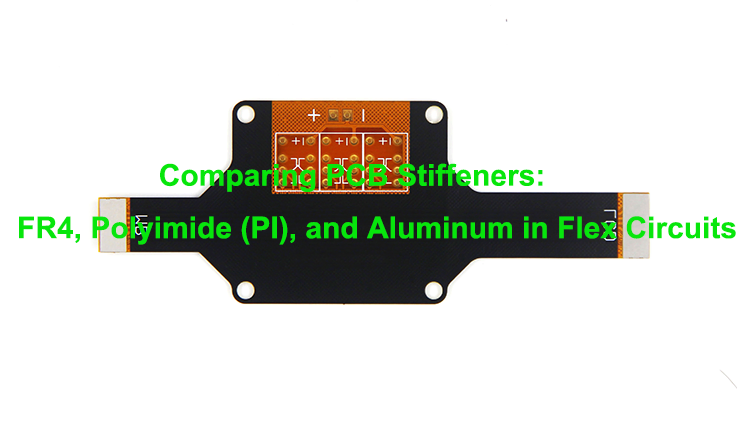
Flex circuits have become increasingly popular in various industries due to their flexibility and compactness. However, in certain applications, additional support and rigidity are necessary to ensure optimal performance and reliability. This is where stiffeners come into play. Stiffeners provide structural support and enhance the rigidity of flex circuits, allowing them to withstand harsh environments and demanding conditions. Among the most commonly used stiffener materials are FR4, Polyimide (PI), and Aluminum. In this article, we will compare these three materials, highlighting their strengths and applications in flex circuits.
What are PCB Stiffeners?
PCB (Printed Circuit Board) stiffeners are rigid materials or components that are used to provide additional support and strength to a PCB. They are typically attached to the PCB to prevent flexing or bending, especially in areas where the PCB may experience mechanical stress or vibration.
PCB stiffeners are commonly made of materials such as FR4 (a type of fiberglass-reinforced epoxy laminate), Polyimide (PI)aluminum, or stainless steel. They are usually in the form of strips, bars, or plates that are mounted along the edges or specific areas of the PCB. The stiffeners can be attached to the PCB through various methods, including adhesive bonding, mechanical fasteners, or soldering.
The primary purpose of using PCB stiffeners is to enhance the structural integrity of the PCB, especially in applications where the board may be subjected to harsh environments or heavy-duty use. They help to minimize the risk of PCB warping, bending, or breaking due to mechanical stress or vibration. PCB stiffeners also help to improve the overall reliability and lifespan of the PCB by reducing the risk of solder joint fatigue or component failure.
In addition to providing mechanical support, PCB stiffeners can also aid in the proper alignment and positioning of components on the PCB. They can help maintain the desired shape and form of the PCB during the manufacturing process, ensuring that the components are correctly mounted and the electrical connections are reliable.
Overall, PCB stiffeners play a crucial role in enhancing the robustness and durability of a PCB, making them ideal for applications that require high reliability and performance.
FR4 Stiffeners
FR4 glass epoxy is widely regarded as the most common and cost-effective option for PCB stiffening. It is particularly advantageous due to its compatibility with the FPC (Flexible Printed Circuit) substrate, as it shares the same laminate material.
Advantages:
There are several pros associated with using FR4 as a stiffening material. Firstly, it is an inexpensive option as it utilizes the same base laminate material as the FPC, eliminating the need for additional material costs. Additionally, FR4 bonds well with FPC adhesive and the lamination process, making assembly straightforward. Moreover, FR4 has a solderable surface finish, allowing for reliable solder pad plating. Furthermore, FR4 is readily available and has short lead times, ensuring easy accessibility for manufacturers. Lastly, FR4 provides adequate stiffness for most applications.
