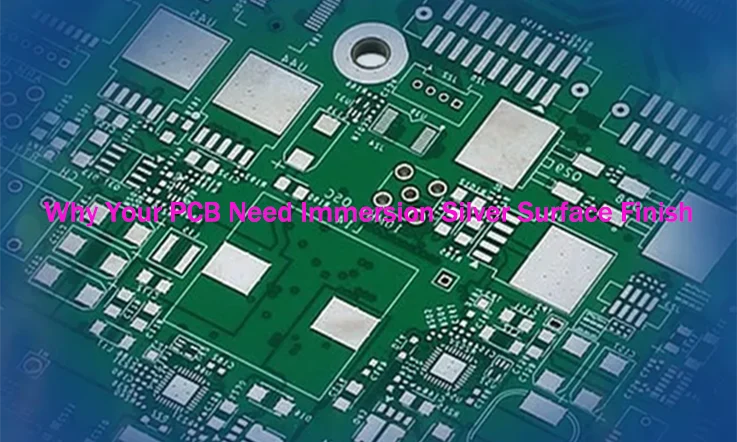
The surface finish of a printed circuit board (PCB) plays a critical role in determining its performance, reliability, and manufacturability. Among various surface finishes available, immersion silver has emerged as a compelling choice for engineers and manufacturers alike. With its exceptional conductivity, solderability, and compatibility with high-frequency applications, immersion silver offers a host of advantages that propel PCB technology to new heights. In this article, we delve into the captivating world of immersion silver surface finish, exploring its benefits, applications, and the key factors that contribute to its widespread adoption in the electronics industry.
What Is Immersion Silver?
Immersion Silver is a type of surface finish used in printed circuit boards (PCBs). It is a thin layer of silver applied to the surface of the PCB during the manufacturing process.
The immersion silver finish is created by immersing the PCB in a silver chemical solution, which allows a thin layer of silver to deposit onto the exposed copper surfaces. This process helps to protect the copper from oxidation and corrosion, thereby improving the overall reliability and lifespan of the PCB.
Advantages:
Immersion silver finish offers several advantages, including excellent solderability, good electrical conductivity, and a flat surface for component placement. It also provides a stable surface for wire bonding and is compatible with a wide range of soldering processes, such as reflow soldering and wave soldering.
Disadvantages:
However, it is worth noting that immersion silver finish is not recommended for applications with high operating temperatures or high humidity environments, as it can be prone to tarnishing or developing a yellowish hue over time. In such cases, alternative surface finishes like immersion tin or gold may be more suitable.
Thickness of Immersion Silver Surface Finish
The thickness of the immersion silver surface finish typically ranges from 5 to 18 micro inches. This measurement refers to the thickness of the silver layer that is deposited onto the copper surface during the immersion silver plating process. The specific thickness within this range can be determined based on the requirements of the PCB design, application, and industry standards.
It is important to note that the thickness of the immersion silver surface finish can have an impact on various factors, including solderability, electrical performance, and overall reliability of the PCB. Therefore, manufacturers carefully control the plating parameters and monitor the deposition process to achieve the desired thickness and ensure consistent quality throughout the production of immersion silver PCBs.
Important Points Regarding Immersion Silver Surface Finish
●Immersion silver offers greater ease of use compared to OSP (Organic Solderability Preservatives).
●In contrast to HASL (Hot Air Solder Leveling), immersion silver provides a more even and flat surface.
●Proper care is required for the storage and handling of PCBs with immersion silver surface finish, more so than with immersion tin.
●Immersion silver is considered to be a more environmentally friendly option than immersion tin.
●When stored in a dry environment, immersion silver finish can maintain its quality for a period of 6 to 12 months, similar to HASL boards.
●Once removed from storage, PCBs with immersion silver finish must be soldered within 24 hours.
●If PCBs with silver finish have been stored for over 12 months, a solderability test must be conducted prior to assembly.
During the process of immersion silver plating, certain common issues may arise such as the galvanic effect and solderability problems. These challenges can be addressed effectively through appropriate measures. It is crucial to pay attention to the choice of materials, handling conditions, and packaging requirements specific to this surface finish.
Immersion Silver Surface Finish Vs Immersion Gold and Immersion Tin
When comparing immersion silver surface finish with immersion gold and immersion tin, there are several key factors to consider. Let’s explore these factors to understand the differences and advantages of each surface finish:
Conductivity:
Immersion silver and immersion gold both offer excellent conductivity. Silver is known for its high electrical conductivity, which makes it an ideal choice for applications that require low resistance and high signal integrity. Gold, on the other hand, provides good conductivity and is highly resistant to oxidation, ensuring long-term reliability.
