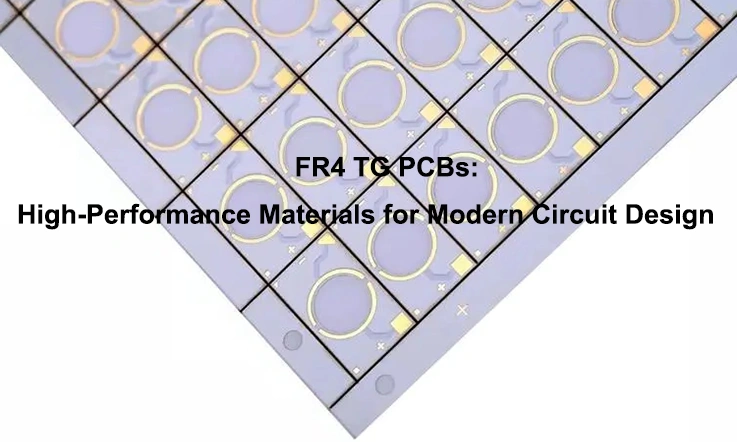
If you’re knee-deep in designing printed circuit boards (PCBs) or running the show in electronics manufacturing, chances are you’ve run into the term “FR4 TG PCB.” But here’s the thing: not everyone fully understands the real deal behind these materials and how they affect your end product.
So, what’s the story with FR4? Well, it’s one of the most widely used materials in PCBs, thanks to its solid mechanical and electrical properties. The “TG” part refers to glass transition temperature, which is like the thermostat that tells you how much heat the material can handle before it starts acting funky. In a nutshell, knowing your Tg is a bit like keeping an eye on your car’s engine temp—you don’t want it to overheat when you’re pushing it to its limits.
In this comprehensive guide, we’ll dive deep into FR4 TG PCBs, from their core properties to manufacturing techniques, and even the nitty-gritty of how they hold up in real-world applications. Buckle up—we’re about to take this ride full throttle!
What is FR4 TG PCB?
FR4 is a glass fiber-reinforced laminate used in the base of most circuit boards. It’s the go-to material because of its excellent electrical insulation and resistance to moisture, and it’s relatively low-cost compared to other materials like PTFE.
But here’s the twist: Tg stands for glass transition temperature, which is the temperature at which the FR4 material softens and loses its rigidity. Think of it as your PCB’s heat tolerance threshold. Once the temperature rises beyond this Tg point, your board can start to bend, warp, or even fail, just like how pizza crust goes soft if you leave it in a humid environment.
In a world where electronics are running hotter and faster, choosing a PCB with a high Tg value can mean the difference between your design holding up or going kaput. Standard Tg for FR4 is around 130°C, but if you’re working in high-temperature environments, like in automotive or industrial applications, you’ll want to bump that up to 170°C or higher.
Classes of FR4 TG PCBs
Just like there are different types of pizza crusts—thin, thick, stuffed—there are different types of FR4 PCBs, each tailored to specific thermal needs. Let’s break it down:
Low Tg FR4 (<130°C)
●Best for: Basic consumer electronics, low-power applications.
●Pros: Cheaper, widely available, and sufficient for low-stress environments.
●Cons: It can’t handle high heat, so it’s likely to bow out if the temperature rises too much.
Medium Tg FR4 (130°C-170°C)
●Best for: More complex circuits, moderate-temperature applications
●Pros: Offers better heat resistance than standard low Tg, making it a solid middle-ground choice for devices that run hotter than your average gadget.
High Tg FR4 (>170°C)
●Best for: High-power electronics, automotive, aerospace, and industrial environments
●Pros: These boards are the heavy hitters, standing up to extreme heat, ensuring that even under the hood of a car or inside a factory, they keep their cool.
●Cons: They come with a higher price tag, but trust us—they’re worth every penny when the stakes are high.
When you’re designing a product for tough environments, you’re going to want High Tg PCBs. They handle the heat better, last longer, and ensure your design performs at its best under stress.
Applications of FR4 TG PCBs
FR4 TG PCBs are a natural fit for industries where reliability and durability are non-negotiable. Here’s where they shine:
Automotive Electronics
In the automotive world, you’ve got systems that generate heat like nobody’s business—engine controls, power systems, and infotainment screens all run hotter than a Las Vegas parking lot in July. For this reason, High Tg PCBs are used in ECUs (Electronic Control Units), powertrain systems, and even lighting modules. These boards resist the high temperatures while ensuring reliability and performance, keeping the vehicle running smoothly.
