays on point.
These Aluminum Core PCB Board also amp up signal integrity by lowering impedance and cutting down on signal loss. This means faster and more dependable data transfer—absolutely essential for high-speed applications like RF and microwave circuits. Designers looking to level up their projects can easily weave aluminum substrates into their designs, crafting PCBs that tackle the demands of modern tech.
So, if you’re ready to take your designs to the next level, consider using aluminum core PCBs in your next project. Let’s turn your ideas into something that truly stands out!
Introduction to Aluminum Core PCBs
Aluminum core printed circuit boards (PCBs) are making waves in the electronics industry, especially when it comes to keeping things cool under pressure. By using aluminum as a substrate, these boards bring thermal conductivity that often exceeds 1.0 W/mK, making them a solid pick over traditional materials like FR4. This feature is a game plan for sectors like LED lighting, automotive, and telecommunications, where efficient thermal management isn’t just nice to have—it’s a must.
In high-power applications like LED assemblies, effective thermal management is key to ensuring longevity. Data shows that devices with optimized heat dissipation can last up to 30% longer. So, when it comes to performance, staying chill is where it’s at! Make sure your designs prioritize heat management to keep things running strong over the long haul. Let’s get those designs right and maximize reliability!
What is an Aluminum Core PCB?
An aluminum core PCB combines a layer of aluminum with standard PCB materials such as epoxy resin and fiberglass. This smart combination not only ensures efficient heat dissipation but also maintains the necessary electrical insulation properties. The aluminum substrate serves as a heat sink, pulling heat away from critical components to prevent thermal buildup that can lead to device failure.
Advantages of Aluminum Core PCBs
●Superior Thermal Management and Thermal Conductivity
One of the standout benefits of aluminum core PCBs is their impressive ability to manage heat. In high-current applications, rapid heat dissipation is necessary to maintain performance. Engineers frequently use thermal vias to enhance heat transfer from the circuit to the aluminum substrate, ensuring that critical components stay within safe temperature limits. For example, in power supply circuits, this technique helps keep sensitive components functioning properly under heavy loads.
Thermal Resistance Analysis: When designing these boards, conducting a thermal resistance analysis is key. It helps predict thermal performance by calculating the thermal impedance of various layers and making sure the design meets required thermal thresholds.
Feature | Aluminum Core PCB | FR4 PCB |
Thermal Conductivity | > 1.0 W/mK | ~0.5 W/mK |
Heat Dissipation Efficiency | High | Moderate |
Weight | Lightweight | Heavier |
Cost | Moderate | Lower initial cost |
●Lightweight Design for Enhanced Performance in Applications
The lightweight design of aluminum core PCBs brings significant advantages in applications where minimizing overall weight is a top priority—think aerospace and automotive sectors. By using aluminum instead of heavier materials like copper, engineers can develop more efficient systems without compromising performance. For instance, in aircraft design, reducing weight can enhance fuel efficiency, making a real difference in operational costs.
For instance, in the automotive sector, aluminum core PCBs are commonly used in power electronics for electric vehicles. They help manage the thermal loads associated with high-voltage battery systems and power inverters, keeping things running smoothly and enhancing overall vehicle efficiency.
Advanced Design Considerations for Aluminum Core PCBs
When it comes to designing aluminum core PCBs, here are some advanced factors to keep in mind:
Layer Stack-Up Design: A well-planned layer stack-up is fundamental for optimizing thermal and electrical performance. This thoughtful design approach enhances heat dissipation and boosts signal integrity. For instance, in high-frequency applications, a carefully arranged stack can significantly reduce electromagnetic interference, leading to clearer signal transmission.
Thermal Via Placement: Strategic placement of thermal vias can seriously boost heat transfer efficiency. Engineers often utilize simulation software to find the best spots for thermal vias in the PCB layout.
Dielectric Properties: Choosing the right dielectric material alongside aluminum is key to ensuring solid electrical insulation while maintaining thermal performance. Advanced materials with high thermal conductivity and low dielectric loss are the way to go.
Ready to elevate your PCB designs? Explore the benefits of aluminum core technology! With its exceptional thermal management and lightweight structure, you can create high-performance electronic applications built to last. Imagine developing devices that run efficiently while keeping temperatures in check—perfect for everything from LED lighting to automotive systems.
