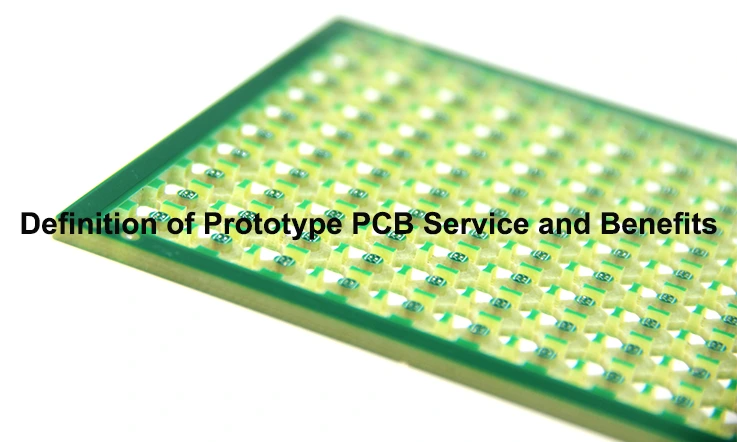
If you’ve ever worked on a PCB project, you know the importance of getting things right the first time—well, almost. That’s where prototype PCB services come into play, acting as a kind of rehearsal for your final product. Think of it like testing out your brand-new car in a safe space before hitting the highway—better to spot those bumps early, right?
In this guide, we’ll dive deep into why prototype PCBs are not just useful but downright essential to any successful project. From saving you a boatload of cash to making sure you avoid hair-pulling moments later down the line, this article is packed with insights you won’t want to miss.
What Is a Prototype PCB?
A prototype PCB (Printed Circuit Board) is essentially the trial version of your final board design. It’s like baking a cake and testing the batter before you toss it in the oven. In essence, you’re checking the flavors, or in this case, the circuit performance, to ensure your final design works just as planned.
Prototyping to Refine PCB Designs
Prototyping is a critical stage in PCB development, giving engineers the chance to iron out the kinks before mass production. Here’s what gets evaluated during this process:
Signal Integrity
You want your signals to travel smoothly across the board, right? Signal integrity testing ensures that there’s no interference or delay, so those signals hit their mark every time.
Thermal Management
Heat is the silent enemy in PCB design. During prototyping, engineers check how the board handles the heat under various loads, ensuring it doesn’t overheat when things get real.
Electrical Functionality
Does your board work the way it’s supposed to? Electrical functionality tests give you the thumbs-up (or not) before production ramps up. You definitely don’t want to discover issues after mass production is already underway.
By prototyping, you can reduce risks, refine designs, and ensure that the final product runs like a well-oiled machine.
Types of Prototype PCB Services
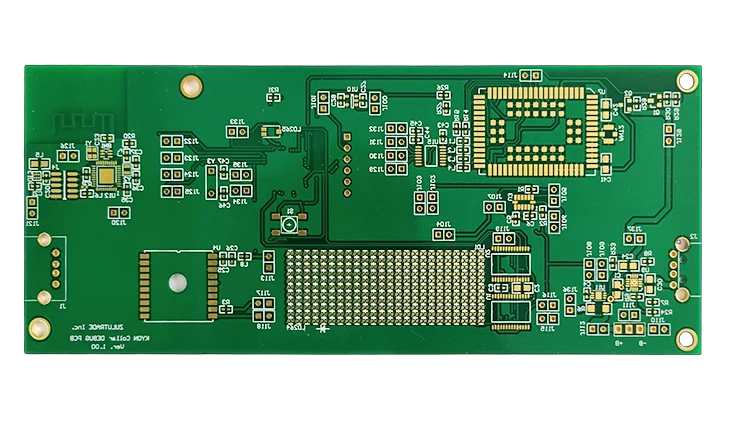
When you’re diving into PCB design, understanding the different types of prototype PCB services is key to picking the right solution for your project. From early-stage concept boards to production-ready prototypes, each service type offers unique advantages that align with specific goals, timelines, and requirements.
