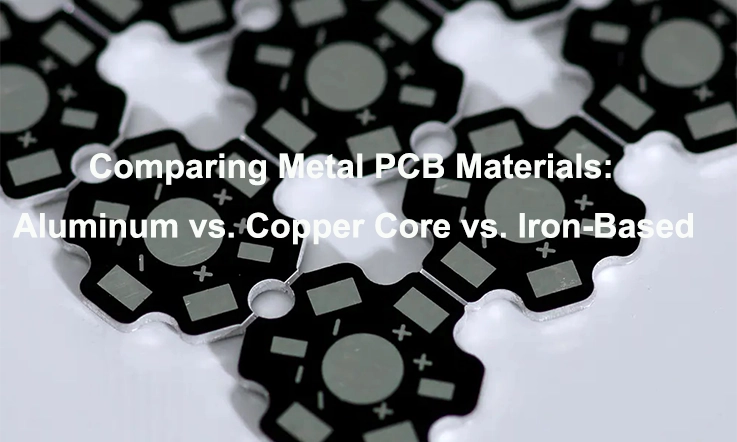
Metal core PCB technology plays a crucial role in effectively managing dissipated heat and enabling the integration of electronic components and systems with higher power densities. Different core material options, such as aluminum, copper, and iron alloys, are available to meet various design constraints and applications.
Aluminum MCPCBs offer the best value for most cost-driven commercial applications that require higher thermal conductivity than standard FR4 PCBs. They provide a cost-effective solution while still delivering improved thermal conductivity.
In cases where maximum heat transfer is critical to the functioning of the product, copper MCPCBs offer the highest performance despite their increased cost. These MCPCBs are the optimal choice when superior thermal dissipation is a priority.
For those seeking a middle ground alternative, iron alloys present a viable option. They provide a balance between performance and cost, making them suitable for applications that require intermediate thermal conductivity.
This article provides a detailed comparison between the different metal core materials used in PCBs covering properties, performance, applications, pros/cons and costs.
Aluminum Core MCPCB
Aluminum is widely regarded as the most prevalent metal base material in metal core PCBs due to its excellent combination of thermal performance, ease of fabrication, and cost-effectiveness.
Typical Properties
1. Heat Transfer Capability; Aluminum has a conductivity of around 130 W/mK which helps in effectively dissipating heat, from electronic parts.
2. Coefficient of Thermal Expansion (CTE): With a CTE of 23 ppm/°C, aluminum demonstrates good compatibility with the thermal expansion characteristics of electronic components, reducing the risk of mechanical stress or failure.
3. Density: Aluminums density of 2.7 g/cm3 allows, for the creation of PCBs, which’s highly beneficial when prioritizing weight reduction.
4. Specific Heat Capacity: With a specific heat capacity of 0.9 J/g°C, aluminum can effectively absorb and dissipate heat, contributing to enhanced thermal management.
5.Availability of Alloys: Aluminum alloys such as 6061, 5052, and 2024 are readily accessible in the market, providing designers with a range of options to meet specific requirements.
Aluminum MCPCBs Possess Key Attributes
Here are some reasons why Aluminum MCPCBs are great, for uses;
1. Good at Getting Rid of Heat: Aluminums ability to transfer heat well helps keep circuits working smoothly for a time.
2. Affordable Option: Using aluminum for making metal core PCBs is cost effective.
3. Lightweight: Aluminums light weight makes it ideal for situations where reducing weight’s important.
4. Compatible with PCB Tech: Aluminum MCPCBs work well with existing PCB manufacturing methods.
5. Easy to Customize: Aluminum can be. Punched easily allowing for customization of PCBs.
6. Friendly: Since aluminum can be recycled it fits in with eco practices.
Typically aluminum MCPCBs range in thickness, from 0.5mm to 6mm, with 1mm to 2mm being commonly used.
Aluminum MCPCBs Find Widespread Application in Various Industries
●Power Supplies
●Solar Inverters
●Automotive Electronics
●LED Lighting
●Power Converters
●Motor Drives
In conclusion aluminum MCPCBs provide a mix of efficiency, ease of manufacturing and cost efficiency, for electronic circuits with medium to high power requirements. The materials excellent heat dispersion properties, simple fabrication process and lightweight characteristics make it a popular option, for uses.