Don’t hesitate—reach out today to discuss how aluminum core PCBs can enhance your next project! Let’s make it happen together!
Key Technical Considerations in Aluminum Core PCB Design

When designing aluminum core PCBs, there are several key technical factors professionals should consider to optimize both performance and reliability. Let’s dive into these aspects that can make a real difference in your designs.
Material Selection for Optimal Performance
●Comparing Aluminum Core PCBs with Copper Core PCBs
In selecting materials for PCBs, the choice between aluminum and copper cores can significantly impact performance, thermal management, and cost-effectiveness.
Feature | Aluminum Core PCB | Copper Core PCB |
Thermal Conductivity | 1~9 W/mK | >3.5 W/mK |
Density | 2.7 g/cm³ | 8.96 g/cm³ |
Cost | Lower | Higher |
Weight | Lightweight | Heavier |
Corrosion Resistance | Good | Moderate |
Applications | LED, automotive | RF, power supplies |
While copper is known for its excellent thermal conductivity, aluminum’s lightweight and cost-effective properties make it a preferred choice for many applications. In areas where weight limitations are critical—like aerospace and portable electronics—aluminum often stands out. Its reduced weight allows for designs that enhance efficiency and performance while keeping costs manageable.
Additionally, aluminum’s resistance to corrosion helps extend the lifespan of components, particularly in challenging environments. For example, outdoor LED lighting can benefit from aluminum, ensuring that fixtures endure harsh conditions over time.
So, when considering materials for your next project, aluminum might be the smart choice. Let’s leverage aluminum’s advantages to create effective and long-lasting designs!
Thermal Performance Requirements
●Importance of Thermal Management in LED Lighting Applications
In high-power LED applications, managing heat effectively is key, as excessive temperatures can lead to reduced performance and shorter lifespans. Aluminum core PCBs excel in thermal management, allowing efficient heat transfer from the LED chips to the substrate. This capability enables designers to rely on aluminum to keep temperatures in check, ensuring LEDs operate at their best.
For example, in street lighting, the ability to dissipate heat efficiently can significantly extend the lifespan of the LEDs. By using aluminum core PCBs, manufacturers create systems that are not only reliable but also economically sound.
Thermal Interface Materials (TIMs): To further enhance thermal performance, using high-conductivity TIMs between the LED and the PCB can optimize heat transfer. Engineers often select materials like thermal paste or thermal pads that provide excellent conductivity while ensuring reliable adhesion.
Heat Sink Design: For applications requiring maximum thermal dissipation, integrating a heat sink into the PCB design can provide additional heat management. This is especially useful in high-intensity lighting systems where thermal load is significant.
Simulation and Analysis: Utilizing thermal simulation software can aid engineers in predicting heat distribution across the PCB. This allows for strategic placement of thermal vias and copper pours, optimizing the board layout to enhance heat dissipation.
Real-world examples have shown that companies using aluminum core PCBs in their LED products often report performance improvements of 15-20% compared to traditional FR4 boards. By keeping thermal performance at the forefront of design considerations, engineers can achieve significant gains in efficiency and product longevity.
Are you ready to take your PCB design to the next level? Don’t overlook the critical role of thermal management in your projects. Explore aluminum core technology for enhanced performance and reliability. Contact us today to discuss how we can support your design needs!
How to Design Multilayer Aluminum Core PCBs?
Designing multilayer aluminum core PCBs is a complex yet rewarding challenge that requires technical expertise and strategic planning. By keeping a close eye on design principles and addressing common challenges, you can craft boards that are not only functional but also reliable.
Understanding Multilayer Design Principles
In multilayer designs, stacking several circuitry layers requires a clear understanding of how each layer interacts. Here’s how to get it right:
Layer Stack-Up Configuration: Your stack-up should optimize thermal and electrical performance. Position the aluminum core directly under heat-generating components, allowing heat to dissipate effectively. Think of it as placing the ice pack right where the bruise is—maximizing relief!
Thermal Via Placement: Properly placed thermal vias are essential for managing heat. Use thermal vias to connect the aluminum core to outer layers, enabling efficient heat transfer. This strategy helps prevent hotspots from popping up unexpectedly.
