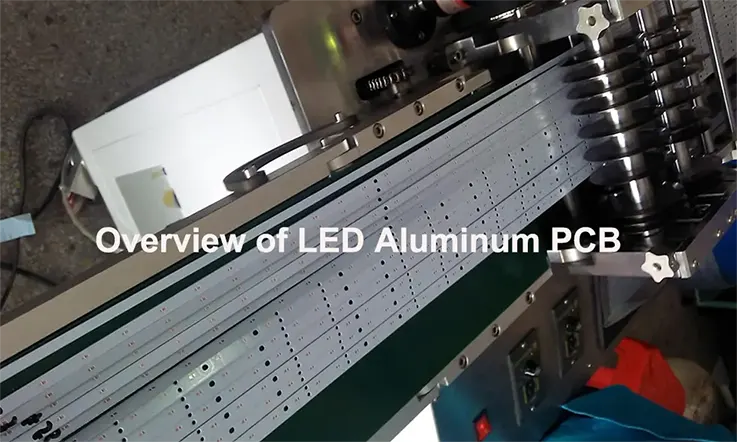
In recent years, LED aluminum PCB technology has taken a leap forward, revolutionizing the lighting industry with energy-efficient and high-performance solutions. Often referred to as metal core PCBs, these boards provide exceptional thermal conductivity, durability, and reliability, making them the go-to choice for LED lighting applications. As the thirst for energy-efficient lighting grows, manufacturers are ramping up their efforts to develop innovative LED aluminum PCBs that stretch the limits of both performance and design.
One trend we’re seeing is the integration of smart technologies into these PCBs, allowing for dynamic lighting solutions that adjust based on real-time data. For instance, imagine streetlights that dim during low traffic hours, saving energy while still keeping our streets safe and well-lit. This kind of adaptability is reshaping how we think about lighting.
Additionally, advancements in materials are paving the way for even better thermal management, which is essential for maintaining LED efficiency. New composite materials that enhance thermal performance are being explored, allowing for sleeker designs without sacrificing functionality.
Here’s a quick look at some key advancements in LED aluminum PCB technology:
Trend | Description |
Smart Technology Integration | PCBs that can adapt lighting based on environmental conditions. |
Advanced Materials | New materials that improve thermal management and durability. |
Customization Options | Tailored designs that meet specific customer needs for various applications. |
By staying on top of these trends, businesses can ensure they’re using the best technology available to meet the demands of today’s market. Want to dive deeper into how these advancements can elevate your lighting solutions? Let’s chat!
Introduction to LED Aluminum PCBs
Definition and Purpose of LED Aluminum PCBs
LED aluminum PCBs have found their sweet spot in the electronics realm, acting as a solid foundation for high-performance lighting solutions. These boards take full advantage of aluminum’s top-notch thermal conductivity to efficiently whisk away the heat generated by LEDs. This capability is key for keeping LEDs running smoothly and extending their lifespan. Unlike your standard PCB materials, aluminum substrates are built to handle the heat that high-power LEDs throw off, making them a must-have for applications where top-notch performance is the name of the game.
Significance of Thermal Management in LED Applications
When it comes to LEDs, heat can be a real party crasher. High temperatures can cause light output to drop and shorten LED life, which can seriously impact overall system reliability. That’s where aluminum PCBs come in, like a trusty sidekick, excelling in thermal management by making sure heat is efficiently moved away from sensitive components. This slick heat dissipation means brighter, longer-lasting LEDs, making aluminum PCBs the go-to choice for designers and manufacturers alike.
Benefits of Aluminum PCBs vs. Traditional PCBs
Feature | LED Aluminum PCB | Traditional PCB |
Thermal Conductivity | Excellent | Moderate |
Lifespan of LEDs | Longer due to better heat dissipation | Shorter under high heat |
Weight | Lightweight yet strong | Heavier and less robust |
Application Flexibility | High (rigid and flexible options) | Limited |
Want to amp up your LED performance? Reach out to us to dig deeper into the benefits of aluminum PCBs!
