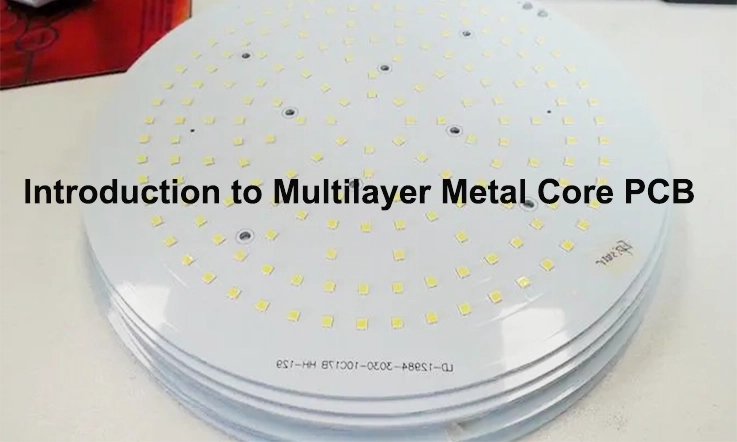
In today’s demanding industries, such asaerospace, military, and high-power electronics, selecting the right printed circuit board (PCB) ensures both performance and reliability. . Multilayer Metal Core PCBs (MCPCBs) are the go-to choice for high-power and high-current applications, thanks to their superior thermal conductivity, heat dissipation, and electrical efficiency. At JarnisTech, we specialize in designing and manufacturing customized Multilayer Metal Core PCBs that meet the most stringent requirements of high-performance systems. Whether you’re tackling challenges in thermal management or power distribution, our expertly crafted MCPCBs offer the ideal solution for your project needs.
Explore how our advanced manufacturing techniques, cutting-edge thermal solutions, and customizable designs can enhance your next high-power application. From concept to final production, we ensure your project runs on time, within budget, and meets all technical standards for peak performance.
Unveiling the Multilayer Metal Core PCB
Multilayer Metal Core Printed Circuit Boards represent a true leap forward in electronic design, particularly when it comes to managing heat in high-power and demanding environments. These PCBs are designed to withstand the heat generated by high-performance applications such as power electronics, automotive systems, and aerospace technologies. Unlike traditional PCBs, which typically rely on a single layer of material to support the circuitry, multilayer MCPCBs integrate multiple layers of metal, offering superior thermal management that ensures performance even under intense thermal stress.
What are Multilayer Metal Core PCBs?
A Multilayer Metal Core PCB is a specialized printed circuit board where multiple layers of metal are used as the base material, usually in combination with insulating layers. The metal core can be aluminum, copper, or other metals, chosen for their excellent thermal conductivity properties. In simple terms, these boards are designed to channel heat away from sensitive components, keeping everything cool under the hood.
Typically, these PCBs are made up of three layers: the top copper layer (for circuitry), the insulating layer (for electrical isolation), and the metal core (for heat dissipation). The copper is often used for high-current routing, while the metal layer beneath helps absorb and spread heat across the surface.
This design enables multilayer MCPCBs to support power-hungry applications without compromising performance. They ensure that high-power components like LEDs or power transistors don’t overheat, which can lead to system failure or degradation over time.
Key Features of Multilayer MCPCBs-
●Superior heat dissipation: The metal core facilitates fast and effective heat transfer.
●Durability and toughness: Designed to withstand extreme environmental conditions, including vibrations, shocks, and high temperatures.
●Enhanced electrical performance: Ensures low resistance and power loss due to the conductive materials used.
For industries like automotive, aerospace, or renewable energy, where reliability is non-negotiable, these PCBs provide the durability needed to keep complex systems running smoothly.
The Structure and Layers of Multilayer MCPCBs
The structure of multilayer MCPCBs is designed to balance both thermal and electrical performance. Here’s how the layers come together:
1.Top Copper Layer: This is where the electrical traces are made. It’s usually a thin copper foil etched to create the necessary circuits. For high-power devices, this layer can handle the current without the risk of overheating, thanks to the efficient heat management of the metal core beneath it.
2.Insulating Layer: Typically made of materials like IMS (Insulated Metal Substrate), the insulating layer sits between the copper and metal core. Its job is to electrically isolate the copper from the metal base, ensuring that electrical signals stay where they belong while still allowing heat to pass through.
3.Metal Core: The heart of the MCPCB, usually made of aluminum or copper, acts as the heat sink for the entire board. Aluminum is often favored for its lightweight and cost-effective nature, while copper is used in higher-end designs for its superior thermal conductivity. The metal core quickly absorbs heat from the components on the surface and spreads it across the PCB, preventing hotspots and improving the overall thermal stability of the system.
4.Bottom Copper Layer: The bottom copper layer, much like the top layer, directs current to the necessary components, ensuring a full circuit path. This layer supports high-power applications, where efficiency and consistent performance are required.
Example: In LED drivers used for high-power lighting, multilayer MCPCBs are the go-to solution because they keep the temperature under control while ensuring that the LED components receive the power they need without risk of thermal failure.