Parameter | Recommended Value |
Via Diameter | 0.3 – 0.5 mm |
Via Thermal Conductivity | ≥ 2.5 W/mK |
Via Pad Size | 1.0 mm |
Ground and Power Plane Design: Integrating dedicated ground and power planes close to the aluminum core can significantly improve signal integrity. This setup acts as a solid reference, much like a sturdy anchor, minimizing noise and interference.
Impedance Control: For high-speed signals, controlling impedance is key. Calculate trace widths based on your specific dielectric material and desired impedance. Keeping traces consistent can help avoid signal loss.
Challenges and Solutions in Multilayer Aluminum Core PCB Design
●Signal Integrity Across Multiple Layers
Maintaining signal integrity in multilayer designs can feel like walking a tightrope, but with the right techniques, it’s manageable:
Controlled Impedance Techniques: When it comes to high-frequency signals, implementing controlled impedance design is a must. To achieve the desired impedance, carefully tailor the trace width and spacing on the PCB. This approach helps minimize reflections, keeping signals crisp and clear. For instance, in RF applications, having well-defined trace widths can make all the difference in signal integrity. By fine-tuning these parameters, designers ensure that signals maintain their shape over longer distances, reducing issues that can arise from impedance mismatches.
Differential Signaling: For critical paths, differential signaling is your ally. By sending equal and opposite signals through paired traces, you can cancel out noise and interference, leading to clearer data transmission. It’s like having a buddy system for your signals!
Layer Pairing for Signal Integrity: Group signal layers with adjacent ground or power planes to create a supportive environment. This pairing can reduce loop areas and enhance signal clarity. A solid foundation goes a long way, much like a good pair of shoes for a long hike.
Simulation and Testing: Don’t skip out on simulation and testing! Use simulation software to visualize thermal and electrical performance, and validate your design with prototypes. Early detection of issues is like finding a leak in your boat before hitting the water.
Are you ready to take your PCB design to the next level? Don’t cut corners—embrace thorough planning and advanced techniques in your projects. By focusing on details like controlled impedance and effective thermal management, you can ensure top-notch performance.
For example, when designing for high-frequency applications, the right trace width can minimize signal reflections, keeping your signals sharp.
Reach out today and discover how our expertise can guide you in crafting the ideal design that meets your needs and exceeds expectations!
Step-by-Step Guide to the Design Process
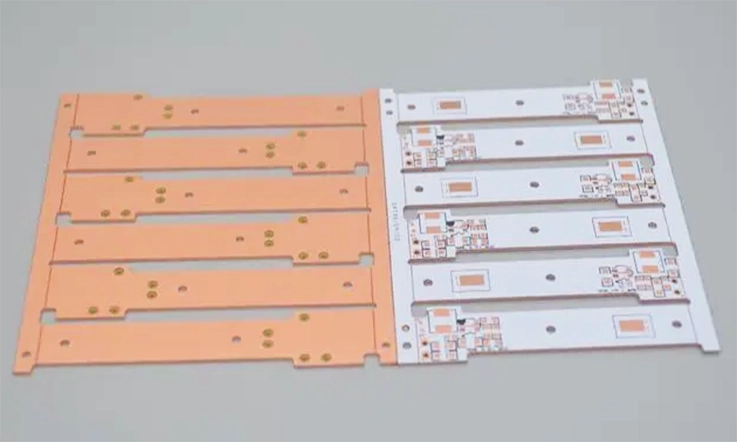
Now that you’re up to speed with the basics of aluminum core PCB design, it’s time to dive into the nitty-gritty. This guide will walk you through the design process step by step, ensuring you’re equipped to create a top-notch product.
1. Schematic Design Best Practices for Aluminum Core PCBs
Clarity is paramount in schematic design. Here’s how to keep things organized and efficient:
Thorough Annotation: Clearly annotate your designs, specifying all materials, layer configurations, and critical parameters. This practice not only helps you keep your ducks in a row but also makes it easy for anyone reviewing your design to understand your choices.
Layer Identification: Use distinct labels for each layer, especially when dealing with multilayer configurations. This can prevent confusion during the manufacturing phase, reducing the likelihood of errors that can cost you time and money.