Types of LED Aluminum PCBs
Rigid Aluminum PCBs for High-Power LED Applications
Rigid aluminum PCBs are the real MVPs of the industry. Designed to withstand the demands of high-power applications, these boards provide unmatched strength and stability. Their sturdy design not only supports heavy components but also keeps everything intact under thermal stress. For example, in automotive lighting systems—where reliability is a big deal—rigid aluminum PCBs deliver performance you can trust. You can count on them to shine bright even when the going gets tough.
Applications of Rigid Aluminum PCBs
Application Area | Benefits |
Automotive Lighting | High reliability under stress |
Industrial Lighting | Excellent thermal management |
High-Power LED Fixtures | Supports heavy components effectively |
Flexible Aluminum PCBs for Innovative LED Designs
On the flip side, flexible aluminum PCBs bring a burst of creativity to the mix. Their ability to bend and adapt lets designers explore unconventional layouts, making them perfect for LED strip lights and intricate designs. A prime example is the use of flexible PCBs in modern home lighting, where they allow for artistic installations that illuminate spaces in fresh and exciting ways. Whether it’s wrapping around corners or fitting into tight spaces, these boards are the go-to for those who want to push the envelope.
Applications of Flexible Aluminum PCBs
Application Area | Benefits |
LED Strip Lights | Adaptable to various shapes |
Decorative Lighting | Enhances artistic design |
Smart Home Devices | Integrates seamlessly into products |
Looking to get creative with your designs? Hit us up to learn how flexible aluminum PCBs can elevate your projects!
Key Features of LED Aluminum PCBs
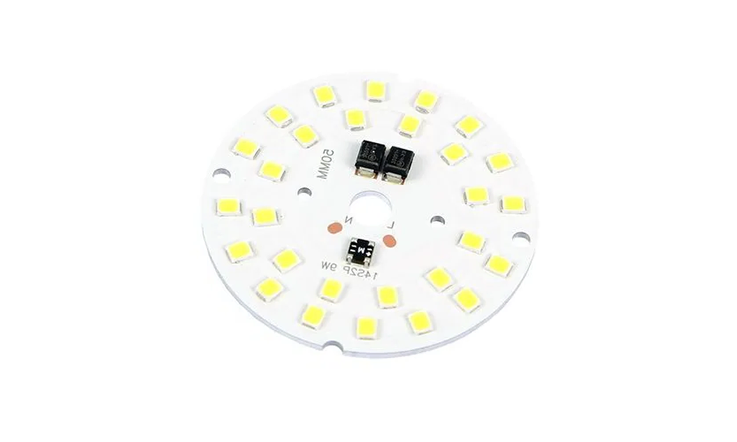
High Thermal Conductivity for Improved LED Performance
One of the standout features of LED aluminum PCBs is their top-notch thermal conductivity. This property ensures that heat generated by LEDs is efficiently whisked away from the light source, leading to enhanced performance and a longer lifespan. High thermal conductivity means less heat buildup, keeping LEDs running cool and bright—a total win-win for any application. For instance, products like high-output stage lighting rely on this capability to deliver vibrant performances that light up the stage.
Impact of Thermal Conductivity on LED Performance
Feature | Benefit |
Heat Dissipation | Keeps LEDs cool |
Enhanced Lifespan | Reduces degradation over time |
Performance Consistency | Maintains brightness |
Design Flexibility in Custom Aluminum PCB Solutions
Customization is the name of the game in today’s competitive market. LED aluminum PCBs offer unmatched design flexibility, allowing manufacturers to tailor boards to meet specific needs. From unique shapes to specialized thermal properties, the ability to customize aluminum PCBs means designers can bring their visions to life without missing a beat. For example, a recent client managed to reduce the overall product weight through a customized PCB design, enhancing portability without sacrificing performance.
