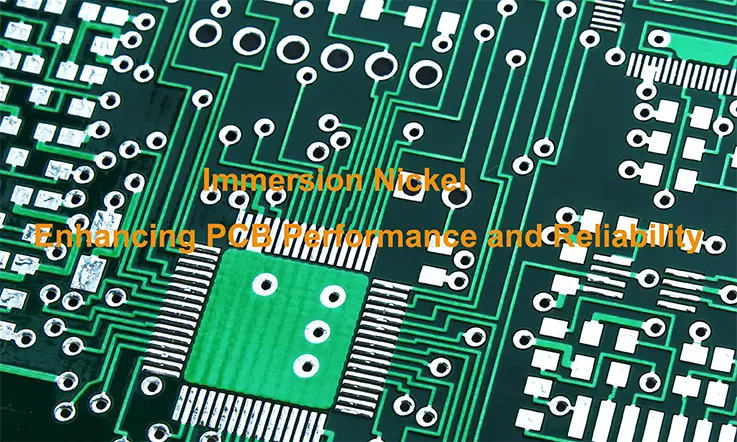
As a PCB engineer, one crucial aspect of our work is selecting the right surface finish for our printed circuit boards (PCBs). Among the various surface finish options available, immersion nickel stands out as a reliable and effective choice. With its unique properties and advantages, immersion nickel plays a vital role in enhancing the performance and reliability of PCBs in diverse electronic applications.
What Is Immersion Nickel?
Immersion nickel is a surface finish used in the manufacturing of printed circuit boards (PCBs). It involves depositing a thin layer of nickel onto the exposed copper surfaces of the PCB. The immersion nickel process is typically performed through an electroless plating technique, where the nickel is chemically deposited onto the copper without the need for an external electrical current.
The immersion nickel layer serves several purposes in PCB fabrication:
1. Corrosion Resistance: Nickel is known for its excellent corrosion resistance properties. The immersion nickel layer acts as a protective barrier, preventing oxidation and corrosion of the underlying copper traces. This helps to ensure the long-term reliability and performance of the PCB.
2. Solderability: The immersion nickel surface provides good solderability, allowing for reliable solder joint formation during the assembly process. It enhances the wetting and adhesion of solder to the PCB surface, which is crucial for proper electrical connections.
3. Flatness: Immersion nickel can contribute to the flatness and planarity of the PCB surface. This is particularly important when dealing with fine-pitch components or devices that require precise alignment during assembly.
4. Wire Bonding: Immersion nickel can also facilitate wire bonding processes. The nickel layer provides a suitable surface for wire bonding connections, ensuring proper bond strength and signal integrity.
5. Wear Resistance: Nickel has good wear resistance properties, making the immersion nickel layer durable and resistant to damage during handling or equipment assembly.
The thickness of the immersion nickel layer typically ranges from a few micrometers to tens of micrometers, depending on the specific requirements of the PCB design. The process parameters, such as the composition of the electroless nickel bath and immersion time, are carefully controlled to achieve the desired nickel thickness and properties.
Disadvantages of Immersion Nickel
While immersion nickel is a widely used surface finish in PCB design, it does have some disadvantages to consider:
1.Thickness Variation:
Immersion nickel can exhibit thickness variation across the PCB surface. This variation can impact the planarity of the PCB, especially on larger boards or areas with dense components. In extreme cases, the thickness variation may lead to solderability issues or uneven solder joint formation.
2.Limited Shelf Life:
Immersion nickel has a limited shelf life compared to some other surface finishes. Over time, the nickel layer can oxidize or become contaminated, affecting its solderability and overall performance. It is crucial to use fresh immersion nickel boards to ensure optimal results.
3.Potential for Black Pad Defect:
In certain cases, immersion nickel can be susceptible to a defect known as “black pad.” Black pad occurs when the nickel layer becomes brittle due to excessive phosphorus content or improper processing. This brittleness can lead to solder joint failures or reliability issues, particularly under thermal cycling or mechanical stress.
4.Solderability Concerns for Lead-Free Assembly:
Immersion nickel may pose challenges in lead-free assembly processes. The immersion nickel surface may not provide optimal wetting for lead-free solder alloys, resulting in poor solder joint formation or reliability. Additional measures, such as the use of flux or alternative surface finishes, may be required for successful lead-free assembly.
5.Cost:
While immersion nickel is generally considered a cost-effective surface finish, it can be more expensive compared to some other options like HASL. The additional processing steps involved in applying the immersion nickel layer contribute to the increased cost. Depending on the specific project budget, this cost difference may be a consideration.
6.Environmental Impact:
The electroless nickel bath used in the immersion nickel process contains chemical solutions that can be hazardous to the environment if not properly managed. Proper disposal and treatment of these chemicals are necessary to minimize environmental impact.
Factors to Consider When Choosing Immersion Nickel
When choosing immersion nickel as a PCB surface finish, there are several factors to consider. These factors can impact the performance, reliability, and cost of the finished PCB. Some of the key factors to consider include:
1.PCB Design Considerations:
Immersion nickel may have specific requirements or limitations based on the PCB design. Factors to consider include the complexity of the design, the type and thickness of copper traces, the presence of fine pitch components or BGAs, and any special requirements for solderability or electrical performance.
2.Performance Requirements:
Evaluate the performance requirements of the PCB and whether immersion nickel meets those requirements. Consider factors such as signal integrity, impedance control, high-frequency performance, thermal management, and reliability in different environmental conditions.
3.Cost and Availability:
Determine the cost-effectiveness of immersion nickel for your specific application. Compare the cost of the finish with other alternatives and consider factors such as material costs, processing costs, equipment requirements, and the availability of immersion nickel services or vendors.