Conceptual Prototypes
A conceptual prototype is an early version of the PCB, designed primarily for internal testing. This stage is all about proof of concept—you’re focusing on the basic functionality of the design without worrying too much about performance or scalability. Engineers use this type of service to quickly see if their design works in theory.
Who It’s For:
Conceptual prototypes are ideal for engineers who are still in the brainstorming phase. You don’t need all the bells and whistles—just a functional board that gives you a taste of what’s to come.
Key Benefit:
Speed. You’re looking at a fast, low-cost way to test ideas. If you’re in a pinch to validate your design, this service gives you a way to move forward without sinking time or money into full production.
Functional Prototypes
Moving a step beyond conceptual, functional prototypes are built to simulate real-world conditions. This service is aimed at verifying both electrical performance and signal integrity, ensuring the board operates within your design’s parameters. Functional prototypes come closer to the final product but are still used for internal testing.
Who It’s For:
Functional prototypes cater to engineers and designers looking to refine their designs. If you’ve already nailed down your concept but want to put it through its paces before mass production, this is your go-to.
Key Benefit:
By focusing on electrical performance and signal integrity, functional prototypes allow you to stress-test your board without the hefty price tag of a full production run. They help reduce rework later, making sure your design is solid before you go big.
Visual Prototypes
A visual prototype doesn’t necessarily have to work; it just needs to look the part. These prototypes are often used for demonstration purposes, especially in presentations or pitches where the focus is more on the form factor than functionality. If you want to show off the aesthetic or layout of your board, a visual prototype is what you need.
Who It’s For:
Visual prototypes are great for teams working on product design or marketing presentations. If you’re gearing up for a client demo or want to get a physical feel for how your PCB will fit into an enclosure, this service has you covered.
Key Benefit:
This type of service lets you get hands-on with the design without worrying about electrical performance. It’s all about appearance and layout, perfect for early-stage visual approval.
Production-Ready Prototypes
Production-ready prototypes are your final stop before mass manufacturing. These boards are fully functional and ready for full-scale testing under real-world conditions. At this point, you’ve already ironed out any design flaws, and now you’re putting the final version of your PCB through rigorous testing to ensure it holds up under stress.
Who It’s For:
These prototypes are for seasoned engineers and manufacturers preparing for the final production run. If you’re ready to scale and want to make sure there are no surprises during full production, a production-ready prototype is your safety net.
Key Benefit:
Full functionality with no compromises. This prototype matches your mass production design exactly, letting you confirm every aspect of your board before committing to a large run.
One-Off Prototyping Services
Sometimes, you just need a single board for testing or demonstration purposes. One-off prototyping services cater to that need by providing a custom PCB for one-time use. Whether it’s a unique demo for a client or a special test for a new design, this service ensures you get exactly what you need.
Who It’s For:
One-off services are perfect for companies that need something ultra-specific without committing to a large quantity. Whether you’re building a prototype for a niche application or creating a custom demo board, this service gives you the flexibility you need.
Key Benefit:
Customization at its finest. This service allows for tailored solutions without the hassle of mass production. It’s ideal for niche applications or one-time demos where flexibility is key.
Multi-Layer Prototyping
Multi-layer prototyping services focus on creating boards with several layers of circuitry. As devices become more complex, the demand for multi-layer PCBs has skyrocketed, especially in industries like telecommunications, aerospace, and automotive.
Who It’s For:
If you’re dealing with high-speed, high-frequency applications, or you need to reduce board size, multi-layer prototyping is for you. This service caters to industries that require compact designs with enhanced functionality.
Key Benefit:
Complex designs with maximum functionality. Multi-layer boards are perfect for saving space and increasing performance without sacrificing quality.
Turnkey Prototyping Services
Turnkey prototyping services take care of everything from PCB design to assembly. These services offer end-to-end solutions, handling every aspect of the process, so you don’t have to juggle multiple suppliers.