Benefits of Customization
Custom Feature | Benefit |
Unique Shapes | Fits specific design requirements |
Tailored Thermal Properties | Optimizes heat management |
Lightweight Materials | Enhances portability |
Got a unique design in mind? Let’s team up and turn your ideas into reality!
Thermal Conductivity of LED Aluminum PCBs
When it comes to LED aluminum PCBs, thermal conductivity is a key player in ensuring optimal performance. Typically, the thermal conductivity of aluminum PCBs falls within the range of 1 to 9 W/m·K, depending on the specific alloy and thickness used. This range allows for effective heat dissipation, which is vital for maintaining the efficiency and longevity of LEDs.
Why Thermal Conductivity Matters High thermal conductivity helps mitigate heat buildup, which can adversely affect LED output and lifespan. For example, when using aluminum PCBs in high-power applications like automotive lighting or streetlights, efficient heat management translates to brighter lights and longer service intervals. Think of it this way: just like a car engine needs a cooling system to run smoothly, LEDs require a solid thermal management strategy to deliver peak performance.
Thermal Conductivity Comparison
Material | Thermal Conductivity (W/m·K) |
Aluminum | 1 – 9 |
Copper | 390-410 |
FR-4 (Standard PCB) | 0.3 – 0.5 |
In this table, you can see the stark difference between aluminum and copper, highlighting aluminum’s effectiveness for LED applications where weight and form factor are also considerations. Copper may have higher thermal conductivity, but its weight and cost can be limiting factors in many designs.
By focusing on the right materials and understanding their thermal properties, manufacturers can significantly enhance LED performance while keeping designs sleek and lightweight. If you’re diving into PCB design, remember that selecting the right substrate isn’t just a technical choice—it’s a game plan for success!
Got questions about how thermal management can level up your LED projects? Let’s connect and explore the possibilities!
Base Materials for LED Aluminum PCBs
Aluminum Substrate Properties: Why Aluminum?
Aluminum has emerged as the go-to substrate for LED PCBs, and it’s easy to see why. Lightweight yet tough, aluminum makes for a breeze when it comes to handling and installation, all while delivering stellar thermal management. This material’s availability and cost-effectiveness are the cherries on top, making aluminum a smart pick for manufacturers aiming to deliver quality products without emptying their wallets. Think of it as the solid foundation that keeps everything running smoothly while keeping your budget in check.
Benefits of Aluminum as a PCB Substrate
Property | Benefit |
Lightweight | Easy handling and installation |
Excellent Thermal Conductivity | Keeps LEDs cool |
Cost-Effective | Budget-friendly option |
Insulating Layer Materials in LED Aluminum PCB Design
The insulating layer plays a key role in aluminum PCB construction. This layer doesn’t just provide electrical insulation; it also helps with thermal management. Materials like epoxy resin and other composites are the usual suspects, enhancing the performance of aluminum PCBs. Grasping the role of these insulating materials can help manufacturers and designers fine-tune their products for optimal results.
Common Insulating Materials and Their Benefits
Material | Benefit |
Epoxy Resin | Strong insulation and heat resistance |
Polyimide | High-temperature stability |
FR-4 (Flame Retardant) | Excellent electrical properties |
Ready to dive into the world of aluminum PCBs? Let’s chat and explore how these materials can elevate your designs!
Applications of LED Aluminum PCBs
High-Power LED Applications and Their Benefits
LED aluminum PCBs really shine in high-power applications, where thermal management is the name of the game. Industries like automotive, outdoor signage, and industrial lighting rely heavily on these boards for their reliability and performance. The ability to efficiently dissipate heat leads to brighter, more efficient lighting solutions that stand the test of time. For instance, the integration of aluminum PCBs in streetlights has transformed urban lighting, significantly cutting energy costs while enhancing visibility—now that’s a solid advantage!
