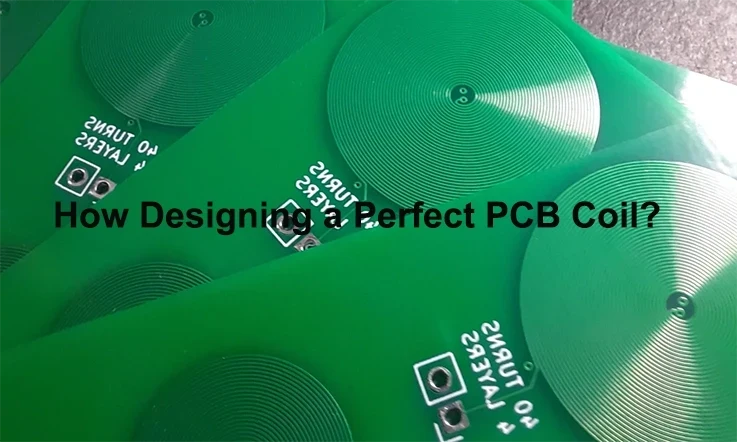
Designing a high quality PCB coil is an endeavor that requires careful consideration of multiple aspects. A designed coil can significantly boost the effectiveness and efficiency of electronic circuits. This post offers engineers an insight into the essential factor to consider and best practices for developing an ideal PCB coil. By adopting a strategy and avoiding typical mistakes engineer can guarantee that their coils achieve exceptional performance, dependability and ease of manufacturing.
Importance of Designing a Perfect PCB Coil
Designing a PCB coil holds significant importance in a range of electronic uses particularly in scenarios requiring signal transmission, power transfer or electromagnetic induction. Here are some key reason highlighting the importance of designing a perfect PCB coil:
Efficient Signal or Power Transfer
PCB coils find application in various fields like wireless communication setups, power sources and inductors. A crafted coil enhances signal or power transmission efficiency by reducing losses enhancing coupling and optimizing impedance alignment. This leads to improved performance and higher efficiency in the overall system.
Electromagnetic Compatibility (EMC)
A design coil layout is crucial for maintaining electromagnetic compatibility. And the electromagnetic compatibility denotes the capability of devices to operate smoothly without causing disruptions to or being disrupted by other devices in close proximity. A designed coil aids in minimizing electromagnetic emissions and vulnerability to external electromagnetic disturbances guaranteeing the dependable performance of the system and averting possible problems such as cross talk or signal distortion.
Frequency Response and Bandwidth
The design of a PCB coil greatly influences its frequency response and bandwidth characteristics. When designers choose the coils characteristics like the number of turns, size and material used they can customize its response to suit needs, for various uses. This becomes crucial in situations where high frequency signals or broad bandwidths are involved.
Size and Space Optimization
PCB coils are frequently employed in electronic gadgets with restricted space. Designing a coil that’s just the right size and shape can conserve precious PCB space and enable sleek and effective system layout. By considering factors such as the coil’s dimensions, shape and orientation, designer can minimize its footprint while still maintaining the desired electrical performance.
Thermal Considerations
Power transfer applications, such as wireless charging or power converters, can generate heat in the PCB coil. A crafted coil considers thermal factors by choosing materials with minimal resistive losses adjusting conductor dimensions and implementing effective heat dissipation methods. This helps in reducing temperature rise, improving power handling capacity, and ensuring long-term reliability of the coil and the surrounding components.
Manufacturing and Assembly
Designing a PCB coil that can be easily manufactured and assembled plays a role in streamlining production processes. When designing coils it is important to take into account factors like manufacturing limitations, soldering or connection ease and compatibility, with used manufacturing methods. Following design principles including adequate spacing, clear labeling and appropriate pad shapes ensures seamless integration of the coil into the PCB assembly procedure.
Advantages of a well-designed PCB coil
● Accurate Inductance
● Low Resistance
● Reduced Electromagnetic Interference (EMI)
● Enhanced Reliability
● Cost Optimization
Features of Poor Coil Design
● Incorrect Inductance
● High Resistance
● EMI Susceptibility
● Reliability Issues
Hence designing a perfect PCB coil design is pivotal in attaining peak system performance, dependability and cost efficiency. Through following established guidelines and taking into account factors engineers can develop coils that satisfy the rigorous standards of contemporary electronic gadgets ensuring precise inductance, minimal resistance, immunity, to EMI interference, improved reliability and cost efficiency.
Factors to Consider in PCB Coil Design
When designing a PCB coil it’s important to take into account element to guarantee the best possible performance and functionality. Here are the essential factor to remember:
Inductance Value
To find the right inductance value for your circuit consider factors. Such as frequency, current and the impedance you want. This will help make sure the coil fits the need of your application.
Trace Geometry
Optimize trace width and spacing to enhance inductance while keeping parasitic capacitance and inductance to a minimum. It’s important to ensure there’s space between traces and other parts. It’s for good signal quality and reduce interference.
Number of Turns
Determine the number of turns needed by considering the desired inductance value and the selected trace layout. Take into account how multiple layers and winding method affect inductance in order to reach the desired level of performance.
Current Density
Choose the appropriate current density to reduce resistance and power loss in the coil. Take into account the heat dissipation abilities of the nearby components to guarantee dependable performance.
