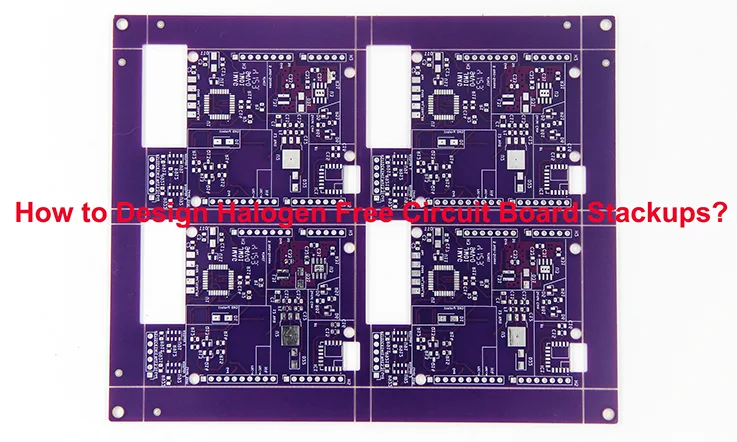
In the era of environmental awareness there is an increasing need for halogen free PCB because they are more environmentally friendly and pose fewer health risks than conventional halogenated PCB. Nevertheless creating halogen free PCB presents challenges. Such as sourcing suitable materials cost considerations and ensuring performance and reliability.
This article manual aims to equip you with the knowledge for designing halogen free circuit board stackups . We’ll delve into the intricacies and challenges with using halogen free materials along with outlining the necessary actions, for crafting a dependable and high performing PCB stackup. By grasping the intricacies and constraints of these materials you will be better equipped to create a robust and compliant halogen free PCB design that meets stringent industry standard.
Design Considerations for Halogen-Free Stackups
Initiating the design process for halogen-free PCB stackups requires careful consideration of several critical factors to achieve superior performance and consistent reliability. It is crucial to address these factors right from the beginning to create a strong and efficient PCB design. The following crucial aspects need assessment to steer the design process and adhere to the required technical and environmental criteria:
Material Selection:
When designing halogen free stackups it’s crucial to choose base materials, prepregs and laminates with care. Every layer in the stackup from the core, to the prepregs and surface finishes should be made using halogen free materials. This detailed process guarantees that the entire stackup meets standards while also preserving its intended performance and reliability features.
Stackup Architecture:
When designing halogen free PCB stackup with specific mechanical features it is essential to carefully consider factors. Such as layer count, thickness of individual layers and their arrangement in the stackup. Given that halogen free materials often exhibit dissimilar dielectric constants and thermal expansion coefficients compared to halogenated materials, these factors must be accounted for during stackup design.
Via Selection and Placement:
Optimal selection of via barrel material and via fill material is crucial to ensure adherence to halogen-free standards. Viable options for halogen-free via barrel materials encompass copper, nickel, and tungsten, while epoxy and conductive paste are among the suitable choices for halogen-free via fill materials.
Fabrication and Assembly:
Manufacturing and assembly halogen free PCBs require special focus. It’s crucial to use materials and methods that’re free of halogens for making laminates drilling, routing, plating, etching, soldering and assembly processes.
Additional Tips for Halogen-Free Stackup Design:
Use a Design for Manufacturability (DFM) tool to anticipate and resolve manufacturing challenges early in the design process. Work closely with your chosen PCB manufacturer to verify their expertise and capacity in producing halogen free PCBs effectively. Thoroughly examine your halogen free PCB stackups through testing to validate their alignment with desired electrical and mechanical performance criteria guaranteeing adherence, to industry norms and regulations.
How to Design Halogen Free Circuit Board Stackups?
Understand Halogen-Free Requirements: Make sure you understand the requirement and guidelines related to halogen free materials for your project. Important standard to keep in mind are IEC61249 -2-21 which details the criteria for using halogen material in printed circuit boards and IPC4101C which define the laminate and prepreg material for PCB.
Select Halogen Free Materials: Choose circuit board material that are specifically labeled as halogen free. These material usually comprise halogen free laminate and prepreg that are free of bromine or chlorine compounds. Seek out material that fulfill the electrical, thermal and mechanical characteristics for your specific use case.
Determine Layer Count: When determining the appropriate number of layers for your circuit board, it is important to carefully assess the complexity of the design and the specific functionality requirement. Consider aspect like signal integrity, power distribution and component density at this stage. Having a thought out layer count is key, to enhancing performance by ensuring proper signal routing, efficient power distribution and effective component placement.
Define Layer Stacking Sequence: Decide on the layer stacking sequence, which determines the arrangement of signal, power, and ground planes within the stackup. A typical stackup for a halogen free design may include signal layers, power planes, and ground planes in alternating layers.