Disadvantages:
However, there are some cons to consider when using FR4 stiffeners. One limitation is the size constraint, as FR4 stiffeners are bound by standard panel sizes and fabricator tooling. Another consideration is that FR4 glass weave has a tendency to absorb humidity and solvents, which can impact its performance. Additionally, the glass fiber reinforcement in FR4 poses a risk of tearing copper off the pad. Lastly, the epoxy resin used in FR4 can be brittle and prone to cracking if subject to excessive loads.
Design Guidelines:
To ensure effective implementation of FR4 stiffeners, it is recommended to keep the unsupported stiffener length short to minimize bending. Using thicker cores, such as 1.6mm, can maximize stiffness. Care should also be taken to avoid any design for manufacturing (DFM) violations, such as minimum trace spacing and hole size requirements. It is advisable to seal exposed glass fibers with solder mask or an additional polyimide (PI) overlay to protect against potential issues.
Overall, FR4 stiffeners offer a quick and cost-effective solution for reinforcing flex circuits due to their material compatibility with the FPC substrate.
Polyimide (PI) Stiffeners
Polyimide films, such as Kapton, offer an enhanced performance option as flex circuit stiffening materials.
Advantages:
There are several advantages associated with using polyimide as a stiffening material. Firstly, polyimide films have high strength and can withstand repeated stress and bending, making them ideal for flexible applications. They also have low moisture absorption, providing resistance to humidity and liquid damage. Additionally, polyimide films have a high-temperature tolerance, withstanding temperatures over 260°C. Furthermore, polyimide is a lightweight material with low density, reducing mass in the application. Moreover, polyimide films are available in thin core options, ranging from 25um to 150um, providing flexibility in design. Lastly, polyimide exhibits excellent chemical resistance, remaining inert to most solvents and acids.
Disadvantages:
However, there are some considerations when using polyimide stiffeners. One drawback is the higher cost, as polyimide films are roughly 5-10 times more expensive than FR4. Additionally, some flex-grade polyimide films may have longer fabrication lead times, impacting project timelines. Another challenge is the adhesive bonding of polyimide to FPC layers, which can be difficult. Furthermore, polyimide films are non-solderable and require metallization for component pads, adding complexity to the assembly process.
Design Guidelines
To ensure effective use of polyimide stiffeners, it may be necessary to apply adhesion-promoting surface treatments. Care should also be taken to avoid handling damage to thin cores, as they are more susceptible to physical harm. Additionally, careful drill and routing parameters are required to prevent damage to the polyimide film. It is also advisable to minimize exposed polyimide edges to protect against potential issues.
All in all, polyimide stiffeners offer excellent strength at minimal thickness for flex circuits that require high performance. However, it is important to consider the higher cost and potential challenges associated with the material.
Aluminum Stiffeners
Metal backing plates or frames, such as those made of aluminum, offer the most rigid option for flex circuit stiffening.
Advantages:
There are several advantages to using aluminum as a stiffening material. Firstly, it provides maximum rigidity with a thin material, making it the strongest option for stiffening. Additionally, aluminum is a lower-cost alternative compared to polyimide films. It is also a lightweight material, especially when using aluminum alloys, which helps reduce overall weight in the application. Furthermore, aluminum can be machined or formed into various shapes, providing flexibility in design. Moreover, aluminum exhibits high thermal conductivity, making it suitable for heat sinking applications.
Disadvantages:
However, there are some considerations when using aluminum stiffeners. One drawback is the potential for thermal expansion mismatch, which can cause warping due to the difference in thermal expansion between the aluminum and other materials in the stackup. Additionally, assembly with aluminum stiffeners may require metallization or insulation to ensure proper integration. Aluminum is also prone to oxidation and corrosion without protective plating. Furthermore, flexible aluminum, particularly when heat treated, may experience springback and requires careful handling during assembly.
Design Guidelines
To ensure effective use of aluminum stiffeners, anodization can be applied to provide insulation and improve oxidation resistance. The selection of adhesives is critical to handle the thermal expansion differences between aluminum and other materials. It is important to allow clearance for flexing zones around stiffeners to accommodate the flexibility of the circuit. Minimizing rigid portions of the assembly can make dynamic flexion easier to achieve.
