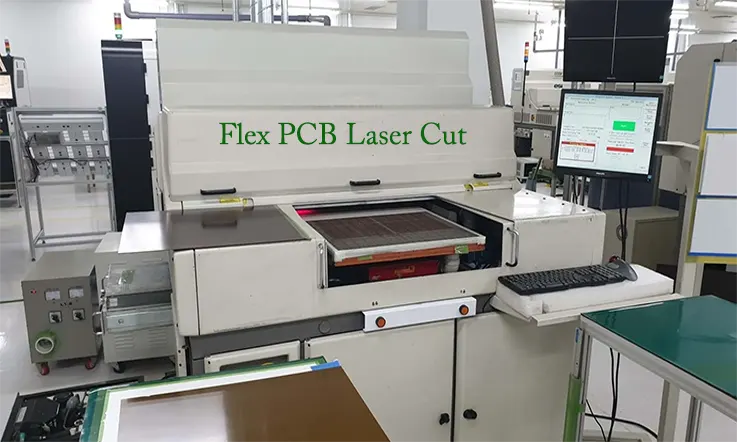
Flexible Printed Circuits (FPCs) have become an integral part of the modern world of electronics, enabling complex devices like wearables, medical devices, consumer electronics, and automotive systems. The manufacturing of these circuits demands precision, reliability, and scalability, which is where FPC laser cutting comes into play.
In this article, we’ll explore how FPC laser cutting is driving innovation in PCB manufacturing. From its evolution and core principles to its diverse applications across industries, we will delve into the various ways this cutting-edge technology is transforming the landscape of flexible PCB production.
The Evolution of FPC Laser Cutting in the PCB Industry
The landscape of flexible PCB (FPC) manufacturing has seen monumental shifts in recent years, and laser cutting technology is one of the primary forces behind these changes. Historically, the PCB industry relied on mechanical cutting methods, but the rise of FPC laser cutting has brought about a transformation, allowing human to achieve levels of precision, speed, and versatility that were previously unimaginable. This evolution continues to unfold, with each iteration pushing the boundaries of what’s possible in PCB production.
Today, the most advanced FPC laser cutting systems are used across industries from consumer electronics to aerospace, offering incredibly fine control over cutting paths and delivering ultra-clean edges. The introduction of this technology has reduced material waste, improved yields, and enhanced the ability to work with complex designs. So, let’s take a deeper dive into the evolution of laser cutting and explore how it has shaped the flexible PCB manufacturing process.
The Origins of FPC Laser Cutting Technology
While laser cutting may seem like a modern marvel, its roots trace back to the early days of laser technology. In the late 20th century, the first laser systems used for PCB depaneling represented a major leap forward for the industry. Back then, laser cutting was relatively slow and had limitations when it came to precision, especially on the thinner, more delicate materials that are common in flexible PCBs. Additionally, the machines struggled with cutting speed and were often not as reliable for high-volume production runs.
Though early FPC laser cutting technology faced challenges, its potential was evident from the start. Over the years, improvements in laser technology, optics, and automation boosted both cutting speed and accuracy. The ability to achieve micron-level precision allowed us to create complex designs with ease and efficiency. This progress set the stage for the advanced laser systems we use today, capable of producing flexible PCBs with exceptional accuracy and minimal material waste. These innovations have shaped how flexible circuits are manufactured, allowing for faster production and higher-quality outputs across industries.
Today’s high-precision FPC laser cutting systems are capable of handling a variety of materials, including polyimide, FR4, and even flexible hybrid electronics (FHE). This flexibility has expanded the possibilities for circuit board design, opening doors for new applications that were previously impossible to achieve with traditional cutting methods.
Comparing Traditional and Modern Laser Cutting Techniques
When comparing traditional cutting methods like mechanical punching or routing to modern FPC laser cutting, the differences are striking. Traditional methods often involve physical contact with the material, leading to stress, heat buildup, and potential damage to the delicate circuitry. Mechanical methods also face limitations in terms of speed, precision, and material compatibility. For instance, punching can distort the material, leading to unwanted burrs or fractures, which ultimately impact the performance of the final product.
On the other hand, laser cutting works by focusing a highly concentrated laser beam onto the material. This approach avoids direct contact with the PCB, which reduces stress on the material and eliminates the possibility of mechanical damage. In addition to reducing risk, FPC laser cutting is much faster and more precise, especially when cutting intricate designs or high-density interconnects (HDI). It allows for smoother cuts with less debris and lower thermal damage, which are essential when dealing with thin, flexible substrates.
This precision and flexibility have made laser cutting the preferred method in industries requiring detailed and complex PCB designs. For example, wearable tech and medical devices both rely heavily on laser cutting to create circuits that fit tight spaces while still maintaining high functionality. As FPC laser cutting continues to evolve, its impact is expanding beyond traditional applications into new frontiers like 3D circuit printing and rigid-flex boards, all thanks to the continuous advancements in laser technology.