Schematic Element | Best Practice |
Components | Label clearly and consistently |
Layers | Distinguish each layer with unique identifiers |
Connections | Annotate with net names for easy tracking |
●Using CAD Software for Accurate Layouts
Modern CAD software has transformed PCB design, and utilizing the right tools is essential:
Precision Layouts: Software like Altium Designer or Eagle allows you to create precise layouts with ease. Make the most of their intuitive interfaces to streamline your workflow and improve accuracy.
Simulation Features: Take advantage of simulation tools within your CAD software to predict thermal performance. Running thermal simulations can help you spot potential hot spots before you hit the production stage, saving you from costly redesigns.
Design Rule Checks (DRC): Ensure you’re running DRCs to catch any errors early in the process. This feature checks for violations in your design that could lead to production issues. It’s like having a second set of eyes on your work!
2. Manufacturing Techniques for Quality Assurance
Quality assurance is non-negotiable in the manufacturing process. Here’s how to ensure your designs come to life as envisioned:
Collaborative Communication: Work closely with your fabricators by providing detailed specifications and documentation. Clear communication is key in preventing errors and ensuring everyone is on the same page.
Prototyping: Before moving into full-scale production, consider creating prototypes. This allows you to test the design and make necessary adjustments based on real-world performance. Prototyping is like a dress rehearsal—better to fix issues before the big show!
●Ensuring Reliability and Efficiency in Production
Reliability is the name of the game when it comes to manufacturing:
Selecting Reputable Manufacturers: Choose manufacturers with a solid reputation in the industry. Look for those with experience in aluminum core PCB production, as they’ll have the expertise to handle your specific needs.
Thorough Inspections: Conduct detailed inspections during production. Regular checks can help catch any discrepancies early on, allowing you to address them before they escalate. This proactive approach is like having a safety net for your designs.
Inspection Stage | Recommended Action |
Pre-production | Review specifications and prototypes |
During production | Conduct regular quality checks |
Post-production | Final inspection before shipping |
Ready to tackle your next PCB project? Don’t leave success to chance—utilize these best practices and get in touch for expert support to elevate your designs!
Cost Analysis of Aluminum Core PCBs
Understanding the costs associated with aluminum core PCBs is key for effective budgeting in any project involving electronic components. Let’s dive into the financial implications to help you make sound decisions.
Cost Comparison with FR4 Materials
While aluminum core PCBs often come with a higher initial price tag compared to traditional FR4 boards, the long-term advantages can be worth the investment. For instance, aluminum’s superior thermal management capabilities can lead to enhanced product reliability and lifespan. A study showed that products utilizing aluminum core PCBs had a failure rate 25% lower than those using FR4 under similar conditions.
When evaluating lifecycle costs, consider the durability and performance benefits. Products that operate at lower temperatures generally consume less energy, leading to further savings over time. So, while the upfront costs might pinch a bit, the overall savings can add up like a snowball rolling downhill.
Cost Factors | Aluminum Core PCBs | FR4 Materials |
Initial Cost | Higher | Lower |
Lifespan | Longer | Shorter |
Failure Rate | Lower (25% reduction) | Higher |
Energy Efficiency | Better | Standard |
●Factors Influencing Manufacturing Costs
Several elements can influence the manufacturing costs of aluminum core PCBs, and being aware of these can help you manage your budget effectively:
Material Selection: The choice between different aluminum grades and thicknesses can impact costs. Higher-quality materials often come with a premium but can enhance thermal performance, which pays off in the long run.
Design Complexity: More intricate designs can increase both manufacturing time and costs. Simplifying the design while maintaining functionality can significantly reduce expenses. For example, a straightforward single-layer design might cost less than a complex multilayer setup.
Production Volume: Higher production volumes typically lower the per-unit cost due to economies of scale. If you’re anticipating a large order, negotiating with your manufacturer can yield better rates.
Don’t leave money on the table—understanding these financial implications will empower you to make the best decisions for your projects! Reach out today to explore how we can help you navigate these considerations!
Practical Applications of Aluminum Core PCBs
Aluminum core PCBs are highly adaptable components utilized across various industries thanks to their outstanding thermal management properties and robustness. Let’s dive into the specific sectors where these boards truly excel.
Industries Utilizing Aluminum Core PCBs
●LED Lighting Solutions and Their Demands
Aluminum core PCBs have gained traction in energy-efficient lighting applications, particularly for LEDs. These boards excel in heat dissipation, addressing the significant thermal challenges that LEDs face during operation. By effectively managing heat, these PCBs not only boost the performance of lighting systems but also enhance their longevity. If you’re looking to optimize your LED projects, consider how aluminum core technology can make a difference!
