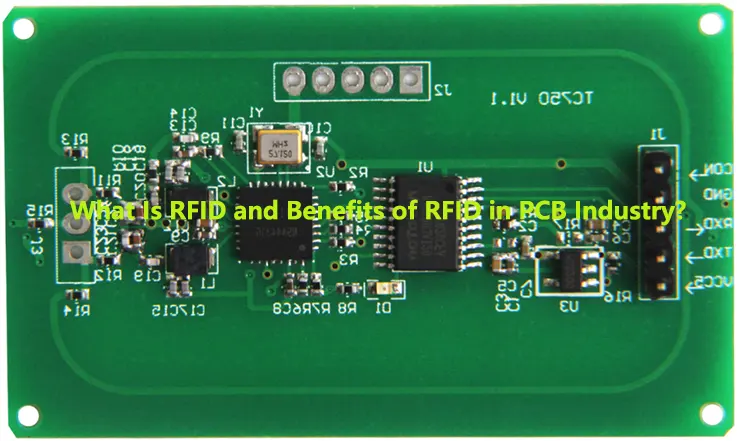
Radio-frequency identification (RFID) technology has emerged as a game-changer in various industries, including the printed circuit board (PCB) manufacturing industry. RFID technology utilizes radio waves to communicate information between RFID tags and readers, allowing for real-time tracking of a wide range of objects, including PCB components and finished products.
The incorporation of RFID technology in the PCB industry offers manufacturers numerous benefits, including streamlining inventory management, facilitating higher product quality control, improving traceability, and boosting production efficiency. Additionally, RFID technology can provide greater visibility into the supply chain, enabling manufacturers to detect bottlenecks and other inefficiencies and optimize operations accordingly.
Innovations in RFID technology continue to emerge, promising even more advancements and benefits for businesses that use this technology. Specifically within the PCB industry, RFID technology is poised to play an increasingly critical role in shaping the future of the industry. By incorporating RFID technology into their operations, PCB manufacturers can gain a competitive edge and remain at the forefront of innovation in this ever-evolving marketplace.
What Is Radio Frequency Identification(RFID) ?
Radio Frequency Identification (RFID) is a wireless communication method that utilizes electromagnetic or electrostatic coupling in the radio frequency range of the electromagnetic spectrum. This process uniquely identifies an item, animal, or person and has the capability to track their location. Essentially, RFID search, identifies, tracks, and communicates with objects and individuals via radio frequency transmissions.
RFID is a technology that retrieves data using digital encoding from an RFID tag, and this information can be read using a reader. During this process, the device functions as a tag or label that is readable by a reader. Unlike traditional barcodes and QR codes, RFID functions by transmitting information wirelessly and through the internet. RFID can be applied using either passive or active methods and provides the ability to read from a concealed location. The collected data is then stored in a database for later retrieval.
Radio-Frequency Identification (RFID): Types
There are two types of such tags:
Active RFID
The apparatus comprises radio frequency identification (RFID) tags that are powered by a connected power supply for transmitting a signal. Concurrently, the apparatus also incorporates an antenna to facilitate the reception of data.
In the case of an active tag, it employs a dedicated power source such as a battery to enable autonomous operation without requiring energy from the source or reader. Therefore, the active tag’s circuitry can operate continuously without the dependence on external power supply, manifesting a self-dependence on its own specialized power source.
Passive RFID
Passive RFID tags, unlike their active counterparts, are not designed with an independent power supply and instead rely on power from the reader. The RFID tags integrated within this apparatus do not have a direct connection to a power supply, and passive RF tags store their energy and utilize it when exposed to emitted power from active antennas and RF tags. Such power is transmitted over specific frequencies as per standards, with low frequency utilizing the 125-134 MHZ range, high frequency employing the 13.56 MHZ range, and ultra-high frequency using the 856 MHZ to 960 MHZ range.
Unlike barcodes, RFID tags do not require direct line-of-sight with the reader and thus can be embedded into the item under surveillance. This enables Automatic Identification and Data Capture (AIDC) through the use of RFID technology.
How Does RFID Work ?