Future Prospects: What’s Next for FPC Laser Cutting?
The future of FPC laser cutting seems limitless. Technological advancements in laser optics, AI, and automation are making it easier to achieve greater precision and higher throughput. For instance, the integration of artificial intelligence (AI) into laser cutting systems promises to enhance process optimization, allowing systems to “learn” from previous cuts and automatically adjust settings to achieve optimal results for different material types and designs.
Additionally, the development of more sophisticated laser wavelengths is enabling us to cut more challenging materials with greater efficiency. UV laser cutting, for example, offers a way to cut extremely fine lines in high-density circuits without introducing excessive heat, making it ideal for applications in flexible electronics and high-density interconnect (HDI) designs. As new laser technologies are introduced, FPC laser cutting will continue to improve in both speed and precision, opening up even more possibilities for flexible PCBs.
In the near future, we can expect more automated FPC laser cutting systems that require minimal human intervention, reducing the potential for errors and further streamlining the manufacturing process. These systems will be able to adjust in real-time to variations in material thickness and other factors, offering a level of adaptability and efficiency that traditional methods simply can’t match.
The Process of FPC Laser Cutting: From Design to Depaneling
Laser cutting in flexible PCB manufacturing is more than just a tool; it represents a significant shift in speed, accuracy, and versatility. From the initial design stages to final depaneling, each step in the FPC laser cutting process requires careful execution to ensure top-notch results. As manufacturing demands evolve, understanding the finer points of each phase can help refine workflows, improve product quality, and increase overall production efficiency.
In this section, we’ll take you through the detailed process of FPC laser cutting, focusing on everything from design optimization to selecting the right laser system for your application. We’ll also explore the technology behind laser depaneling, and how advances in automation are making this process faster, more accurate, and cost-effective than ever before.
FPC Laser Cutting Process Overview
The FPC laser cutting process is more than just about the laser—it’s a carefully planned, multi-phase operation that begins long before the first cut is made. A smooth and efficient laser cutting job depends on thoughtful planning and seamless execution from the start. From the initial design stage to the final depaneling step, each phase must work together to deliver the best results. Let’s walk through each stage of the process to see how they connect and contribute to the final product.
Step-by-Step Overview of the FPC Laser Cutting Workflow-
1.Design Optimization: It all starts with the design phase. This is where things get exciting. FPC designs must be optimized for laser cutting in order to reduce material waste and ensure precision. Software like CAD (Computer-Aided Design) allows engineers to fine-tune the layout, ensuring that the patterns are not only functional but also compatible with laser cutting techniques. This step also involves adjusting the design to account for things like kerf (the width of the cut) and the placement of vias and pads.
2.Preparation: Once the design is finalized, the next step is material preparation. Flexible PCBs can be made from a variety of substrates like polyimide, PET, and FR4, each requiring different laser settings. The material is then loaded onto the laser cutting machine, where it is carefully aligned and secured. This phase often involves setting up the laser parameters to ensure the correct cutting power, speed, and frequency for the material being used.
3.Laser Cutting: With everything in place, the laser cutting machine begins the task of cutting through the flexible PCB material. The laser beam precisely follows the design outline, ensuring clean, accurate cuts. This process can be adjusted to handle various thicknesses of material, offering incredible flexibility in the types of circuits that can be produced.
4.Depaneling: After the laser cutting is complete, the next phase is depaneling. This is where individual circuit boards are separated from the larger panel. With laser depaneling, the process is both fast and precise, as the laser beam creates minimal heat and leaves behind clean edges.
Importance of Design Optimization for Laser Cutting-
While FPC laser cutting systems are incredibly powerful, they still require design optimization to achieve the best possible results. A poor design can lead to material wastage, poor edge quality, and higher costs. For example, an inefficient trace layout or improperly placed vias might lead to unnecessary cuts, increasing the amount of scrap produced.
By using CAD software, we can simulate how the laser cutting machine will handle the circuit layout, allowing for adjustments in real-time. This can save us a lot of headaches in the long run by ensuring that the final cut is precise and minimal in terms of waste. A well-optimized design can significantly lower the total cost of production while improving the final product’s quality.
Types of Lasers Used in FPC Laser Cutting
The laser cutting process is not one-size-fits-all. Different types of lasers are employed depending on the material being cut, the desired precision, and the complexity of the design. Choosing the right laser system can make a world of difference in terms of quality, speed, and cost-efficiency.
CO2 Lasers vs UV Lasers: Understanding the Differences for FPC Applications-
Two of the most commonly used laser types in FPC laser cutting are CO2 lasers and UV lasers. Each of these has its strengths and weaknesses, depending on the application.
1.CO2 Lasers: These are the workhorse of many FPC laser cutting systems. They are generally used for cutting thicker materials like FR4 or multi-layer rigid-flex PCBs. CO2 lasers operate at a longer wavelength (10.6 microns), which allows them to easily cut through a variety of materials. They are also more cost-effective compared to UV lasers, making them the go-to option for many manufacturers.