High-Power LED Applications
Industry | Benefits |
Automotive | Enhanced reliability in lighting systems |
Outdoor Signage | Improved visibility with lower energy costs |
Industrial Lighting | Consistent performance under stress |
LED Strip PCB Solutions: Enhancing Flexibility and Performance
LED strip lights have taken the lighting market by storm, and flexible aluminum PCBs are at the heart of their success. These boards can be crafted to fit into virtually any configuration, making them perfect for creative lighting solutions. With their superior thermal properties, flexible aluminum PCBs ensure that LED strips stay vibrant and functional, even in tough environments. Designers have noted that using flexible PCBs has opened up fresh possibilities for artistic light installations, pushing the boundaries of what traditional lighting can do.
Benefits of Flexible LED Strip PCBs
Feature | Benefit |
Design Versatility | Fits into any configuration |
Thermal Management | Keeps LEDs bright and functional |
Artistic Potential | Enables creative installations |
Thinking about enhancing your product line with LED strip solutions? Let’s connect and explore your options!
Purchasing Considerations for LED Aluminum PCBs
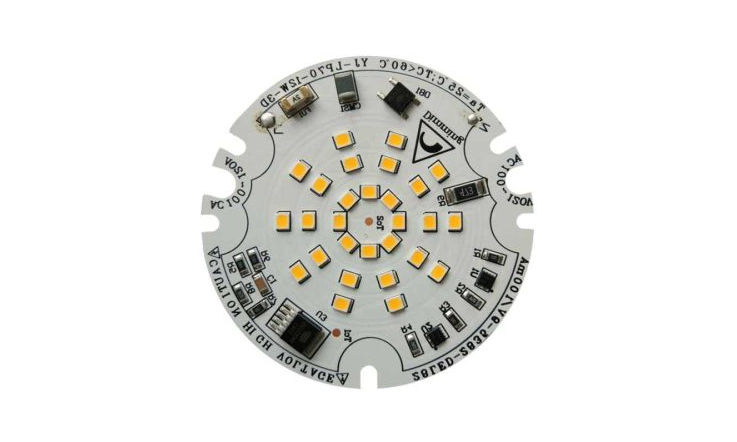
Factors to Evaluate When Sourcing Aluminum PCBs
When hunting for LED aluminum PCBs, buyers should keep several factors in mind to snag the best product for their needs. Quality, thermal performance, and customization options are all key elements to assess. Engaging with suppliers and asking pointed questions can help clarify the value on offer. Potential buyers might inquire: “What specific thermal management features does this PCB boast?” or “Can you share case studies showcasing the performance of your boards?”
Key Factors in Sourcing Aluminum PCBs
Factor | Description |
Quality | Assess manufacturing standards and certifications |
Thermal Performance | Look for features that enhance heat dissipation |
Customization Options | Determine flexibility in design and features |
Cost-Effectiveness and Value of Aluminum PCB Manufacturing
Cost often plays a significant role in procurement decisions, but aluminum PCBs deliver fantastic value. While initial costs may fluctuate, the long-term benefits—like durability and high performance—frequently overshadow the upfront investment. Grasping the cost structure and potential ROI is essential for making savvy decisions that fit within budget constraints.
Cost vs. Value in Aluminum PCBs
Aspect | Initial Cost | Long-Term Benefits |
Durability | Moderate | Reduced replacement costs |
Thermal Management | Variable | Enhanced performance over time |
Custom Features | Higher | Tailored solutions for specific needs |
Ready to make an informed purchasing decision? Let’s chat about how our solutions can align with your budget and performance needs!
Manufacturing Processes for LED Aluminum PCBs
Advanced PCB Fabrication Techniques
The manufacturing of aluminum PCBs utilizes cutting-edge fabrication techniques that ensure top-notch quality and efficiency. Processes like laser cutting, CNC machining, and advanced soldering are standard fare in creating high-performance boards. Grasping these techniques helps buyers appreciate the craftsmanship and tech behind their products. Manufacturers employing state-of-the-art methods often achieve tighter tolerances, boosting overall board performance—talk about precision!
