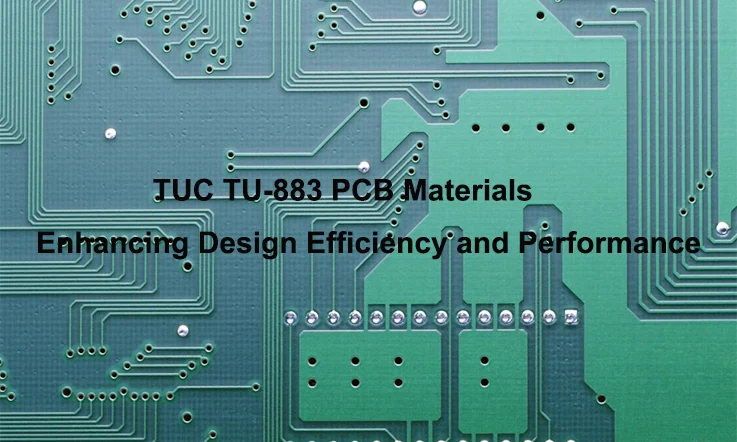
As a PCB manufacturer, the choice of materials is crucial to deliver high-quality, reliable, and efficient PCBs to meet the demands of the industry. TUC TU-883 PCB materials offer a range of exceptional properties and advantages that enable manufacturers to excel in their production processes. In this article, we will explore the superior characteristics and benefits of TUC TU-883 materials from the perspective of a PCB manufacturer.
Overview of TUC TU-883
ThunderClad 2 (TU-883) is a cutting-edge material belonging to the category of very low loss substrates, which is developed using a high-performance resin. This advanced material incorporates a reinforcement of regular woven E-glass and is meticulously engineered with a resin system possessing an exceptionally low dielectric constant and dissipation factor. These remarkable characteristics make ThunderClad 2 an ideal choice for applications requiring high-speed, low-loss performance in the realm of radio frequency and wireless technologies.
Notably, ThunderClad 2 material is not only compatible with environmentally friendly, lead-free manufacturing processes, but it also seamlessly integrates with FR-4 processes. Moreover, ThunderClad 2 laminates offer outstanding resistance to moisture, improved coefficient of thermal expansion (CTE), exceptional chemical resistance, remarkable thermal stability, and an impressive resistance to conductive anodic filament (CAF) formation.
Overall, ThunderClad 2 stands out as a state-of-the-art material that combines the benefits of a high-performance resin and regular woven E-glass reinforcement. Its exceptionally low dielectric constant and dissipation factor, along with its compatibility with various manufacturing processes, make it an excellent choice for demanding applications in the fields of high-speed, low-loss, radio frequency, and wireless technologies. Additionally, its exceptional resistance to moisture, improved CTE, superior chemical resistance, thermal stability, and CAF resistance further enhance its suitability for a wide range of applications.
Applications of TUC TU-883 PCB Materials
TUC TU-883 PCB materials, such as ThunderClad 2, find extensive applications in various industries and technologies. Some notable applications include:
1.Radio Frequency (RF):
TUC TU-883 materials are well-suited for RF applications due to their low loss characteristics and excellent high-frequency performance. They can be used in the design and manufacturing of RF amplifiers, filters, antennas, transceivers, and other RF components.
2.Backplane and High Performance Computing:
The exceptional electrical properties of TUC TU-883 materials make them ideal for backplane applications in high-performance computing systems. These materials provide low loss and high-speed signal transmission, enabling reliable and efficient data communication across the backplane.
3.Line Cards and Storage:
TUC TU-883 materials are commonly used in line cards and storage devices, where high-speed data transfer and signal integrity are crucial. These materials enable the design of high-density, high-speed interconnects, ensuring reliable data transmission and minimizing signal loss.
4.Servers:
TUC TU-883 materials are employed in server applications to enable high-speed data processing and communication. They help maintain signal integrity, reduce crosstalk, and ensure efficient thermal management in server systems.
5.Telecom and Base Stations:
TUC TU-883 materials are suitable for telecom infrastructure and base station applications. They enable the design of high-performance circuitry for wireless communication systems, ensuring reliable signal transmission and low loss in high-frequency applications.
6.Office Routers:
TUC TU-883 materials can be utilized in the manufacturing of office routers to achieve high-speed data transfer and reliable network connectivity. These materials help maintain signal integrity and minimize signal loss, ensuring efficient data routing and communication.
Standard Availability of TUC TU-833 PCB Laminates
Based on the information provided, here is the standard availability of TUC TU-833 PCB materials:
1. Thickness: TUC TU-833 laminates are available in a thickness range of 0.002″ (0.05mm) to 0.062″ (1.58mm). This allows for flexibility in selecting the appropriate thickness for your specific application. The laminates are available in both sheet and panel form, providing options for different manufacturing processes.
2. Copper Foil Cladding: TUC TU-833 laminates offer a range of copper foil cladding options. The copper foil cladding thicknesses available for built-up and double-sided PCBs range from 1/3 oz to 5 oz. This allows for customization based on the desired electrical conductivity and current-carrying capacity of the PCB.