Who It’s For:
Busy design teams and manufacturers looking for a hassle-free solution. If you’re juggling tight deadlines and can’t afford to manage multiple vendors, turnkey prototyping takes the burden off your plate.
Key Benefit:
Efficiency and convenience. By offering a one-stop-shop solution, turnkey services allow you to focus on design while leaving the manufacturing logistics to the experts.
Here is a data table that summarizes the types of Prototype PCB Services discussed earlier:
Service Type | Description | Ideal For | Key Benefit |
Conceptual Prototype | Early design version focused on basic functionality. | Engineers in brainstorming phase. | Fast and low-cost validation of ideas. |
Functional Prototype | Simulates real-world conditions, verifies performance. | Engineers refining designs before mass production. | Ensures design performs within set parameters. |
Visual Prototype | Aesthetically focused, non-functional board for presentation. | Teams working on product design or marketing. | Highlights appearance and layout. |
Production-Ready Prototype | Fully functional board for rigorous, real-world testing. | Engineers preparing for mass manufacturing. | Matches the final design for pre-production. |
One-Off Prototyping | Custom PCB for specific one-time use cases. | Companies needing specialized or niche applications. | Offers tailored solutions without mass production. |
Multi-Layer Prototype | PCBs with multiple layers for more complex applications. | High-speed, high-frequency designs requiring compactness. | Combines functionality and space-saving design. |
Turnkey Prototyping | End-to-end service, handling design to assembly. | Teams needing a hassle-free, all-in-one solution. | Streamlines the entire prototyping process. |
Which Prototype PCB Service Fits Your Needs?
With a variety of options, it’s vital to choose the right service based on your project’s phase and objectives. Whether you’re just starting with a concept or prepping for a full-scale launch, there’s a prototyping service that aligns with your timeline, budget, and design complexity. Keep in mind that the right service ensures smoother production and fewer headaches later on—so choose wisely, and don’t be afraid to ask for what you need.
Why You Need Prototype PCB Services Right Now?
Ready to dive into your next project? Don’t go in blind. Reach out to a trusted prototype PCB service provider and get the ball rolling on a smoother, faster, and more reliable design process.
Remember, every great product started with a prototype!
Benefits of Prototype PCB Services
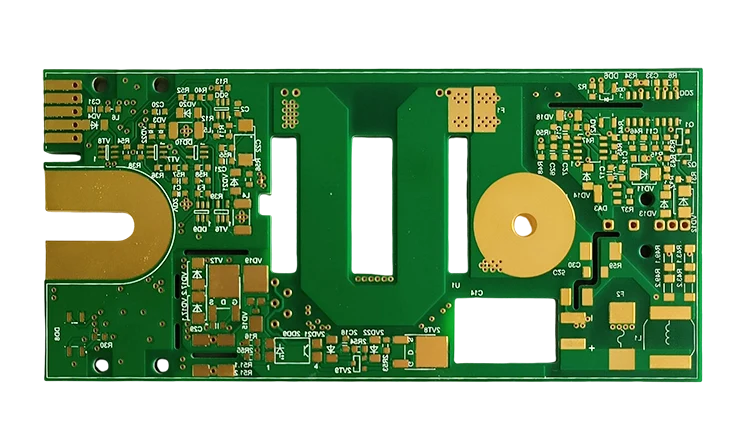
When you’re staring down the barrel of an expensive production run, taking a detour into prototyping land can save you more than a few headaches—and cash. So, why are prototype PCBs such a big deal?Here are some key reasons why prototype PCB services make all the difference.
Faster Design Iteration
In today’s fast-paced world, there’s no room for messing around. Prototype PCBs let you run multiple design iterations quickly and efficiently. This is especially useful if you’re working with complex designs or tight deadlines. Imagine needing to tweak a circuit at the eleventh hour—prototypes help you do just that without putting your whole project in jeopardy.
