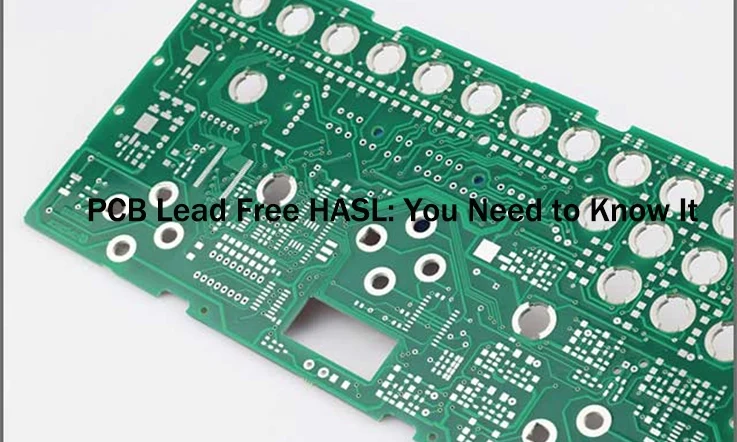
As a leading PCB manufacturer, we understand the critical role that surface finishes play in ensuring the performance, reliability, and environmental compliance of printed circuit boards (PCBs). In this article, we delve into the world of surface finishes, focusing specifically on the highly sought-after lead-free HASL (Hot Air Solder Leveling) process.
With its ability to deliver reliable soldering and meet stringent environmental regulations, lead-free HASL has become a preferred choice for various industries. Join us as we explore the benefits, applications, and considerations associated with this surface finish, shedding light on why it has gained prominence in the PCB manufacturing landscape.
What Is PCB Lead Free HASL Surface Finish?
Lead-Free HASL (Hot Air Solder Leveling) is a surface finish used in printed circuit boards (PCBs). It is an alternative to the traditional HASL process, which involved the use of lead-based solder. Lead-Free HASL was developed as a response to environmental concerns regarding the use of lead in electronics manufacturing.
Lead-Free HASL involves applying a layer of solder paste onto the PCB’s copper pads. The PCB is then subjected to a high-temperature reflow process, where the solder paste melts and forms a smooth, even layer on the copper surfaces. After that, excess solder is removed using hot air knives, leaving behind a flat, solder-coated surface.
The lead-free solder used in this process typically consists of a mixture of tin, silver, and copper (Sn-Ag-Cu). This solder alloy provides good solderability and ensures reliable solder joints. Lead-Free HASL is widely used in various applications, including consumer electronics, automotive electronics, telecommunications, and industrial equipment.
One important thing to note is that Lead-Free HASL may have certain disadvantages compared to other surface finishes. It can be susceptible to uneven surface finishes and solder bridging between closely spaced components. Additionally, the thickness of the solder layer can vary, which may affect the flatness of the PCB surface. Therefore, it’s important to consider the specific requirements of your application and consult with your PCB manufacturer to determine if Lead-Free HASL is suitable for your needs.
Composition and Characteristics of lead-free HASL
Lead-free HASL (Hot Air Solder Leveling) is a surface finish used in PCB (Printed Circuit Board) manufacturing that replaces the traditional lead-based HASL process. It involves the application of a solder coating on the PCB surface to facilitate soldering of electronic components. The composition and characteristics of lead-free HASL can vary depending on the specific formulation used by manufacturers. However, here are some common aspects:
Solder Alloy: Lead-free HASL utilizes solder alloys that are free from lead (Pb). Common lead-free solder alloys used in HASL include:
Tin-Silver-Copper (Sn-Ag-Cu): This alloy is one of the most widely used lead-free solder alloys and offers good mechanical strength, thermal conductivity, and reliability.
Tin-Copper (Sn-Cu): This alloy is another common choice for lead-free HASL and provides good solderability and thermal fatigue resistance.
Flux: A flux is typically applied during the HASL process to remove oxides from the PCB surface and promote solder wetting. Lead-free HASL fluxes are formulated to work specifically with lead-free solder alloys and ensure proper solder coverage. They are designed to provide good solderability and minimize defects such as solder bridging or insufficient wetting.
Thickness: The thickness of the lead-free HASL coating can vary depending on the specific requirements of the PCB design and application. Typically, the solder coating thickness ranges from a few micrometers to tens of micrometers.
Characteristics:
Solderability: Lead-free HASL provides good solderability, allowing for reliable solder joint formation between the PCB and electronic components.
Thermal Resistance: Lead-free solder alloys used in HASL exhibit good thermal resistance, ensuring the solder joints can withstand temperature variations during operation.
RoHS Compliance: Lead-free HASL is formulated to meet the requirements of RoHS regulations, ensuring compliance with restricted substances such as lead.
It’s important to note that the specific composition and characteristics of lead-free HASL can vary between manufacturers and may be optimized based on factors such as the PCB design, assembly process, and desired performance criteria.
