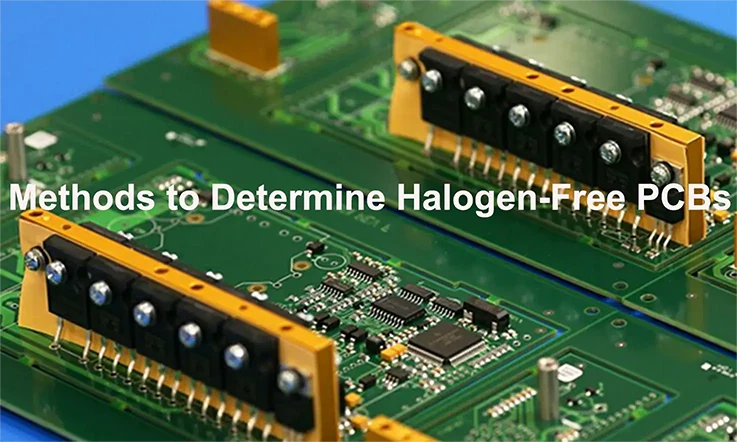
In the world of printed circuit board the move towards halogen free materials has become increasingly important. With concerns about the environmental and health effects of halogenated flame retardants there is a growing demand for halogen free PCB. Ensuring the reliability and compliance of these PCB require effective methods for their identification. This article explores the techniques and approaches used to analyze halogen free PCB providing valuable insights, into the advancement in this crucial area of PCB production.
Background on Halogen-Free PCBs
Halogen free circuit board, also known as Halogen free PCBs are designed without the use of flame retardants like polybrominated diphenyl ethers (PBDEs) or polychlorinated biphenyls (PCBs). These flame retardants were previously added to PCBs to reduce fire risks. However due to their effects on human health and the environment caused by bioaccumulation there has been a move, towards using halogen free PCB.
The significance of halogen free PCB has drawn considerable focus because of the growing recognition of the environmental and health risks tied to halogenated flame retardants. In light of these worries many nation and areas have put forth regulations to restrict or completely prohibit the use of these hazardous compounds in PCB. This move towards halogen free materials mirrors a worldwide dedication to lessening the consequences and possible health dangers associated with conventional halogenated material encouraging the embrace of safer and more eco friendly options in PCB production.
Various methodologies exist to ascertain the halogen free status of PCB. These method usually involve extracting halogens from the PCB material and then analyzing the extracted substances using techniques. Like ion chromatography or X-ray technology. Ion chromatography help in measuring the amount of halogens by separating and analyzing individual halogen ions while X-ray spectroscopy can detect halogens without damaging the material.
Switching to halogen frees PCB brings several benefits. Such as reducing environmental impact improving human health and safety and meeting regulatory requirements. Many PCB makers now offer halogen free options as a suitable alternative to traditional PCBs by using different flame retardants like phosphorus based or nitrogen based materials. The transition to halogen-free PCBs represents a pivotal stride towards diminishing the environmental and health repercussions associated with electronic waste.
Regulatory Requirements for Halogen-Free PCBs
The rules and regulations concerning halogen free printed circuit boards are always changing, as more countries and areas are placing limits on the use of halogenated flame retardants. Important guidelines for halogen free PCB include global standard like IEC61249-2-21 which specify that the highest acceptable levels of chlorine and bromine should not exceed 1500 ppm and for iodine it should be under 900 ppm in halogen free PCB.
Furthermore, the IPC-4101 standard outlines performance requirements and test methods for halogen-free and low-halogen printed boards, defining halogen-free PCBs as those containing less than 1500 ppm of chlorine and bromine, and less than 900 ppm of iodine. The EU RoHS Directive, a pivotal regulation in the European Union, restricts the use of hazardous substances in electrical and electronic equipment, including halogenated flame retardants, mandating that PCBs marketed in the EU contain less than 0.1% (1000 ppm) of bromine and chlorine.
Many countries have created their specific guidelines for halogen free PCBs in addition to the global and local regulations. For example Chinas compulsory standard (GB/T 29741 2013) sets restrictions on the halogen levels in PCBs with limits of 1500 ppm for chlorine and bromine and 900 ppm for iodine.
It is essential for PCB manufacturer and end-users to be well-informed about the regulatory requirement for halogen free PCB within their respective jurisdiction. Following these rule is crucial to guarantee that product meet safety standard and industry norms. It’s important to remember that the regulatory demand, for halogen free PCB can shift, emphasizing the need to keep informed about the most recent regulatory update to ensure compliance.
Methods for Determining Halogen Content in PCB
Method for analyzing halogen content in PCBs:
Ion Chromatography (IC):
Ion chromatography is a widely used analytical technique for determining the halogen content in PCB. This technique includes separating halogen ions as they move through a column and then accurately measuring them using a conductivity detector. IC is valued for its sensitivity and precision making it reliable approach for identifying and measuring particular halogens, like chlorine, bromine and fluorine in PCB sample.