Cost-Effective Testing
Let’s get real—producing PCBs isn’t cheap. But throwing down stacks of cash on a final run only to discover something went sideways? That’s a nightmare. Prototyping allows you to test your design in a real-world setting without having to commit to full-scale production. It’s like sampling the goods before buying in bulk.
Error Detection Early On
Here’s a tough pill to swallow: no matter how skilled you are, design errors happen. Instead of waiting until mass production to discover an issue that could throw your entire project off-track, prototypes help you find these issues upfront. Picture this: it’s like spotting a crack in the foundation before you build the whole house.
Optimizing PCB Performance
Prototyping allows you to refine every aspect of your design. Engineers can tweak and test things like signal integrity, power distribution, and thermal management to optimize the board’s performance. You’re not just aiming for “good enough” here—you’re fine-tuning the product until it works like a dream.
If you can nail these elements during prototyping, your production runs will go off without a hitch. You’ll end up with a polished product ready for the spotlight.
Speeding Up Time-to-Market
Speed is the name of the game in electronics, and a quick turnaround can give you the competitive edge. Prototype PCB services allow for rapid design iterations, testing, and finalization. This shaves weeks—or even months—off your project’s timeline.
Fast prototyping means you can iterate your designs, test them, and make adjustments in no time. That’s how you take your product from concept to shelf at lightning speed. And in this industry, being first to market is huge.
Cost-Efficiency and Risk Reduction
Catching errors early with prototypes also saves money. Let’s face it: mistakes during mass production can cost you big. Fixing a design flaw after you’ve manufactured thousands of units is a financial nightmare. Prototypes help you catch and fix those mistakes when the stakes—and costs—are lower.
By refining your designs during the prototyping phase, you drastically reduce the risk of costly reworks down the line. It’s like finding the loose threads before the whole thing unravels.
The PCB Prototyping Process: Step-by-Step Breakdown
The prototype PCB process can be a bit like assembling a jigsaw puzzle—lots of moving parts, but when done right, the pieces fit together perfectly.
Step 1: Design and Schematic Review
First up, your design needs to be rock solid. Any errors here can ripple through the entire production cycle. It’s like building a skyscraper—get the blueprints wrong, and the whole thing comes tumbling down. Designers use specialized software (think Eagle, Altium, or KiCad) to ensure everything lines up before moving forward.
Step 2: Prototype Fabrication
Next, it’s off to the fabricators who bring your design to life. Depending on your needs, they’ll either use CNC milling or other manufacturing techniques to produce your prototype PCB. This is like putting together a test model of your final product—it’s all about ensuring the design fits and functions as planned.
Step 3: Testing and Validation
Once you’ve got the prototype in hand, it’s time to put it through its paces. Think of this as your circuit’s trial by fire. Testing ensures that every aspect of your design—from thermal management to electrical signal integrity—works as intended. If things go sideways, this is your opportunity to fix those issues without throwing money down the drain.
Prototype vs. Mass Production: Why Prototyping Is Worth the Investment?
Here’s the thing—mass production without a prototype is like diving headfirst into a pool without knowing how deep it is. Sure, you could get lucky and everything might go off without a hitch. But the more likely scenario is that something goes wrong, and fixing it mid-production is not only expensive but also stressful as hell.
Cost Comparison
Prototyping isn’t just a nice-to-have—it’s a money-saver. Imagine paying for 10,000 PCBs only to discover a design flaw that forces a redesign. With prototyping, you catch those errors upfront and fix them without having to eat the cost of scrapped boards. And trust me, you don’t want to be that person in the boardroom explaining why the budget just went out the window.
Flexibility in Design Changes
The beauty of prototypes is the flexibility they offer. Want to tweak a design? Go for it! Need to optimize performance? No problem. With prototypes, you’ve got the breathing room to make adjustments before it’s too late.
