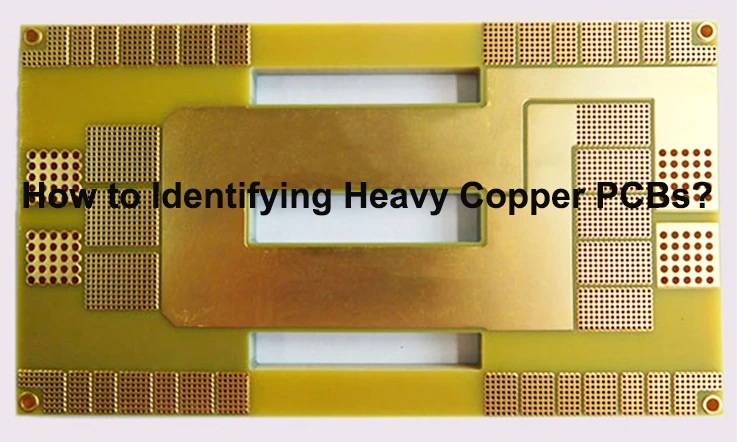
Comprehending the unique characteristics of heavy copper PCBs is vital when defining circuit boards fit for high-current and high-power demanding applications. Heavy copper PCBs, notable for their augmented copper layer thickness, have the ability to withstand escalated current loads while providing superior heat dissipation. Within this discourse, we investigate the techniques applied for pinpointing heavy copper PCBs, along with the important factors designers and manufacturers should be conscious of. This understanding empowers these stakeholders to make educated decisions in their selection and application of heavy copper PCBs.
Fabrication of Heavy Copper PCBs
Within the sphere of printed circuit boards (PCBs), heavy copper PCBs are differentiated by their markedly denser copper layer when contrasted to regular alternatives. Characteristically, heavy copper PCBs feature a copper density of 2 ounces per square foot (oz/ft²) or more, outpacing the standard 1 oz/ft² or less commonly observed in standard PCBs. These tailored PCBs come into play in situations calling for high-current and high-power applications, embodying uses in power distribution frameworks, high-frequency circuits, automotive electronics, industrial machinery, and sustainable energy systems.
Not dissimilar to the production process of a standard PCB, the fabrication technique for heavy copper PCBs involves some further steps to accommodate the heavier copper layering. The following key stages are involved:
Planning: CAD software tools are used to design the PCB structure. Special emphasis is laid on the denser copper layer and its effects on electrical properties.
Selection of Materials: High-performing laminate resources such as FR-4 or polyimide are the common choices for the PCB base layer. The copper foil, markedly thicker than its standard counterpart, used in heavy copper PCBs may comprise of oxygen-free copper or alloyed copper.
Lamination: The additional copper layer is appended to the substrate material via a high-temperature and high-pressure process, demanding higher pressure and longer lamination times than in the standard PCB production process.
Drilling: Component and via holes are created in the laminated material using drill bits specifically tailored for heavy copper PCBs.
Plating: The copper layer undergoes plating with a thin layer of solder mask to shield against oxidation and corrosion. Solder masks on heavy copper PCBs are typically thicker, thereby offering enhanced protection.
Application of Solder Paste: Solder paste is applied to the copper pads where the components are to be positioned. The solder paste mix must be particularly suited for use in heavy copper PCB manufacture.
Component Placement: Components are mounted and soldered in place via reflow ovens or wave soldering machines. It’s vital to exercise strict control over the soldering process to establish strong and sound solder junctions.
Inspection and Verification: One the PCB is ready, an extensive inspection and testing are performed to ensure compliance with design specifications. Heavy copper PCBs may call for further testing methodologies like X-ray inspection or non-destructive testing (NDT) to assure the integrity of the amplified copper layer.
While heavy copper PCBs provide several advantages over their standard counterparts such as reduced resistance and inductance while improved heat dissipation and increased durability, it’s not all positives. They also carry potential drawbacks.
Disadvantages:
●Increased Cost: Due to the use of heavier copper foils and additional processing steps, heavy copper PCBs staff a higher manufacturing cost compared to standard PCBs.
●Weight Considerations: Heavy copper PCBs weigh more than standard PCBs which may pose a challenge in weight-sensitive applications.
●Limited Availability: Most manufacturers may not offer heavy copper PCBs readily, particularly in the case of small quantities or custom designs, leading to sourcing limitations.
●So, heavy copper PCBs can play an integral role in high-current and high-power applications through their protective attributes, despite their elevated costs, increased weight, and sourcing challenges. Careful evaluation of these factors is required to match the specific application requirements.
Why it Matters to Identify Heavy Copper PCBs Right?
The accurate distinction of heavy copper PCBs is essential for numerous crucial reasons:
Dependability: Heavy copper PCBs are frequently implemented in high-current and high-power applications which demand reliable performance. Precise detection ensures that the PCB fabricated meets the exact specifications to handle the intended electrical load.
Safety: If a heavy copper PCB is mistakenly identified as a standard copper PCB, it can lead to overheating, component failure, and potentially dangerous situations, including fire. Accurate identification helps to avert these safety risks by ensuring that the PCB is designed and manufactured to accommodate the increased power requirements.