Automatic Identification and Data Capture (AIDC) encapsulates several technologies, which includes radio frequency identification (RFID). AIDC techniques, utilizing radio waves, automate the identification of items, extract data, and seamlessly feed the collected information into computer systems with minimal or no human intervention. The primary components of an RFID system are an RFID tag (smart label), an RFID reader (interrogator), and an antenna.
An RFID tag features an integrated circuit and an antenna that facilitate the transmission of data to the RFID reader. Upon capture, the radio waves are converted to an easy-to-use data format by the reader. The data accumulated by the tags is accessed via a communications interface and transmitted to the host computer system. Here, it gets stored in a database for future retrieval and analysis.
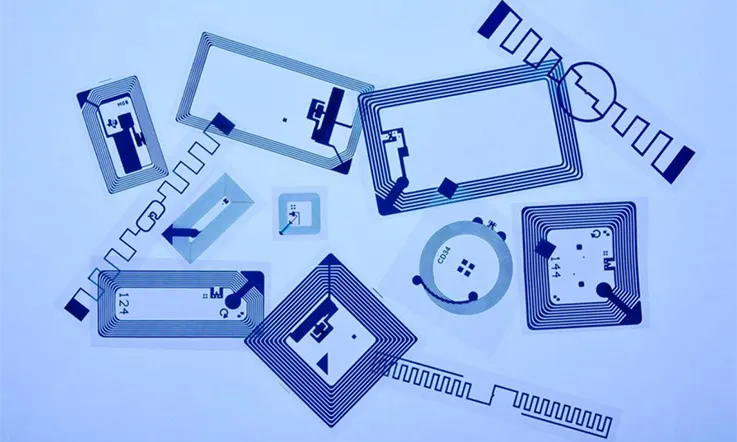
Features of RFID
Radio Frequency Identification (RFID) offers various features, including:
● Automation: RFID allows for the automation of data collection and management with minimal human intervention, making it an efficient and cost-effective solution for businesses.
● Non-line-of-sight: As RFID utilizes radio waves, it does not require direct line-of-sight between the reader and tag, making it ideal for monitoring items in difficult-to-reach or cluttered environments.
● Multiple tag reading: RFID technology enables the simultaneous reading of multiple tags by a single reader, making it easy for businesses to track large numbers of items accurately.
● Data storage capacity: RFID tags have varying data storage capacities, ranging from just a few bytes to several kilobytes, allowing for the storage of various types of data, including product information, shipping details, and historical maintenance records.
● Long-range reading: RFID is capable of long-range reading, enabling scanning of multiple tags from a distance of several meters, making it ideal for use in applications like warehouse management and logistics.
● Real-time data capture: RFID enables real-time data capture and analysis, providing businesses with up-to-date information on inventory levels, location, and condition of goods, which can be used to optimize operations and improve supply chain efficiency.
Advantages of RFID
Advantages of Radio Frequency Identification (RFID) technology include:
● Increased productivity and efficiency: RFID eliminates the need for manual data entry, reducing labor costs and errors in data collection. This streamlines processes, saves time, and improves accuracy, leading to increased productivity and efficiency.
● Improved inventory management: RFID enables real-time tracking and monitoring of inventory levels, providing accurate and up-to-date information on product availability, location, and condition. This leads to improved inventory accuracy, better demand forecasting, reduced stock-outs, and overstocking, ultimately lowering costs and improving customer satisfaction.
● Enhanced security: RFID can be used to prevent theft and unauthorized access to assets such as equipment, vehicles, or high-value items. It also offers the ability to track the movement of goods throughout the supply chain, reducing the risk of counterfeiting and tampering.
● Increased supply chain visibility: RFID provides end-to-end visibility across the supply chain, enabling businesses to track products from manufacturing to delivery. This improves supply chain visibility and transparency, leading to increased efficiency, reduced errors, and improved vendor management.
● Cost savings: RFID can help businesses reduce costs by improving processes, lowering labor costs, and reducing inventory expenses. RFID can also help minimize losses due to theft, damage, or spoilage, ultimately leading to improved profitability.
● Versatility: RFID technology can be employed in a variety of applications across a range of industries, from inventory and asset management to logistics and healthcare.
