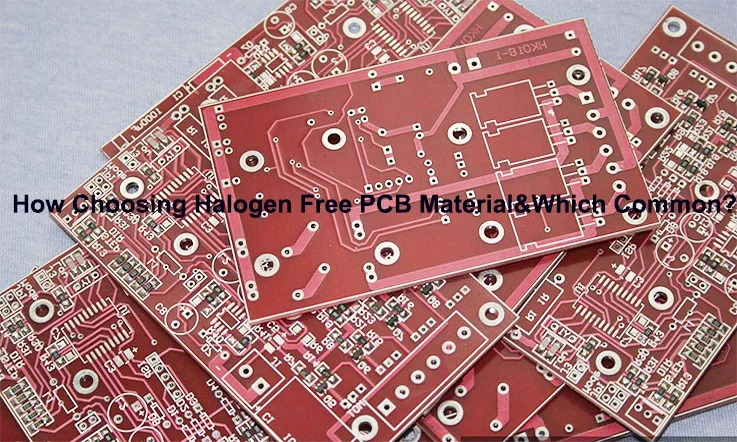
Choosing the PCB material is essential in electronic design and halogen free options are becoming more popular for their environmental friendliness and enhanced safety features. This piece will delve into the importance of opting for halogen free PCB materials cover various commonly used options, in the market and offer insights to help you make well informed choices.
Overview of Halogen-Free PCB Materials
Halogen free PCB material refer to printed circuit board that do not include halogenated flame retardants. Such as bromine or chlorine. These material have gained popularity because of their impact on the environment and health.
Materials that do not contain halogens are known for not including elements like fluorine, chlorine, bromine, iodine and astatine. Halogens are often used as flame retardants in plastics and other material. When they burn they release harmful fumes. Halogen free material have advantages, over those that contain halogens.
● Reduced toxicity
● Improved environmental performance
● Enhanced electrical performance
The primary distinction between halogenated and halogen-free PCBs lies in the type of flame retardant utilized. Halogenated PCBs use flame retardants with halogens while halogen free PCBs choose for halogenated alternatives. Non-halogenated flame retardants generally possess lower toxicity levels and exhibit greater environmental compatibility when compared to their halogenated counterparts. Additionally they have a lesser effect on the electrical properties of the PCB material.
How Choosing Halogen-Free PCB Materials?
When selecting halogen-free PCB material, several factors should be taken into consideration. These factor encompass the needs of the application, such as temperature tolerance, resistance to chemicals and electrical characteristics. Moreover assessing the cost implications is crucial since halogen free material might come at a price compared to their halogen containing counterparts. In addition, availability also plays a role in decision making as halogen free materials could potentially have longer lead times. Here are some key aspects to keep in mind when opting for halogen PCB materials.
Compliance with Regulations and Environmental Impact:
Halogen free materials play a role in adhering to environmental rules like the Restriction of Hazardous Substances (RoHS) directive. It’s crucial to choose materials that meet these standards to prevent any issues. Moreover halogen-free materials are more environmentally friendly, as they do not release harmful halogen gases when exposed to high temperatures. When picking materials it’s essential to think about their effects environmental and give preference to sustainable and eco friendly options.
Performance Requirements and Cost:
When selecting halogen free material it’s crucial to take into account the particular performance need of the application, such as temperature range, electrical characteristics and mechanical durability. Select for material that fulfill these requirements to guarantee the reliability and durability of the PCB. While halogen free options may be more expensive compared to halogenated ones it’s important to weigh these costs against the advantage. Assessing the cost efficiency of these materials over the products lifespan is vital, for making a well informed choice.
Availability and Lead Times and Compatibility with Manufacturing Processes:
To prevent any production hiccups it’s important to verify that these material are compatible with PCB manufacturing processes and can be processed and put together without any hassle. Additionally, to make sure that can quickly get halogen free material for production as these material may be harder to find or not as easily accessible, as the traditional halogenated ones.