Common Challenges in Prototype PCB Development
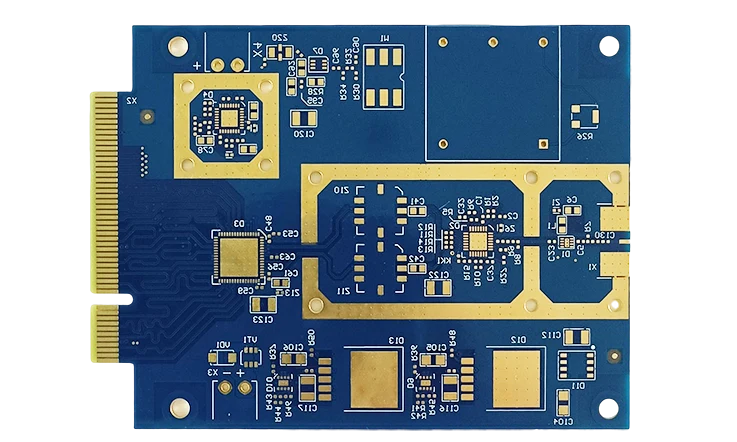
Even with all the benefits, prototyping isn’t without its hurdles. Knowing these challenges upfront can help you navigate the process more smoothly.
Challenge 1: Time Constraints
Deadlines in PCB design can be brutal. Prototypes speed things up, but managing multiple design iterations while racing against the clock is no easy feat. This is why teaming up with a fast and reliable PCB prototype manufacturer is essential. A solid partner helps you avoid bottlenecks, keeping the project moving at full speed—no one likes being stuck in neutral when the finish line is in sight.
Challenge 2: Material Selection
Choosing the right materials for your prototype is like picking the right fabric for a custom suit—balance is everything. You want materials that mimic the performance of your final product, but they shouldn’t burn through your budget. The trick is finding that sweet spot between cost and quality. A trusted prototype service can help guide your decision, so you’re not stuck second-guessing every material choice.
The Future of Prototype PCB Services
PCB prototyping has taken a leap forward with new materials like FR-4 and high-Tg laminates. These materials aren’t just tough and heat-resistant—they’re lighter, more durable, and give you that performance edge you need in today’s high-power applications. FR-4 remains a favorite for its solid balance of price and durability, while high-Tg laminates keep things running cool when dealing with more heat-sensitive designs. If you’re thinking about pushing your design to the next level, these materials are a game-changer.
As technology advances, so do PCB prototyping methods. Here’s a look at some of the exciting trends that are shaping the future of the industry.
3D Printing for PCBs
One of the most groundbreaking advancements in PCB prototyping is the use of 3D printing technology. This innovation allows for faster production times and more complex designs. Imagine printing a functional circuit board right from your desktop—how cool is that?
With 3D printing, the lead time for a working prototype shrinks dramatically. No more waiting around for traditional manufacturing—3D printing gets you a working board much quicker. Want to experiment with unique layouts? 3D printing lets you design beyond the limitations of traditional manufacturing, allowing for complex shapes and intricate patterns. Need to make a tweak? No problem. With 3D printing, adjustments can be made in real-time, cutting out the need for additional manufacturing runs.
Integration with IoT Devices
Welcome to the era of IoT (Internet of Things), where PCBs have to do more in less space. The demand for smaller, power-efficient boards is skyrocketing, which means prototyping has to get smarter, faster, and more complex. IoT integration is driving innovation, requiring designs that support multi-functional applications, all while keeping power consumption low. This shift is pushing designers to think outside the box and create smarter, more connected solutions in record time. If you’re working on an IoT device, the pressure is on, but the tools are there to help you shine.
As IoT devices become more ubiquitous, the demand for faster, more flexible PCB prototyping has skyrocketed. Prototyping services that can handle these complex, connected devices will be at the forefront of the industry in the coming years.
How to Choose the Right Prototype PCB Service for Your Needs?