Therefore, aluminum or metal stiffeners offer the strongest option for flex circuits but require additional processing steps for proper integration into the stackup.
Comparing Performance of Stiffeners
Parameter | FR4 | Polyimide | Aluminum |
Rigidity | Medium | Low | High |
Thermal conductivity | Medium | Low | High |
CTE | Medium | Medium-Low | High |
Moisture absorption | High | Low | Medium |
Solderable | Yes | No | No |
Chemical resistance | Medium | High | High |
High temperature | Medium | High | High |
Lead time | Short | Medium | Medium |
Cost | Low | High | Medium |
The selection of the most suitable material for stiffeners in a given application depends on the specific mechanical, thermal, and chemical requirements, with polyimide and aluminum emerging as top performers. However, it is important to note that these options come at a significantly higher cost compared to basic FR4 stiffeners. Therefore, a careful evaluation of the aforementioned needs is crucial in determining the optimum choice of material.
Comparing Cost of Stiffeners
When it comes to selecting stiffener material, cost is a significant factor to consider. Let’s compare the relative costs of different options:
FR4 Stiffeners
FR4 is the most cost-effective choice as it does not require any additional material expenses. It can be processed using basic fabrication methods.
Polyimide Stiffeners
Polyimide, on the other hand, is 5-10 times more expensive than FR4. This is due to the additional cost of the film, as well as the metallization and bonding processes involved.
Aluminum Stiffeners
Aluminum comes at a 2-3 times higher cost than FR4, primarily due to the material itself being more expensive. In addition, extra processing steps are required to pattern and isolate the metal layers.
For larger boards and high-volume production, the enhanced performance offered by polyimide or aluminum stiffeners can justify the additional costs. However, for lower complexity flex assemblies, FR4 provides sufficient reinforcement at the most affordable price.
If only small localized areas of an assembly require reinforcement, basic FR4 backbone boards are suitable. It is crucial to align cost factors with the performance requirements of each unique design.
Overall, the choice of stiffener material should be made based on a careful evaluation of cost and performance considerations.
Guidelines for Selecting Stiffeners
Here is a summary of the considerations for choosing the optimal stiffener material:
When to Choose FR4:
FR4 is a suitable choice when cost is a primary concern, especially for high production volumes. It provides adequate rigidity with thicker FR4 cores and is suitable for applications with lower temperature or chemical resistance requirements. It is also suitable for assemblies that only require small localized stiffened regions.
When to Choose Polyimide:
Polyimide is preferred when thin, high-performance materials are needed. It offers extreme flexibility and can withstand dynamic bending cycles. It is also suitable for applications that require high temperature or chemical resistance, as well as low moisture absorption.
When to Choose Aluminum:
Aluminum is the material of choice when maximum rigidity and structural support are required. It is ideal for larger or longer stiffener sizes that necessitate metal reinforcement. Additionally, it is suitable for applications that require heatsinking for power components or a hermetic assembly with a metal enclosure.
Each flex circuit project should be evaluated independently to determine the ideal stiffener material. Factors such as cost, manufacturability, and performance should be carefully considered to strike the right balance.
In Conclusion
The selection of the optimal stiffener material for flex circuits depends on several factors, including cost, performance requirements, size and shape, component compatibility, manufacturing processes, and flexibility needs. FR4 is a cost-effective choice suitable for applications with lower temperature or chemical resistance requirements. Polyimide offers excellent flexibility and is ideal for applications requiring thin, high-performance materials and extreme bending cycles. Aluminum provides maximum rigidity and structural support and is preferred for larger or longer stiffeners and applications that require heatsinking or hermetic assembly. It is crucial to assess each project independently and strike the right balance between cost, manufacturability, and performance to ensure the best stiffener material is selected for the specific flex circuit application.