Copper Core MCPCB
Copper is a highly sought-after metal base material for metal core PCBs, particularly in demanding thermal applications, due to its significantly higher thermal conductivity compared to aluminum.
Notable Properties:
1. Thermal Conductivity: Copper has a conductivity of around 400 W/mK which helps in effectively dissipating heat, from electronic parts.
2. Coefficient of Thermal Expansion (CTE): Coppers Coefficient of Thermal Expansion (CTE) is 17 ppm/°C showing that it aligns well with the expansion properties of parts. This helps lower the chances of strain or breakdown.
3. Density: Copper has a density of 8.9 g/cm3, which provides robustness and stability to PCB constructions where added weight is not a concern.
4.Specific Heat Capacity: With a specific heat capacity of 0.39 J/g°C, copper possesses the ability to absorb and dissipate heat effectively, contributing to superior thermal management.
Benefits:
Copper MCPCBs offer numerous benefits for demanding thermal applications:
1. Extremely High Thermal Conductivity: Coppers impressive thermal conductivity surpasses that of aluminum ensuring heat transfer, for applications requiring thermal dissipation to maintain reliability.
2. Well-Established PCB Technology: Copper MCPCBs can be seamlessly integrated into established PCB manufacturing processes, facilitating efficient production.
3. Widely Available: Copper is readily accessible in the market, ensuring a consistent supply for manufacturing needs.
4. Compatibility with FR4 Processes: Copper MCPCBs can be fabricated using standard FR4 processes, simplifying the manufacturing approach and reducing costs.
5. Solderable and Recyclable: Copper is solderable, enabling easy assembly of components, and it is also recyclable, aligning with environmental sustainability practices.
Copper based metal core printed circuit boards (MCPCBs) typically range in thickness from 0.25mm to 4mm with the used thickness falling between 0.5mm and 2mm.
Applications:
Copper MCPCBs find significant application in various industries, including:
●RF Power Amplifiers
●Power Modules
●Solar Microinverters
●High Power LED Lighting
●High-Density Computer Systems
The exceptional thermal performance of copper MCPCBs justifies their higher cost in applications where thermal dissipation is crucial for ensuring reliability.
Therefore, copper MCPCBs provide a compelling solution for demanding thermal applications, thanks to their significantly higher thermal conductivity compared to aluminum. Their excellent heat dissipation capabilities, compatibility with established PCB technology, and widespread availability make them an ideal choice for high-power electronic circuits.
Iron Alloy Core MCPCB
Iron mixtures, which might include metals, like nickel, cobalt and aluminum provide a budget option compared to copper while also delivering heat conductivity than aluminum, in metal core PCBs. The characteristics of these mixtures can differ based on what they’re made of;
Specific Properties:
●Thermal Conductivity: Iron alloys have the ability to offer conductivity of around 65 W/mK, which exceeds the efficiency of aluminum.
●Coefficient of Thermal Expansion (CTE): These alloys typically exhibit CTE values ranging from 10 to 15 ppm/°C, ensuring good compatibility with the thermal expansion characteristics of electronic components.
●Density: The density of iron mixtures typically ranges 7 to 8g/cm3, per centimeter striking a balance, between durability and weight.
●Specific Heat Capacity: With specific heat capacities ranging from 0.44 to 0.46 J/g°C, these alloys possess the ability to absorb and dissipate heat effectively.
Benefits:
Using iron alloys, in metal core PCBs has advantages:
●Improved Thermal Conductivity: Iron alloys offer thermal conductivity, than aluminum leading to improved heat dissipation.
●Lower Cost: These alloys are a more cost-effective option compared to copper, making them an attractive choice for applications where budget considerations are important.
●FR4 Compatibility: Iron alloys can be readily fabricated using standard FR4 processes, streamlining manufacturing and cost-effectiveness.
●High Strength for Thin Cores: Iron alloys despite being less dense provide strength, for applications requiring cores enabling the creation of lighter and sleeker PCB designs. Metal core PCBs with iron alloys typically have a range of 0.1mm, to 3mm falling between 0.2mm and 0.5mm.