Comparing Multilayer Metal Core PCBs with Traditional PCBs
In a traditional PCB, the heat generated during operation can be a limiting factor, as conventional materials such as FR4 are less effective at dispersing heat. In contrast, multilevel MCPCBs utilize materials like aluminum or copper as the base substrate, which have significantly higher thermal conductivity. This allows the PCB to dissipate heat more effectively, maintaining optimal performance even in high-current or high-power scenarios. For industries that demand reliability, such as military, aerospace, or high-power lighting, multilayer MCPCBs offer a design solution that supports sustained power delivery while maintaining system integrity.
Let’s talk about traditional PCBs vs. multilayer MCPCBs. While traditional PCBs can handle basic circuit routing, their heat management and current-carrying capabilities are limited. As soon as you start dealing with high power, like in automotive electronics or power supplies, the need for something more robust becomes obvious.
●Traditional PCBs are typically made with materials like FR4 (fiberglass), which has great insulation properties but is not great at dissipating heat. If you use traditional PCBs for high-power applications, you’re setting yourself up for overheating and potential failure, especially with high-current industrial devices or military-grade electronics that demand a lot from their components.
●In contrast, multilayer MCPCBs take thermal and electrical management to the next level. The metal core design significantly boosts heat dissipation, ensuring devices remain stable even under heavy operation. Additionally, these PCBs accommodate more compact and densely packed circuitry, meaning you can enjoy both reliability and high-performance without compromise.
Example: In solar power systems, the solar inverters use multilayer MCPCBs because they manage both the high current and the thermal load generated in these devices. Traditional PCBs wouldn’t cut it because they would overheat too quickly, leading to system failure or reduced efficiency.
Here’s a quick comparison table for clarity:
Feature | Traditional PCBs | Multilayer MCPCBs |
Thermal Management | Moderate | Excellent |
Material | FR4, fiberglass | Aluminum, Copper |
Electrical Performance | Good, but limited | High current handling |
Durability | Low to moderate | High (shock, vibration) |
Cost | Low | Moderate to high |
Applications | Basic electronics | High-power, LED, Military, Automotive |
For high-power systems, such as military equipment or aerospace technology, where failures can lead to costly setbacks or even system-wide breakdowns, multilayer MCPCBs are a reliable investment. They don’t just get the job done—they ensure the long-term stability of the system under extreme conditions.
Thermal Management and Heat Dissipation in Multilayer Metal Core PCBs
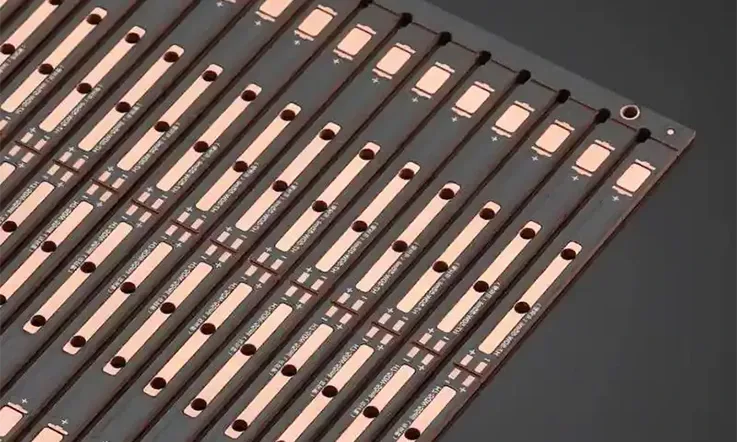
In high-power applications, managing heat is a major consideration when designing multilayer metal core PCBs. Devices like power electronics, LED lighting, and aerospace systems generate significant heat during operation, and improper heat dissipation can lead to performance degradation and early failure of components. Multilayer MCPCBs offer an effective way to address these challenges.
In this section, we’ll explore how multilayer MCPCBs handle thermal conductivity, tackle thermal resistance, and implement solutions like thermal interface materials (TIMs) and other advanced techniques to keep systems running smoothly in demanding environments. Let’s take a closer look at the ways multilayer MCPCBs are designed to manage heat efficiently in these high-power systems.
How Multilayer Metal Core PCBs Excel in Thermal Conductivity?
When it comes to managing heat, thermal conductivity is a core factor. Unlike traditional PCBs, multilayer metal core PCBs use materials like copper and aluminum, which excel at transferring heat. The metal core acts as an efficient heat sink, drawing heat away from high-power components and helping distribute it across the board.
●Thermal Conductivity and MCPCBs: The metal layer in multilayer MCPCBs is instrumental in managing heat. Copper, with its excellent thermal conductivity, ensures that heat is efficiently transferred away from sensitive components. By adjusting the thickness and composition of the metal core, the board can be tailored to meet the specific thermal requirements of the application.