2.UV Lasers: On the other hand, UV lasers have a shorter wavelength (around 355 nm), which allows them to achieve finer cuts with minimal heat input. This makes them ideal for cutting delicate flexible PCB materials like polyimide and PET, which require minimal thermal distortion. The precision of UV lasers enables us to produce high-density interconnect designs with high accuracy, a major advantage in industries like medical devices and wearables.
Laser Type | Wavelength | Best For | Material Compatibility | Cutting Precision | Application Example |
CO2 Laser | 10.6 microns | Cutting thicker materials (e.g., FR4) | Polyimide, PET, FR4 | 50-100 microns | Used in rigid-flex PCBs, HDI boards. |
UV Laser | 355 nm | Cutting thin, delicate materials (e.g., polyimide) | Polyimide, PET | 20-30 microns | Ideal for flexible circuits with fine lines. |
Choosing the Right Laser for Your FPC Cutting Needs-
Choosing between CO2 and UV lasers depends on a variety of factors including material type, design complexity, and cost considerations. For example, if you’re working with flexible circuits that have intricate designs with tight tolerances, UV laser cutting may be your best option. However, if you’re cutting a thicker FR4 or rigid-flex board, CO2 laser cutting could be a more economical choice.
Pulse vs Continuous Wave Laser Cutting Technology for Flex Circuits-
Another important distinction when choosing a laser system is between pulse and continuous wave (CW) lasers. Pulse lasers emit energy in short, high-intensity bursts, making them best for cutting very fine details on flexible PCBs. This type of laser is often used for applications requiring extreme precision, such as cutting through thin polyimide or creating fine vias in high-density boards.
In contrast, continuous wave lasers emit a constant stream of energy, making them better suited for cutting thicker materials or for operations that require a continuous, steady cut. CW lasers are commonly used in high-volume production where speed is a priority, such as in HDI boards or rigid-flex circuits.
Laser Mode | Type of Laser | Best Used For | Cutting Speed | Power Setting | Precision Level |
Pulse Laser | Pulsed | High-precision cutting of fine traces and detailed patterns | Low to Medium | Adjustable | High (Micron Level) |
Continuous Wave Laser | Continuous | Cutting thicker substrates like FR4 or multi-layered PCBs | High | Fixed | Moderate to High |
●Pulse lasers are good for high-precision applications, like cutting fine traces or intricate patterns in flexible PCBs.
●Continuous wave lasers are better suited for rigid-flex applications where higher cutting speeds and thicker materials are involved.
Advanced Laser Systems for Precision Depaneling
As the demands for smaller, more intricate electronics increase, laser cutting systems have evolved to meet these needs. Advanced laser depaneling systems, equipped with state-of-the-art features and automated controls, are now a common sight in PCB manufacturing facilities.
Automated Laser Cutting Systems and Their Impact on Efficiency-
The advent of automated laser cutting systems has greatly improved the efficiency and consistency of FPC Laser Cutting. These systems have the ability to adjust settings in real-time based on feedback from the material being cut, ensuring consistent quality and reducing human error.
Feature | Benefit | Application Example |
Automated Laser Systems | Speed up production and reduce setup times. | In mass production of flexible PCBs for consumer electronics. |
Laser Parameter Adjustment | Adjust laser settings on-the-fly for material changes. | Used in wearable electronics production where material thickness can vary. |
These automated laser systems allow us to streamline their operations and achieve consistent cuts even when dealing with complex and high-volume orders. The ability to automatically adjust laser settings depending on the material properties ensures that laser cutting parameters are always optimized for the specific material being used.
The Role of Laser Depaneling in Reducing PCB Waste-
Laser depaneling is a core step in the FPC production process, offering precision cuts with minimal material waste. Unlike traditional mechanical methods that often apply force and can cause stress or cracks in the material, laser depaneling works without physical contact. This non-invasive approach ensures that flexible circuits are cut cleanly and accurately, preserving their integrity while delivering consistent, high-quality results. It’s the go-to solution when precision and material preservation are top of mind.
Depaneling Method | Waste Reduction (%) | Advantages | Application Focus |
Laser Depaneling | 10%-20% better than mechanical methods. | High precision, minimal scrap, no material stress. | High-end flex PCBs for medical devices and automotive applications. |
Mechanical Depaneling | Higher material waste compared to laser. | Less expensive upfront costs. | Typically used for thicker substrates like rigid PCBs. |
Laser depaneling is a cost-effective and eco-friendly option for manufacturers looking to minimize waste. This process ensures precise cuts, reducing scrap material and improving overall yield. In industries like medical devices and consumer electronics, where high production rates are essential, it enhances efficiency. By lowering material waste, laser depaneling helps control costs while maintaining product quality, making every unit count.