4.Reliability and Durability:
Assess the reliability and durability of immersion nickel in the intended operating environment. Consider factors such as corrosion resistance, resistance to oxidation, resistance to wear and tear, and the ability to withstand thermal cycling or mechanical stress.
5.Industry Standards and Requirements:
Check if there are any specific industry standards or regulatory requirements that mandate or recommend the use of immersion nickel for your application. Compliance with these standards can be crucial for certain industries such as aerospace, automotive, medical, or telecommunications.
6.Compatibility with Assembly Processes:
Evaluate the compatibility of immersion nickel with the subsequent PCB assembly processes. Consider factors such as solderability, solder joint reliability, compatibility with lead-free soldering, and the impact on assembly yield or process complexity.
7.Future Scalability and Upgradability:
Consider the potential for future scalability or upgradability of the PCB design. Evaluate if immersion nickel allows for easy rework or repair, if it can accommodate future component changes or upgrades, and if it supports any future technology advancements or changes in the industry.
Factors Considered when Using Immersion Nickel Finish in PCB Design
When considering the use of an immersion nickel (EN) finish in PCB design, several factors should be taken into account. Here are some key considerations:
1. Surface planarity: Immersion nickel provides a flat and even surface for component placement. It is important to ensure that the PCB design has proper planarity to achieve good solder joint formation and minimize the risk of solder bridging or open connections.
2. Fine-pitch components: Immersion nickel is often preferred for PCBs with fine-pitch components, such as microprocessors or BGAs (Ball Grid Arrays). The flat and smooth surface of immersion nickel helps ensure precise component alignment and facilitates accurate solder ball placement.
3. Solder joint reliability: Immersion nickel provides good solderability and solder joint durability. However, it’s essential to consider the specific requirements of your application. If your design demands high-reliability solder joints, such as in aerospace or automotive electronics, additional measures like thicker nickel plating or selective gold plating on critical areas may be necessary.
4. Corrosion resistance: Immersion nickel offers excellent corrosion resistance, protecting the copper surfaces from oxidation. This is particularly important if the PCB will be exposed to harsh environments or if it requires a long lifespan. Consider the operating conditions and potential exposure to moisture, humidity, or chemical agents when selecting immersion nickel as the surface finish.
5. Contact resistance: Immersion nickel has a relatively low contact resistance compared to other surface finishes. This makes it suitable for applications where electrical conductivity is critical, such as high-frequency circuits or RF (Radio Frequency) designs. However, it’s important to ensure that the nickel thickness is sufficient to maintain low contact resistance over the expected lifespan of the PCB.
6. Compatibility with assembly processes: Immersion nickel is compatible with various assembly processes, including soldering, wire bonding, and press-fit connectors. Consider the specific assembly methods planned for your PCB design and ensure that the immersion nickel finish is suitable for those processes.
7. Cost considerations: The cost of immersion nickel as a surface finish can vary depending on factors such as board size, complexity, and volume. Evaluate the cost implications and compare them with other surface finish options to determine the most cost-effective solution for your project.
By considering these factors, you can make an informed decision about whether immersion nickel is the appropriate surface finish for your PCB design, taking into account the specific requirements of your application and the desired performance characteristics.
Comparison with Other Surface Finishes
When comparing immersion nickel finish with other surface finishes commonly used in PCB design, several factors should be considered. Here’s a comparison with some popular surface finishes:
1. HASL (Hot Air Solder Leveling): HASL is a cost-effective surface finish that involves coating the PCB surface with a layer of molten solder, which is then leveled using hot air. Compared to immersion nickel, HASL has lower flatness and solderability. It is not suitable for fine-pitch components due to the potential for solder bridging. However, HASL is still widely used for non-complex and non-critical applications due to its affordability.
2. OSP (Organic Solderability Preservative): OSP is a thin organic coating applied to the bare copper surface of the PCB to protect it from oxidation. OSP offers good solderability and flatness, making it suitable for fine-pitch components. However, OSP has limited shelf life and can be sensitive to environmental conditions. It is not as durable as immersion nickel in terms of corrosion resistance and wear resistance.
3. ENIG (Electroless Nickel Immersion Gold): ENIG, also known as immersion gold, is a two-layer finish similar to immersion nickel. The primary difference is that ENIG uses a layer of electroless nickel followed by a layer of immersion gold. ENIG provides excellent solderability, flatness, and corrosion resistance, making it suitable for a wide range of applications. However, ENIG is generally more expensive than immersion nickel and may not be necessary for all PCB designs.
4. OSP + ENIG: Some PCB designs may opt for a combination of OSP and ENIG finishes. This approach involves applying OSP on the copper traces and immersion gold on the exposed pads. OSP provides a protective layer for the copper and ENIG offers superior solderability and flatness on the pads. This combination can provide the benefits of both finishes and may be cost-effective for certain applications.
Overall, the choice of surface finish depends on the specific requirements of the PCB design, including factors such as cost, solderability, flatness, corrosion resistance, and environmental considerations. Immersion nickel offers a balance between cost-effectiveness, durability, and solderability, making it a popular choice for many applications. However, it is essential to evaluate the specific needs of the PCB design and consult with PCB manufacturers or experts to determine the most suitable surface finish.
In Conclusion
Immersion nickel is an invaluable surface finish for PCB engineers, offering numerous advantages for enhanced performance and reliability. Its corrosion resistance, solderability, flatness, and durability make it a popular choice in various electronic applications. However, it is essential to be aware of potential challenges such as thickness variation, black pad defect, and solderability concerns for lead-free assembly. By understanding these factors and working closely with PCB manufacturers, we can harness the benefits of immersion nickel while mitigating any drawbacks.