X-ray Fluorescence (XRF) Spectroscopy:
X-ray fluorescence (XRF) spectroscopy is an used non destructive method for analyzing halogen levels in PCB. It works by exposing the sample to X-rays, which then produce distinct fluorescent X-rays based on the elements in the material. By studying these emitted X-rays XRF devices can precisely measure the amount of halogens. This technique is valued for its quickness ease of use and ability to assess samples without causing harm making it a dependable and effective choice for evaluating halogen content in PCB material.
Fourier Transform Infrared (FTIR) Spectroscopy:
FTIR spectroscopy proves to be a method for measuring the halogen levels in PCBs. Through examining how the sample absorbs radiation this approach allows for accurate detection and measurement of compounds containing halogens. With its capacity to provide in depth insights into the chemical composition of PCB materials, therefore FTIR spectroscopy emerges as a flexible and trustworthy method.
Combustion Ion Chromatography (CIC):
Combustion Ion Chromatography (CIC) is a method used to analyze the halogen levels in PCB samples. The procedure begins by burning the sample, which releases halogens as gases. These gases are then. Examined using ion chromatography allowing for accurate measurement of halogen content. This analytical method is important for ensuring that PCB material meet standard, by precisely determining their halogen levels.
Inductively Coupled Plasma Mass Spectrometry (ICP-MS):
Inductively Coupled Plasma Mass Spectrometry (ICP-MS) is an advanced analytical technique known for its high sensitivity and precision. This technique involves ionizing the sample material within a high temperature plasma source and then analyzing the generated ions using mass spectrometry. With its sensitivity in measuring trace amounts ICP-MS proves to be a valuable tool for evaluating halogen levels in PCB contributing essential information, for quality assurance and meeting environmental regulations effectively.
Therefore, these techniques provide choices for identifying the halogen levels in printed circuit boards allowing manufacturers to guarantee adherence to regulations concerning halogen free PCBs. The decision on the method to use could hinge on considerations. Like sensitivity, precision and sample size needs for the assessment.
Benefits of Using Halogen-Free PCBs
Utilizing halogen free PCBs offers a multitude of advantages:
● Environmental Impact Reduction
● Enhancement of Human Health and Safety
● Regulatory Compliance
● Enhanced Product Quality
● Cost Savings in Manufacturing
Ultimately, the adoption of halogen-free PCBs delivers a host of benefits, including environmental friendliness, improved human health and safety, regulatory compliance, enhanced product quality, and potential cost savings in manufacturing processes. As awareness of the adverse environmental and health impacts of halogenated flame retardants escalates, the demand for halogen-free PCBs is anticipated to rise. Manufacturers embracing halogen-free PCBs position themselves favorably to meet evolving customer preferences and adhere to forthcoming regulatory mandates.
Case Study
Analysis of Halogen-Free PCBs in Electronic Assemblies
A prominent electronics manufacturer sought to assess the halogen content of the printed circuit boards utilized in their product due to concern regarding the environmental and health implications of halogenated flame retardants. With a commitment to ensuring regulatory compliance, the manufacturer submitted sample of their PCBs to an accredited independent laboratory for analysis. Employing ion chromatography, the laboratory conducted comprehensive testing to determine the halogen content of the PCBs.
The analysis results showed that the tested PCBs had chlorine and bromine levels below 1500 ppm, well as iodine levels under 900 ppm. This confirms that the PCBs meet the requirements for halogen free PCBs set by industry standards. Like IEC61249-2-21 and IPC4101. This thorough analysis assured the manufacturer that their products adhere to the standard for halogen content in PCBs.
Validation of a Combustion-Ion Chromatography Method
A research lab wanted to confirm the accuracy of a combustion ion chromatography (CIC) technique, for measuring the halogen levels in printed circuit boards (PCBs). To validate the method the lab decided to use a certified reference material (CRM).
After preparing a set of Certified Reference Material (CRM) samples and analyzing them using the Combustion Ion Chromatography (CIC) method the lab managed to assess the precision and accuracy of this analytical approach. The results showed that the CIC method consistently produced halogen content measurements that were within 5% difference, from the certified values of the CRM samples. This consistent performance highlights the dependability and effectiveness of the CIC method in quantifying halogens in different materials.
Furthermore, the laboratory extended the application of the CIC method to analyze a diverse array of PCB samples. The findings from these tests showcased the methods reliability and accuracy in measuring halogen levels across concentrations in PCBs. This thorough validation not verified the precision of the CIC method but also illustrated its efficiency and flexibility in evaluating halogen content in PCBs with varying complexities. The successful use across samples reinforces the CIC method as a versatile and reliable tool, for analyzing halogens in PCB production and quality assurance.
Sum Up
The analysis of halogen-free PCBs plays a crucial role in promoting sustainability, ensuring product safety, and complying with regulatory standards. Manufacturers can use analytical approaches to accurately determine the halogen levels in PCBs and adhere to industry standards. As the PCB manufacturing sector progresses employing analytical methods to evaluate halogen free materials will be crucial, for fostering creativity improving standards and satisfying environmentally aware customers.