Optimizing Laser Parameters for High-Quality FPC Cutting-
To get the best results in FPC laser cutting, it’s essential to adjust the laser settings according to the specific material, thickness, and design. Fine-tuning parameters like laser power, speed, and focus ensures optimal cutting performance. By tailoring these factors, we can avoid common issues such as excess heat, material deformation, or rough edges. With the right adjustments, you’ll be able to achieve sharp, clean cuts and maintain high production rates without sacrificing quality.
Parameter | Optimal Setting for Polyimide | Optimal Setting for FR4 | Impact of Incorrect Settings |
Laser Power | 25W-30W | 50W-60W | Low power leads to incomplete cuts; too high causes thermal damage. |
Cutting Speed | 10-12 mm/s | 20-25 mm/s | Slow cutting reduces throughput; too fast causes poor quality. |
Pulse Frequency | 30 kHz | 15 kHz | Higher frequencies yield finer detail but lower power. |
Advantages of FPC Laser Cutting: Why It’s Preferred in PCB Manufacturing
In today’s competitive manufacturing landscape, FPC Laser Cutting has become a preferred method for producing flexible PCBs due to its exceptional precision, efficiency, and the ability to manage delicate materials. Let’s delve deeper into the advantages that make FPC Laser Cutting an indispensable tool for modern PCB manufacturing.
Achieving High Precision with FPC Laser Cutting
Tight Tolerances and Fine Geometries in Flexible Circuit Boards-
When it comes to flexible PCBs, precision is of the utmost importance. Laser cutting delivers micron-level accuracy, ensuring that even the most intricate patterns are cut without any distortion. Unlike traditional methods like mechanical cutting, which can deform or leave jagged edges, laser cutting offers clean, precise cuts with minimal deviation from the original design specifications.
How FPC Laser Cutting Supports High-Precision Manufacturing for Wearables-
Laser cutting offers high precision, especially in wearable devices, where every trace and interconnection must be aligned for proper functionality and durability. The high precision of laser cutting results in minimal trace loss and a smooth surface finish, which is essential for flexible PCBs used in these applications.
Reducing Circuit Defects and Enhancing Reliability-
By minimizing mechanical stress and thermal distortion, laser cutting significantly reduces the risk of defects such as delamination and cracking, which are common in flexible PCBs when using traditional mechanical methods. This results in more reliable and durable circuits.
Feature | Laser Cutting | Mechanical Cutting |
Precision Level | High (Micron-Level) | Moderate (Limited by Tool Wear) |
Risk of Delamination and Cracking | Low (No Mechanical Stress) | High (Mechanical Forces Applied) |
Edge Quality | Smooth, Clean Cuts | Rougher Edges, Possible Burrs |
Speed and Efficiency in FPC Laser Cutting
Faster Prototyping with Laser Cutting Technology-
Laser cutting reduces the time it takes to go from design to prototype. This process enables us to produce high-precision flexible PCBs more quickly, which in turn allows for faster adjustments to design changes and quicker prototype refinements, all without unnecessary delays.
Cutting Costs and Reducing Manufacturing Time for Flexible PCBs-
Laser cutting provides faster production speeds compared to traditional mechanical methods, which often involve slower tooling and more complex setup processes. The efficiency of laser cutting reduces overall manufacturing costs and streamlines the production of flexible PCBs, resulting in lower cost per unit and faster time to market.
The Role of Laser Cutting in Accelerating Time-to-Market for New Products-
Laser cutting speeds up manufacturing times and shortens prototyping stages, helping us get their products to market faster. This is especially helpful in industries like consumer electronics, where the race against time to launch new products is a common challenge. By streamlining the process, laser cutting lets us react quicker to design changes, cutting out delays and keeping the momentum going. This helps to shave time off the overall development process, keeping things moving smoothly and giving companies a competitive edge when it comes to meeting tight deadlines.
Metric | Laser Cutting | Mechanical Cutting |
Setup Time | Short (Fewer Adjustments Needed) | Long (Tool Changes & Adjustments) |
Production Speed | High (Faster Material Processing) | Moderate (Longer Setup Times) |
Time-to-Market | Reduced (Quicker Prototype Testing) | Increased (Slower Setup & Testing) |
Minimizing Thermal Damage and Mechanical Stress with FPC Laser Cutting
How Laser Cutting Minimizes Heat-Affected Zones in FPC Manufacturing-
A major advantage of laser cutting over traditional methods is its minimal heat-affected zone (HAZ). Mechanical cutting methods, which generate significant heat during the process, can cause thermal damage to flexible PCBs, leading to issues such as warping or delamination. In contrast, laser cutting uses focused light to cut the material with minimal heat generation, reducing these risks.
Stress-Free Depaneling: Preventing Cracking and Delamination in Flexible PCBs-
Laser cutting also reduces the mechanical stress typically associated with depaneling flexible circuits. Mechanical cutting tools often rely on force to separate the PCB from the panel, which can cause cracks or delamination in the PCB, especially for delicate materials. Laser cutting, being a non-contact process, ensures that no additional mechanical stress is applied to the material, preventing damage during the depaneling process.
