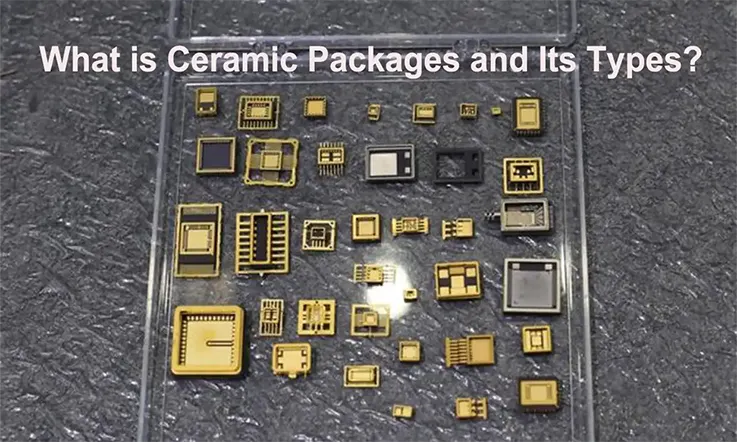
This article offers a look into ceramic packages delving into their various types and uses. By grasping the features and advantages of each type engineers and manufacturers can make well informed choices to guarantee top notch performance and dependability of electronic gadgets. These packages are crafted to shield components from factors and establish electrical links to the printed circuit board serving as crucial elements in the realm of electronics by ensuring a secure housing for sensitive electronic parts.
Importance of Ceramic Packages in Electronics
Ceramic packages are crucial in the realm of electronics due to their role, in guaranteeing the dependability, efficiency and durability of electronic device. Here are the primary factors highlighting the significance of ceramic packages in the electronics sector.
Thermal management
Ceramic packages have heat conductivity allowing electronic components to dissipate heat efficiently. It is essential to manage heat to avoid overheating as this can result in reduced performance, early malfunction or severe harm, to electronic devices. By ensuring the operating temperatures ceramic packages improve the durability and lifespan of electronic systems.
Electrical insulation
Ensuring the integrity of electrical signals and avoiding malfunctions or damage caused by unintended electrical connections, ceramic packages provide a protective barrier. In addtion, preventing electrical interference and short circuits between components, ceramic materials have excellent electrical insulation properties.
Mechanical stability
Particularly important in applications subjected to harsh environments, include automotive, aerospace, and industrial settings, where electronic devices may be exposed to extreme temperatures, pressure, or physical impacts, ceramic packages offer high mechanical strength and rigidity. Enabling them to withstand mechanical stresses, vibrations, and shocks, this resilience is a key advantage of ceramic packages.
Chemical resistance
Ceramic packages exhibit chemical inertness, making them highly resistant to corrosion, moisture and many chemical substances.This resistance is crucial in settings where electronic device might be exposed to chemicals or sterilization procedures like in medical or industrial settings. By using ceramic packages electronic component can maintain stability and functionality over the long term in demanding environment.
RF/microwave performance
Facilitating the development of advanced communication systems, wireless technologies, and radar systems, ceramic packages have low dielectric loss and high-frequency capabilities. Enabling the reliable transmission and reception of high-frequency signals, these properties make ceramic packages well-suited for RF/microwave applications.
Miniaturization
Ceramic packages can be manufactured in compact sizes with high precision, allowing for the miniaturization of electronic devices. With electronic parts getting tinier and more merged ceramic packages offer the needed packaging solution to adapt to the reduced sizes while upholding efficiency and dependability.
Compatibility with semiconductor materials
Ensuring the integrity of electronic components during temperature variations, ceramic substrates have a close thermal expansion coefficient match with semiconductor materials such as silicon. Reducing the risk of stress-induced failures caused by thermal cycling, this compatibility is a significant advantage of ceramic substrates.
Definition of Ceramic Packages
Ceramic packages are a type of packaging used in electronic components to protect, uphold and establish electrical connections for semiconductor devices. These packages are crafted from materials like alumina or aluminum nitride, known for their exceptional thermal conductivity top notch electrical insulation and reliable performance. Renowned for their heat dissipation capabilities ceramic packages are favored for demanding applications requiring effective thermal control. They come in variations such, as Ceramic Dual In Line Packages (CDIP) Ceramic Quad Flat Packs (CQFP) Ceramic Ball Grid Arrays (CBGA) tailored to suit different semiconductor devices and usage scenarios.
Types of Ceramic Packages
Leaded ceramic packages: This packages feature metal leads that come out from the package body. Making it easy to connect the package to a PCB circuit board. This type of packages are widely used in application.
Leadless Ceramic Packages: This packages do not have metal leads. Use solder balls or other contact points, for connecting to the PCB. Leadless ceramic packages are becoming more popular because of their size and cost effectiveness.
Hybrid Ceramic Packages: This packaging combine elements from both leaded and leadless ceramic packages providing benefits from each type.
When choose on the ceramic package for a particular use engineers take into account factors such as the number of connections needed the size of the component and the environment it will be, in. By considering these aspects they can choose the right ceramic package to guarantee top performance, dependability and longevity of electronic devices.
Applications of Ceramic Packages
Ceramic packages find extensive application across various electronic fields, including:
● Automotive electronics
● Defense electronics
● Medical devices
● Industrial controls
● Networking
● Power electronics
● RF/microwave electronics
● Military and aerospace electronics
● Medical electronics
Ceramic packages offers benefits compared to other packaging materials making them ideal for a wide range of electronic uses. Their excellent heat conductivity, thermal expansion, strong electrical insulation and chemical stability, making them popular and effective in different industries.
Current Trends and Future Directions
Miniaturization: The increasing need for more portable electronic device has led to the development of ceramic packages. As a result, that are becoming progressively smaller and thinner enabling the creation of compact and lightweight device.
Advanced Packaging: Ceramic packages are advancing to include functionalities and features. For example they now integrate components like resistors and capacitors to improve performance and shrink the size of electronic devices. Furthermore cooling systems are built in to tackle the heat management issues, in high power applications.
Reliability Improvements: The demand for devices that can endure tough conditions has driven the creation of ceramic packagaes with enhanced durability characteristics. This encompasses improvements, in the strength of solder connections and resistance to moisture guaranteeing the durability and reliable of parts in demanding operational environments.
Ongoing research and development in ceramic packaging:
The progress in top ceramic materials is geared towards boosting heat transfer, electrical isolation and mechanical characteristics. Innovations in metallization methods strive to enhance the durability and dependability of soldered joints. Furthermore novel packaging concepts are under investigation to maximize the dispersal of heat and shield against interference (EMI). Embedding elements within ceramic enclosures aids in shrinking dimensions and cutting costs while integrating sensors for live tracking of environmental factors, like temperature and humidity adds to their capabilities.
In a Word
Shaping the future of technology, the development of smaller, more powerful, and reliable electronic devices will be enabled by advancements in ceramic packaging, including ongoing miniaturization, increased use of advanced features, and improved reliability. As the industry progresses, ceramic packaging will continue to advance. Selected based on factors like connection density, size, and environmental requirements, leaded, leadless, and hybrid ceramic packages offer distinct advantages. Providing protection and connectivity for delicate electronic components, ceramic packages are essential components in modern electronics.