3. Prepregs: TUC TU-833 laminates are available in both roll and panel form for prepregs. Prepregs are the resin-impregnated fiberglass sheets used to bond the layers of a PCB together. The availability of prepregs in roll or panel form provides flexibility in manufacturing processes and allows for efficient usage based on the specific requirements of the PCB design.
4. Glass Styles: TUC TU-833 laminates offer various glass styles for the prepregs. The mentioned glass styles include 106, 1080, 3313, and 2116. These glass styles refer to different types of fiberglass weaves used in the prepregs. Additionally, the availability of other prepreg grades upon request suggests that there may be further customization options available to meet specific application needs.
It’s important to note that the standard availability mentioned above may vary depending on the specific manufacturer or supplier.
Industry Approvals of TUC TU-833
Based on the information provided, here are the industry approvals and specifications for TUC TU-833 PCB materials:
1.IPC-4101 Type Designation:
TUC TU-833 laminates have an IPC-4101 type designation of /134. IPC-4101 is a specification that defines the requirements for base materials used in the fabrication of printed circuit boards. The /134 designation indicates a specific type within the IPC-4101 standard.
2.IPC-4101/134 Validation Services QPL Certified:
TUC TU-833 laminates have received validation services and are QPL (Qualified Products List) certified according to IPC-4101/134. This certification indicates that the laminates have met the specified requirements and have been qualified for use in accordance with industry standards.
3.UL File Number:
The UL (Underwriters Laboratories) file number for TUC TU-833 laminates is E189572. UL is a global safety certification organization, and the UL file number indicates that the laminates have undergone testing and evaluation to meet specific safety standards.
4.ANSI Grade:
The information provided does not specify an ANSI (American National Standards Institute) grade for TUC TU-833 laminates. The ANSI grade typically refers to the flammability and electrical performance of the material. It’s important to consult with the manufacturer or supplier to obtain the specific ANSI grade information for these laminates.
5.Flammability Rating:
TUC TU-833 laminates have a flammability rating of 94V-0. The 94V-0 rating is a standardized flammability classification defined by the UL standard. It indicates that the laminates have passed the vertical flame test and are considered self-extinguishing.
6.Maximum Operating Temperature:
The maximum operating temperature for TUC TU-833 laminates is specified as 160°C. This indicates the highest temperature at which the laminates can reliably operate without significant degradation of their electrical or mechanical properties.
Performance of TUC TU-883 PCB Laminates
TUC TU-883 PCB laminates, such as ThunderClad 2, offer exceptional performance characteristics that contribute to their suitability for various applications. Here are the key performance features of TUC TU-883 laminates:
1. Excellent Electrical Properties: TUC TU-883 laminates exhibit outstanding electrical properties, ensuring reliable signal transmission and minimal signal loss. These properties are crucial for maintaining signal integrity and enabling high-speed data communication.
2. Low Dielectric Constant: The dielectric constant of TUC TU-883 laminates is less than 4.0. This low dielectric constant helps minimize signal attenuation and ensures efficient signal propagation in high-frequency applications.
3. Low Dissipation Factor: TUC TU-883 laminates have a dissipation factor of less than 0.005. This low dissipation factor indicates minimal energy loss in the form of heat, allowing for high-efficiency signal transmission and reducing the risk of signal degradation.
4. Stable Dk/Df Performance: TUC TU-883 laminates offer stable and flat dielectric constant (Dk) and dissipation factor (Df) performance across a wide frequency range and temperature variations. This stability ensures consistent electrical performance in different operating conditions.
5. Compatibility with Modified FR-4 Processes: TUC TU-883 laminates are compatible with modified FR-4 processes, making them easier to integrate into existing manufacturing processes. This compatibility enables smooth production transitions and reduces the need for process adjustments.
6. Excellent Moisture Resistance: TUC TU-883 laminates exhibit excellent resistance to moisture, minimizing the risk of performance degradation or failure in humid environments. This moisture resistance contributes to the long-term reliability of PCBs using these laminates.
7. Lead-Free Reflow Process Compatible: TUC TU-883 laminates are compatible with lead-free reflow processes, which are environmentally friendly and comply with regulations regarding hazardous substances. This compatibility ensures compliance with industry standards and regulations.
8. Improved Z-Axis Thermal Expansion: TUC TU-883 laminates demonstrate improved z-axis thermal expansion properties. This improvement helps reduce the risk of delamination or mechanical stress-induced failures, ensuring the reliability of PCBs in various thermal environments.
9. Anti-CAF Capability: TUC TU-883 laminates possess anti-conductive anodic filament (CAF) capability. This feature helps prevent the formation of conductive paths within the laminate, reducing the risk of electrical short circuits and enhancing the overall reliability of the PCB.
10. Excellent Through-Hole and Soldering Reliability: TUC TU-883 laminates exhibit excellent through-hole and soldering reliability. They provide robust adhesion and compatibility with soldering processes, ensuring reliable connections and reducing the likelihood of solder joint failures.