The Advantages of Laser Cutting Over Mechanical Methods for Stress-Free Manufacturing-
Compared to traditional mechanical methods, laser cutting offers a stress-free approach to PCB manufacturing. The precise, non-contact nature of laser cutting allows flexible PCBs to be handled with minimal risk of damage or defects, making it the nice choice for high-quality, reliable production.
Factor | Laser Cutting | Mechanical Cutting |
Heat-Affected Zone (HAZ) | Minimal (Focused Energy) | High (Widespread Heat Impact) |
Risk of Cracking and Delamination | Low (Non-Contact Process) | High (Force Applied) |
Stress on Material | No Stress (Precision Cutting) | High Stress (Force During Cutting) |
Key Factors for Successful FPC Laser Cutting
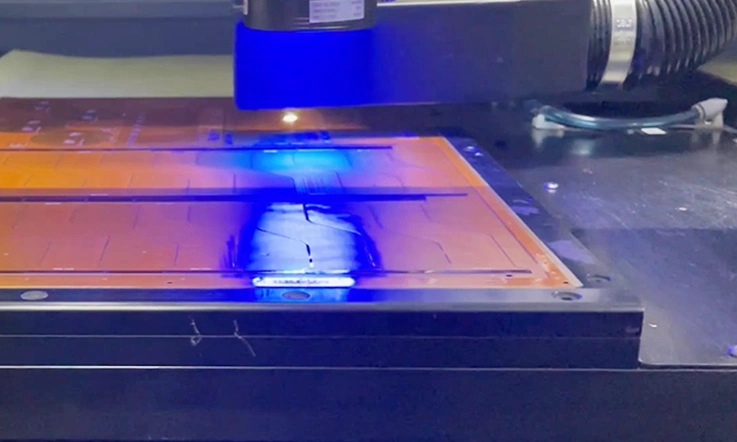
To achieve the best results in FPC Laser Cutting, a few core factors must be considered. Successful production of flexible PCBs goes beyond material choice; it also requires the correct laser settings and addressing the unique challenges that flex circuits present. By examining these elements—from material selection to optimizing laser settings and managing common challenges—we can ensure the best outcome in the laser cutting process, leading to efficient production and top-quality results.
Material Compatibility for Optimal FPC Laser Cutting
The Importance of Choosing the Right Material for Laser Cutting (Polyimide, PET)-
When it comes to FPC Laser Cutting, choosing the right material makes all the difference. The material used directly influences the efficiency and success of the laser cutting process. Polyimide, for instance, is a go-to material for flexible PCBs due to its excellent heat resistance and flexibility, making it ideal for electronics that have to endure high temperatures. PET (Polyethylene Terephthalate), on the other hand, is more popular for its ease of processing and lower cost, although it doesn’t quite measure up to Polyimide in terms of thermal performance. So, whether you’re looking for toughness in extreme conditions or a more cost-effective solution, your material choice will steer the whole cutting process.
Choosing the right material ensures that the laser can make precise cuts without causing excessive thermal damage or warping. Improper material selection can lead to poor-quality cuts, excess heat generation, or even laser system malfunctions. For instance, Polyimide requires careful power control to avoid excessive heating, while PET demands the right cutting speed to maintain the integrity of the PCB.
How Material Properties Influence the Quality of Laser Cuts in FPCs-
Material properties such as thickness, density, and thermal conductivity significantly influence the quality of the cuts in flexible PCBs. For example, thicker materials may require more powerful lasers, while denser materials may demand slower cutting speeds to avoid issues like melting or material distortion. Additionally, thermally conductive materials like Polyimide require extra attention to prevent the laser from overheating the material during the cutting process.
Material | Key Characteristics | Laser Cutting Considerations |
Polyimide | High thermal stability, flexible | Low power, slower speed to prevent overheating |
PET | Cost-effective, easy to process | Higher speed, moderate power for clean cuts |
FR4 | Rigid, flame-resistant | Higher power, slower speed for clean edges |
Laser Cutting Different Materials: Challenges and Solutions-
Different materials present unique challenges. For instance, Polyimide and PET both require specific adjustments in cutting settings. Polyimide’s high thermal stability can sometimes lead to excessive heat buildup around the cutting area, which can cause the material to warp if not handled properly. Conversely, PET, while easier to process, may produce smoke and debris that can impact the precision of the cut. The solution? Carefully balancing laser power, speed, and focus to match the material’s properties.
Optimizing Laser Cutting Parameters for Flex Circuits
Fine-Tuning Laser Power, Speed, and Focus for Best Results-
To achieve the best results in FPC Laser Cutting, adjusting the laser power, speed, and focus is where the magic happens. Getting the right balance between these factors ensures clean, precise cuts without damaging the material with unnecessary heat. This attention to detail guarantees smooth, effective cuts, saving time and material. Fine-tuning these parameters can help avoid issues down the road and ensure that the finished product meets expectations without any unnecessary setbacks.
