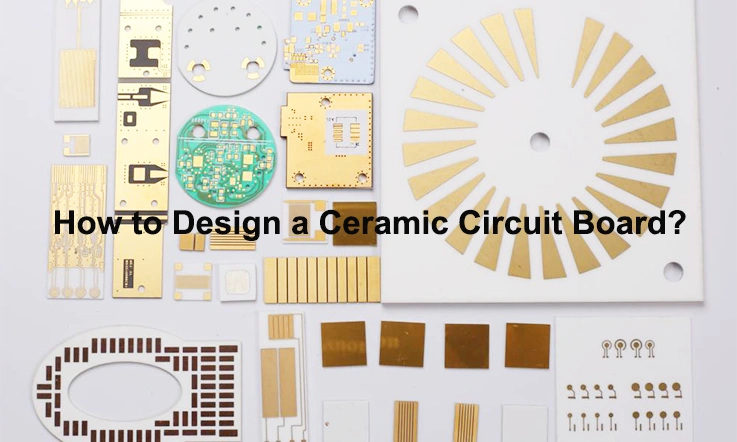
Designing a ceramic circuit board (CCB) requires careful consideration of various factors to ensure optimal functionality, reliability, and performance. Ceramic substrates possess characteristics that render them ideal for challenging uses. This piece acts as a manual presenting the sequential procedure, for crafting a CCB and emphasizing essential factors at every phase. Starting from picking the substrate to designing the layout managing thermal conditions and selecting components engineers can utilize this manual to produce top notch ceramic circuit boards tailored to their needs.
Importance of Circuit Boards in Electronic Devices
1. Structural Support: Circuit boards serve as bases maintaining correct positioning and safeguarding electronic parts from potential harm due, to vibrations or sudden impacts. They provide stability and shielding in gadgets exposed to motion or harsh conditions.
2. Electrical Connectivity: Circuit boards contain conductive traces and vias that establish essential electrical connections among the various components on the board. These connections are vital, for routing signals and distributing power efficiently ensuring the device operates correctly.
3. Miniaturization: Circuit boards enable the miniaturization of electronic devices by providing a compact and efficient means to package a multitude of components within a limited space. This progress is essential in todays electronics as there is always a need, for devices that’re compact and easy to carry around.
4. Reliability Enhancement:Electronic components are protected by circuit boards from things like moisture, dust and electromagnetic interference. They establish a controlled environment, for operation which lowers the chances of malfunctions and enhances the devices reliability overall.
5. Troubleshooting and Repair Facilitation: Circuit boards make it easier for technicians to troubleshoot and repair device. Their structure and design enable technicians to quickly identify part and connections making it easy to detect and resolve any issues that arise.
Circuit boards play a role in ensuring that electronic devices function effectively and reliably. They have many types. Such as Flexible PCB, High Density Interconnect PCB, Ceramic PCB and Metal Clad PCB each tailored to specific need and application. The choice of board type depends on factors like size, weight, flexibility and performance requirement. Overall these circuit boards are vital, for providing support, connectivity and functionality that contribute to the progress of technology.
Introduction to Ceramic Circuit Boards
Ceramics possess properties that make them ideal, for high performance and challenging applications. Unlike the choices of fiberglass or composite materials ceramic circuit boards use ceramics as the substrate material making them a specialized form of printed circuit board.
Advantages of Ceramic Circuit Boards:
●High Thermal Conductivity
●Low Coefficient of Thermal Expansion (CTE)
●High-Frequency Performance
●Excellent Chemical Resistance
●Durability and Reliability
Applications of Ceramic Circuit Boards:
Ceramic circuit boards are frequently utilized in situations where top notch performance, dependability and longevity’re crucial. Some usual applications include:
●Automotive electronics
●Aerospace and defense systems
●Medical devices
●Industrial automation
●High-power electronics
Types of Ceramic Substrates:
Various types of ceramic materials are used as substrates for ceramic circuit board. Therefore ceramic circuit board each possessing distinct characteristics and uses. Some common varieties include:
● Alumina
● Zirconia
● Beryllia
● Aluminum Nitride
● Boron Nitride
● Silicon Carbide
● Silicon Nitride
The selection of the ceramic base material is determined by the needs of the application taking into account aspects. Such as thermal efficiency, strength, electrical characteristics and cost factors.