Disadvantages of RFID
Radio Frequency Identification (RFID) technology has a few potential disadvantages, including:
● High initial investment: Implementing an RFID system requires significant investment in hardware, software, and infrastructure such as readers, antennas, and middleware. These costs can be prohibitively high for some businesses, especially small to medium-sized enterprises.
● Limited reading capabilities: Although RFID has a longer range than other automatic identification technologies, it still has limitations in reading range and may struggle with metal or liquid products or products with a high water content.
● Privacy concerns: RFID raises concerns around personal privacy and data protection, as tagging of consumer goods or tracking of individuals can lead to concerns about the misuse of personal information.
● Interference with other systems: RFID operates on radio frequencies, which can potentially interfere with other electronic systems in the vicinity. This could lead to system failure or malfunction, especially in sensitive environments such as hospitals or aircraft.
● Standardization: Lack of standardized protocols can be a barrier to the implementation of RFID solutions, especially in global supply chains where teams need to integrate data from multiple sources into a single system.
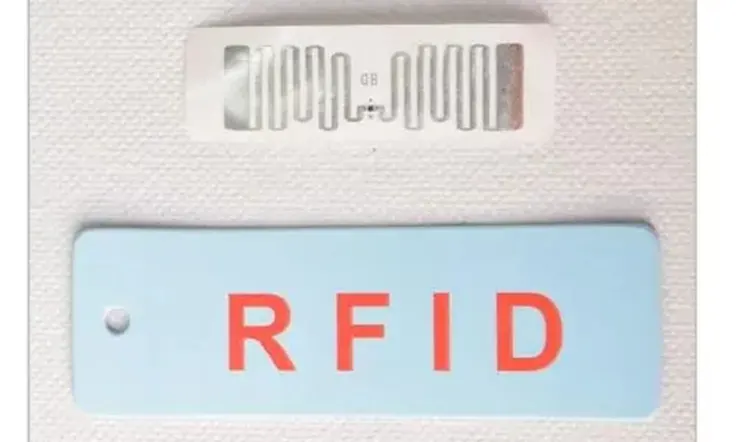
Application of Radio Frequency Identification (RFID)
RFID tags have proven to be versatile tools, finding their way into a wide array of business sectors. In the automotive industry, RFID tags attached to vehicles during production enable performance monitoring along assembly lines, while the tracking of RFID-tagged medications as they move through warehouses ensures efficient inventory management. Microchipping pets and livestock also facilitates identification. Furthermore, retailers take advantage of these tags to speed up checkout processes, bolster security, and discourage theft by customers and employees.
Given their ability to track valuable assets, commodities, and living creatures, RFID tags give rise to legitimate concerns regarding privacy and data protection. In response to these apprehensions, standard specifications have been created to address security and privacy issues.
To avoid traceability, reader and tag authentication, and over-the-air privacy concerns, on-chip cryptography is utilized in the ISO/IEC 18000 and ISO/IEC 29167 standards. These standards also address digital signatures for use with RFID and barcodes to ensure the data’s legitimacy, its source, and its read method. This work is carried out within the ISO/IEC JTC 1/SC 31 Automatic identification and data capture techniques working group.
In the electronics industry, UHF RFID label tags are attached to finished products after the assembly process. A new approach enables the direct integration of PCB RFID label tags at earlier production stages.
Implementing PCB RFID tags provides detailed tracking information to management, allowing for precise identification of specific printed circuit boards and facilitating efficient inventory tracking and identification of production bottlenecks.
Benefits of RFID in PCB Industry
In the recent past, Radio Frequency Identification (RFID) technology has made remarkable advances, leading to substantial benefits across various industries. One sector that has shown growing interest in RFID adoption is the Printed Circuit Board (PCB) industry. By incorporating RFID technology into the production process, PCB manufacturers can improve efficiency, enhance quality control, and increase traceability.
The follow is benefits of RFID technology in the PCB industry:
● Streamlined Inventory Management: The implementation of RFID tags in PCB production simplifies inventory management by providing real-time monitoring of components and finished products. These tags contain vital information such as component specifications, serial numbers, and manufacturing dates, enabling efficient tracking and control over inventory levels. Additionally, RFID tags provide enhanced visibility into the supply chain, enabling manufacturers to detect bottlenecks and other inefficiencies and optimize operations accordingly.