●Laser Power: Too much power can cause excessive heat, resulting in material distortion. Too little power, and the laser won’t cut through the material properly. Typically, laser power for flexible PCBs ranges from 5 to 50 watts, depending on the material’s thickness.
●Cutting Speed: Speed plays a direct role in cut quality. If the cutting speed is too fast, the laser won’t have enough time to make a clean cut, leading to rough edges. On the other hand, cutting too slowly can overheat the material, creating unnecessary thermal damage.
●Focus: The laser focus is essential for achieving a fine cut. A focused laser delivers a narrower and more concentrated beam, ensuring clean, precise cuts with minimal heat impact. Focusing too wide can cause excess heat buildup and reduce the cut quality.
Parameter | Optimal Setting | Effect on Cut Quality |
Laser Power | 5-50 watts (depending on material) | Correct balance prevents overheating |
Cutting Speed | 10-20 mm/s (depending on material) | Fast speeds reduce cut quality, slow speeds can overheat |
Focus Depth | 0.1-0.2 mm (depending on material) | Precise focus for clean, sharp cuts |
How to Adjust Laser Settings for Different FPC Applications-
Laser settings must be tailored for different FPC applications, ranging from wearables to medical devices. Wearables often require smaller, more intricate cuts, demanding precise settings to avoid damaging delicate components. Conversely, medical device PCBs often feature thicker or more rigid materials that require increased laser power and slower cutting speeds.
Achieving the Right Balance Between Speed and Precision in FPC Laser Cutting-
Achieving the perfect balance between speed and precision is one of the biggest challenges in laser cutting flexible PCBs. Speeding up the process can reduce production time, but if done improperly, it can lead to poor-quality cuts and defective products. Precision, on the other hand, ensures that high-density circuits are perfectly formed. Finding the right balance is all about knowing the application and adjusting the settings accordingly. In production environments with tight deadlines, optimization of speed without compromising precision is often the need to meeting market demands.
Overcoming Challenges in FPC Laser Cutting Technology
Managing Complex Geometries and Fine Features in Flexible Circuits-
Flexible PCBs are often designed with complex geometries and fine features that require precision cutting. As technology evolves, the designs of flexible circuits become more intricate, with tighter tolerances and smaller components. Laser cutting must keep up with these demands without compromising accuracy.
To overcome these challenges, modern FPC Laser Cutting systems come equipped with advanced features like dynamic focus adjustment and AI-powered path optimization. These advancements allow the laser to adjust its cutting path in real-time, ensuring precision even in complex designs.
Addressing Heat-Affected Zones and Thermal Stress in Laser Cutting-
During the laser cutting process, heat-affected zones (HAZ) can cause issues like warping or delamination, impacting the quality of the flexible PCB. To tackle this problem, modern laser systems use pulse-modulated lasers, which help minimize the buildup of continuous heat and keep distortion in check. Additionally, managing the right cutting speed is a big deal, as going too fast or slow can lead to thermal stress that may cause lasting damage to the flexible material. By dialing in the perfect parameters, we can ensure clean, precise cuts and avoid unnecessary flaws that could throw off the final product.
Solving Common Problems in FPC Laser Cutting and Depaneling-
While laser cutting offers several advantages, it’s not without its challenges. Common issues like material warping, burrs, and smearing can occur if the laser settings are not properly tuned or if the material is incompatible with the laser. Fortunately, solutions like improved cooling systems, optimized laser paths, and advanced material pre-treatment can help overcome these problems. Regular maintenance and system calibration are also essential to ensure the laser system operates at peak efficiency.
Problem | Solution | Effect on Quality |
Material Warping | Adjust cutting speed, optimize focus depth | Prevents deformation and ensures clean edges |
Burr Formation | Use pulse lasers, adjust power settings | Reduces rough edges and improves cut quality |
Smearing | Use cleaner materials, reduce cutting speed | Minimizes residue and maintains precision |
FPC Laser Cutting for High-Density and Multi-Layer Circuits
In the world of modern electronics, high-density interconnections (HDI) and multi-layer circuits are increasingly common. Therefore, as designs grow more intricate and require tighter tolerances, FPC Laser Cutting becomes a go-to solution for creating these advanced circuits. This technology offers unmatched precision, flexibility, and efficiency, enabling us to meet the demands of complex, multi-layer designs that require both reliability and high performance.
The Role of FPC Laser Cutting in HDI and Multi-Layer Circuits
Understanding the Need for High-Density Interconnections (HDI) in Modern Electronics-
HDI technology is shaking up the electronics scene. It involves circuits that pack more wiring into less space, made possible by techniques like microvias, blind and buried vias. These designs are a must for making compact, lightweight devices that don’t cut corners on performance. When it comes to manufacturing these advanced HDI circuits, FPC Laser Cutting is the go-to option for crafting ultra-fine traces, vias, and microvias with pinpoint precision.
