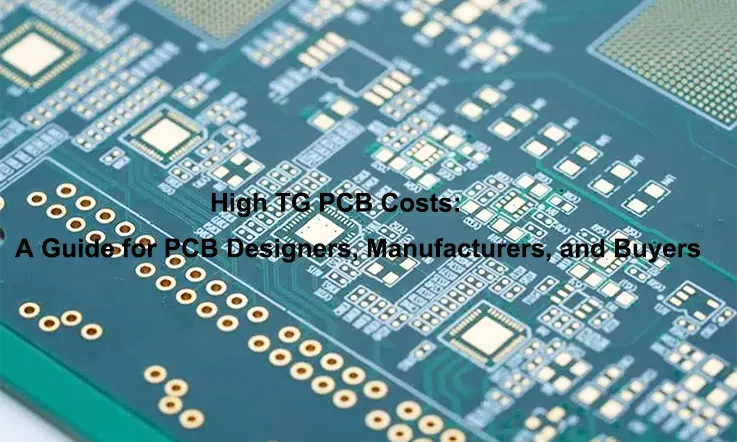
Let’s be real—nobody wants to pay more than they need to, especially in the fast-moving world of PCBs. But when you’re talking High TG PCBs, some costs are just par for the course. Whether you’re a PCB designer, an electronics manufacturer, or someone who needs to buy these little wonders in bulk, you know that cost control is more art than science. And hey, it’s not just about pinching pennies; it’s about making smart choices so your PCB performs like a champ, even when things get hot under the collar.
We’re diving into what drives High TG PCB costs and how you can keep them from spiraling out of control. Grab a cup of coffee and settle in—we’re about to break this down from top to bottom, with plenty of tips to save you money without sacrificing quality.
What the Heck is a High TG PCB Anyway?
Before we dive into the dollars and cents, let’s talk about what High TG PCBs actually are. TG, or Glass Transition Temperature, is a fancy way of saying “how much heat can your board take before it starts acting funky.” In short, the TG value is the temperature where your PCB material shifts from a solid, glass-like state to something a bit more rubbery. For most standard PCBs, that’s usually around 130°C. But for High TG PCBs, you’re looking at a TG of 170°C or higher.
Why does this matter? Well, if you’re building something that gets hot—like, really hot—you need a PCB that can handle the heat without melting into a gooey mess. This is where High TG PCBs come into play. They’re specifically designed for high-performance, high-temperature applications where your standard board just won’t cut it.
How Materials Drive High TG PCB Costs?
When it comes to PCB material costs, it’s a no-brainer that your choice of materials will greatly impact your budget. For High TG PCBs, the most common base materials are FR-4, Polyimide, and PTFE. Each of these materials comes with its own set of benefits and drawbacks, especially in terms of cost and performance.
Pros and Cons of High TG PCB Materials
Material | Pros | Cons |
High TG FR-4 | Cost-effective, moderate heat resistance, widely available | Limited thermal performance for extreme applications |
Polyimide | Excellent heat resistance, ideal for aerospace & military | Higher cost, complex manufacturing |
PTFE (Teflon) | Superior electrical properties, great for RF applications | Very expensive, harder to process |
FR-4: The workhorse of PCB materials. It’s relatively cheap and can handle moderate heat, making it a good candidate for general-purpose designs. However, when you step up to High TG FR-4, the costs start climbing due to its enhanced ability to tolerate higher temperatures.
Polyimide: This material is a champ when it comes to heat. It’s commonly used in aerospace and automotive applications where durability and heat resistance are non-negotiable. But let’s face it—this isn’t the cheapest material on the block. Expect to pay a premium for its thermal stability.
PTFE: Also known as Teflon, PTFE is ideal for high-frequency applications. If your project needs both high heat resistance and superior electrical performance, this is the way to go. However, it comes with a steeper price tag, often reserved for niche, high-performance needs.
These materials are like choosing between a sedan, a sports car, and a luxury SUV—each serves a purpose, but they come with their own price tags.
Layer Count and Thickness: Why More is Always More Expensive?
When you’re designing your High TG PCB, it’s easy to think, “Hey, why not add a couple more layers?” Well, more layers mean more cash out of your pocket. The additional layers require extra lamination cycles, more material, and more time on the production floor. Think of it like building a sandwich: more layers of bread, cheese, and meat take longer to prep and cost more.
Let’s also talk about board thickness. A thicker PCB can offer more durability and thermal resistance, but it’ll also drive up your cost per square inch. It’s like ordering a deep-dish pizza—you’re getting more, but you’re also paying for it. The real challenge here is finding that sweet spot between performance and cost without overdoing it.
