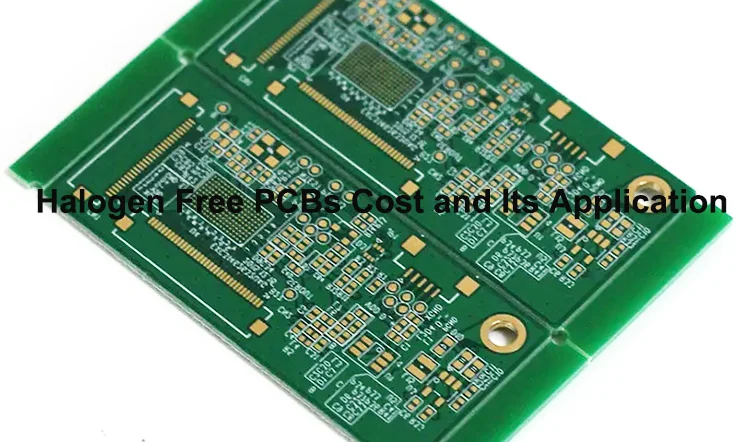
In the few years there has been a significant increase in the use of halogen free PCB due to their safety features and environmental benefits. However there may still be some uncertainty regarding their cost and potential uses. This article aims to provide an overview of halogen free PCB including factor affecting their prices the advantages they provide and how they are used in different industries. By delving into these aspects readers will develop an understanding of halogen free PCBs and their importance in today world
What is Halogen Free PCBs?
Halogen free printed circuit boards (PCBs) are PCBs that do not contain flame retardants. Halogens, such as fluorine, chlorine, bromine, iodine and astatine are often utilized as flame retardants in materials. As we know that halogen have harmful effect due to toxicity and corrosiveness.
Halogen free circuit boards are made with flame retardants like phosphorus based nitrogen based or inorganic compounds that are safer for people and the environment. These boards have benefits compared to traditional halogenated ones. Such as lower fire risk since they are less likely to catch fire and spread flames. Moreover halogen free circuit boards show better electrical performance features such as insulation resistance and reduced dielectric loss, than their halogenated versions.
Moreover PCBs that are free of halogens adhere to the RoHS directive ensuring they are devoid of substances prohibited by the European Union. This emphasis, on responsibility highlights the sustainability and safety advantages linked to the utilization of halogen free PCBs.
Types of Halogen Free PCBs
There are some primary categories of halogen-free PCBs:
● High Speed PCBs
● Rigid-Flex PCBs
● Ceramic PCBs
● High-frequency PCBs
● Thermal management PCBs
● RF PCBs
● Microwave PCBs
Benefits of Halogen Free PCBs
● Environmental friendliness
● Health and safety
● Compliance with regulations
● Improved fire safety
● Electrical performance
In general using halogen free PCB brings various advantages that support sustainability, health, safety and compliance with regulations in the electronics sector.
Factors Affecting the Cost of Halogen Free PCB
The cost of halogen-free PCB can vary depending on several factors. Some of the key factors that can influence the cost of halogen-free PCB include:
Board Size and Complexity:
The dimensions and complexity of a PCB design are factor in deciding the production cost. Bigger PCBs or those with complex layout typically need more material and take longer to produce which can result in higher expenses. When the design get more sophisticated or larger in size the resources and precision need for manufacturing also go up resulting in increased cost.
Number of Layers:
PCBs can be single sided, double sided and multilayered. The production of multilayer PCBs is more intricate involving steps, materials and time all contributing to a higher total cost.
Material Selection:
The selection of the base material could impact the cost of halogen free PCB. Superior materials that adhere to performance standard might come at a higher cost compared to basic materials.
Copper Weight:
The thickness of the copper layers on the PCB referred to as copper weight can affect the cost. Greater copper weights result in higher material expenses. Add complexity to manufacturing processes.
Surface Finish:
The type of surface finish used on the PCB can impact its price. Certain surface finish, like gold plating tend to be pricier than other. Could contribute to the total cost of the PCB.
