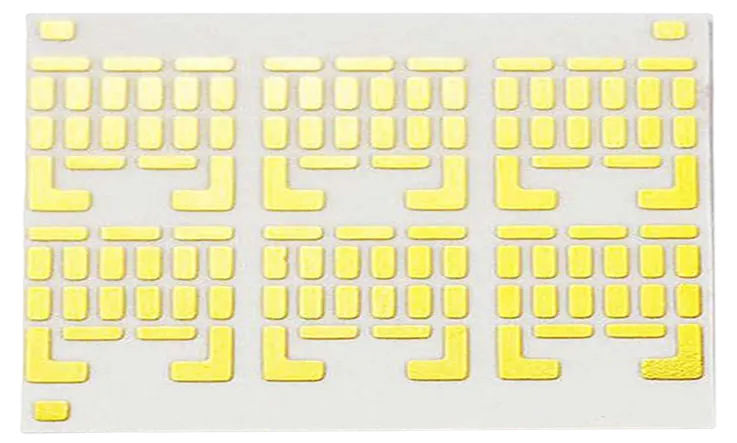
Silicon Carbide Ceramic PCBs represent a cutting edge technology with benefits for high temperature and high power uses. Unlike Printed Circuit Boards (PCBs) these boards are crafted from ceramic materials granting them exceptional heat resistance, chemical durability and robustness, against mechanical strains.
Lets explore the characteristics and benefits of Silicon Carbide Ceramic PCBs in this piece. We’ll delve into their production methods design factors to consider and where they are commonly used.
What Exactly Is Silicon Carbide Ceramic PCB?
Silicon Carbide (SiC) is a relatively new semiconductor material. It provide an alternative to traditional semiconductor material such as silicon due to its high breakdown field, exceptional thermal conductivity and impressive saturation velocity. SiC remarkable electrical and physical feature have demonstrated its potential as a material in the semiconductor industry.
A Silicon Carbide Ceramic PCB is a circuit board that uses material containing a high amount of silicon carbide. Because of its mix of feature, like excellent thermal conductivity, high strength and effective electrical insulation this type of PCB is becoming more popular.
Special care is required to ensure the integrity of the circuits, as the manufacturing process and design considerations for silicon carbide ceramic PCB differ from traditional PCBs. They also offer improved reliability and reduced size and weight Ideal for use in high temperature and high power applications. Such as power electronics, automotive, aerospace and defense, silicon carbide ceramic PCB provide advantage compared to traditional circuit boards made of fiberglass or other materials.
Manufacturing Process of Silicon Carbide Ceramic PCBs
The manufacturing process of Silicon Carbide Ceramic PCBs typically involves the following steps:
Preparation and Forming
Starting off we mix silicon powder with various ceramic components and additives to make a uniform slurry. Afterward this slurry undergoes drying to create a powder that can be pressed or molded. The dried silicon carbide powder is then shaped into forms using methods like uniaxial pressing, isostatic pressing or slip casting. This process transforms the materials into the needed shapes, for the ceramic circuit boards.
Sintering and Machining
The formed parts are put in a furnace with temperatures, where binders are removed and the powders are compacted and fused. After the sintering process the ceramic components undergo shaping using tools such, as laser cutters or diamond drills. This stage includes forming the required features and circuitry to create the proper shape and design of the circuit board.
Metallization and Finishing
Metallic layers are applied to areas of the ceramic board using technologies like sputtering or plating. This process establishes the electrical connections needed for circuit boards. Following this insulation layers, typically crafted from materials such as alumina or glass are added over the metalized layers to ensure electrical insulation. Subsequently the ceramic PCB boards undergo a series of processes including polishing, cleaning and testing, to guarantee they comply with all standards for functionality, dependability and integrity.
Design Considerations for Silicon Carbide Ceramic PCBs
Designing a Silicon Carbide Ceramic PCB involves considerations compared to traditional PCB and demand careful attention. Below are factors to consider when designing a Silicon Carbide Ceramic PCB:
● Thermal Management: Silicon Carbide Ceramic PCBs, with thermal conductivity demand careful thermal management. It’s essential to cool the PCB possibly using heat sinks, thermal pads or thermal vias to enhance heat dissipation efficiency.
● Mechanical Strength: The durability of PCB need very careful handling and secure installation to prevent any structural harm. It is crucial not to subject the PCB to mechanical stresses during assembly.
● Insulation and Dielectric Properties: The exceptional insulating characteristics of Silicon Carbide Ceramic PCB necessitate a thorough evaluation of the insulation and dielectric attributes of the PCB materials employed. Designers must meticulously manage the spacing between the traces and cutouts, on the board to prevent any electrical malfunctions.
● Manufacturing Constraints: Manufacturers must consider the machining and manufacturing methods required for Silicon Carbide Ceramic PCBs to guarantee that the chosen fabrication processes can produce the final design. This often includes, implementing design for manufacturability (DFM) strategies and creating production prototypes.
● Connector Compatibility: Choosing the connectors for Silicon Carbide Ceramic PCB is crucial particularly, in situations where the circuit board may face extreme temperatures or intense vibrations that could affect the stability of the connections.