Industrial Equipment
Ever seen factory machines running 24/7? Those beasts don’t stop, and neither should the electronics running them. Industrial automation systems demand PCBs that can handle extended periods of heat, vibration, and constant power cycling. High Tg PCBs are often found in motor controllers, industrial sensors, and power supply units, where heat resistance and reliability are non-negotiable.
Telecommunications
With the rise of 5G and other high-frequency technologies, PCBs need to keep signals crisp and clear, even when the circuits are working overtime. In high-frequency applications, signal integrity can degrade when the board heats up, leading to dropped calls or weak signals. High Tg PCBs ensure that signal integrity is maintained, even in the face of rising temperatures.
Power Supplies and Inverters
In the world of power electronics, devices that handle high current loads generate heat. FR4 TG materials are ideal for power inverters, transformers, and DC-DC converters, where consistent performance is essential. Their ability to stand up to prolonged heat exposure without losing their shape or electrical properties makes them a must-have for these applications.
Why High Tg PCBs Are the Right Choice?
There are a bunch of reasons why High Tg PCBs are the MVPs of the PCB world. Sure, they handle heat better than your average Joe, but there’s more to it than that.
Thermal Management
Heat and electronics don’t mix—ask any designer who’s tried to cram components into a tight space. When things heat up, you need to keep your cool. High Tg PCBs are built to manage thermal stress, whether that’s through thicker copper traces, better heat dissipation, or clever thermal via placement. These boards keep your components from melting down when the going gets hot.
Electrical Performance
As frequencies climb, so does the risk of signal degradation and EMI (electromagnetic interference). High Tg PCBs offer more stable dielectric properties, allowing for cleaner signals and better performance in high-speed circuits. It’s kinda like getting better reception on your favorite FM station—no static, just smooth tunes.
Durability
Electronics exposed to high temperatures go through thermal cycling, where they repeatedly heat up and cool down. This expansion and contraction can wreak havoc on a PCB’s structure, leading to cracks or delamination. But with High Tg PCBs, you get a durable solution that’s built to last in harsh environments, whether it’s a jet engine or a server farm.
The Manufacturing Process for FR4 TG PCBs
Making a High Tg PCB isn’t your standard day at the office. These boards require a bit more finesse, and the process often includes more robust materials and techniques.
Laminate Construction
High Tg materials like FR4 are chosen for their stability under high heat. These materials are fiberglass-reinforced, giving them added strength while maintaining the necessary dielectric properties.
Multilayer Stackup
In multilayer boards, especially those using high Tg materials, the stackup design is key. The layout of the layers—signal, ground, and power planes—has to be spot-on to ensure that the board can handle high frequencies without signal loss or crosstalk. Get the layer count wrong, and it’s like trying to tune a guitar with loose strings—not gonna work.
Surface Finish
Choosing the right surface finish is critical for any PCB, but with High Tg boards, it’s even more essential. You want a finish that ensures strong solderability while protecting the board from corrosion. Common finishes include HASL, ENIG, and OSP. Each has its perks, but for high-reliability applications, ENIG offers better longevity, while HASL gives more cost-effective protection.
Here’s a table summarizing the pros and cons of common surface finishes for FR4 TG PCBs:
Surface Finish | Pros | Cons |
HASL (Hot Air Solder Leveling) | – Cost-effective and budget-friendly – Excellent solderability – Widely available | – Uneven surface, not ideal for fine-pitch components – Can add thermal stress during finishing |
ENIG (Electroless Nickel Immersion Gold) | – Smooth, flat surface suitable for fine-pitch components – Great for high-end applications – Long shelf life | – More expensive – Risk of “black pad” issue – Complex and time-consuming process |
OSP (Organic Solderability Preservative) | – Eco-friendly and RoHS-compliant – Low-cost alternative to ENIG – Good for surface-mount technology (SMT) | – Short shelf life – Less durable – Prone to oxidation if stored too long |
This table provides a quick, skimmable comparison of the surface finishes most commonly used in FR4 TG PCBs, helping designers and buyers make informed decisions based on their project needs.
Thermal Management Techniques for FR4 TG PCBs
When heat is your number-one enemy, having the right thermal management strategies in place can save the day. High Tg PCBs come with built-in features to handle higher temperatures, but smart design choices go a long way in making sure your board performs like a champ.
Thick Copper Traces
Increasing the copper thickness on your PCB can help spread the heat across the board, preventing hotspots that could fry your components. It’s like adding a radiator to your car engine—more surface area means better cooling.