As the demand for miniaturization increases, HDI designs require precise cutting of materials that are both thin and flexible. These designs allow for better performance in applications like wearables, where space is at a premium, and medical devices, which require compact and reliable circuitry. FPC laser cutting supports these needs by offering non-contact cutting, which ensures that even the most intricate designs are produced with no risk of damaging sensitive components.
How FPC Laser Cutting Supports Multi-Layer Circuit Production-
Multi-layer PCBs require the alignment and precise cutting of multiple layers of material, often stacked on top of each other. Each layer must be cut separately to maintain alignment and integrity during the final assembly. FPC Laser Cutting ensures that the delicate process of cutting through these multiple layers happens without generating heat that could affect the material or cause misalignment.
With laser cutting, the layers are cut sequentially with micron-level precision, which guarantees that the layers stay intact and aligned. Laser systems are able to precisely follow complex paths in multi-layer designs, ensuring a smooth and reliable depaneling process. This also eliminates the need for mechanical stress, which is common with traditional cutting methods and could potentially damage the layers.
The Precision of Laser Cutting in Handling Fine Line and Microvia Structures-
The creation of fine lines and microvias is one of the most important features in HDI and multi-layer circuit design. These fine lines are often less than 0.1mm in width and require ultra-precise cutting techniques to avoid defects. FPC Laser Cutting can achieve this level of precision, making it better for cutting through the thin layers and delicate traces found in HDI circuits.
Whether it’s cutting microvias for signal transmission or creating fine trace patterns for high-speed signals, the precision offered by laser cutting systems ensures that the final product meets the high-performance standards demanded by the industry. The minimal heat-affected zone (HAZ) also ensures that sensitive structures like microvias and fine traces remain intact and functional.
Feature | Laser Cutting Advantage | Traditional Methods Limitation |
Trace Precision | Micron-level precision | Potential for trace distortion |
Material Integrity | Non-contact cutting prevents damage | Physical pressure may damage layers |
Heat-Affected Zone (HAZ) | Minimal HAZ for fine traces and vias | Higher risk of heat damage to circuits |
Cutting Speed | Faster cutting for complex designs | Slower, more prone to misalignment |
Laser Cutting for Complex Designs and Fine Patterns
Achieving Fine Details with Laser Technology for HDI Circuits-
When it comes to HDI and multi-layer circuits, the ability to create fine patterns and intricate designs is absolutely crucial. Laser cutting allows for clean, sharp edges that can be produced with tight tolerances, making it an indispensable tool for high-performance circuit boards. Whether dealing with fine pitch components, fine-line traces, or multiple vias, laser cutting ensures that each feature is accurately executed according to design specifications.
The laser’s precision makes it good for cutting fine geometries, including patterns used in HDI circuits and complex designs. It’s not just about precision; it’s also about versatility. Laser cutting can handle a variety of materials, from flexible substrates like polyimide to more rigid options like FR4—all while ensuring the design remains intact and functional.
How Laser Cutting Enables Complex, High-Performance Circuit Designs-
As electronics become more advanced, there’s an ever-growing demand for high-performance circuit designs that feature complex geometries and intricate interconnections. Traditional methods of depaneling and cutting simply can’t keep up with the fine geometries needed in today’s high-speed electronics.
Laser cutting, however, can manage complex shapes and intricate layouts without altering the properties of the material. From HDI designs featuring tiny vias to the fine traces needed for signal integrity, the laser’s precision ensures that each layer of the circuit performs optimally. Therefore, many Manufacturers now rely on lasers to meet the demands of industries where flexible circuits and multi-layer boards are no longer a luxury but a necessity.
The Impact of FPC Laser Cutting on High-Density Flexible PCB Designs-
In high-density flexible PCBs, where space is tight, laser cutting delivers a level of precision and flexibility that traditional methods can’t match. When dealing with multi-layer circuits, maintaining the integrity of each layer while cutting fine details is essential. Laser cutting handles this challenge smoothly by preventing damage to the delicate layers during the depaneling process, something that’s all too common with mechanical cutting. With laser cutting, you can count on a clean job without worrying about compromising the circuit’s performance.
Laser cutting is also faster, more efficient, and requires minimal human intervention, which makes it the perfect choice for automated production lines. So, when it comes to flexible PCBs, laser cutting makes it possible to meet design challenges head-on without compromising performance.
Advanced Laser Systems for Multi-Layer Depaneling
Integrating Laser Depaneling in Multi-Layer PCB Production Lines-
When it comes to separating multi-layer circuits, laser cutting really shows its value. It can slice through multiple layers without misaligning or damaging any of them. By integrating laser depaneling into the multi-layer PCB production process, we can efficiently and accurately separate circuits—especially when dealing with designs that include stacked vias or blind and buried vias. This precision ensures that the layers stay intact, making laser cutting the go-to solution for intricate designs where the integrity of every layer is a must.