Multilayer PCBs: For High TG designs, especially those with more complex circuitry, multilayer boards are pretty much a given. But, remember, every additional layer adds to your final bill.
PCB Thickness: A thicker board doesn’t just add material costs; it also increases the complexity of the production process. Manufacturers will need to adjust for things like drilling and plating, and all of that adds up.
Manufacturing Complexity: The Real Cost Driver
One of the sneakiest factors driving up High TG PCB costs is manufacturing complexity. Sure, it’s easy to think it’s just a few extra dollars here and there, but once you start adding fine trace and space, advanced stack-ups, and high-density interconnects (HDI), the costs can pile up faster than you’d expect. Why? Because the more intricate the design, the harder it is to manufacture. You’re pushing the capabilities of machines and materials, and that complexity comes at a premium.
Then, let’s throw in the challenge of lead-free assembly. Environmental regulations (like RoHS compliance) are pushing manufacturers toward lead-free soldering processes. Lead-free might be a win for the environment, but it’s a tougher process because it requires higher soldering temperatures, which naturally puts more strain on the materials—especially your High TG PCB.
Surface Finishes: Choosing the Right One Without Going Overboard
Selecting a surface finish for your High TG PCB is like choosing the right paint for your house—some are more durable, some are cheaper, and some are all about performance.
Pros and Cons of Surface Finishes for High TG PCBs
Finish | Pros | Cons |
ENIG | Flat surface, high durability, great for fine-pitch components | High cost |
HASL | Affordable, good for general use | Poor performance in high-temp environments, uneven surface |
OSP | Lead-free, low-cost, environmentally friendly | Short shelf life, not as durable as metal finishes |
ENIG (Electroless Nickel Immersion Gold): This is the gold standard (no pun intended). It offers excellent corrosion resistance and a flat surface, making it ideal for fine-pitch components. But, as you might expect, the price tag for ENIG is higher than most other finishes.
HASL (Hot Air Solder Leveling): If you’re looking to save some cash, HASL is a budget-friendly option. It’s good for general-purpose boards but doesn’t fare well in high-temperature environments.
OSP (Organic Solderability Preservative): If you want an environmentally friendly option, OSP offers a cost-effective, lead-free finish. However, it’s not as durable as ENIG, making it better suited for short-term applications.
The trick is knowing which surface finish fits your needs without driving your costs through the roof. If you don’t need ENIG’s precision or corrosion resistance, choose for HASL or OSP to save money.
Prototyping and Production: Where the Money Really Goes
Prototyping is where many designers and manufacturers see their budgets balloon. Small-batch production runs are notoriously expensive due to setup costs and lower economies of scale.
Prototyping Costs: If you’re running just a few boards, the price per unit can skyrocket. To mitigate this, focus on designing a prototype that covers the essentials without adding unnecessary features.
Volume Production: Once you move from prototyping to full-scale production, your cost per square inch drops. High-volume runs benefit from economies of scale, making larger production runs more cost-effective in the long term.
Balancing your prototype’s complexity with cost efficiency is key. Start small, but keep your eye on scaling for when you move to full production.
Assembly Costs: The Other Half of the Equation
Pros and Cons of Assembly Methods
Assembly Method | Pros | Cons |
Through-Hole | Strong mechanical bonds, good for heavy components | Bulky, more expensive than surface-mount |
Surface Mount | Compact, allows for higher component density | May require finer pitch and advanced technology |
Once your board is designed and manufactured, you’ve still got to get everything put together, and that’s where assembly costs come in. Turnkey assembly services are becoming more popular because they take the hassle out of sourcing components and assembling the board, but you’re going to pay for that convenience.
Then there’s your BOM (Bill of Materials). If your components are rare, expensive, or in high demand, that’s going to drive up your total cost. And don’t forget the additional fees for prototyping—if you’re only doing a small run, you’re looking at a much higher cost per unit.
Component Sourcing: Make sure your components are readily available to avoid any spikes in costs or delays in your timeline.
Prototyping Costs: For smaller runs, the costs can get high. Sometimes it’s worth cutting down on non-essential features in early prototypes to save money until you’re ready for a full production run.
Cost Optimization: Tips for Saving Money Without Compromising Performance
Let’s face it—nobody’s got an unlimited budget, and even if you did, you wouldn’t want to waste money where you don’t have to. Here are some tips to optimize your High TG PCB costs without cutting corners.
Smart Design: Keep your design as simple as possible. You don’t always need that extra layer or super-complex trace arrangement. Simple designs are easier to manufacture and test, which means fewer headaches and lower costs.