Design Considerations for Ceramic Circuit Boards
Substrate Selection: Select the ceramic substrate material by assessing factors like thermal conductivity coefficient of thermal expansion and electrical properties. Look into choices such as alumina, zirconia and beryllia each, with pros and cons depending on the design specifications and intended use.
Trace Width and Spacing, Via Design, and Plane Design: Determine the appropriate trace width and spacing considering current carrying capacity, signal frequency, and dielectric constant of the ceramic substrate. Use wider traces for high-current applications and narrower traces for high-frequency signals. Optimize via size, shape, and placement to ensure proper electrical connectivity and minimize signal distortion, using blind and buried vias to enhance density and signal integrity. Establish robust and continuous ground planes to minimize noise and crosstalk, and design power planes with adequate copper thickness to handle required current and minimize voltage drop.
Thermal Management and Component: Leverage the high thermal conductivity of ceramic substrate for effective heat dissipation, and consider thermal vias or heat sinks to further enhance thermal performance. Choose components compatible with the thermal and electrical properties of the ceramic substrate, opting for surface mount technology components to improve reliability and ease of assembly.
Fabrication Process and Reliability Testing: Specify appropriate fabrication process parameters, including screen printing, sintering and firing temperature, while implementing stringent quality control measures to ensure dimensional accuracy and electrical performance. Focus on reliability by taking into account changes, vibrations and moisture protection. Test the ceramic circuit board thoroughly for both performance and durability, through various environmental conditions.
How to Design a Ceramic Circuit Board?
Designing a ceramic printed circuit board require considering various factor to guarantee the reliability of the PCB. Here is a guide on designing a circuit board.
1.Define Design Requirements: Make sure to provide a description of what your ceramic circuit board needs. Such as its purpose how it will be used, performance expectations and any rules or guidelines that must be followed. This step is crucial to make sure the design meets all requirements and regulations laying a groundwork, for the design process as a whole.
2.Select Ceramic Substrate: Select the ceramic base material depending on the thermal conductivity coefficient of thermal expansion (CTE) and electrical characteristics you need. Compare options like alumina, zirconia and beryllia weighing their pros and cons against your design needs. This decision plays a role, in ensuring top notch performance and dependability in the end product.
3.Schematic and Layout Design: Develop a detailed schematic diagram of the circuit, specifying components, their connectivity, and any required signal conditioning or control circuitry. Use schematic capture software for accurate documentation. Translate the schematic into a physical layout design on the ceramic substrate, considering component placement, signal integrity, power distribution, and thermal management to ensure efficient and reliable performance.
4.Trace Routing and Via Design: Route the traces on the ceramic substrate, considering factors such as current carrying capacity, signal frequency, and the dielectric properties of the ceramic material. Ensure appropriate trace widths, spacing, and impedance control for high-frequency signals. Determine the optimal location, size, and type of vias (plated through-holes, blind vias, buried vias) to maintain proper electrical connectivity and maximize routing density while minimizing signal distortion.
5.Finalization and Production: Design solid and continuous ground planes to minimize noise and crosstalk, and create power planes with sufficient copper thickness to handle required currents and minimize voltage drops. Utilize the high thermal conductivity of ceramic substrates for effective heat dissipation, incorporating thermal vias or heat sinks as needed. Select compatible components, perform comprehensive design rule checks, and generate Gerber files for manufacturing. After prototype fabrication, conduct thorough testing and validation, refine the design if necessary, and document the final design, including schematics, layout files, BOM, and design notes for future reference.
Final Thoughts
Designing a ceramic circuit board involves a systematic approach to meet the performance and reliability demands of modern applications. Engineers achieve performance in their ceramic PCB designs by choosing the right ceramic substrate fine tuning trace routing implementing effective thermal management techniques and selecting components with care. Rigorous testing, validation procedures and thorough documentation play roles in ensuring the success of the design process. With this guide, at hand engineers can confidently develop ceramic circuit boards that offer outstanding performance, reliability and functionality across various applications.