Now that you know the ins and outs of prototyping, it’s time to pick the right service for your project. Here’s what you should look out for:
Experience in Your Industry
Not every PCB manufacturer is built for your sector. If you’re designing for aerospace, automotive, or consumer electronics, you need someone who knows the ropes. A provider with industry expertise can better predict challenges and fine-tune designs to meet specific standards.
Turnaround Time
How fast can they deliver? In electronics, you can’t afford to wait around. A provider that offers fast turnaround times without sacrificing quality keeps you ahead of the competition. Let’s be real: speed matters, but sloppy work can set you back even more. Look for a provider who can balance both.
Customization Options
You want flexibility, right? Whether you’re testing out a new material or playing with complex designs, you need a partner who offers customized solutions. The best PCB services are those that don’t try to fit you into a box but instead work with you to create the best prototype for your specific needs.
Wrapping It All Up: Why Prototype PCBs Are a Must for Every Designer?
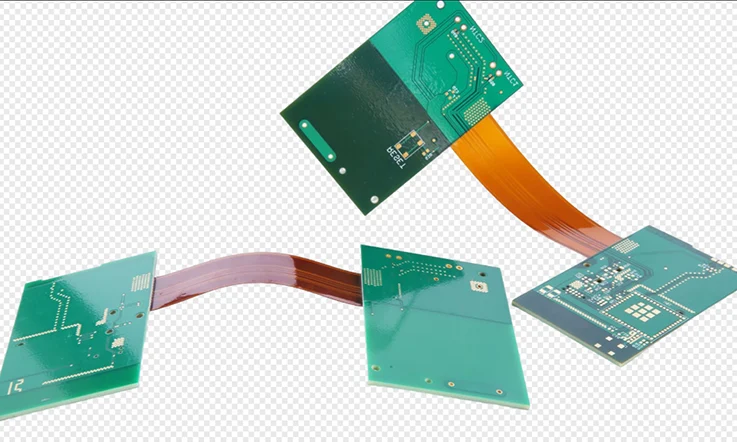
In the end, prototype PCB services aren’t just a nice-to-have—they’re essential. They save you time, money, and headaches down the line. Whether you’re a newbie to the world of PCB design or a seasoned pro, prototyping lets you test, tweak, and perfect your designs without blowing your budget.
So, if you’re ready to take your next project to the next level, don’t hesitate—get that prototype going, test your ideas, and avoid costly mistakes when it matters most.
Ready to take your design from concept to reality? Don’t let a minor mistake trip you up when you can test your designs upfront. Reach out today to learn how our PCB prototype services can help you avoid those expensive pitfalls and hit the ground running with confidence.
FAQs
What is the typical cost of a PCB prototype?
The cost varies based on size, material, and complexity, but ranges from $50 to $500 for a basic prototype.
How long does PCB prototyping take?
Turnaround time can be as quick as 24 hours, but usually takes about 5 to 7 days depending on the complexity.
What are the best materials for a prototype PCB?
Materials like FR-4, polyimide, and high-Tg laminates are popular for their durability and performance during prototyping.
Can I Make Changes to My Design After Receiving the Prototype?
Yes, one of the biggest advantages of prototyping is the ability to revise your design after testing. Once you receive the prototype, you can identify issues or improvements and make changes before moving forward with full-scale production.
How Many Iterations of a Prototype Are Typically Needed?
The number of iterations depends on the complexity of the design and how many tweaks are necessary after each test. Simple designs may need just one or two prototypes, while more complex, multi-layered PCBs could require several iterations to get everything just right.
What design software is required to design prototype PCB?
Designing prototype PCBs requires specialized software to handle schematic capture, PCB layout, simulation, and verification. Some of the most popular PCB design tools include:
●Altium Designer – Comprehensive PCB design and layout tool.
●Eagle – Known for its user-friendly interface and large library.
●KiCad – Open-source PCB design software for beginners and professionals.
●OrCAD – Ideal for complex circuit simulations and analysis.
●DipTrace – Offers intuitive tools for schematic capture and PCB layout.
Each software offers distinct features based on design complexity, budget, and user experience.