Applications:
Iron alloy-based metal core PCBs find application in various industries, including:
●Telecom Systems
●Automotive
●LED Lighting
●Industrial Electronics
Iron alloys, such as iron-nickel-cobalt, provide a favorable compromise between performance and cost for intermediate thermal conductivity core materials. These alloys offer improved thermal conductivity over aluminum while maintaining cost-effectiveness, making them a suitable choice for applications where a balance between performance and affordability is essential.
Comparing Metal PCB Materials: Aluminum vs. Copper Core vs. Iron-Based
Parameter | Aluminum | Copper | Iron Alloy |
Thermal conductivity | 130 W/mK | 400 W/mK | Up to 65 W/mK |
CTE | 23 ppm/°C | 17 ppm/°C | 10-15 ppm/°C |
Density | 2.7 g/cm3 | 8.9 g/cm3 | 7-8 g/cm3 |
Specific heat | 0.9 J/g°C | 0.39 J/g°C | 0.44-0.46 J/g°C |
Cost | Low | High | Medium |
Common thickness | 1-3mm | 0.5-2mm | 0.1-0.5mm |
Metal PCBs, commonly referred to as metal core PCBs (MCPCBs) are widely favored for power uses due, to their efficient heat dissipation and thermal control features, which contribute to the durability and dependability of electronic parts. When considering metal PCB materials, aluminum, copper core and iron based materials stand out as the three options. Lets evaluate them based on criteria.
Thermal Conductivity:
Copper Core: Copper has the highest thermal conductivity among the three materials, allowing it to efficiently transfer heat from electronic components.
Aluminum: Although aluminum has lower thermal conductivity than copper, it still provides adequate heat dissipation capabilities.
Iron-Based:Iron containing materials typically exhibit heat conductivity, than copper and aluminum which renders them less suitable, for high power uses
Cost:
Aluminum: Aluminium is often chosen for budget projects due, to its cost effectiveness compared to the materials available.
Copper Core: Although copper is pricier, than aluminum it provides conductivity. It is frequently utilized in situations where efficient power and heat dispersal’re essential.
Iron-Based: Iron based materials come in price ranges, which depend on their composition and how they are made.
Weight:
Aluminum: Aluminum is known for its properties making it a good choice, for situations where reducing weight’s crucial.
Copper Core: The copper core adds weight to the PCB compared to aluminum due, to its denser nature.
Iron-Based: Iron based materials may have a weight that falls between aluminum and copper varying based on their composition.
Strength and Rigidity:
Aluminum: Aluminum offers good strength and rigidity, providing mechanical support to the PCB.
Copper Core: While copper is less hard, than aluminum it still offers strength and stiffness.
Iron-Based: Iron containing materials may exhibit levels of strength and stiffness which can vary based on their makeup. Nonetheless they typically do not possess the level of strength, as aluminum or copper.
Corrosion Resistance:
Aluminum: Aluminum is prone to oxidation and corrosion. Proper surface treatment or coating is necessary to enhance its corrosion resistance.
Copper Core: Copper has better corrosion resistance than aluminum but can still oxidize over time. Surface treatment or coating is recommended for improved longevity.
Iron-Based: Iron-based materials are susceptible to rust and corrosion. Suitable protective coatings or treatments are necessary to prevent deterioration.
In general deciding on the metal PCB material depends on factors, like the needs of the application, such as managing heat staying within a budget dealing with weight restrictions and resisting corrosion. Copper core PCBs have conductivity but come at a higher cost whereas aluminum PCBs offer a more affordable choice with good heat dissipation abilities. Iron based materials could work for some cases. Typically have thermal conductivity and resistance, to corrosion.
Summary
Metal core PCB technology enables the efficient management of heat dissipation in electronic components and systems. Aluminum MCPCBs offer excellent value for cost-driven applications, while copper MCPCBs provide unmatched thermal performance at a higher cost. Iron alloys serve as a middle ground alternative. Designers must carefully evaluate their options to select the most suitable metal PCB technology that meets the specific requirements of their application.
Our services
Metal Core PCB Manufacturing & Assembly