●Why This Matters: In power electronics and LED systems, overheating can cause components to fail, reducing their lifespan and disrupting performance. By selecting the appropriate material and designing the PCB for efficient heat flow, multilayer MCPCBs prevent such issues and maintain long-term performance.
Material | Thermal Conductivity (W/m·K) | Typical Applications |
Copper | 390 | High-power electronics, LEDs |
Aluminum | 237 | General electronics, automotive |
Addressing Thermal Resistance Challenges in Multilayer Metal Core PCBs
While the metal core offers excellent heat dissipation, thermal resistance in other layers can impact overall performance. In multilayer MCPCBs, the dielectric layer between the metal core and the outer layers contributes to thermal resistance. Reducing this resistance is essential to ensure heat flows efficiently from the components to the core and out of the PCB.
●Thermal Resistance and Layer Design: The thickness and material properties of the dielectric layer have a direct impact on thermal resistance. For example, ceramic-based materials provide better thermal conductivity compared to traditional epoxy resins, making them ideal for high-performance applications. Additionally, the design of the via structure and the use of thin dielectric layers can help further reduce thermal resistance.
●Thermal Pathways: Efficient thermal design includes using well-placed thermal vias and ensuring that heat has a clear path to the metal core. Materials with high thermal conductivity, along with proper via placement, enhance the board’s ability to dissipate heat.
Thermal Challenge | Solution | Materials/Techniques |
Thermal Resistance | Use thin dielectric layers and high-conductivity materials | Ceramic substrates, copper vias |
Heat Dissipation | Design direct heat pathways using thermal vias | Heat sinks, thermal vias |
Thermal Interface Materials (TIM) for Multilayer Metal Core PCBs
Thermal Interface Materials (TIMs) enhance the efficiency of heat transfer between components and the metal core in multilayer MCPCBs. These materials help fill microscopic gaps between surfaces, improving thermal conductivity and reducing resistance to heat flow. By ensuring better heat dissipation, TIMs contribute to the overall reliability of high-power systems, supporting long-term performance even in demanding environments. When selecting TIMs for your project, consider their thermal conductivity properties to match the specific heat management needs of your application.
●Role of TIMs: Common TIMs include thermal pastes, pads, and films, which are chosen based on their ability to efficiently transfer heat while maintaining durability under extreme conditions. Silicone-based pads are often used for LED applications, while graphite films are popular in high-frequency circuits due to their superior thermal performance.
●Why It Matters: Without effective TIMs, multilayer MCPCBs would struggle to efficiently transfer heat from the components to the metal core, causing thermal bottlenecks and potential overheating. The right TIMs ensure that the heat generated in high-power systems is efficiently conducted away from the sensitive areas.
TIM Material | Thermal Conductivity (W/m·K) | Typical Application |
Silicone Pads | 1.0-3.0 | LEDs, power electronics |
Graphite Films | 200-500 | High-frequency devices |
Advanced Thermal Solutions for Power Electronics and LED Applications
When working with power electronics and LED applications, advanced thermal solutions are required to keep systems within operating temperature limits. These applications are notorious for generating high heat, and without effective management, the device’s performance and reliability can be compromised.
●Advanced Thermal Solutions: To meet the demands of these high-power systems, solutions like liquid cooling, heat pipes, and phase-change materials (PCMs) are often incorporated alongside multilayer MCPCBs. Liquid cooling systems use circulating coolant to absorb and remove heat more effectively than passive methods.
●Innovative Designs: In LED lighting, heat sinks are often used to maximize surface area for convection cooling. For power electronics, micro-channel cooling and forced-air cooling are increasingly used to manage the intense heat generated in high-density circuits.
Thermal Solution | Application | Benefits |
Liquid Cooling | Power electronics, LEDs | Enhanced heat dissipation |
Heat Pipes | Aerospace, high-power electronics | Efficient heat transfer across surfaces |
Phase Change Materials | LED applications, military | High thermal capacity |
Design and Manufacturing of Multilayer Metal Core PCBs
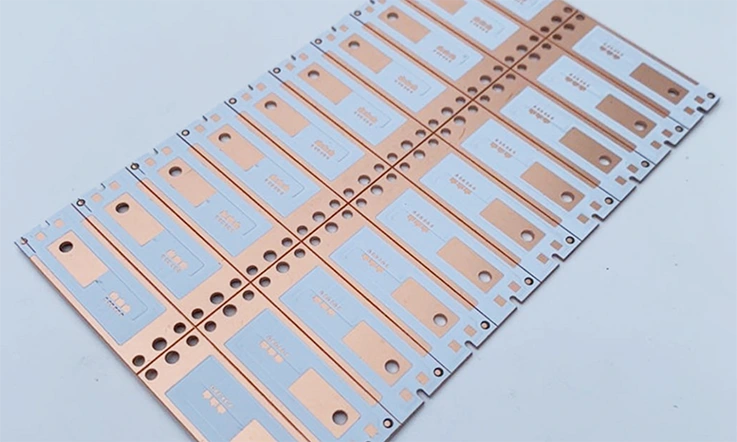
When it comes to designing and manufacturing multilayer metal core PCBs (MCPCBs), it’s not just about choosing materials and picking the right processes—it’s about getting everything right from the ground up. In high-power industries like aerospace, military, and power electronics, each step of the design and manufacturing process must ensure thermal efficiency, electrical performance, and mechanical integrity.