Applications of Silicon Carbide Ceramic PCBs
Silicon Carbide Ceramic PCBs offer a set of features and benefit that make them well suited for various high temperature and high power uses. Below are a few application where Silicon Carbide Ceramic PCBs are commonly utilized:
● Power Electronics
● Automotive
● Aerospace and Defense
● Medical Devices
● Industrial Applications
Understanding of Silicon Carbide
Silicon carbide (SiC) is a type of semiconductor made up of silicon (Si) and carbon (C). The bond in SiC is very strong making it stable in terms of heat, strength and chemical properties. SiC exists in crystal structures known as polytypes each with its own unique physical properties. Among these the 4H SiC polytype is widely acknowledged as the choice for applications, in power electronics.
Silicon Carbide Ceramics Structure
Silicon Carbide exhibits a variety of crystal structures boasting a collection of more than 250 distinct types. A notable feature of SiC is its nature as it encompasses a diverse array of crystal structures known as polymorphs that bear resemblances to each other. While these polymorphs vary in three dimensions they maintain similarities in two dimensions, within a layered system hierarchy.
SiC Material Properties
Silicon Carbide (SiC) is a semiconductor that boasts a bandgap range wider than that of Silicon (3.26 eV vs. 1.12 eV). SiC possesses a host of favorable properties critical for power electronics applications.
SiC has a strength that is ten times higher than Silicon making it a reliable choice for high voltage applications. It allows for voltage support with devices placed closer together due to its powerful dielectric properties. The reduced distance between drains and channel contact in devices results, in lower electrical resistance and decreased power losses.
SiCs wider bandgap leads to free electrons and lower leakage current, which reduces thermal carrier generation. Moreover SiC devices demonstrate more consistent leakage currents across various temperatures compared to conventional Si devices. These characteristics make SiC MOSFETs and diodes preferable for high temperature uses.
SiC exhibits superior thermal conductivity, three times greater than Silicon, promoting better heat dissipation. It enables lower operating temperatures and less stress on switches, which are crucial elements of power electronic device design.
Moreover, SiC offers twice the electron saturation speed of Silicon, enabling higher switching speeds that result in reduced switching losses. Higher pulse-width-modulation (PWM) frequencies with certain power conversion topologies can result in smaller, lighter, and more affordable passive elements. Passive elements are often the most substantial and costliest elements of the system.
Manufacturing SiC wafers poses challenges compared to producing Si wafers. To create SiC boules, a chemical deposition process within a vacuum chamber is employed, unlike the melting method used for silicon. This meticulous process is both time consuming and demanding to execute. The cutting of wafers, from these boules, which are made of a tough and fragile material often utilized in industrial cutting application necessitates specialized techniques.
Silicon Carbide Advantages
In 2011 Cree brought Silicon Carbide to the market. This material has a field strength ten times higher than that of Silicon. As a result it needs material to handle high temperatures leading to significantly lower ON resistance. SiC also shows consistent ON resistance stability across a wide temperature range compared to Silicon with only a 1/10th change from 25C to 150C. Additionally SiC has better thermal conductivity, than both Silicon and GaN.
Silicon Carbide Ceramics Applications
Prior to the discovery of boron carbide in 1929, silicon carbide was recognized as the most robust synthetic material available. It boasts a hardness rating of 9 putting it on par with diamonds when it comes to toughness. Moreover SiC crystals showcase fracture characteristics that make them extremely efficient in applications, like grinding wheels, abrasive fabric and paper goods.
SiC stands out for its ability to conduct heat, strong resistance to high temperatures, minimal expansion when heated and durability against chemical reactions and sudden changes in temperature. These feature make SiC become a valuable material for producing high temperature bricks and other refractory item.
Additionally SiC ceramic can act as a semiconductor. Has electrical conductivity comparable to both insulating and metallic materials. Coupled with its thermal characteristics this quality makes SiC a prime candidate for replacing conventional semiconductors like silicon, in high temperature settings.
Final Thoughts
Your Silicon Carbide Ceramics PCB Supplier
Silicon Carbide Ceramic PCBs provide a set of feature and benefit that make them well suited for applications requiring high temperatures and power. They possess thermal conductivity, durability, robustness, resistance to damage, high power capacity and outstanding electrical insulation qualities. These attributes make them a top pick for industries, include power electronics, aerospace, automotive and defense.
Creating Silicon Carbide Ceramic PCBs involves an intricate and specific manufacturing process compared to standard PCBs. Designers must pay attention to factors like thermal regulation, mechanical durability, insulation and dielectric characteristics production limitations and compatibility, with connectors.
JarnisTech is a leading producer of top notch silicon carbide items that find extensive applications in diverse sectors. We are delighted to provide advice on selecting materials, designing and potential uses. If you need information don’t hesitate to get in touch with us. Should you have any queries. Need clarification, on SiC or other ceramic materials not mentioned on our site feel free to reach out to us. Our team is here round the clock to offer you prompt help and assistance.
Related Posts:
●Overview of Alumina Substrate
●How Layout a Multilayer Ceramic PCB Stack-ups?
●How to Design a Ceramic Circuit Board?
●Leading Global 12 Ceramic PCB Manufacturers
●Manufacturing Standards for Ceramic PCB Production
●What is Ceramic Packages and Its Types?
PCB Fabrication
Ceramic PCB Manufacturing & Assembly