Thermal Vias
Thermal vias are another trick of the trade. These are tiny holes drilled through the PCB that allow heat to flow from one layer to another, dissipating it more effectively. Think of them as little heat highways that get the temperature out of the danger zone.
Considerations for Selecting FR4 TG Materials
Application Requirements
When choosing your material, start by asking yourself: What’s my end goal? Are you building a high-powered motor controller or a standard consumer gadget? The demands of your application will dictate whether you go with a standard or High Tg material. It’s all about knowing what your board will be up against.
Layer Count and Thickness
The more layers your PCB has, the more complex the thermal dynamics get. Thicker boards tend to retain more heat, so if you’re designing a multilayer PCB (which is pretty common these days), choosing the right FR4 TG material becomes even more critical. More layers = more heat retention. That’s a fact. But with high Tg materials, your board can handle the extra layers without breaking a sweat.
In a high-layer-count PCB, the thickness of the dielectric layers also matters. A thicker dielectric will usually mean better insulation but could also mean that heat gets trapped inside, making heat dissipation more challenging. This is where thermal vias and thicker copper traces come into play.
Emerging Technologies and High Tg PCBs
5G Infrastructure
As the world gears up for the widespread implementation of 5G networks, the demand for high Tg PCBs is climbing fast. In 5G equipment, where signals are transmitted at much higher frequencies, signal integrity is king. High Tg materials help maintain clean signal transmission even when devices run at high speeds and temperatures.
When it comes to the antennas and base stations for 5G, heat is a real issue, given that these systems operate 24/7, often outdoors in tough environments. High Tg PCBs help ensure that the technology behind 5G can handle high heat without any signal loss or degradation, giving you that lightning-fast internet speed without a hitch.
Electric Vehicles (EVs)
Electric vehicles (EVs) are another area where High Tg PCBs are becoming a necessity. Think about it: EVs have power systems that are constantly generating heat, especially in the battery management systems (BMS), motor controllers, and charging circuits. In these high-power applications, standard FR4 materials might not cut it. You need High Tg to ensure the circuits don’t warp or degrade over time due to excessive heat.
Also, high-current applications inside EVs demand more robust thermal management solutions. Using high Tg materials in the design of power modules can drastically reduce the risk of circuit failure, ensuring long-term reliability in electric vehicle performance.
Key Design Trade-offs for FR4 TG PCBs
Copper Weight vs. Thermal Management
A classic design dilemma in PCB manufacturing is balancing copper weight with thermal performance. Thicker copper traces are fantastic for heat dissipation, but they also increase the overall cost of the board and can make manufacturing more challenging. The key is to strike a balance between adding enough copper to manage heat effectively and keeping the board’s cost within a reasonable range.
By choosing high Tg materials, you can reduce some of the need for thicker copper because the board itself is better able to withstand high temperatures. This lets you hit that sweet spot between cost and performance without sacrificing durability.
PCB Thickness vs. Signal Integrity
When working with multilayer PCBs, you’ll often find that thicker boards lead to better signal isolation. But here’s the kicker: thicker boards also trap more heat. In high-frequency applications, signal integrity is everything, so the key is designing your stack-up with high Tg FR4 materials that keep the signals crisp, while also managing heat efficiently through the use of thermal vias and power planes.
Case Study: High Tg PCB Implementation in Applications
Automotive Case Study
A major automotive manufacturer faced issues with engine control modules (ECMs) overheating during extreme temperature changes. These modules were exposed to temperatures ranging from freezing cold to blistering heat under the hood. After several test failures using standard FR4 boards, they switched to high Tg PCBs with a Tg of 180°C.
The results? The boards held up under stress, and there was a significant reduction in board warping and thermal cycling failures. By opting for high Tg FR4 materials, the manufacturer saw a dramatic improvement in reliability, especially in harsh environments.
5G Base Station Project
A telecommunications company working on 5G base stations was experiencing signal loss due to overheating. The original PCB design used a medium Tg material, which couldn’t handle the thermal stress of constant, high-frequency signal transmission. By switching to high Tg PCBs with better thermal management features (such as thick copper traces and thermal vias), the company solved their heat issues and saw a marked improvement in signal integrity.
The project’s success showcased how high Tg materials are not just about surviving heat—they’re about maintaining optimal electrical performance under intense conditions.