Material Selection: Sure, Polyimide is fantastic, but if your project can handle it, choosing for High TG FR-4. It’s much more affordable and often gets the job done.
Surface Finishes: If your PCB isn’t going to be in a high-temperature or high-frequency environment, don’t spring for ENIG. HASL or OSP might be just fine and will save you a good chunk of change.
Production Volume: Always try to batch your production runs. Large volumes significantly lower the cost per square inch compared to small-batch production.
Prototyping Wisely: Keep your prototyping simple. You don’t need to pack every feature.
Advanced Manufacturing: Hidden Costs You Should Know About
The complexity of your design plays a massive role in your High TG PCB costs. Advanced features like HDI (High-Density Interconnects), blind and buried vias, or fine trace and space requirements add layers of complexity—and cost.
HDI Technology: When you need a compact, high-performance design, HDI is the go-to. But don’t expect this technology to come cheap. The advanced manufacturing techniques required to create HDI PCBs push production costs higher.
Lead-Free Soldering: Environmental regulations like RoHS compliance often mean switching to lead-free soldering, which requires higher temperatures. This puts more strain on your materials and your budget. It’s a necessary evil for eco-conscious designs but does add to the final cost.
Case Studies: Learning from Experience
Here’s where the rubber meets the road. Real-world case studies and examples are invaluable for understanding how design choices impact costs in different industries.
Automotive Applications: For example, one client designing a High TG PCB for an automotive ECU was able to reduce costs by switching from Polyimide to High TG FR-4 for non-critical layers. This simple material shift saved over 15% on the total production cost while maintaining performance.
Aerospace Applications: In another case, an aerospace company designing for extreme environments needed Polyimide but found that by optimizing the board’s stack-up and reducing unnecessary layers, they shaved 10% off their initial estimates.
Learning from these examples can help you navigate your own cost-saving strategies.
Balancing Cost and Performance in High TG PCBs
In the world of High TG PCBs, achieving the right balance between cost and performance can feel like walking a tightrope. Whether you’re a PCB designer, manufacturer, or buyer, you want to keep costs in check while ensuring your boards hold up under high heat and stress. From material choices to layer count and advanced manufacturing techniques, every decision matters.
But hey, you don’t have to figure it out all by yourself! Whether you’re looking to shave off costs on your next big project or need help optimizing a complex High TG PCB design, our team of seasoned pros is just a call away. We’ll help you navigate the nitty-gritty details, recommend the best materials, and work out ways to lower costs without cutting corners.
So why not drop us a line? We’d love to talk shop and help you make your next High TG PCB project a slam dunk. Let’s chat about how we can turn those design ideas into a reality—without breaking the bank!
Wrapping Up
At the end of the day, the cost of a High TG PCB boils down to smart choices. Material choices, design complexity, manufacturing processes, and production volume all play significant roles in determining your final costs. The good news? With smart decisions—like opting for High TG FR-4 over Polyimide when appropriate, or choosing the right surface finish—you can balance performance and cost effectively.
Keep these tips in your back pocket the next time you’re looking to spec out your High TG PCB, and you’ll be well on your way to saving some serious cash while keeping your boards running cool, even when the heat is on.
Q&A: Common Questions About High TG PCB Costs
Q1: Why do High TG PCBs cost more than regular PCBs?
High TG PCBs use specialized materials, like High TG FR-4 or Polyimide, that can withstand elevated temperatures. This increases both material and manufacturing costs, as more complex processes are involved. Their high reliability in demanding environments like automotive or aerospace justifies the extra price.
Q2: How can I reduce the cost of my High TG PCB design?
Opt for cost-effective materials like High TG FR-4 instead of Polyimide where possible. Simplify your layer count, avoid unnecessary features, and consider lower-cost surface finishes such as HASL over ENIG for less heat-sensitive applications. Ordering in larger quantities will also help lower per-unit costs.
Q3: Does the choice of surface finish affect the price significantly?
Yes. ENIG is pricier but offers better corrosion resistance and is ideal for high-reliability applications. On the other hand, HASL or OSP finishes are more affordable and suitable for general-purpose boards, though they may not last as long in extreme conditions.
Q4: How does layer count influence High TG PCB costs?
Each additional layer increases manufacturing complexity, requiring more material and process steps. While multilayer boards provide more routing options and higher performance, they come with a higher price tag. Reducing unnecessary layers is an easy way to lower costs without compromising functionality.
Q5: Can I use High TG PCBs in low-temperature applications?
Absolutely! High TG PCBs offer increased reliability and durability, even in less demanding environments. While you might not need the extra heat resistance, their performance advantages—like reduced warping—can still make them a solid choice for high-frequency or high-density designs.