Solderability:
Immersion silver and immersion tin are both solderable surface finishes. However, immersion silver tends to offer better solderability due to its ability to form a thin layer of silver-tin intermetallic compounds during the soldering process. This helps to improve the wetting and bonding between the solder and the PCB surface.
Corrosion Resistance:
Immersion gold is known for its exceptional corrosion resistance, making it highly suitable for harsh environments or applications where exposure to moisture or chemicals is a concern. Immersion silver also offers good corrosion resistance, but it may not be as robust as immersion gold in certain conditions. Immersion tin, on the other hand, is more susceptible to oxidation and can degrade over time, potentially impacting the long-term reliability of the PCB.
Cost:
Immersion silver is generally more cost-effective compared to immersion gold. Silver is more readily available and less expensive than gold, making it a cost-efficient option for many applications. Immersion tin is typically the most cost-effective option among the three surface finishes.
Application-Specific Considerations:
The choice of surface finish depends on the specific requirements of the application. Immersion gold is often preferred for applications that demand high reliability, such as aerospace, medical, or military applications. Immersion silver is commonly used in high-speed digital, RF, and microwave applications where low loss and high signal integrity are critical. Immersion tin is suitable for applications that do not require long-term reliability or exposure to harsh environments.
Why is Immersion Silver Becoming a Popular PCB Surface Finish Choice Recently?
Silver has emerged as a preferred choice for surface modification on printed circuit boards (PCBs), particularly in the context of 5G circuitry. This trend can be attributed to silver’s exceptional conductivity, surpassing that of gold or copper. The application of a thin, soaked silver layer on the PCB facilitates optimal signal flow throughout the circuitry.
The advantages of silver extend beyond its superior conductivity. Its thinness can be precisely controlled, reaching levels as low as 0.1 micron. This characteristic enables easy surface modification, resulting in enhanced flatness of the circuit board. Consequently, it becomes well-suited for higher structural levels that require thinner links and gaps.
This novel surface modification technique finds its greatest utility in scenarios where the transmission of high-frequency signals is paramount. Unlike traditional methods such as Electroless Nickel/Immersion Gold (ENIG) or Electroless Nickel/Electroless Palladium/Immersion Gold (ENEPIG), silver-based modifications eliminate the need for a nickel layer. Nickel layers can introduce impedance and attenuate power, particularly in the context of high-frequency data transmission. The absence of a nickel layer ensures optimal power retention and facilitates seamless transmission of higher frequency signals.
Therefore, the utilization of silver as a surface modification material on PCBs has gained prominence due to its superior conductivity, ease of surface modification, and compatibility with high-frequency signal transmission. This advancement holds significant promise in meeting the evolving demands of the 5G circuitry landscape.
How is Immersion Silver PCB Produced?
The production of immersion silver PCB involves several key steps to achieve the desired surface finish. Here is an overview of the process:
1. Preparation of Copper Surface: The first step is to prepare the copper surface of the PCB. This typically involves cleaning the copper to remove any contaminants or oxidation. The copper surface may be treated with a micro etching solution to create a micro-roughened texture, which promotes adhesion and enhances the effectiveness of the immersion silver process.
2. Immersion Silver Plating Bath: The PCB is then immersed in a specially formulated plating bath containing a stable solution of silver ions. The bath is designed to facilitate the displacement reaction, where the silver ions displace the copper metal from the pad surface. The composition of the plating bath may vary depending on the specific requirements of the immersion silver process.
3. Controlled Deposition: The immersion silver plating process involves a controlled and gradual deposition of silver onto the copper surface. The plating conditions, including temperature, current density, and immersion time, are carefully controlled to ensure a uniform and dense layer of silver is deposited. The slow speed of deposition helps promote the formation of a high-quality crystalline structure.
4. Rinsing and Drying: Once the desired thickness of the immersion silver layer is achieved, the PCB is removed from the plating bath and thoroughly rinsed to remove any residual chemicals or impurities. Proper rinsing is essential to prevent contamination and ensure the integrity of the surface finish. After rinsing, the PCB is dried using appropriate methods, such as hot air or controlled temperature drying, to eliminate moisture.
5. Quality Control: After the immersion silver plating process, the PCB undergoes rigorous quality control measures. This may include visual inspection, measurement of silver thickness, and various tests to assess solderability and other relevant properties. Quality control ensures that the immersion silver finish meets the required specifications and standards.
It is worth noting that the specific details and parameters of the immersion silver PCB production process may vary among different manufacturers and depending on the specific application requirements. Manufacturers may employ proprietary formulations and techniques to optimize the performance and reliability of the immersion silver surface finish.