Internal and External Factors Impacting PCB Selection
External Factors: Cost vs. Performance
Choosing between a standard FR4 PCB and a high Tg PCB often comes down to a cost-performance trade-off. Sure, high Tg materials cost more upfront, but what’s the cost of failure? If your PCB fails in a critical system—like in an electric vehicle’s powertrain or a 5G base station—those failures could cost far more in downtime, repair, and lost revenue.
Internal Factors: Design Complexity
As circuits get more complex and require more layers, you’ll often find yourself needing to bump up the Tg rating. With each additional layer, the thermal stress on the board increases, so design complexity can often dictate whether or not high Tg FR4 is the best fit. In most multilayer designs where temperature control is a concern, going for a high Tg PCB becomes less of an option and more of a requirement.
Wrapping Up: The Future of FR4 TG PCBs
As electronics continue to evolve—becoming more powerful, more compact, and more reliable—the demand for High Tg PCBs is only going to grow. From 5G networks to electric vehicles, these boards are becoming the backbone of modern, heat-intensive applications. Their ability to handle thermal stress, ensure signal integrity, and increase long-term reliability makes them a must-have in a wide range of industries.
Whether you’re a PCB designer, an electronics manufacturer, or someone sourcing materials for a new project, high Tg materials should be on your radar. They might cost a little more, but in the long run, they offer the durability and performance that keep your designs rock-solid—no matter how hot things get.
Final Word
In the world of high-performance electronics, don’t let heat be the thing that melts your dreams. By choosing the right materials and leveraging the advantages of High Tg PCBs, you’re setting yourself up for success. So next time you’re on a design sprint, make sure your PCB can handle the pressure. After all, when it comes to electronics, it’s all about playing it cool.
Common Questions About FR4 TG PCBs
Q1: Why is Tg Rating So Critical When Choosing FR4 PCBs?
The Tg rating, or glass transition temperature, tells you how much heat the material can handle before it starts to soften. For high-performance applications, especially in industries like automotive, aerospace, or telecommunications, a higher Tg rating means your board will stand up better under the heat. In these environments, heat is a constant factor, and using a PCB with a low Tg might be like taking a hot rod to the desert without enough coolant—it’s bound to overheat.
Q2: How Do I Choose the Right Tg for My Application?
It depends on where and how you plan to use the PCB. If your design will be running in high-temperature environments—think power electronics, industrial controls, or 5G infrastructure—a high Tg FR4 material (above 170°C) is your best bet. But for simpler, consumer-level devices that don’t generate much heat, a standard Tg of around 130°C may work just fine. It’s all about matching the heat tolerance of the material to the demands of your project.
Q3: What Are the Pros and Cons of Surface Finishes Like HASL, ENIG, and OSP?
When you’re dealing with FR4 TG PCBs, choosing the right surface finish for the job is just as crucial as picking the right Tg. Different finishes have their strengths and drawbacks, and knowing which one to go for depends on your end use, budget, and environmental requirements.
Q4: Are High Tg FR4 PCBs Really Necessary for Consumer Electronics?
In most consumer electronics, the answer is probably no. Devices like smartphones, tablets, or standard home appliances don’t typically run hot enough to need high Tg materials. A standard Tg of 130°C will usually do the trick. However, if your device is pushing the limits with high power output or operates in extreme environments (think of gaming consoles or high-performance laptops), then opting for a medium Tg might be a smart move.
Q5: What Are the Risks of Not Using a High Tg PCB in High-Temperature Applications?
Skipping out on a high Tg PCB in a high-temp application is like forgetting to pack sunscreen for a beach day—it’s a recipe for disaster. When the temperature gets too hot and exceeds the board’s Tg, the material can start to soften, warp, and eventually delaminate. This means signal integrity goes out the window, components start to malfunction, and in extreme cases, the entire board can fail. That’s not something you want happening in critical applications like automotive engine controls or power supplies.
Q6: How Do I Optimize the Design of a High Tg FR4 PCB for Thermal Management?
Thermal vias are like tiny highways that help spread the heat from one layer of your PCB to another, improving heat dissipation and reducing the likelihood of hot spots. By strategically placing thermal vias around components that generate the most heat (like power regulators or high-current ICs), you ensure that your board stays cool under pressure.
Increasing the copper weight of your traces helps improve thermal conductivity, allowing heat to spread more evenly across the board. It’s like adding extra lanes to a traffic jam—it keeps things flowing more smoothly. Thicker copper not only manages heat better but also improves the board’s ability to handle higher current loads, making it ideal for power-hungry designs.