Advanced Fabrication Techniques
Technique | Description | Benefits |
Laser Cutting | High-precision cutting using lasers | Reduced waste and enhanced accuracy |
CNC Machining | Computer-controlled machining | Consistent quality and complex designs |
Advanced Soldering | Innovative soldering techniques | Improved connections and durability |
Quality Control Practices in PCB Assembly
Quality control plays a pivotal role in PCB manufacturing. Rigorous testing procedures, from thermal assessments to electrical performance checks, ensure that every board meets industry standards. When selecting a supplier, asking about their quality assurance practices can provide peace of mind that you’re investing in a solid product. Buyers should consider inquiries about specific testing methodologies, such as thermal cycling tests or visual inspections, to gauge the thoroughness of the manufacturer’s quality processes.
Quality Control Practices
Testing Methodology | Purpose | Benefit |
Thermal Cycling Tests | Assess thermal durability | Ensures performance under temperature variations |
Visual Inspections | Check for physical defects | Catches issues before they become problems |
Electrical Performance Checks | Validate operational effectiveness | Guarantees functionality meets specifications |
Ready to get the ball rolling on your PCB project? Let’s chat about how our advanced manufacturing processes can meet your needs!
Customization and Cost-Effectiveness in LED Aluminum PCB Design
Tailored PCB Design for Specific Client Needs
Customization enables manufacturers to meet specific client requirements, adding real value to LED aluminum PCBs. Whether it’s tweaking the layout, enhancing thermal properties, or adjusting dimensions, tailored designs can significantly boost product performance and customer satisfaction. For example, a recent case involved a client needing a PCB for a bustling environment; customization helped them achieve the durability and performance they were after—talk about hitting the nail on the head!
Customization Options
Customization Aspect | Description | Impact on Performance |
Layout Adjustments | Modifying component arrangement | Enhances efficiency and space utilization |
Thermal Property Changes | Altering materials for better heat dissipation | Improves lifespan and brightness |
Dimension Adjustments | Adjusting size to fit specific applications | Ensures compatibility with existing systems |
Cost-Effective Manufacturing Strategies in PCB Production
Implementing cost-effective manufacturing strategies is essential for maintaining profitability. Techniques that optimize production without skimping on quality can lead to significant savings. Chatting with suppliers about these strategies can help you strike the right balance between cost and quality that meets your business needs. For instance, manufacturers using lean production techniques often find ways to reduce waste while maintaining high standards—saving bucks without cutting corners!
Cost-Effective Strategies
Strategy | Description | Benefits |
Lean Manufacturing | Reducing waste in production processes | Cost savings and improved efficiency |
Bulk Purchasing | Buying materials in larger quantities | Lower material costs |
Automated Production | Utilizing machinery for repetitive tasks | Increased speed and consistency |
Want to learn how customization can boost your PCB performance? Reach out today to explore tailored solutions that fit your needs!
Challenges in LED Aluminum PCB Design
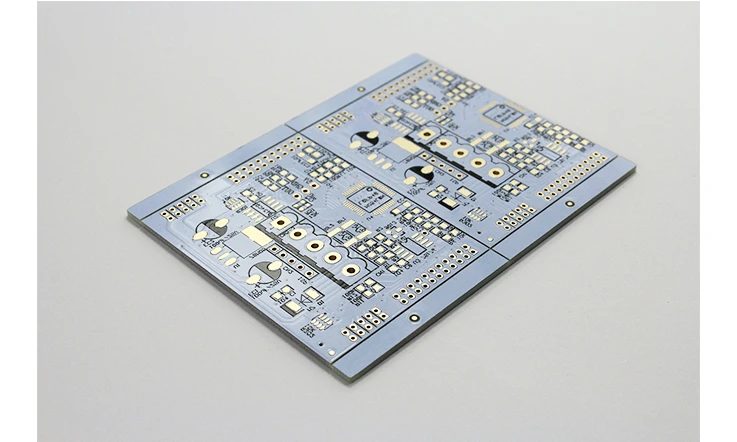
Addressing Thermal Management Challenges in PCB Design
While aluminum PCBs are designed for thermal management, challenges can pop up during the design phase. Factors like component placement and airflow must be carefully navigated to avoid heat issues. Teaming up with experienced engineers can help spot and tackle these challenges early on. For instance, strategic component placement can minimize hotspots, making your board run smoother and more efficiently—talk about hitting the sweet spot!