11. Halogen-Free: TUC TU-883 laminates are halogen-free, which means they do not contain halogen-based flame retardants. This feature promotes environmental sustainability and compliance with regulations concerning hazardous substances.
All in all, TUC TU-883 PCB laminates offer excellent electrical properties, low dielectric constant, low dissipation factor, stable performance over frequency and temperature, compatibility with modified FR-4 processes, moisture resistance, improved thermal expansion characteristics, anti-CAF capability, reliable through-hole and soldering performance, and halogen-free composition. These performance features make TUC TU-883 laminates a reliable choice for high-performance PCB applications.
Disadvantages of TUC TU-883
While TUC TU-883 PCB laminates offer numerous advantages, it’s important to consider potential disadvantages as well. Here are a few factors that could be considered as disadvantages:
1. Cost: TUC TU-883 laminates may have a higher cost compared to standard FR-4 laminates. The advanced materials and manufacturing processes involved in producing high-performance laminates contribute to the higher cost. This could be a disadvantage for projects with strict budget constraints.
2. Availability: Depending on the region and specific requirements, TUC TU-883 laminates may have limited availability compared to more commonly used laminates. This could pose challenges in sourcing the materials, especially in certain geographical locations or for smaller-scale projects.
3. Processing Complexity: TUC TU-883 laminates may require specific processing techniques and parameters to achieve optimal performance. This could involve adjustments to manufacturing processes, such as temperature profiles during lamination and soldering, which may require additional expertise or equipment.
4. Design Considerations: The unique characteristics of TUC TU-883 laminates, such as low dielectric constant and dissipation factor, may require careful consideration during the design phase. Designers need to ensure compatibility with other components and the overall system requirements to maximize the benefits of these laminates.
5. Learning Curve: Working with TUC TU-883 laminates may require some learning and adaptation, especially if the design and manufacturing team is more familiar with traditional FR-4 materials. This learning curve could involve understanding the specific properties, handling requirements, and processing considerations of these laminates.
It’s worth noting that the perceived disadvantages may vary depending on the specific application, project requirements, and the experience and resources available to the design and manufacturing team.
Key Factor When Choose TUC TU-883 PCB Materials
When choosing TUC TU-883 PCB materials, several factors should be considered to ensure they meet the requirements of your specific application. Here are some key factors to consider:
1.Electrical Performance:
Evaluate the electrical properties of TUC TU-883 laminates, such as dielectric constant, dissipation factor, and signal integrity. Consider the frequency range and operating conditions of your application to ensure the laminates provide the necessary electrical performance.
2.Thermal Performance:
Assess the thermal properties of TUC TU-883 laminates, including their thermal conductivity, coefficient of thermal expansion (CTE), and their ability to dissipate heat. These properties are crucial for applications that generate significant heat or require efficient thermal management.
3.Mechanical Strength:
Consider the mechanical strength and rigidity of TUC TU-883 laminates, especially if your application involves mechanical stress, high vibration, or components with heavy weight. Evaluate factors such as flexural strength, tensile strength, and impact resistance to ensure the laminates can withstand the mechanical demands.
4.Environmental Compatibility:
Assess the environmental compatibility of TUC TU-883 laminates for your application. Consider factors such as moisture resistance, resistance to chemicals or solvents, and the ability to withstand temperature variations. Ensure the laminates can operate reliably in the intended environmental conditions.
5.Manufacturing Compatibility:
Evaluate the compatibility of TUC TU-883 laminates with your manufacturing processes. Consider factors such as their compatibility with standard PCB fabrication techniques, ease of handling, and compatibility with soldering processes. Ensure that the laminates can be efficiently integrated into your manufacturing workflow.
6.Cost:
Consider the cost of TUC TU-883 laminates in relation to your project budget. Evaluate the overall value proposition and weigh the performance benefits against the cost. It’s important to strike a balance between performance requirements and cost considerations.
7.Availability and Support:
Assess the availability of TUC TU-883 laminates in the market and the support provided by the manufacturer or supplier. Ensure that the laminates are readily available when needed and that you can access technical support or assistance if required.
8.Compliance and Certifications:
Check if TUC TU-833 laminates comply with industry standards and certifications relevant to your application. Examples include UL certification for fire resistance or RoHS compliance for restricted substances. Compliance with these standards ensures the quality and reliability of the laminates.
By considering these factors and aligning them with the specific requirements of your application, you can make an informed decision when choosing TUC TU-883 PCB materials that best meet your needs.
In Conclusion
TUC TU-883 PCB materials provide a comprehensive solution for PCB layout designers aiming to optimize design efficiency and enhance overall performance. With their excellent electrical properties, high thermal stability, and reliable mechanical strength, TUC TU-883 materials offer a solid foundation for creating high-quality PCBs. By leveraging the benefits of TUC TU-883 materials, designers can achieve improved signal integrity, efficient power distribution, and increased reliability in their PCB designs. Embracing these advanced materials empowers designers to push the boundaries of innovation and deliver exceptional electronic products to meet the demands of today’s technology-driven world.
Our services
TUC PCB Laminate & Materials Series