Let’s explore how material selection, design best practices, and a precision-driven manufacturing process come together to deliver MCPCBs that meet the most stringent demands of high-power systems. From aerospace to high-power equipment, it’s all about getting the right mix of quality control, precision, and efficiency—and that’s what makes multilayer MCPCBs stand out from the crowd.
The Importance of Material Selection for Multilayer Metal Core PCBs
For multilayer MCPCBs, material selection isn’t something to take lightly. The materials used directly affect the board’s thermal conductivity, electrical properties, and overall durability. Whether you’re designing for aerospace, high-current industrial devices, or military-grade equipment, choosing the right materials can make or break the success of your project.
The primary material choices for the metal core are typically aluminum, copper, or copper-alloy materials. Aluminum is commonly used due to its lightweight and cost-effective nature, while copper is preferred for more advanced applications requiring superior heat dissipation.
But it’s not just about the metal. The insulating layers—often made from materials like IMS (Insulated Metal Substrate)—play a significant role in isolating the metal core from the electrical components, providing the necessary electrical insulation while ensuring heat can still be effectively transferred away from the active components.
Here’s a breakdown of the typical materials used in multilayer MCPCBs:
Material Type | Properties | Applications |
Aluminum | Lightweight, good thermal conductivity | LED systems, automotive lighting |
Copper | High thermal conductivity, durable | High-power systems, aerospace |
IMS (Insulated Metal Substrate) | Insulation with thermal conductivity | Power electronics, military systems |
Polyimide | High thermal resistance, flexibility | Flexible MCPCBs, high-temperature |
In industries where thermal management is a concern, copper offers the highest thermal conductivity, making it ideal for applications where heat management is of the utmost importance. In contrast, aluminum provides a good balance between cost and thermal efficiency, making it the go-to for many commercial and consumer applications.
The takeaway? The material selection process in multilayer MCPCBs is as much about balancing cost with performance as it is about picking the right materials for the specific demands of the industry.
Multilayer MCPCB Design: Best Practices for Aerospace and Power Electronics
When it comes to multilayer MCPCB design, one size doesn’t fit all. For industries like aerospace, automotive, and power electronics, precision design is non-negotiable. These sectors demand PCBs that can handle extreme temperatures, high currents, and mechanical stress while providing long-term reliability.
In aerospace, for instance, the multilayer MCPCB needs to not only handle high currents but also manage thermal expansion and vibration resistance. Aerospace systems, including satellites and avionics, operate in extreme environments, often subjecting their components to fluctuating temperatures and constant movement. Therefore, multilayer MCPCB design must take into account:
●Thermal expansion matching: The materials used in the PCB must expand at a similar rate to the metal core and the other components, so that stress doesn’t build up and cause failures.
●High-reliability standards: Aerospace systems require a zero-failure tolerance. Therefore, multilayer MCPCB design must ensure that thermal management and mechanical integrity are baked into the design.
●Signal integrity: In power electronics, especially in systems like solar power inverters and automotive powertrains, preventing high-frequency signals from interfering with power distribution is a top concern. If these signals mix with the power lines, they can disrupt the performance and efficiency of the system. To address this challenge, it’s important to carefully design the PCB layout to minimize electromagnetic interference (EMI) and crosstalk.
For power electronics, it’s essential that the multilayer MCPCB design includes adequate space for heat sinks and conductive paths that can carry the current without excessive heating. This may require wide traces, optimal layer stackups, and additional heat dissipation features.
Best practices for design often include:
●Layer optimization: More layers can improve both signal integrity and thermal dissipation, but the design must account for the increased complexity and potential cost increases.
●Thermal simulation: Using thermal simulations to predict heat flow within the design can help avoid potential hotspots and ensure that heat is properly managed across the PCB.
●Design for manufacturability (DFM): Ensure that your design is optimized for the manufacturing process, minimizing potential issues during fabrication.
Manufacturing Process for Multilayer Metal Core PCBs: Precision and Quality Control
Once the design phase is complete, the next step is manufacturing. The manufacturing process for multilayer MCPCBs must be executed with precision to ensure the final product meets the necessary standards for thermal efficiency, electrical integrity, and mechanical durability.
At the core of the manufacturing process is precision etching, which is used to create the circuit traces on the copper layers. The process involves multiple steps:
1.Material preparation: The metal core (aluminum or copper) is cut to the required size and prepped with a specialized insulation layer.
2.Layer bonding: The copper layers are bonded with the insulating layer to form the core structure. Special techniques like lamination or adhesive bonding are used to ensure that the layers are properly aligned and bonded.