Handling and Storage of Immersion Silver Finished PCBs
Handling and storing PCBs with an immersion silver finish requires special care to maintain their quality and prevent damage. Here are some guidelines:
Handling: When handling immersion silver finished PCBs, it is important to avoid direct contact with the silver surface. Finger oils and contaminants can affect the solderability and electrical performance of the finish. Always wear gloves or handle the boards by their edges to minimize contact.
ESD Precautions: Electrostatic discharge (ESD) can damage electronic components and PCBs. Take appropriate ESD protection measures such as wearing an ESD wrist strap and working on an ESD-safe surface to prevent static discharge from affecting the immersion silver finish.
Cleaning: Before assembly or further processing, ensure that the immersion silver finished PCBs are properly cleaned. Use a mild cleaning agent specifically designed for PCBs and follow the manufacturer’s instructions. Avoid using harsh chemicals or abrasive cleaning methods that could damage or remove the silver finish.
Environmental Conditions: Immersion silver finished PCBs should be stored in a controlled environment to prevent tarnishing or oxidation. Avoid exposing the boards to high humidity, extreme temperatures, or direct sunlight, as these factors can degrade the silver finish. Ideally, store the PCBs in an anti-static bag or a dry, cool, and dark place.
Shelf Life: Immersion silver finishes have a limited shelf life due to their susceptibility to tarnishing. It is recommended to use the PCBs within a reasonable time frame to ensure the best solderability and performance. Consult with the PCB manufacturer or supplier for specific shelf life recommendations.
Compatibility: Immersion silver finishes may not be compatible with certain materials or processes. Ensure that the PCBs are compatible with the components, soldering methods, and conformal coatings used in your specific application.
By following these guidelines, you can handle and store immersion silver finished PCBs properly, maintaining their quality and preserving their performance.
Constantly Problem for Immersion Silver PCB and How to Solve?
While immersion silver is a popular surface finish for PCBs, it can also present some common challenges. Here are a few common problems that can occur with immersion silver PCBs and potential solutions:
1.Silver tarnish:
Immersion silver is susceptible to tarnishing when exposed to air or certain environmental conditions. Tarnish can affect solderability and lead to poor solder joints. To address this issue, proper handling and storage of PCBs is essential. The use of anti-tarnish coatings or packaging materials can help prevent tarnish. Additionally, minimizing the exposure time between the silver finish application and subsequent assembly processes can reduce the risk of tarnishing.
2.Silver migration:
Silver migration refers to the unintended movement of silver ions across the PCB surface, leading to short circuits or electrical failures. This phenomenon can occur when there is moisture or contamination present on the PCB. To prevent silver migration, it is crucial to ensure proper cleanliness and moisture control during the manufacturing process. Thorough cleaning and drying of PCBs before immersion silver plating can help minimize the risk of migration.
3.Surface roughness or unevenness:
Immersion silver can sometimes result in a rough or uneven surface finish, which can impact solderability and component placement. This issue can be addressed by optimizing the immersion silver plating process parameters, such as bath composition, temperature, and immersion time. Proper control and monitoring of these parameters can help achieve a smooth and uniform silver surface.
4.Solderability issues:
While immersion silver generally provides good solderability, certain factors can affect the solderability of the finish. Contamination, oxidation, or inadequate flux activation can lead to poor wetting and weak solder joints. To ensure optimal solderability, it is important to follow proper storage and handling procedures for PCBs, use appropriate fluxes, and ensure proper reflow soldering profiles.
5.Compatibility with other surface finishes:
Immersion silver may not be compatible with certain surface finishes or processes. For example, it is not recommended to use immersion silver in combination with OSP (Organic Solderability Preservative) or certain solder mask materials. It is important to consider the compatibility of immersion silver with other finishes or processes in the PCB design and manufacturing stages.
Final Thoughts
The immersion silver surface finish stands as a testament to the relentless pursuit of excellence in PCB technology. Its remarkable conductivity, solderability, and compatibility with high-frequency applications have revolutionized the electronics industry. As the demand for faster, more reliable, and efficient PCBs continues to surge, immersion silver has emerged as a trusted ally, enabling engineers to unlock the full potential of their designs. With its ability to enhance signal integrity, improve thermal performance, and facilitate seamless assembly processes, immersion silver surface finish paves the way for a new era of advanced electronic applications.
In conclusion, immersion silver surface finish stands as a testament to the relentless pursuit of excellence in PCB technology. Its remarkable conductivity, solderability, and compatibility with high-frequency applications have revolutionized the electronics industry. As we continue to push the boundaries of innovation, immersion silver will undoubtedly play a pivotal role in shaping the future of electronic devices, empowering us to achieve new levels of performance, reliability, and efficiency.