Electrical performance of lead-free HASL
The electrical performance of lead-free HASL (Hot Air Solder Leveling) is generally comparable to that of traditional lead-based HASL, provided that the process is properly executed and the PCB design meets the required electrical specifications. Here are some key aspects related to the electrical performance of lead-free HASL:
1. Conductivity: Lead-free HASL coatings typically use solder alloys that have good electrical conductivity. The most commonly used lead-free solder alloys, such as Sn-Ag-Cu or Sn-Cu, offer conductivity levels similar to or better than traditional lead-based solder alloys. This ensures efficient flow of electrical current through the solder joints and the PCB traces.
2. Impedance Control: Lead-free HASL does not significantly affect the impedance characteristics of PCB traces when applied within the specified thickness range. However, it’s important to consider the thickness of the solder coating and its impact on the overall impedance requirements of high-speed signal traces. Thicker coatings may slightly alter the impedance, which should be accounted for during the PCB design stage.
3. Signal Integrity: Properly soldered lead-free HASL connections can maintain good signal integrity. The solder joints formed through the HASL process should provide low resistance, low capacitance, and low inductance connections, which are essential for maintaining the desired electrical performance of the PCB.
4. High-Frequency Performance: Lead-free HASL can support high-frequency signal transmission, provided that the PCB design and layout are appropriately optimized for high-frequency applications. Factors such as controlled impedance, signal routing, and proper grounding techniques play a crucial role in ensuring high-frequency performance.
5. Reliability of Electrical Connections: The electrical connections formed by lead-free HASL should be reliable and capable of withstanding the expected operational conditions. Proper solder wetting and adhesion between the solder coating and the PCB pads or component leads are critical for ensuring reliable electrical connections over the long term.
It’s worth noting that the electrical performance of lead-free HASL can also be influenced by other factors such as the PCB material, trace routing, component placement, and the overall design considerations. It’s important to carefully evaluate the specific electrical requirements of the PCB and consider the impact of the chosen surface finish on its electrical performance.
So Why Lead-free HASL is Necessary?
Lead-free HASL (Hot Air Solder Leveling) is necessary due to environmental and health concerns associated with the use of lead in electronic products. Lead is a toxic substance that poses risks to human health and the environment, particularly during manufacturing, use, and disposal of electronic devices.
The transition to lead-free electronics was primarily driven by the implementation of regulations such as the RoHS (Restriction of Hazardous Substances) directive. RoHS restricts the use of certain hazardous substances, including lead, in electrical and electronic equipment sold in the European Union and other regions that have adopted similar regulations.
By using lead-free HASL, manufacturers can comply with these regulations and ensure that their products are safer for both consumers and the environment. Lead-free HASL involves the use of alternative materials, such as lead-free solder alloys, to achieve a solder coating on the PCB surface.
In addition to regulatory compliance, lead-free HASL offers several advantages. It provides improved solder joint reliability, as lead-free solder alloys have comparable or better mechanical properties than traditional lead-based solders. Lead-free HASL also promotes better long-term reliability, as it reduces the risk of tin whisker formation, which can lead to electrical shorts in electronic components.
Precautions for Lead-Free HASL in PCB Manufacturing
When using lead-free HASL (Hot Air Solder Leveling) as a surface finish in PCB manufacturing, it is important to take certain precautions to ensure optimal results and product reliability. Here are some key precautions to consider:
1. Material Compatibility: Verify the compatibility of the PCB materials with lead-free HASL. Some materials, such as high-temperature laminates or certain substrates, may not be suitable for this process. Consult with your PCB manufacturer or material supplier to ensure compatibility.
2. PCB Design Considerations: Design the PCB with appropriate pad sizes and spacing to accommodate the lead-free HASL process. Ensure that the pads are large enough to allow sufficient solder coverage and avoid solder bridging between adjacent pads.
3. Thermal Considerations: Lead-free HASL involves subjecting the PCB to high temperatures during the solder leveling process. Consider the thermal impact on sensitive components, such as heat-sensitive ICs or components with limited temperature tolerance. Implement thermal management techniques, such as heat sinks or thermal vias, if necessary.
4. Component Selection: Select components that are compatible with lead-free soldering. Some components may require higher reflow temperatures or have specific soldering requirements. Consult the component datasheets or manufacturers for recommended soldering profiles and compatibility with lead-free solder.
5. PCB Cleaning: Properly clean the PCB after lead-free HASL to remove flux residues and any contaminants. Residual flux can lead to reliability issues or corrosion over time. Use appropriate cleaning methods, such as aqueous or solvent-based cleaning, to ensure thorough removal of flux residues.
6. Handling and Storage: Handle lead-free HASL PCBs with care to avoid physical damage to the solder joints. Store the PCBs in appropriate conditions to prevent exposure to moisture, humidity, or extreme temperatures, which can degrade the solderability and long-term reliability of the surface finish.