3.Etching: Once the material is bonded, the circuit pattern is etched into the copper layer through photolithography or laser etching. This step ensures both electrical reliability and signal integrity.
4.Drilling and vias: The next step involves creating holes for the vias—electrical connections between layers. These vias must be drilled with extreme precision to ensure no short circuits occur.
5.Final testing and inspection: Once the board is assembled, rigorous testing is done to ensure that the board meets thermal, mechanical, and electrical specifications.
For military applications or high-power equipment, quality control during manufacturing is absolutely essential. These PCBs must undergo additional rounds of testing, including:
●Thermal cycling tests to simulate the stress caused by extreme temperature variations.
●Mechanical stress tests to evaluate the board’s performance under shock and vibration.
●Electrical testing to confirm the correct functionality of every trace and via.
PCB Fabrication for Military and High-Power Equipment: Design Considerations
The fabrication process for multilayer MCPCBs used in military or high-power equipment is especially challenging. These boards need to handle a range of environmental factors, from extreme temperatures and mechanical stress to the electrical demands of high-current systems.
For military applications, the design considerations often include:
●Enhanced durability: These PCBs need to endure extreme environments, such as exposure to radiation, vibration, and electromagnetic interference (EMI). Selecting the right substrates and materials ensures they meet these demanding conditions.
●High-reliability standards: Military PCBs must meet standards like MIL-PRF-31032 for reliability, ensuring they perform in life-or-death situations without failure.
Example: For a military radar system, the multilayer MCPCB used to route power to the antennas must handle high currents while also managing the heat generated by these high-power components. Special attention is given to thermal conductivity, vibration resistance, and electrical insulation to ensure the system stays functional even in the harshest environments.
Challenges and Solutions in Multilayer Metal Core PCB Manufacturing
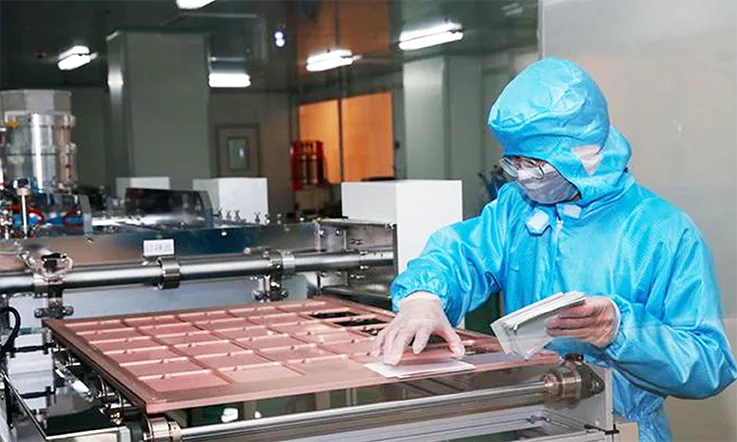
Multilayer metal core PCBs are essential components for industries that rely on high-power systems, including aerospace, military applications, and power electronics. The design and production of these boards present several challenges, from material selection and manufacturing constraints to managing thermal performance under demanding conditions. In this section, we’ll examine some of the primary challenges in MCPCB manufacturing and how effective solutions help overcome these obstacles to ensure high-performance boards.
Overcoming Material and Manufacturing Constraints
The selection of materials and the ability to handle manufacturing constraints are two central aspects of multilayer metal core PCB production. For industries like aerospace and military, selecting materials capable of withstanding high temperatures, vibration, and other extreme conditions is a must. Materials not only impact the thermal conductivity and mechanical strength of the boards but also determine their cost-effectiveness and longevity.
●Material Selection: The material choice directly impacts the performance of multilayer MCPCBs. For high-power applications, materials such as ceramic substrates or copper alloys are commonly selected due to their excellent thermal conductivity and electrical properties. These materials effectively manage the heat generated during high-power operation, ensuring optimal performance while maintaining electrical conductivity. By choosing the right material, the PCB can handle demanding tasks, offering both durability and efficiency in the process.
●Manufacturing Constraints: Manufacturing multilayer MCPCBs requires strict precision, especially when it comes to layer alignment and via placement. Advanced processes such as laser drilling and automated inspection systems are used to meet the rigorous demands of multilayer designs. These techniques ensure that each layer is aligned properly, and defects are minimized to preserve the integrity of the board during production.
Challenge | Solution | Materials/Processes |
Material Selection | Choose ceramic-based materials and copper alloys | Aluminum, ceramic substrates, high-performance copper |
Manufacturing Constraints | Laser drilling and automated inspection | Precision soldering, layer alignment techniques |
Handling High-Current Demands in Multilayer Metal Core PCB Production
For systems with high-current requirements—such as electric vehicles, industrial machinery, and power electronics—multilayer MCPCBs must be designed to withstand the heat and power demands without compromising their structural integrity or performance.
