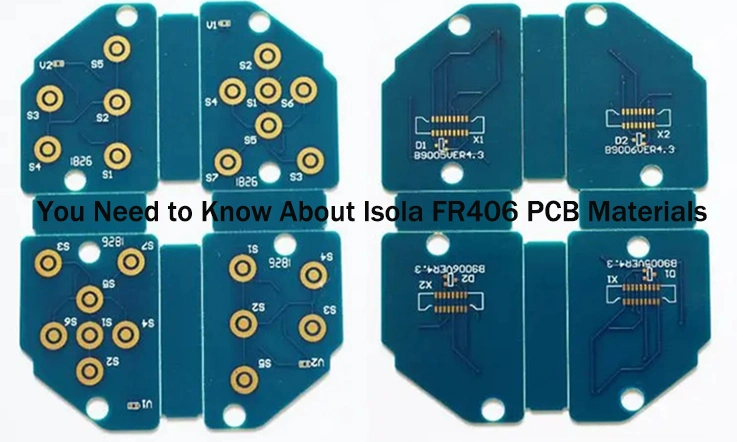
Isola FR406 is a high-performance PCB material widely used in various industries due to its exceptional properties and reliability. This article provides an in-depth exploration of the characteristics and applications of Isola FR406, highlighting its significance in the field of printed circuit board manufacturing.
Definition of Isola FR406 PCB Material
Isola FR406 PCB material refers to a type of high-performance laminate used in the manufacturing of printed circuit boards (PCBs). It is a composite material composed of a fiberglass-reinforced epoxy resin substrate. The FR406 material offers excellent electrical properties, such as low dielectric constant and loss, making it suitable for high-frequency applications. It also exhibits good dimensional stability, heat resistance, and mechanical strength. Overall, Isola FR406 is a popular choice for demanding electronic applications that require high-speed signal transmission and reliability.
Properties Does Isola FR406
Isola FR406 PCB material offers outstanding properties that significantly contribute to its high-performance characteristics.
High Glass Transition Temperature (Tg):
One notable attribute is its high glass transition temperature (Tg), which reaches 170 degrees Celsius. This feature makes Isola FR406 an ideal choice for demanding applications where thermal performance is crucial. The elevated Tg greatly enhances the material’s ability to withstand high temperatures during PCB fabrication and operation.
Low Z-axis Coefficient:
Another key advantage of Isola FR406 is its low Z-axis coefficient of thermal expansion (CTE). Before reaching the glass transition temperature, the Z-axis CTE is merely 60ppm/ºC, while it increases to 250ppm/ºC after the transition. This low CTE value indicates that Isola FR406 exhibits minimal expansion or contraction when exposed to temperature variations, ensuring excellent dimensional stability.
Low and Stable Dielectric Constant:
Isola FR406 also boasts a low and stable dielectric constant of 3.93. This electrical property is particularly advantageous for high-frequency applications, as it allows for efficient signal transmission and reduced power loss. The material’s low dielectric constant enhances its suitability for various electronic applications where signal integrity and minimal energy loss are paramount.
High Thermal Stability:
With a decomposition temperature of 300 degrees Celsius, Isola FR406 demonstrates high thermal stability. It will only undergo chemical decomposition when operating above this temperature threshold. The material’s ability to withstand such high temperatures ensures its reliability and longevity in demanding environments.
Mechanical Integrity:
To further enhance its mechanical properties, Isola FR406 incorporates square weave E-glass reinforcement. This reinforcement technique involves the use of electronic glass fiber cloth, which provides added strength and durability to the material. The square weave pattern enhances the overall mechanical integrity of Isola FR406, making it highly resistant to mechanical stresses and ensuring the reliability of the PCB.
Overall, Isola FR406 PCB material offers exceptional properties that make it a preferred choice for high-performance applications. Its high glass transition temperature, low Z-axis CTE, low and stable dielectric constant, high decomposition temperature, and square weave E-glass reinforcement collectively contribute to its outstanding performance and reliability in demanding electronic designs.
What Is the Difference Between Isola-FR406 vs 370HR?
Isola FR406 and Isola 370HR are both popular PCB materials known for their high performance and reliability. While they share some similarities, there are key differences between them.
1. Glass Transition Temperature (Tg):
●Isola FR406: The Tg of Isola FR406 is 170 degrees Celsius, indicating its ability to withstand high temperatures during fabrication and operation.