Substrate Material
Select base material that has electrical loss and good heat conduction to reduce inefficiencies and enhance functionality. Consider option such as FR-4, polyimide, or specialized material based on the specific application requirement.
Shielding and Grounding
Utilize efficient shielding methods to reduce interference and establish good grounding to prevent disruptions and uphold signal quality. This helps create a robust and reliable coil design.
Manufacturing Considerations
Adjust the etching tolerances for consistency in inductance levels throughout production. Choose soldering techniques to prevent coil damage and establish durable connections for sustained effectiveness.
Simulation and Validation
Use simulation software to anticipate how coils will perform and detect any potential issues before creating prototypes. Confirm the design by taking measurement and conducting test to guarantee accuracy and functionality in real world scenarios.
Additional Factors:
● Environmental Conditions
● Cost and Availability
● Form Factor
● Testability
Designing a Perfect PCB Coil Step-by-Step
Step 1: Determine Inductance Requirements:
To begin it’s important to grasp the circuit needs and establish the inductance value by taking into account aspects, like frequency, current and impedance.Additionally, consider how the inductance will affect the circuit’s functionality and overall performance.
Step 2: Analyze Circuit Constraints:
Assess at the space on the PCB. Check for any limitations that could affect how the coil is designed. Keep in mind things, like the size of the board how its laid out and where other parts are positioned to make sure the coil integration in smoothly.
Step 3: Select Coil Type and Configuration:
Select the appropriate coil type based on application requirement. Such as solenoid, toroidal, or air core. Also decide on the coil setup. Whether it should be single layer or multi layer. Based on how much space you have and what performance goals you want to achieve.
Step 4: Calculate Coil Parameters:
Determine how many turns are necessary to reach the desired inductance based on the chosen type and arrangement of the coil. Calculate the trace width spacing and thickness based on current density considerations factoring in power dissipation and resistance.
Step 5: Optimize Trace Geometry:
Utilize simulation software or analytical calculations to optimize the trace geometry for maximum inductance and minimal parasitic effects. Adjust trace width, spacing, and shape to minimize resistance, parasitic capacitance, and electromagnetic interference.
Step 6: Choose Substrate Material:
Choose substrate material that offer low dielectric loss, high thermal conductivity and suitable electrical properties. Evaluate choices like polyimide or custom material depending on the required performance, cost and accessibility.
Step 7: Implement Shielding and Grounding:
Try using shielding methods like grounded planes or shields to decrease interference. Also make sure you have the grounding to lower noise and uphold signal integrity, in the design.
Step 8: Validate Design Through Simulation and Prototyping:
Utilize simulation tools to verify the coil’s performance, including its inductance, resistance, and electromagnetic characteristics. Follow up by prototyping the coil design and conducting tests to validate its functionality and performance under real world condition.
Step 9: Consider Manufacturing Process:
Make sure the design is easy to manufacture considering etching tolerances, panelization and solder mask needs. Also ensure that the coil design can be smoothly incorporated into the production process and meets manufacturing limitations.
Step 10: Evaluate Cost and Reliability:
Evaluate the cost efficiency of the design by assessing material expenses, manufacturing techniques and component accessibility. Also guarantee the coils dependability by taking into account aspects, like heat regulation, environmental factors and projected lifespan.
Simulation and Validation in PCB Coil Design
Simulation
● Utilize electromagnetic simulation software to create a comprehensive virtual model of the coil and its surrounding environment.
● Input design parameters such as trace geometry, number of turns, and substrate properties into the simulation software.
● Simulate the coil’s behavior under various operating conditions, such as different frequencies and currents.
● Analyze the simulation results to predict important performance metrics like inductance, resistance, and impedance.
Validation
● Fabricate a physical prototype of the coil based on the simulated design.
● Conduct measurements using dedicated equipment like inductance meters or impedance analyzers.
● Compare the measured results with the predictions from the simulation to validate the accuracy of the design.
● Make necessary adjustments to the design if significant discrepancies are identified during the validation process.
Benefits of Simulation and Validation
By using simulation and validation engineers can minimize the chances of design mistakes by catching potential problems early on. These tools are essential for tuning circuit performance to ensure that the coil meets specific inductance and resistance requirements. Moreover testing the design under operational scenarios enhances its reliability enabling the early detection and resolution of any possible issues before they impact the final product. This method not speeds up product launches by reducing the need for multiple physical prototypes but also leads to significant cost savings by addressing design flaws at an earlier stage in the development process.
Tips for Effective Simulation and Validation
1. Use accurate material properties and boundary conditions in the simulation model to ensure realistic results.
2. Perform simulations at multiple frequencies and current levels to capture a wide range of operating conditions.
3. Validate the design over a range of temperatures and environmental conditions to ensure its robustness.
4. Increase confidence in the design by comparing simulation results with measurements from multiple physical prototypes.
5. Thoroughly document simulation and validation results for future reference and traceability.
Sum up
Designing a PCB coil involves a precise and detailed approach requiring meticulous attention to specifics and adherence to established standards. By taking into account factors like the need for inductance optimizing trace geometry implementing EMI shielding and managing considerations engineers can develop coils that align with the required specifications and enhance circuit performance. Moreover the inclusion of simulation and validation processes is essential, to ensuring the accuracy and dependability of the designs. Through preparation, iteration and validation procedures engineers can successfully accomplish the task of creating an ideal PCB coil that delivers optimal functionality, efficiency and reliability across a range of electronic applications.