● Enhanced Quality Control: In the PCB industry, ensuring quality control is of utmost importance, as faulty products can result in device malfunctions or hazardous situations. RFID technology is a valuable tool in enhancing the quality control process by enabling continuous monitoring of PCBs throughout the production lifecycle. This real-time tracking capability aids manufacturers in promptly detecting defects or inconsistencies, allowing for timely rectification before they cause significant disruptions or safety concerns.
● Improved Traceability: The integration of RFID technology allows PCB manufacturers to meticulously trace every phase of the production process. This heightened traceability capability empowers manufacturers to swiftly identify the source of defects or quality concerns, which in turn enables swift resolution and minimizes the possibility of future issues. Additionally, this enhanced traceability assists manufacturers in upholding industry regulations and standards while providing valuable product data to customers regarding their products’ manufacturing history.
● Reduced Labor Costs: One of the significant advantages of RFID technology is the ability to automate data collection and effectively manage inventory. By eliminating the need for manual tasks such as barcode scanning or manual counting, PCB manufacturers can realize significant cost savings. In addition, the automation of these labor-intensive tasks can reduce human error in inventory management and quality control processes, leading to improved efficiency and accuracy.
● Increased Production Efficiency: RFID systems can be instrumental in optimizing production processes by providing up-to-date information on component availability and location. This enables manufacturers to plan their production schedules more effectively, resulting in greater efficiency. By utilizing RFID technology, businesses can decrease lead times and make better use of resources, resulting in improved profitability.
● Enhanced Security: RFID technology can also bolster security within the PCB manufacturing process by limiting access to specific areas or components. This additional security measure can assist in safeguarding intellectual property, preventing unauthorized entry, and maintaining the sanctity of the manufacturing process.
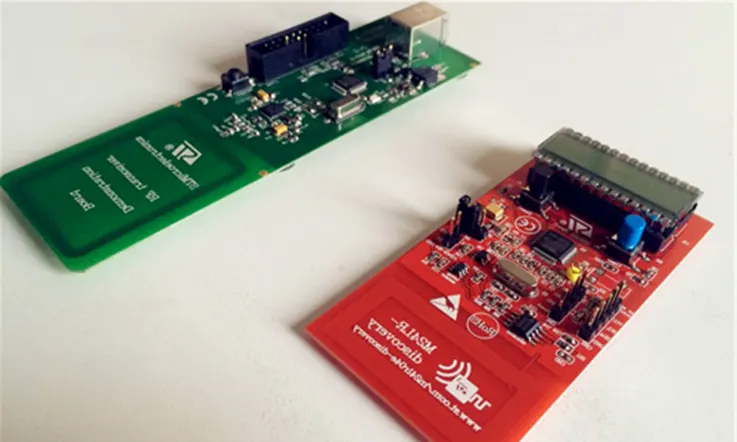
Challenges of RFID implementation in PCB Industry
There are several challenges associated with the implementation of RFID (Radio Frequency Identification) technology in the PCB (Printed Circuit Board) industry, including:
● Cost: The cost of implementing an RFID system can be high, especially for small and medium-sized PCB manufacturers, and integrating it into existing systems may require significant investment.
● Compatibility: RFID technology may not be compatible with all types of products or materials used in the PCB industry, which can make it difficult to implement across the supply chain.
● Interference: The use of RFID in the PCB industry may be hampered by interference from other electronic devices or materials that can block or hinder radio signals.
● Data Management: RFID generates large volumes of data, and managing and analyzing this data can be challenging without the proper infrastructure and tools.
● Privacy and Security Concerns: The use of RFID technology raises concerns about privacy and security as data can be intercepted or stolen during transmission or storage.
Overcoming Challenges with Proper Planning and Implementation
Overcoming challenges associated with implementing RFID (Radio Frequency Identification) technology in the PCB (Printed Circuit Board) industry requires proper planning and implementation, including:
● Cost-effectiveness: By conducting a cost-benefit analysis, manufacturers can determine the potential benefits of RFID technology, identify areas where it can be implemented most cost-effectively, and explore options for financing the investment in RFID.