●Isola 370HR: The Tg of Isola 370HR is 180 degrees Celsius, offering a slightly higher temperature tolerance compared to FR406.
2. Coefficient of Thermal Expansion (CTE):
●Isola FR406: The Z-axis CTE of Isola FR406 is 60ppm/ºC before the glass transition temperature, increasing to 250ppm/ºC after the transition. This low CTE ensures excellent dimensional stability under temperature variations.
●Isola 370HR: The Z-axis CTE of Isola 370HR is 55ppm/ºC before the glass transition temperature, increasing to 200ppm/ºC after the transition. It also demonstrates low CTE, similar to FR406.
3. Dielectric Constant:
●Isola FR406: The dielectric constant of Isola FR406 is 3.93, indicating low electrical energy loss and suitability for high-frequency applications.
●Isola 370HR: The dielectric constant of Isola 370HR is 4.04, slightly higher than FR406 but still within a range suitable for high-frequency applications.
4. Decomposition Temperature:
●Isola FR406: The decomposition temperature of Isola FR406 is 300 degrees Celsius, beyond which it chemically decomposes.
●Isola 370HR: The decomposition temperature of Isola 370HR is also 300 degrees Celsius, demonstrating similar thermal stability to FR406.
5. Reinforcement:
●Isola FR406: FR406 utilizes square weave E-glass reinforcement, which enhances its mechanical properties and overall strength.
●Isola 370HR: 370HR incorporates a traditional glass fabric reinforcement, providing mechanical strength and stability to the material.
It’s important to note that the specific requirements of a PCB design and application will dictate the choice between Isola FR406 and Isola 370HR. Both materials have their strengths and are widely used in various industries, including telecommunications, aerospace, and automotive. Consulting with a PCB designer or manufacturer can help determine the most suitable material for a particular project based on its specific needs and performance requirements.
Effects of Heat Rate and Pressure on Isola FR406 Lamination
The heat rate and pressure during the lamination process have significant effects on the properties and performance of Isola FR406 PCB material. Here are the key considerations:
1. Heat Rate:
●Heating Too Slowly: If the heat rate is too slow during lamination, it can result in inadequate resin flow and incomplete bonding between the layers. This can lead to delamination issues and reduced mechanical strength.
●Heating Too Rapidly: Excessive heat rate can cause excessive resin flow and create voids or resin-rich areas within the laminate. This can negatively impact the electrical and mechanical properties of the PCB.
2. Pressure:
●Insufficient Pressure: Insufficient pressure during lamination can lead to poor bonding between the layers, resulting in weak interlayer adhesion and reduced overall strength. It may also result in voids or air pockets between the layers, compromising the electrical and thermal performance.
●Excessive Pressure: Applying excessive pressure can cause excessive resin squeeze-out and result in thin resin-rich areas. This can lead to resin starvation in other areas, affecting the uniformity of the laminate and potentially causing issues such as resin-starved vias.
Optimizing the heat rate and pressure during lamination is crucial to ensure the desired properties and performance of Isola FR406. It is recommended to follow the manufacturer’s guidelines and specifications for the specific material and laminate stack-up being used. The ideal heat rate and pressure can vary depending on factors such as the thickness of the laminate, the number of copper layers, and the specific lamination equipment being utilized.
By carefully controlling the heat rate and pressure, it is possible to achieve a well-bonded, void-free laminate with optimal electrical, mechanical, and thermal properties. This ensures the reliability and performance of the Isola FR406 PCB material in various applications.
Significance of Relative Thermal Index for Isola FR406
The Relative Thermal Index (RTI) is a crucial parameter that provides valuable information about the long-term thermal performance and reliability of Isola FR406 PCB material. The RTI is defined as the maximum continuous operating temperature at which the material can perform reliably over an extended period without significant degradation.
The significance of the RTI for Isola FR406 lies in its ability to determine the maximum temperature at which the material can be safely operated without compromising its electrical, mechanical, and thermal properties. Here are some key points highlighting the significance of the RTI:
1.Reliability Assessment:
The RTI serves as a key parameter for evaluating the long-term reliability of Isola FR406. It provides an indication of the material’s ability to withstand elevated temperatures consistently without experiencing degradation, such as resin decomposition or loss of mechanical strength.
