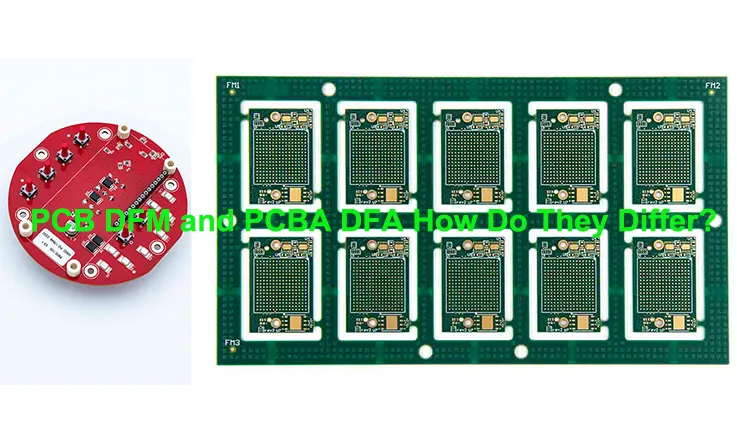
In contemporary times, the lexicon of electronics hobbyists and novices has seen the increasing use of terms such as DFM (Design for Manufacture), DFA (Design for Assembly), and more broadly, DFX (Design for Excellence). To alleviate any confusion, our aim is to establish the term PCBA Design for Assembly (PCBA DFA) as a prominent concept, emphasizing its distinctive nature and crucial role within a turnkey environment.
At the same time, we aim to underscore the disparities between conventional PCB DFM (Design for Manufacture) and PCBA DFA (Design for Assembly) approaches. Additionally, we provide compelling justifications for prioritizing investment in robust DFA practices and thorough inspections.
PCB DFM and PCBA DFA: How Do They Differ?
PCB DFM (Design for Manufacturability) and PCBA DFA (Design for Assembly) are two important concepts in the electronics manufacturing industry. While they are related and often used in conjunction, they have distinct focuses and objectives.
1. PCB DFM (Design for Manufacturability):
PCB DFM is the process of designing a printed circuit board in a way that maximizes its manufacturability and reliability.
It involves considering various manufacturing constraints and guidelines during the design phase, such as component placement, trace routing, layer stackup, and design rules.
The goal of PCB DFM is to ensure that the design can be manufactured efficiently, with minimal defects and at a reasonable cost.
It helps to optimize the manufacturing process, reduce the risk of errors, and improve the overall quality of the PCB.
2. PCBA DFA (Design for Assembly):
PCBA DFA is the process of designing the assembly of components onto a printed circuit board in a way that maximizes efficiency and reduces assembly time and cost.
It focuses on the arrangement and accessibility of components, the optimization of assembly processes, and the reduction of manual labor.
PCBA DFA considers factors such as component packaging, orientation, and spacing, as well as the use of standardized parts and automated assembly techniques.
The goal of PCBA DFA is to streamline the assembly process, minimize the risk of errors, and improve the overall efficiency and cost-effectiveness of the assembly operation.
Overall, PCB DFM primarily focuses on the design of the PCB itself, considering manufacturing constraints and guidelines, while PCBA DFA focuses on the design of the assembly process, considering the arrangement and accessibility of components to optimize assembly efficiency. Both concepts are important for ensuring a successful and efficient manufacturing and assembly process in the electronics industry.
JarnisTech: PCB DFM is Provided From the Onset
PCB DFM is an essential requirement for manufacturers to ensure their ability to manufacture a product effectively. A manufacturer’s competence is determined by their capability to assess if a design can be successfully manufactured. If there are issues with the supplied materials that prevent assembly, it is not the fault of the assemblers. Just like a chef cannot be expected to make a cake with ingredients meant for a pizza, assemblers cannot be expected to work with incompatible materials.
In turnkey PCB assembly and product development, we gather the necessary components to create a functional device. However, occasionally, we may receive incorrect or incompatible parts, akin to receiving pepperoni and tomato puree instead of the ingredients for a spongey red velvet cake. PCB designers are aware that even a small mistake can ruin the entire batch. While achieving perfection on the first attempt is ideal, the reality is that with numerous parts from different manufacturers, each with varying reliability, it rarely happens. The complexity and room for error in creating a single functioning device are often underestimated, leading to oversight or improper execution of essential checks such as footprint verification. This is where a DFA check performed by a qualified engineer can prove invaluable.
At JarnisTech, we offer a Design for Assembly review for all PCB assembly orders to avoid any unpleasant surprises when they matter the most. Our experienced engineers, with extensive hands-on product development expertise, are best suited to provide you with peace of mind. While optional, opting for this review can be the deciding factor in the success of your project.
We are excited to announce that we are now including the highly acclaimed Design for Assembly (DFA) review with every PCBA order, and it comes at no additional cost. We want to emphasize the value of this service, and we believe in it so strongly that we have decided to offer it completely free of charge. We invite you to verify this by checking our prices. This service can make a significant difference to the success of your project, and we highly recommend taking advantage of it.
Conclusion
PCB DFM and PCBA DFA are integral components of the electronics manufacturing process. PCB DFM focuses on designing a PCB that can be manufactured efficiently and reliably, while PCBA DFA ensures that the assembly process is streamlined and cost-effective. By incorporating both aspects into the design and assembly phases, manufacturers can enhance efficiency, reduce costs, and achieve a successful end product.