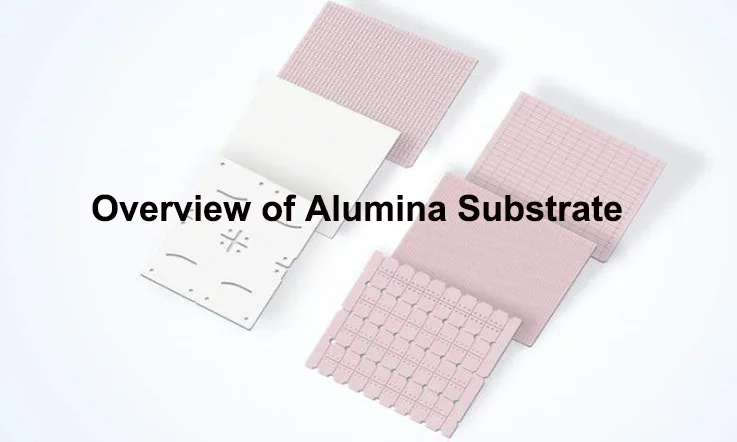
Alumina substrates, with their exceptional properties and versatility, play a crucial role in various industries and technologies. These substrates, made from high-quality alumina powder, provide a reliable platform for applications requiring thermal management, electrical insulation, and mechanical stability. From power electronics to LED packaging, automotive systems to aerospace and defense, alumina substrates have become a cornerstone of advanced technologies. This article delves into the applications, manufacturing processes, and benefits of alumina substrates, highlighting their indispensable role in shaping the future of numerous industries.
What Is Alumina Substrate?
Alumina substrate refers to a type of substrate material that is made primarily from aluminum oxide (Al2O3). It is commonly used in various electronic and semiconductor applications, including integrated circuits, circuit boards, sensors, and high-power devices.
The term “substrate” refers to a solid material on which other components or materials are deposited or attached. In the context of electronics, the substrate serves as the foundation or base on which electronic components are mounted, and it provides electrical insulation and mechanical support.
Alumina substrate is favored for its excellent electrical insulation properties, high thermal conductivity, and good mechanical strength. It has a high dielectric constant, which allows for efficient signal transmission and reduces signal loss. Alumina also has good chemical resistance, making it suitable for use in harsh environments.
Manufacturing Alumina Substrates: Production Stages
The production of alumina substrate involves a series of robust and high-quality manufacturing processes. These steps ensure the production of reliable and high-performance substrates. The key steps involved in alumina substrate manufacturing are as follows:
1. Raw Material Selection:
The initial step in the manufacturing process is the careful selection of raw materials. The focus is primarily on the particle size distribution of the alumina powder and its purity. High-quality alumina powder, such as aluminum oxide powder or aluminum hydroxide, is chosen to ensure the desired consistency and composition of the substrate. Accurate mixing and blending of the raw materials are essential to maintain the quality of the final product.
2. Powder Preparation:
The selected raw materials undergo various preparation methods to control the purity, size, and shape of the powder. This can involve processes such as washing, grinding, filtering, and mixing. The powder preparation step ensures that the alumina powder meets the required specifications for the substrate manufacturing process.
3. Forming Methods:
In this stage, the prepared powder is formed into green sheets, which will later be shaped into the desired substrate. Techniques such as extrusion and tape casting are commonly used to form the green sheets. The green sheets are then cut into the desired size and shape. Molding processes like compression molding, injection molding, and extrusion molding are employed to shape the green sheets into the desired substrate form.
4. Sintering Process:
The sintering process, also known as the firing process, is a crucial step in alumina substrate production. It involves subjecting the molded substrate to high temperatures to achieve densification. The sintering process fuses the alumina particles together, resulting in a substrate with the desired reliability. This process ensures the formation of a dense footprint, crystal structure, optimal density, and the required mechanical strength. The sintering process also enhances the electrical properties of the substrate, ensuring its high performance.
By following these manufacturing steps, alumina substrate production achieves the desired reliability, mechanical strength, electrical properties, and overall quality. These substrates find extensive applications in various industries where their thermal conductivity, electrical insulation, and chemical resistance are essential.
Properties of Alumina Ceramic Substrates
Alumina ceramic substrates, also known as alumina ceramic boards or plates, possess several key properties that make them suitable for various applications. Some of the notable properties of alumina ceramic substrates include:
1.High thermal conductivity:
Alumina ceramic substrates have excellent thermal conductivity, allowing for efficient heat dissipation. This property is crucial in electronic devices where heat management is critical to maintain optimal performance and prevent overheating.
2.Electrical insulation:
Alumina ceramic substrates offer excellent electrical insulation properties, making them ideal for applications where electrical isolation is required. They have a high dielectric strength, enabling efficient signal transmission and reducing the risk of electrical short circuits.