Performance: Heavy copper PCBs possess distinct electrical properties in comparison to their standard counterparts, such as lower resistance and inductance. Proper identification ensures that the circuit design is optimized to deliver the desired results in terms of heat management, the capacity to carry current, and overall electrical features.
Cost-Effectiveness: Heavy copper is undoubtedly more expensive compared to standard copper. Accurate identification prevents the wastage of resources and overcompensation for features that do not meet the required specifications. By accurately recognizing heavy copper PCBs, manufacturers can ensure the economical use of materials.
Traceability: It’s essential to maintain traceability for quality control and product liability purposes. Accurate identification enables manufacturers to trace the materials used in the production of heavy copper PCBs to ensure compliance with industry standards and facilitate the resolution of potential issues during the product life cycle.
Furthermore, in the high-reliability applications’ industry like aerospace, automotive, and medical devices, precise identification of heavy copper PCBs becomes paramount. Adhering to the correct specifications and materials ensures safety, performance, and longevity of electronic products in these critical sectors.
The increasing incidence of spurious and subpar PCBs in the electronics sector is a concern worth addressing. Precise recognition of heavy copper PCBs acts as a strategic method to alleviate the possibility of encountering counterfeit or mediocre materials, thereby protecting the comprehensive quality and dependability of electronic commodities.
All in all, the accurate distinction of heavy copper PCBs is indispensable for ensuring reliability, safety, performance, economical efficiency and traceability within the realm of the electronics industry, particularly in high-reliability applications.
Considerations For Identifying Heavy Copper PCBs
When looking for heavy copper PCBs for your specific use you should take into account the following aspects:
Current and Power Requirements: Ascertain the current and power needs of your circuit or system. Heavy copper PCBs are specifically curated to handle high-current and high-power applications. Verify that the copper thickness and width are sufficient to handle the required current without undue voltage drop or heating.
Copper Thickness: Heavy copper PCBs are marked by their heavier copper layer. The requisite copper thickness should be determined based on your application’s requirements.
Copper Weight Distribution: Evaluate the distribution of copper weight across the PCB. Judging whether a uniform copper thickness throughout the entire board is required or specific areas need heavier copper traces for localized high-current paths is essential.
Heat Dissipation: Assess the thermal dissipation requisites of your circuitry. Owing to their denser copper strata, heavy copper PCBs provide superior heat dissipation, which can aid in averting overheat scenarios and component malfunction. Contemplate the necessity of amplified thermal conductivity for the application, and determine whether heavy copper traces or planes can proficiently mitigate heat..
Mechanical Considerations: Analyze any mechanical restrictions or limitations for your PCB. Heavy copper PCB’s, generally thicker and heavier, may impact the overall size and compatibility of your design.1
Manufacturing Capability: Confirm the manufacturing capability of your PCB manufacturer or supplier, as heavy copper PCBs require specialized equipment and processes to handle the denser copper layers.
Economic Factors: It is pivotal to take into account the financial ramifications linked to heavy copper PCBs. Owing to the usage of denser copper layers and supplemental processing actions during fabrication, the production expenses associated with heavy copper PCBs are invariably elevated relative to standard PCBs.
Availability and Turnaround Time: It is of great relevance to evaluate the accessibility and delivery schedule of heavy copper PCBs from your preferred manufacturer. Confirming that the manufacturer can accommodate your production timeframe and volume necessities is crucial for a smooth project realization.
Through careful analysis of these components, you can pinpoint the most apt heavy copper PCBs that satisfy the electrical, thermal, mechanical, and fiscal requisites of your distinct application.
Methods for Identifying Heavy Copper PCBs
To discern heavy copper PCBs, several techniques exist:
Visual Examination: Owing to their noticeably thicker and darker copper layers compared to standard PCBs, heavy copper PCBs are visually distinctive.
Micrometer Assessment: Utilizing a micrometer allows for precise measurements of the copper layer’s dimensions. Typically, the characteristic signature of heavy copper PCBs is a copper layer thickness that surpasses 2 oz/ft².
Resistance Quantification: As a product of the augmented thickness of the copper stratum when compared to standard PCBs, heavy copper PCBs generally have decreased resistance. This characteristic can be substantiated using a multimeter to evaluate the resistance of the copper layer.
Inductance Quantification: Measurement of inductance of the copper layer can be conducted using an appropriate meter. The superior density of the copper layer in heavy copper PCBs usually exhibits as lower inductance, in contrast to standard PCBs.
Imaging and Inspection Modalities: Techniques like Automated Optical Inspection (AOI) and X-ray inspection are proven tools for detecting heavy copper PCBs. AOI can discern variations in the thickness and grain of the copper layer, whereas X-ray inspection can pinpoint any hidden internal flaws or voids within the copper layer.
It is worth noting that while some standard PCBs might possess a thicker copper layer than normal, these may not attain the thickness typical of heavy copper PCBs. Therefore, it is prudent to utilize multiple detection techniques to accurately identify heavy copper PCBs.
To Summarize
Accurately recognizing copper PCBs is crucial when selecting the appropriate circuit boards for applications requiring high current and power. By using a combination of inspection, micrometer measurements, resistance measurements, inductance measurements and advanced imaging methods engineers and manufacturers can distinguish between heavy copper PCBs and standard ones. Familiarity with these identification approaches enables decision making guaranteeing the effective use of heavy copper PCBs and ensuring consistent and efficient performance, in electronic systems.