●Challenge: As current flows through the PCB’s traces, heat is generated. If not managed properly, this heat can degrade the performance of the board, lead to circuit failures, or affect signal integrity. Thermal vias and thicker copper traces are necessary to handle the heat generated from high-current flow, but designing these features within the constraints of multilayer construction adds a level of complexity.
●Solution: To address these challenges, we can increase the thickness of the copper traces to reduce the electrical resistance and handle higher currents. Additionally, thermal vias are implemented to provide efficient heat dissipation by connecting the metal core to the outer layers of the PCB. By doing so, the board can distribute heat more effectively and reduce the risk of thermal damage.
Challenge | Solution | Design/Techniques |
Handling High Current | Use thicker copper traces and thermal vias | Copper plating, thermal vias |
Preventing Overheating | Advanced plating and current distribution | High-performance materials |
Addressing Design and Tolerance Challenges
The design of multilayer MCPCBs requires precise placement of all components, such as signal traces and thermal vias, within strict tolerances. Even minor misalignments or design deviations can lead to performance degradation, especially in high-frequency systems used in aerospace or military electronics. Careful attention to detail during the design phase ensures that these boards can handle the demanding requirements of their applications, while maintaining the necessary functionality and efficiency.
●Challenge: Maintaining precise tolerances in multilayer PCBs is essential, especially for high-frequency applications where signal integrity is affected by even minor misalignments. In addition, layer thickness variation can lead to uneven heat distribution, negatively impacting thermal performance.
●Solution: To manage these tolerance challenges, laser drilling and automated alignment systems are employed to ensure precise layer placement. We also use 3D modeling software to simulate the board’s design before fabrication, allowing us to visualize potential issues and adjust the design accordingly. By maintaining strict control over tolerance levels, we ensure that the signal traces and thermal vias are correctly aligned to maintain the board’s performance and durability.
Challenge | Solution | Techniques |
Design Tolerances | Laser drilling and automated alignment | 3D modeling software, stress testing |
Signal Integrity | Use of tight tolerances for high-frequency systems | Precision PCB design, signal simulations |
Ensuring Reliable Thermal Performance in Harsh Environments
In industries where harsh environments are the norm, ensuring that multilayer MCPCBs maintain reliable thermal performance is a major consideration. Applications such as military systems, aerospace, and high-power industrial electronics often involve extreme temperature fluctuations, making it difficult for conventional materials and designs to manage the heat load effectively.
●Challenge: Thermal performance in harsh environments is a constant challenge for multilayer MCPCBs. High temperatures can lead to degradation of the materials and thermal stress in the layers, leading to PCB failure. Effective thermal management is necessary to prevent overheating and maintain board functionality.
●Solution: To enhance thermal performance, multilayer MCPCBs are designed with thermal vias, high-conductivity materials such as copper or ceramic substrates, and heat sinks. These techniques help to distribute the heat more effectively and maintain the integrity of the PCB. In extreme environments, liquid cooling systems or solderless technologies can also be incorporated to enhance heat dissipation.
Challenge | Solution | Materials/Designs |
Thermal Performance | Use of copper-based substrates and ceramic coatings | Liquid cooling, high-thermal conductivity materials |
Harsh Environments | Solderless technologies and advanced cooling | Thermal vias, heat sinks |
How Customizing Multilayer Metal Core PCBs for High-Power and High-Current Applications?
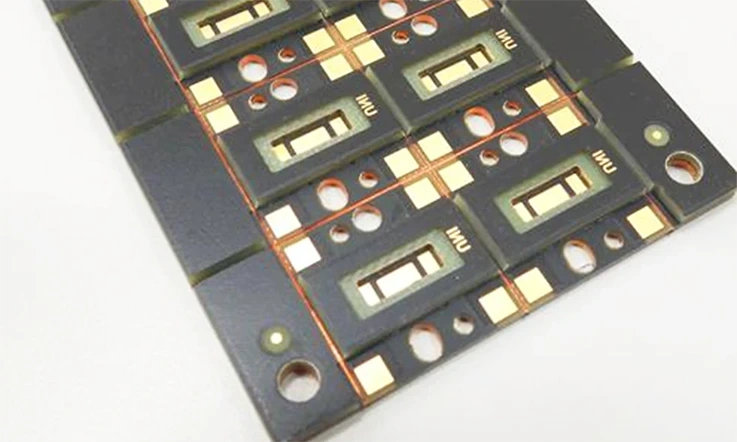
In industries like aerospace, military manufacturing, and power electronics, the need for custom solutions in Multilayer Metal Core PCBs has surged. These applications demand performance that exceeds the capabilities of conventional PCBs, particularly in high-power and high-current environments. Whether it’s for power distribution systems or high-voltage systems, designing a Multilayer MCPCB to meet these needs isn’t just about throwing together layers of copper and insulation. It’s about crafting a board that will handle demanding workloads while maintaining reliability in tough environments. The following sections explore how we can customize these designs to meet specific application needs.