7. Quality Control and Testing: Implement rigorous quality control measures throughout the manufacturing process to monitor the quality and reliability of lead-free HASL PCBs. Conduct electrical testing, solderability testing, and reliability assessments to ensure compliance with industry standards and customer requirements.
By following these precautions, you can maximize the benefits of lead-free HASL while ensuring the reliability and performance of your PCBs.
Difference between Lead-free HASL and traditional HASL for PCBs
The main difference between Lead-Free HASL and traditional HASL for PCBs lies in the composition of the solder used in the process and the environmental impact.
1.Composition:
Traditional HASL uses a lead-based solder alloy, typically containing a high percentage of lead (Pb). Lead is known to be toxic and harmful to the environment. In contrast, Lead-Free HASL uses a solder alloy that is free from lead. The most common lead-free solder alloy used in Lead-Free HASL is a mixture of tin, silver, and copper (Sn-Ag-Cu).
2.Environmental Impact:
The use of lead in electronics manufacturing has raised concerns due to its harmful effects on human health and the environment. Lead-Free HASL was developed as a more environmentally friendly alternative to traditional HASL. By eliminating lead from the solder alloy, Lead-Free HASL helps reduce the environmental impact associated with electronics manufacturing and disposal.
3.Solderability:
Lead-Free HASL generally provides comparable solderability to traditional HASL. The solder alloy used in Lead-Free HASL, such as Sn-Ag-Cu, offers good wetting and bonding properties, ensuring reliable solder joints between components and PCB pads.
4.Thermal Stress:
Lead-Free HASL may have slightly higher thermal stress compared to traditional HASL. This is because lead-free solder alloys have a higher melting point than lead-based solder. The higher thermal stress can potentially affect the long-term reliability of the solder joints, especially in applications subject to extreme temperature cycling.
5.Surface Finish:
The appearance of the surface finish may differ between Lead-Free HASL and traditional HASL. Lead-Free HASL tends to have a slightly duller appearance compared to the shiny appearance of traditional HASL. This visual difference is due to the different solder alloy compositions.
When choosing between Lead-Free HASL and traditional HASL, it’s important to consider the specific requirements of your application, such as environmental regulations, solderability, thermal stress, and aesthetic preferences. Consulting with your PCB manufacturer can help you determine the most suitable surface finish for your needs.
Industries and Applications Suitable for Lead-free HASL
Lead-free HASL (Hot Air Solder Leveling) is widely used in various industries and applications where reliable soldering and environmental compliance are important. Some industries and applications suitable for lead-free HASL include:
1.Consumer Electronics:
Lead-free HASL is commonly used in consumer electronics products such as smartphones, tablets, laptops, gaming consoles, and home appliances. These products often require high-volume manufacturing and demand environmentally friendly solutions.
2.Automotive Electronics:
Lead-free HASL is suitable for automotive electronics applications, including engine control units, infotainment systems, dashboard electronics, and advanced driver assistance systems (ADAS). The automotive industry has strict requirements for reliability, temperature resistance, and compliance with environmental regulations.
3.Industrial Electronics:
Lead-free HASL is used in industrial electronics applications such as industrial control systems, automation equipment, power supplies, and instrumentation. These applications often require robust and reliable solder joints that can withstand harsh operating conditions.
4.Telecommunications:
Lead-free HASL is employed in telecommunications equipment, including routers, switches, base stations, and network infrastructure components. These applications require high-speed signal transmission, good thermal performance, and long-term reliability.
5.Medical Devices:
Lead-free HASL is suitable for medical device applications, including diagnostic equipment, patient monitoring systems, and implantable devices. These applications often require high levels of reliability, biocompatibility, and compliance with medical regulations.
6.Aerospace and Defense:
Lead-free HASL can be used in aerospace and defense applications, such as avionics, satellites, radar systems, and military electronics. These applications demand high reliability, resistance to extreme temperatures, and compliance with stringent industry standards.
7.Industrial Control and Power Electronics:
Lead-free HASL is commonly used in industrial control systems, power electronics, motor drives, and renewable energy systems. These applications require reliable solder joints, good thermal dissipation, and compliance with industry standards.
In Conclusion
The surface finish of PCBs holds immense significance in the realm of electronic manufacturing. Lead-free HASL stands out as a surface finish that combines reliable soldering, environmental compliance, and broad applicability across diverse industries. Its ability to provide excellent electrical performance, withstand harsh operating conditions, and meet stringent regulatory requirements make it an attractive choice for consumer electronics, automotive, industrial, telecommunications, medical, aerospace, and defense applications.
As a PCB manufacturer committed to delivering high-quality and environmentally friendly solutions, we recognize the value of lead-free HASL and its role in ensuring the success of your electronic designs. Trust us to provide you with superior PCBs featuring lead-free HASL surface finish, enabling you to achieve exceptional performance, reliability, and compliance with the ever-evolving industry standards.