Thermal Management Considerations
Challenge | Solution | Benefits |
Component Placement | Optimize layout to enhance airflow | Reduces hotspots and improves efficiency |
Airflow Restrictions | Design for adequate ventilation | Keeps components cooler for better performance |
Thermal Interface Materials | Choose high-conductivity materials | Enhances heat dissipation |
Key Design Considerations for Optimal LED PCB Performance
To truly maximize performance, several design considerations come into play. From component layout to substrate thickness, every little detail counts in the effectiveness of the PCB. Partnering with design experts can help ensure that all aspects are finely tuned for the best results. A recent design workshop showed that small tweaks in the layout could lead to major gains in thermal performance—proof that sometimes it’s the little things that pack a punch!
Design Considerations
Design Factor | Impact on Performance | Recommendations |
Component Layout | Affects thermal efficiency | Space components for better airflow |
Substrate Thickness | Influences heat dissipation | Choose optimal thickness based on application |
Insulating Layer Material | Affects electrical insulation and thermal properties | Use high-quality materials for best results |
Facing challenges in your PCB design? Let’s troubleshoot together! Contact us for expert advice that’ll steer you in the right direction!
Wrapping Up
Future Trends in LED Aluminum PCB Technology and Applications
As the demand for LED technology continues to soar, innovations in aluminum PCBs are set to follow suit. Emerging trends in materials and manufacturing processes promise even more efficient solutions. For instance, the introduction of advanced materials that enhance thermal properties, alongside the integration of smart technologies into PCB designs, is paving the way for a new era in lighting applications.
One exciting trend is the development of eco-friendly aluminum substrates. These materials not only improve thermal management but also align with the growing demand for sustainable practices in electronics. Additionally, the rise of IoT (Internet of Things) is driving the creation of smart aluminum PCBs that can communicate data about performance and conditions in real-time.
Imagine a scenario where smart PCBs in streetlights adjust their brightness based on ambient light levels, optimizing energy consumption while enhancing visibility. This adaptability is the future of LED lighting, and aluminum PCBs are at the heart of this transformation.
Ready to stay ahead of the curve in LED technology? Let’s explore how these trends can benefit your projects!
LED Aluminum PCB FAQ
What advantages do aluminum PCBs have over traditional FR-4 boards?
Aluminum PCBs provide superior thermal management and durability, making them ideal for high-performance applications.
Can I customize my aluminum PCB?
Yes! Most manufacturers offer customization options tailored to your specific design needs.
How can I ensure the quality of my PCB supplier?
Ask about their manufacturing processes, quality control measures, and request references or samples to assess quality.
What industries primarily use LED aluminum PCBs?
Common industries include automotive, consumer electronics, and industrial lighting.
What are the lead times for custom LED aluminum PCBs?
Lead times vary by supplier, but it’s essential to communicate your timeline upfront for the best results.
Related Posts:
1. Differentiating FR4 Glass Fiber and Aluminum Substrate for PCBs
2.Leading Global 10 Aluminum PCB Manufacturers
3.Aluminum Base PCBs: The Future of High-Power Electronics
4.Significance of Aluminum Clad PCBs in Advancing Electronic Device
5.How Leveraging Aluminum PCB Substrates: in Your Next Stackup Design?