Tailoring Multilayer MCPCB Designs for High-Current Power Distribution
When designing for high-current power distribution, the physical layout of the PCB plays a central role in managing both heat and current flow. High-power systems require MCPCBs that can handle large current levels without issues like overheating or voltage drop. Addressing these challenges involves selecting the right materials, optimizing the number of layers, and adjusting design details to improve thermal management and efficient current routing. By making informed design choices, you can create a more reliable and long-lasting solution that keeps the system running smoothly.
To achieve efficient current distribution ,we need to carefully consider the width of traces, copper thickness, and the selection of materials with low resistance. Additionally, the layout should incorporate enough surface area for heat dissipation, while minimizing the length of current paths to avoid unnecessary losses. Customizing these features ensures that the MCPCB can deliver stable power even under heavy load conditions.
Key Design Strategies-
●Thicker Copper Layers: Using thicker copper layers in the design helps to manage high current demands and minimizes the chance of overheating.
●Optimized Trace Widths: Wider traces help distribute heat more evenly and reduce resistance, which aids in managing power distribution effectively. By increasing the width of the traces, the PCB can accommodate higher currents without excessive heat accumulation or power loss. This design adjustment ensures smoother power flow through the system, supporting consistent performance while preventing overheating.
●Thermal Management Features: Integrating thermal vias and pads helps in spreading heat across the board, improving overall performance.
By applying these strategies, you ensure that Multilayer MCPCBs can handle high-current applications with minimal thermal strain, maintaining performance without compromising on durability.
Custom Solutions for High-Voltage and High-Power Systems
High-voltage and high-power systems place immense stress on the PCB, requiring designs that offer not just electrical conductivity but also insulation and thermal management. The challenge here is balancing the need for efficient power transmission with the requirement for safety and long-term reliability. Multilayer Metal Core PCBs for these systems require precision, specifically tailored to the voltage and current levels involved.
In high-voltage applications, insulating layers are essential. The dielectric materials used in MCPCBs must feature a high breakdown voltage and a low dissipation factor to meet performance needs. Additionally, minimizing signal interference and managing electromagnetic compatibility (EMC) are necessary steps. The MCPCB must effectively handle both power and signal transmission, preventing cross-talk or performance issues, and ensuring smooth operation throughout the system.
Design Considerations for High-Voltage Systems-
●Layer Stack-up Customization: Specific layer stack-ups with tailored insulation properties ensure that there’s no cross-talk between power and signal traces.
●High-Dielectric Materials: High-performance dielectric materials like polyimide, PTFE, or high-temperature epoxies are essential to withstand the high voltage.
●Precision Engineering: To manage high power systems, precise control of layer alignment and trace placement helps to avoid issues like arcing or breakdown.
By incorporating these custom solutions, MCPCBs are not just able to handle high voltages, but they can also perform reliably under demanding high-power conditions.
Addressing Thermal Cycling Challenges in High-Power Devices
In high-power systems, thermal cycling can have a significant impact on the long-term performance of MCPCBs. High currents and power levels generate heat, and when components experience fluctuating temperatures over time, the board must endure this stress without compromising its integrity. This is where thermal cycling challenges arise, and why careful consideration of thermal management is necessary during design.
To address this, the use of highly thermally conductive materials in Multilayer Metal Core PCBs is essential. The metal core acts as a heat sink, channeling heat away from high-power components and spreading it across the board. Properly designed via systems and heat sinks further improve heat dissipation, allowing the MCPCB to handle thermal cycling without failure.
Techniques to Manage Thermal Cycling-
●Thermal Via Design: Ensuring thermal vias are placed in the optimal locations helps spread heat across the board, reducing hotspots.
●Material Selection for Thermal Resistance: Choosing materials with high thermal conductivity allows the board to cool faster during temperature fluctuations.
●Enhanced Soldering Techniques: Specialized soldering techniques, such as those used in aerospace applications, help ensure that components stay firmly attached despite temperature-induced expansions and contractions.
By addressing these challenges head-on, Multilayer MCPCBs remain robust, even when subjected to extreme thermal cycling in high-power devices.
Enhancing Performance and Reliability of Multilayer MCPCBs for Power Electronics
Power electronics, such as power supplies and inverters, depend on MCPCBs to maintain stable and continuous operation. To enhance performance and durability, the design must focus on effective heat management, robust materials, and solid electrical performance. This means carefully selecting materials, fine-tuning trace layouts, and ensuring that every layer in the MCPCB serves its purpose in creating a balanced and efficient power delivery system.
Optimizing Multilayer MCPCB design for power electronics involves more than just handling heat; it also includes ensuring that the traces are laid out in such a way that electrical losses are minimized. High-frequency noise is another issue to address, which is why incorporating effective grounding and shielding techniques is necessary.
Improvement Strategies for Power Electronics MCPCBs-
●Increased Trace Widths: Wider traces help to handle higher currents and reduce the risk of electrical losses.
●Fine-Tuned Layering: Properly designed layers not only ensure efficient heat dissipation but also allow for better power delivery with minimal interference.