2.Design Considerations:
The RTI helps PCB designers determine the operational limits of Isola FR406 in terms of temperature. It enables them to make informed decisions regarding the thermal management of the circuit board, ensuring that the material is not subjected to temperatures beyond its specified capabilities.
3.Safety and Compliance:
Compliance with safety standards and regulations is essential in many industries. The RTI helps demonstrate the suitability of Isola FR406 for specific applications, ensuring that the material meets the required performance criteria and safety standards under the expected operating conditions.
4.Material Selection:
The RTI provides a basis for comparing and selecting different PCB materials for specific applications. By considering the RTI values, designers can assess the thermal robustness of Isola FR406 compared to other materials and make an informed choice based on the desired operating temperature range.
5.Lifetime Performance:
The RTI gives an indication of the material’s ability to maintain its performance and reliability over an extended period. By operating within the specified RTI limits, the risk of premature failure due to thermal stress is minimized, ensuring a longer lifetime for the PCB and the overall electronic system.
Why is Manufacturing PCBs with Isola FR406 So Expensive?
There are several reasons why manufacturing PCBs with Isola FR406 can be expensive:
Material Cost: Isola FR406 is a high-performance material with excellent electrical properties, high thermal resistance, and low dielectric constant. It is specifically designed for high-frequency applications. The cost of this material is generally higher compared to standard FR-4 materials used in PCB manufacturing.
Manufacturing Complexity: Isola FR406 material requires specialized manufacturing processes and equipment to handle its unique properties. This can increase the overall manufacturing cost as it requires skilled labor and advanced equipment.
Quality Control: Isola FR406 material has strict quality control requirements to ensure consistent performance and reliability. This involves rigorous testing and inspection processes during the manufacturing process, which can add to the overall cost.
Limited Availability: Isola FR406 is not as widely available as standard FR-4 materials. The limited availability can result in higher material costs due to lower economies of scale.
Certification and Compliance: Isola FR406 material may require specific certifications and compliance with industry standards. Meeting these requirements can add additional costs to the manufacturing process.
Overall, the combination of material cost, manufacturing complexity, quality control, limited availability, and certification requirements contribute to the higher cost of manufacturing PCBs with Isola FR406.
Isola-FR406 Applications for PCB Board
Isola FR406, renowned for its high-performance characteristics, finds extensive application in various sectors and markets, including:
Medical, Industries, and Instrumentation:
The exceptional properties of Isola FR406 make it well-suited for medical devices, industrial equipment, and instrumentation. Its high glass transition temperature, low CTE, and stable dielectric constant ensure reliable performance in demanding environments.
Consumer Electronics:
Isola FR406 is a preferred choice for consumer electronics due to its ability to handle high temperatures and provide excellent thermal performance. It is utilized in devices such as smartphones, tablets, laptops, and other consumer electronic products.
Storage and Computing:
The reliability and thermal stability of Isola FR406 make it suitable for storage and computing applications. It offers robust performance in data centers, servers, high-speed storage systems, and other computing equipment.
Aviation and Military:
Isola FR406 is extensively used in the aviation and military sectors, where ruggedness, durability, and high temperature resistance are critical requirements. It is deployed in aircraft electronics, missile systems, radar equipment, and other defense applications.
RF and Microwave:
Isola FR406’s low dielectric constant and high-frequency performance make it an excellentchoice for RF (Radio Frequency) and microwave applications. Its stable electrical properties enable efficient signal transmission and reduced power loss, making it indispensable in wireless communication systems, satellite technology, and microwave components.
Telecommunications:
Isola FR406 is highly suitable for telecommunications infrastructure, including base stations, network equipment, and high-speed data transmission systems. Its low dielectric constant and reliable thermal performance contribute to optimal signal integrity and overall system efficiency.
Transportation and Automotive:
Isola FR406’s robustness and high-temperature tolerance make it an ideal material for transportation and automotive applications. It is used in onboard electronic systems, automotive control units, advanced driver-assistance systems (ADAS), and other critical automotive components.
In Conclusion
Isola FR406 PCB material stands as a versatile and dependable choice for high-performance applications across various industries. Its exceptional properties, including high glass transition temperature, low CTE, stable dielectric constant, and mechanical reinforcement, make it a preferred material for demanding electronic designs.