Common Halogen Free PCB Materials in the Market
There are halogen free PCB materials on the market each with unique properties tailored for different applications. Some of the utilized halogen free PCB materials are FR4 (Flame Retardant 4) FR408 (High Temperature FR4) Isola I-Speed (Ideal, for High Speed Circuitry) Nelco N4000-13 (Designed for RF/Microwave applications) and Teflon (Known for its Exceptional Chemical Resistance).
FR4 is an used type of glass reinforced epoxy laminate that is often found in the manufacturing of PCB. It comes in grade, including halogen free options. In contrast FR408 is another type of glass reinforced epoxy laminate designed for use in applications where higher operating temperatures are required. It also offers halogen free grades. These two materials are the most prevalent halogen free PCB material due to their favorable balance of cost, performance and availability.
Other notable halogen-free PCB materials include:
Isola I-Speed (High-Speed Circuitry): Isola I-Speed is specifically designed for high-speed digital applications. It is available in halogen-free grades, catering to applications with stringent environmental requirements.
Nelco N4000-13 (RF/Microwave): Nelco N4000-13 is a high frequency laminate designed for use in RF and microwave application. It have halogen free option making it suitable for eco friendly designs.
Teflon (Extreme Chemical Resistance): It is a type of fluoropolymer is well regarded for its ability to withstand harsh chemicals. In situations where environmental factorsre significant there are Halogen free variations of Teflon that can be utilized.
While FR4 and FR408 are frequently used halogen PCB materials but Isola I-Speed, Nelco N4000-13 and Teflon stand out for their unique characteristics tailored to different purposes. Isola I-Speed is great for speed digital tasks, Nelco N4000-13 is perfect for RF and microwave uses and Teflon offers exceptional resistance to chemicals.
Differences between Halogenated and Halogen-Free PCBs
When evaluating halogen free PCB material important aspects to take into account are the glass transition temperature (Tg) coefficient of thermal expansion (CTE) dielectric constant (Dk) and dissipation factor (Df). A higher Tg is advantageous for operations in elevated temperatures whereas a lower CTE is preferred for maintaining stability. A lower Dk is ideal for high-speed applications, and a lower Df is essential for minimizing power loss.
The primary distinction between halogenated and halogen free PCB lies in the type of flame retardant employed. Halogenated PCB use flame retardants, with bromine or chlorine which help stop fires from spreading. However when they burn halogenated flame retardants can release toxic fumes.
In contrast, halogen free PCB employ non-halogenated flame retardant that lack halogen element. These alternatives are less effective at fire suppression compared to halogenated variants but do not emit toxic fumes when burned.
Additional disparities between halogenated and halogen free PCB encompass factors. Such as cost, availability, and environmental impact. Halogenated PCB are usually cheaper and easier to acquire compared to halogen ones. Nevertheless, halogenated PCB can lead to the production of pollutants such as dioxins and furans while halogen free PCB do not have a role in their creation.
Halogen free PCB offer several advantages, including reduced toxicity, improved environmental performance, and better electrical propertie. These qualities make them ideal, for uses that emphasize safety and eco friendliness. Yet it’s essential to note that opting for halogen PCB could result in increased expenses and restricted availability when compared to their halogen containing alternatives.
Halogen free PCBs are used in a variety of industries. Like equipment, aerospace technology, industrial controls, transportation networks and environmental conservation effort. Their utilization is particularly advantageous in scenarios where safety and environmental performance are critical factor to consider.
Common Applications of Halogen-Free PCBs
● Medical devices
● Aerospace applications
● Industrial control systems
● Transportation systems
● Environmental protection
Moreover halogen free PCBs are commonly used across industries such as consumer electronics, telecommunications, data storage and military applications. With the increasing need, for eco sustainable solutions the usage of halogen free PCBs is projected to increase consistently. These materials provide benefits in terms of lower toxicity, better environmental impact and increased operational effectiveness.
Sum Up
Selecting the halogen free PCB material is crucial for attaining peak performance, environmental friendliness and adherence to regulations. Popular choices, like FR4, FR408, Isola I-Speed, Nelco N4000-13 and Teflon provide a variety of characteristics that cater to needs. By taking into account specifications meeting regulatory standards assessing performance criteria and weighing cost considerations engineers and designers can intelligently choose halogen free PCB materials for their electronic designs success.