Automated laser depaneling systems allow us to process multiple boards in a single operation, significantly improving throughput. These systems offer continuous monitoring and adjustment of laser parameters to ensure each board is cut with the utmost precision, even when dealing with complex multi-layer designs.
How Automated Laser Systems Enhance Multi-Layer PCB Manufacturing-
With automated laser systems, we can cut multi-layer flexible PCBs faster, more accurately, and with less waste. These systems use feedback loops to adjust parameters like laser power and cutting speed in real-time, allowing them to process boards more efficiently while maintaining the precision needed for high-density circuits.
In addition to improving speed, automation also reduces human error and ensures that each PCB is processed to the highest standards, making it good for high-volume production runs. These systems can also integrate easily with other stages of PCB manufacturing, such as pick-and-place for component assembly, further streamlining the production process.
Optimizing Laser Parameters for Layer-by-Layer Cutting of FPCs-
Cutting multi-layer flexible PCBs requires optimizing laser parameters for each individual layer. The laser’s power settings, speed, and focus must be adjusted to accommodate the specific material and layer thickness. With advanced laser systems, we can fine-tune settings to ensure that each layer is cut precisely without compromising the overall alignment of the circuit.
Adjusting the cutting depth for each layer is another factor to consider. If the cut goes too deep, the laser can cause damage to the underlying layers; too shallow, and the cut won’t be clean enough. Finding the right balance is all about getting that sweet spot, ensuring the cut is clean and precise while keeping the layers intact. When these settings are dialed in correctly, they help achieve the best results, ensuring the multi-layer PCB does what it’s supposed to do—perform like a pro.
Parameter | First Layer Setting | Intermediate Layer Setting | Final Layer Setting |
Laser Power | Moderate to High | Moderate | Low to Moderate |
Cutting Speed | Moderate | Faster | Slow to ensure clean cut |
Focus Depth | Shallow | Moderate | Deep for cutting through the material |
Why Choose Us for Your Flexible and Rigid-Flex PCB Projects?
When it comes to flexible and rigid-flex circuit boards, we stand as the go-to partner for businesses seeking precision, reliability, and innovation. Here’s why our company should be your choice:
1.State-of-the-Art Technology and Equipment We operate with the latest in laser cutting technology, ensuring that every FPC and rigid-flex PCB is produced with unmatched accuracy. Our high-precision equipment, including CO2 and UV lasers, ensures that every cut is clean, precise, and meets the stringent demands of modern electronics.
2.Advanced Manufacturing Techniques We combine cutting-edge production methods with years of experience in flexible PCB technology. Our automated laser systems not only optimize production time but also reduce waste and ensure that each circuit board is manufactured to the highest standards. From the initial design to the final depaneling process, we maintain tight quality controls at every stage of production.
3.Uncompromising Quality Our commitment to quality is evident in every product we deliver. We strictly adhere to industry standards and conduct rigorous testing to ensure that each flexible circuit board meets or exceeds performance expectations. Whether for consumer electronics, wearables, medical devices, or automotive applications, our products are designed to last and perform under demanding conditions.
4.Expert Engineering Team Our engineering team is one of the most knowledgeable in the field of flexible PCBs. With years of expertise in design, manufacturing, and troubleshooting, we are equipped to handle even the most complex projects. From providing design consultations to troubleshooting during production, our team is always ready to provide solutions and guidance at every step.
5.Comprehensive After-Sales Support We believe in building lasting relationships with our clients. Our dedicated customer service team is always available to offer technical support, ensure the smooth delivery of products, and assist with any post-production queries. Whether you need further engineering adjustments, product revisions, or guidance with assembly, we’ve got you covered.
Please Contact Us Toady:
By choosing us for your flexible and rigid-flex PCB needs, you’re not just getting a supplier—you’re partnering with a team that cares about your success. Trust us to bring your ideas to life with precision, efficiency, and quality.
FAQ & FPC Laer Cut
What types of materials can be processed with FPC laser cutting?
FPC laser cutting can handle various materials such as polyimide (PI), PET, polyester, and other flexible substrates commonly used in PCB production.
How does FPC laser cutting improve circuit board precision?
Laser cutting uses focused light beams to cut circuits with micron-level precision, ensuring that designs with fine lines and small features are accurately created without the mechanical stress seen in traditional methods.
What is the difference between CO2 and UV lasers in FPC laser cutting?
CO2 lasers are suitable for cutting a wider range of materials, while UV lasers are ideal for fine, detailed cuts on thinner substrates, offering higher precision and less heat generation.
How does FPC laser cutting minimize waste in PCB manufacturing?
Laser cutting systems are designed to make clean cuts with minimal heat-affected zones, reducing the chance of material waste and improving overall efficiency in production.
What is the maximum thickness that can be processed by FPC laser cutting?
The thickness of materials that can be processed varies depending on the laser type and power settings, but typically, FPC laser cutting handles substrates up to 0.5 mm thick efficiently.