Production Volume:
The amount of PCBs being manufactured can impact the price per unit. When production runs are larger it usually leads to low cost per unit as its economies of scale.
Lead Time:
Shorter the time needed for completion could lead to production methods but this might come with extra expenses. It’s beneficial to plan in advance and factor longer lead times to keep costs down.
Testing and Quality Control:
Implementing testing and strict quality control measure can increase the total expenses associated with halogen free PCB. To guarantee compliance with quality benchmarks and performance criteria it may be essential to conduct supplementary testing processes. This often entails A more thorough inspection process, which ultimately adds to the expense but is crucial for maintaining the integrity and reliability of the final product.
By taking these aspect into account and collaborating closely with JarnisTech. As a top PCB manufacturer we can enhance the design and manufacturing process to control expenses efficiently without compromising on the quality for halogen free PCBs.
How to Reduce the Cost of Halogen Free PCBs?
To lower the expenses of making halogen free PCBs various strategic methods can be applied. These approaches concentrate on optimizing the design selecting materials wisely and manufacturing processes to maintain cost effectiveness without sacrificing quality. By evaluating every production aspect substantial cost savings can be attained without jeopardizing the functionality or dependability of the halogen free PCBs.
Design Optimization:
Spending time and energy on optimizing the PCB design could result in reduce cost in the production phase. A well structured and efficient design can minimize material waste and streamline production, ultimately reducing manufacturing cost.
Layer Reduction:
To reduce manufacturing costs consider reducing the layers in a PCB layout. By simplifying the design, fewer layers translate to reduced complexity in production, which in turn makes the fabrication process more straightforward. It also reduces the need, for materials resulting in cost savings overall. This strategy streamlines manufacturing. Maintains cost effectiveness while preserving functionality.
Standard Shape Selection:
Choosing a standard shape for PCB design can significantly reduce manufacturing costs. Using shapes aligns better with existing production methods cutting down on the requirement, for custom tools or extra steps. This simplified method not eases the manufacturing process but also prevents additional costs linked to unique designs. By adhering to shapes manufacturers can ensure cost effectiveness and uniform production quality.
Bulk Ordering:
Placing orders for PCBs in quantities can frequently result in lower costs per unit. Ordering in bulk enables cost savings through economies of scale resulting in decreased manufacturing expenses, per PCB. By combining orders into quantities it is possible to reduce overall costs.
Applications of Halogen Free PCBs
Aerospace and Defense:
Halogen free PCBs are used in aerospace and defense application. Such as satellites, missiles and radar devices. These boards need to meet safety regulations and endure harsh environmental situations.
Medical Electronics:
In medical electronics devices such as pacemakers, defibrillators and surgical equipment, the halogen free PCBs are essential. It is important that these PCB are biocompatible, dependable and compliant with safety standard.
Industrial Automation:
Halogen free printed circuit board are frequently utilized in industrial automation equipment. Such as logic controllers (PLCs) distributed control systems (DCSs) and robotics. These boards must be durable enough to endure challenging conditions and guarantee reliable performance.
Consumer Electronics:
Halogen free PCB play a role in popular devices. Like smartphones, tablets and laptops. These PCB are designed to be compact, lightweight and energy efficient.
Other applications of halogen free PCB, include automtive electronics, telecommunications equipment, renewable energy systems and power electronics. The rising need for devices is projected to boost the popularity of halogen free PCB in the industry.
Final Thoughts
The cost of halogen free PCBs is impacted by a variety of elements yet their advantages, such as lower fire risk improved electrical efficiency and environmental adherence make them a worthwhile purchase. They are utilized in industries underscoring their significance in contemporary electronic systems.
In summary halogen free PCB have benefits in terms of safety, performance and environmental compliance. While they may be more expensive than halogenated PCB the advantages they provide often justify the higher costs. As the demand for devices continues to grow the market for halogen free PCB is expected to increase, establishing them as a crucial component in the future of electronics production.