For example, companies that switched to aluminum core designs have reported a remarkable 20% increase in energy efficiency. This improvement translates to lower operational costs and a smaller carbon footprint—definitely a win-win.
Application Type | Benefit | Reported Efficiency Increase |
LED Street Lighting | Improved heat dissipation | 20% |
Indoor LED Fixtures | Longer lifespan | 15% |
Automotive Lighting | Enhanced reliability | 18% |
●Consumer Electronics and Emerging Technologies
Aluminum core PCBs are making waves in consumer electronics, particularly in compact devices like smartphones, tablets, and wearables. As manufacturers push the limits of design and functionality, efficient heat management becomes increasingly crucial. These boards excel in heat dissipation, allowing for innovative designs without sacrificing performance.
For instance, a leading smartphone manufacturer integrated aluminum core PCBs into their latest model, resulting in a 30% reduction in heat generation during peak usage. This improvement not only enhanced user experience by preventing overheating but also allowed for a sleeker design without bulky heat sinks.
Device Type | Feature | Performance Improvement |
Smartphones | Slimmer design | 30% less heat generation |
Wearable Devices | Enhanced battery life | 25% longer operation time |
High-Performance Laptops | Increased processing power | 20% faster thermal recovery |
Considering the diverse applications of aluminum core PCBs? Let’s get you started on designing the perfect solution for your next project. Reach out for expert guidance and take your designs to the next level!
Wrapping Up
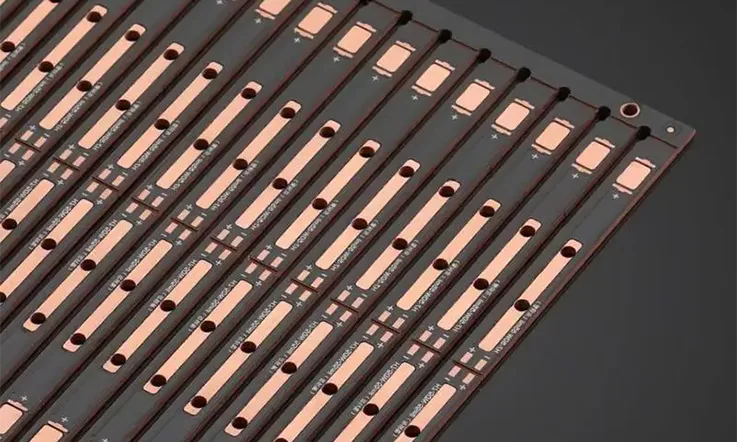
Designing the perfect aluminum core PCB takes attention to detail, a solid understanding of materials, and a focus on thermal management. As the electronics landscape continues to evolve, staying informed about new technologies and best practices will position you for success. Embrace these principles, and you’ll be well on your way to creating outstanding aluminum core PCBs.
“So, gear up, get into the nitty-gritty of the design, and let’s create something extraordinary with aluminum core PCBs!”
FAQ About Aluminum Core PCB Design
What are the benefits of using aluminum core PCBs over traditional materials?
Aluminum core PCBs provide superior thermal management, which is essential for high-performance applications.
Are aluminum core PCBs more expensive than FR4?
While the upfront cost may be higher, the long-term performance benefits often justify the investment.
Can aluminum core PCBs be used in multilayer designs?
Absolutely! With the right design principles, multilayer aluminum core PCBs can be very effective.
What design software do you recommend for PCB design?
Tools like Altium Designer, KiCad, and Eagle are popular choices for PCB design.
How can I troubleshoot common issues in aluminum core PCB design?
Regular inspections and maintaining clear documentation are key. Also, simulations can help predict thermal performance before production.
Related Posts:
1. Differentiating FR4 Glass Fiber and Aluminum Substrate for PCBs
2.Leading Global 10 Aluminum PCB Manufacturers
3.Aluminum Base PCBs: The Future of High-Power Electronics
4.Overview of LED Aluminum PCB
5.Significance of Aluminum Clad PCBs in Advancing Electronic Device
6.How Leveraging Aluminum PCB Substrates: in Your Next Stackup Design?