3.Mechanical strength and stiffness:
Alumina ceramic substrates exhibit high mechanical strength and stiffness, providing excellent structural support. They are resistant to mechanical stress, vibration, and thermal shocks, making them suitable for demanding applications that require mechanical stability.
4.Chemical resistance:
Alumina ceramic substrates have good chemical resistance, making them resistant to corrosion and degradation caused by exposure to various chemicals and harsh environments. This property enables their use in applications where chemical compatibility is essential.
5.Low thermal expansion:
Alumina ceramic substrates have a low coefficient of thermal expansion. This means they expand and contract minimally with temperature changes, reducing the risk of thermal stress and cracking. It allows for better dimensional stability and reliability of the substrate.
6.High operating temperature:
Alumina ceramic substrates can withstand high temperatures, typically up to 1600°C (2912°F) depending on the specific grade. This high-temperature tolerance makes them suitable for use in high-temperature environments and applications that involve elevated temperatures.
7.Smooth and flat surface:
Alumina ceramic substrates are manufactured with smooth and flat surfaces, ensuring ease of mounting and attachment of electronic components. The surface quality facilitates good adhesion of conductive materials and promotes reliable electrical connections.
How Many Types of Alumina Substrates?
There are several types of alumina substrates available, each with its own specific characteristics and applications. The types of alumina substrates can be broadly categorized based on their composition, purity level, and manufacturing processes. Some common types of alumina substrates include:
1.High-purity alumina (HPA):
High-purity alumina substrates are made from aluminum oxide with a purity level of 99.99% or higher. They are known for their exceptional electrical insulation properties, high thermal conductivity, and excellent mechanical strength. HPA substrates are commonly used in high-power and high-frequency electronic devices, as well as in applications requiring high reliability and precision.
2.Low-temperature co-fired ceramics (LTCC):
LTCC alumina substrates are fabricated using a co-firing process at relatively low temperatures. They are designed to have a multilayer structure, with electrical traces and vias embedded within the substrate. LTCC substrates are widely used in microelectronics and microwave applications, offering a combination of excellent electrical performance, high density, and design flexibility.
3.Thick film alumina substrates:
Thick film alumina substrates are manufactured by screen printing a layer of alumina paste onto a supporting material, such as a metal or ceramic plate. They are cost-effective and provide good electrical insulation and thermal conductivity. Thick film alumina substrates are commonly employed in hybrid integrated circuits (HICs), sensors, and other electronic applications.
4.Thin film alumina substrates:
Thin film alumina substrates involve depositing a thin layer of alumina onto a supporting substrate, typically through techniques such as sputtering or chemical vapor deposition. These substrates offer excellent electrical insulation, high thermal conductivity, and compatibility with thin film processing techniques. Thin film alumina substrates are commonly used in microelectronics, MEMS (Micro-Electro-Mechanical Systems), and semiconductor devices.
5.Polycrystalline alumina substrates:
Polycrystalline alumina substrates are made from sintered alumina powder. They exhibit good electrical insulation and thermal conductivity properties, along with high mechanical strength. Polycrystalline alumina substrates are widely employed in power electronics, LED packaging, and high-temperature applications.
Advantages of Alumina Substrate PCBs
Alumina substrate PCBs (Printed Circuit Boards) offer several advantages over traditional PCB materials like FR4 (fiberglass-reinforced epoxy). Some of the key advantages of alumina substrate PCBs include:
●High thermal conductivity
●Excellent electrical insulation
●Mechanical strength and stability
●Chemical resistance
●High operating temperature
●Dimensional stability
●Compatibility with thin film processing
●Design flexibility
●Cost-effective
These advantages make alumina substrate PCBs a preferred choice in various industries, including power electronics, LED lighting, automotive, aerospace, and telecommunications, where high reliability, thermal management, and electrical insulation are critical.
Applications of Alumina Substrates
Alumina substrates find applications in a wide range of industries and technologies due to their excellent properties. Some common applications of alumina substrates include:
●Power electronics
●LED packaging
●High-frequency applications
●Automotive electronics
●Aerospace and defense
●Medical devices
●MEMS (Micro-Electro-Mechanical Systems)
●Sensor technology
●Ceramic heaters
●Printed Circuit Board
The versatility and beneficial properties of alumina make it a preferred choice in many industries where thermal management, electrical insulation, reliability, and durability are essential.
Summary
Alumina substrates have emerged as essential components in the advancement of various industries and technologies. Their impressive thermal conductivity, electrical insulation, and mechanical strength make them ideal for applications ranging from power electronics to aerospace systems. The rigorous manufacturing processes ensure the production of high-quality substrates, meeting the stringent demands of modern technologies.
As we embark on a future driven by innovation, alumina substrates will continue to be at the forefront, enabling progress and pushing the boundaries of what is possible. With their reliability, durability, and exceptional performance, alumina substrates truly serve as a cornerstone of advanced technologies.
Our services
Ceramic PCB Manufacturing & Assembly