●Reinforced Copper Pads: Using thicker copper pads on power traces helps increase the board’s overall strength and reliability, especially under extreme conditions.
With these strategies, Multilayer MCPCBs can consistently deliver high performance and long-term reliability in power electronics, ensuring they meet the rigorous demands of the industry.
Why Choose Us for Manufacturing Multilayer Metal Core PCBs for Your Project?
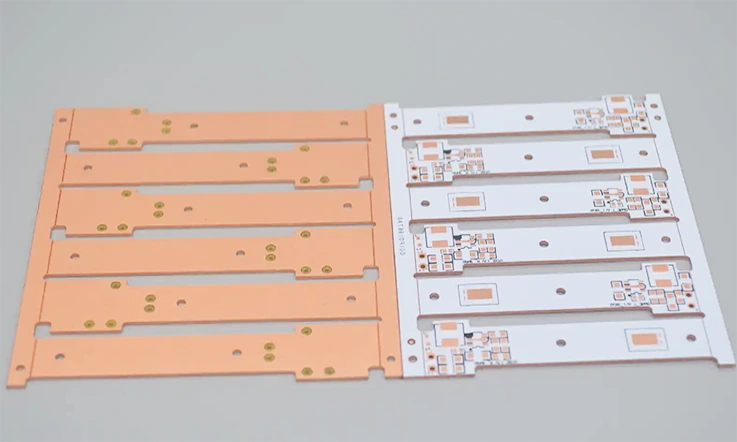
When it comes to selecting a manufacturing partner for your Multilayer Metal Core PCB project, you need a company that not only understands the complexity of these advanced circuit boards but also has the experience and technical expertise to deliver high-quality, reliable solutions. At JarnisTech, we offer customized Multilayer MCPCBs tailored to meet the specific demands of industries like aerospace, military, high-power electronics, and industrial applications. Here’s why partnering with us for your Multilayer Metal Core PCB manufacturing is the best decision for your next project.
1.Expertise in High-Current and High-Power Applications
At JarnisTech, we specialize in manufacturing Multilayer Metal Core PCBs designed to handle high-current and high-power applications. Our team of experienced engineers understands the challenges posed by these demanding systems, including the need for efficient power distribution and thermal management. With a deep knowledge of the materials and techniques required, we can provide you with a PCB that ensures optimal electrical performance and heat dissipation, even in the most strenuous environments.
2.Comprehensive Expertise in Aerospace and Military-Grade Applications
For industries like aerospace and military, where reliability and performance are non-negotiable, we have the expertise to create Multilayer MCPCBs that meet the highest standards. Our designs are engineered to withstand extreme environmental conditions, including high vibrations, thermal fluctuations, and exposure to harsh chemicals. With our advanced manufacturing capabilities, we can create PCBs that meet military specifications (MIL-SPEC) and aerospace standards, ensuring that your project performs under even the toughest conditions.
3.Advanced Manufacturing Techniques and Precision Quality Control
We pride ourselves on using state-of-the-art manufacturing techniques and cutting-edge technology to produce Multilayer Metal Core PCBs. Our advanced processes, from material selection to fabrication, ensure that each PCB is made to the highest standards. Rigorous quality control measures are applied at every step of production, so you can trust that your PCBs will meet or exceed your expectations.
4.Competitive Pricing with Exceptional Value
We understand that cost efficiency is a priority for our clients, especially in high-volume manufacturing. At our company, we offer cost-effective solutions for manufacturing Multilayer Metal Core PCBs, providing excellent value without sacrificing quality. Our expertise in mass production ensures that you can achieve the economies of scale necessary for your project while receiving a high-performance product.
5.End-to-End Support and Collaboration
At JarnisTech, we understand that teamwork makes the dream work. From the first sketch of the design to the final product delivery, we stay closely aligned with our clients to make sure their needs are met and their expectations exceeded. Our engineers are hands-on throughout every stage, offering support to ensure that everything runs like clockwork and that all technical specifications are spot on. We’re with you every step of the way, making sure your project goes from concept to completion with precision and efficiency.
Contact Us Today:
Ready to take your project to the next level? Get in touch with us today, and let’s discuss how our Multilayer MCPCBs can drive the performance and reliability of your system forward.
Multilayer Metal Core PCBs & FAQ
1. Can Multilayer Metal Core PCBs be flexible?
Typically, MCPCBs are rigid due to the metal core, but they can be designed for flexibility in some specialized applications.
2. What is the lifespan of a Multilayer Metal Core PCB?
MCPCBs have a long lifespan when properly managed for thermal cycling and mechanical stress, especially in high-power environments.
3. Can Multilayer Metal Core PCBs handle high-frequency signals?
With proper design and materials, MCPCBs can be used in high-frequency applications, though the metal core can sometimes impact signal propagation.
4. Are Multilayer Metal Core PCBs customizable?
Yes, MCPCBs can be tailored for specific needs, including different metal cores, layer counts, and additional features like thermal vias.
Our services
Metal Core PCB Manufacturing & Assembly