Plan Power and Ground Plane Distribution: Distribute power and ground planes strategically throughout the stackup to minimize noise, provide solid return paths, and ensure proper power distribution. It’s advisable to have dedicated power and ground planes adjacent to signal layers to reduce electromagnetic interference (EMI) and maintain signal integrity.
Consider Impedance Control: If your design requires controlled impedance traces, incorporate appropriate dielectric materials and trace geometries to achieve the desired impedance values. This is crucial for high speed designs. Get advice from your PCB manufacturer on the practices for controlling impedance.
Define Copper Weight and Thickness: Determining the copper weight and thickness needed for each layer is crucial when designing PCB. The copper weight directly influences the current-carrying capacity of the traces, making it a critical factor in ensuring the electrical performance of the board. Moreover the thickness of the copper not influences the overall thickness of the PCB but also impacts its flexibility. It’s important to strike a balance, between these factor to ensure that the board has the right mechanical and electrical properties while still functioning properly in its final form.
Incorporate Solder Mask and Silkscreen Layers: Include solder mask layers to protect copper traces and pads from oxidation and facilitate soldering. Add silkscreen layers for component identification and assembly reference markings.
Define Board Thickness: Decide on the thickness of the board considering mechanical needs, like fitting into casings or meeting particular size limits. Make sure the selected thickness falls within what your PCB manufacturer can handle.
Verify Compliance: It’s really important to make sure that the materials and stackup design you choose completely meet the halogen requirements and industry standards set during the initial design stage. This process guarantees that every aspect of the design follows rules. If theres any doubt it’s an idea to talk to your PCB manufacturer or get guidance from a compliance specialist. Taking this care can prevent problems during production and guarantee that the end product meets all required environmental and performance standards.
Document the Stackup: Develop a detailed stackup documentation that outlines the sequence of layers types of materials used, thicknesses, copper weights and any other relevant factors. This documentation is essential, for maintaining consistency throughout the manufacturing and assembly processes.
Challenge and Limitations of Designing Halogen Free PCB Stack-up
Designing halogen-free circuit board stackups presents engineers with a range of challenges and constraints that require careful consideration. Overcoming these challenges demands an methodical strategy to guarantee the end design meets performance and dependability criteria while also complying with environmental and regulatory mandates. Effectively solve these intricacies is essential for achieving a halogen free PCB stackup that functions effectively in diverse situations.
Challenges:
Material Availability and Cost: It can be challenging to source materials for creating halogen free PCB compared to using halogenated ones making it tricky to find the right materials that meet specific requirements. Additionally halogen free materials typically come at a price than their halogenated possibly resulting in higher overall manufacturing cost for halogen free PCB. When selecting material it’s crucial to take these factor into account as they can impact both the costs and feasibility of designing and manufacturing PCB.
Performance and Reliability: Halogen free materials frequently display mechanical characteristics in contrast to their halogen containing equivalents impacting the PCBs overall effectiveness. Furthermore halogen free PCBs might exhibit reduced dependability under circumstances as halogenated materials generally deliver better safeguarding against environmental elements like moisture and heat. This difference, in performance underscores the importance of material choice and design deliberations when selecting halogen free options to guarantee the PCB complies with the necessary durability and operational criteria.
Overcoming the Challenges:
Despite the challenges involved it is feasible to design PCB stackups that’re free of halogen and still offer top notch performance and reliability. Through selection of materials and optimizing the stackup design engineers can tackle the constraints linked to halogen free materials.
Limitations:
Nevertheless it’s crucial to recognize that there are some challenges when creating halogen PCB stackups that cannot be completely resolved. For example halogen free materials might not offer the degree of safeguarding against moisture and heat as halogenated materials do. Therefore halogen free PCBs may not be ideal for application requiring high reliability or exposure, to severe environmental factors.
Which Types PCBs Board will Need Halogen Free Stack-ups?
Halogen free PCB configurations are often necessary, for a variety of printed circuit boards utilized across industries. Below are an instances of PCB varieties that frequently need halogen free stackups:
● Single-Sided PCBs
● Double-Sided PCBs
● Multilayer PCBs
● High-Speed PCBs
● RF/Microwave PCBs
● Flexible PCBs
● High-Density Interconnect (HDI) PCBs
Final Thoughts
Designing circuit board stackups without halogen is a part of modern PCB design in line with the increasing focus on environmental sustainability. By choosing halogen free materials optimizing the stackup structure and considering manufacturing and assembly processes engineers can develop PCBs that are both high performing and eco friendly. Embracing halogen free design methods not only minimizes the potential hazards associated with halogens but also supports a more environmentally friendly future. Lets aim for halogen circuit board stackups to lead the way, towards a cleaner and safer electronics industry.