● Compatibility: Conducting a thorough review of the types of materials, processes, and products will be used in PCB manufacturing before implementing RFID can help ensure compatibility and reduce the risk of issues arising.
● Interference: Manufacturers can work with technology vendors to identify and address interference caused by other electronic devices, materials, or environmental factors that could impact the performance of RFID.
● Data Management: Proper planning and implementation of an RFID system should include the development of a data management plan, including how data will be collected, processed, stored, and analyzed.
● Privacy and Security Concerns: Addressing privacy and security concerns should be part of the planning and implementation process, including measures in place to protect confidential data.
Case Studies and Success Stories of RFID in PCB Industry
There are several successful implementations of RFID (Radio Frequency Identification) technology in the PCB (Printed Circuit Board) industry. Here are a few examples of case studies and success stories:
● JarnisTech: JarnisTech, a global PCB manufacturing services company, implemented an RFID-based material tracking system that uses mobile devices to track the location and status of materials at each stage of production. This system helped reduce search time for misplaced materials, improve inventory accuracy and reduce inventory levels by 25%.
● Sanmina-SCI Corporation: Sanmina-SCI, a contract manufacturer of electronics, implemented an RFID-based system for tracking and managing inventory of materials in their PCB manufacturing operations. The system provided real-time visibility into inventory levels and reduced inventory inaccuracies by 90%, leading to a significant reduction in overall manufacturing costs.
● Motorola Solutions: Motorola Solutions, a provider of mission-critical communications and analytics solutions, implemented an RFID-based system to track and manage inventory levels of components used in their PCB manufacturing processes. The system enabled real-time tracking of inventory, reducing the incidence of stock shortages and minimizing lead times.
● Intel Corporation: Intel implemented an RFID-system for tracking the production status of PCBs on production lines. The system reduced the incidence of operator errors and provided real-time visibility into production status, leading to improved quality and increased productivity.
Overall, these case studies demonstrate the potential benefits of RFID technology in the PCB industry, including enhanced inventory management, improved quality control and operational efficiency, and reduced costs.
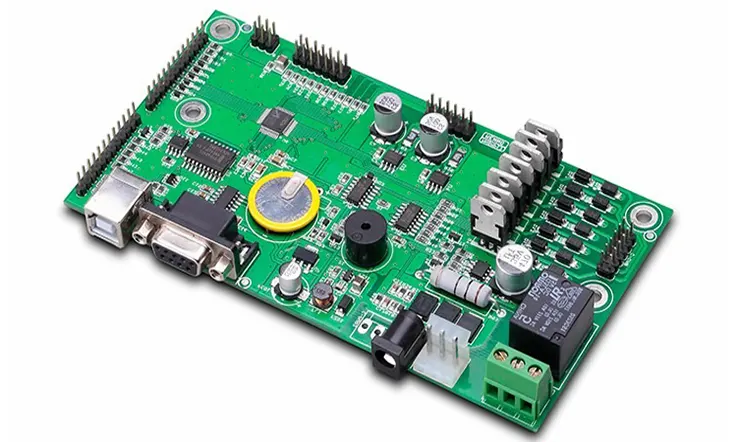
Future of RFID in PCB Industry
The future of RFID in the PCB industry is promising, with advancements in technology and the increasing demand for more efficient and reliable manufacturing processes. Some possible future developments include:
● Integration with the Internet of Things (IoT) for real-time data tracking and monitoring.
● Increased use of RFID-enabled sensors for temperature, humidity, and vibration monitoring during production and shipment.
● Use of RFID in combination with other technologies like AI and machine learning for predictive maintenance and quality control.
● Adoption of more secure RFID implementations for preventing counterfeiting and enhancing supply chain security.
● Emergence of new applications for RFID-based systems in the PCB industry, such as smart packaging and asset tracking.
Conclusion
RFID (Radio Frequency Identification) technology has the potential to revolutionize the PCB (Printed Circuit Board) industry by improving inventory management, enhancing production processes, increasing traceability and product visibility, and enhancing quality control. However, the implementation of RFID technology in the PCB industry does face challenges such as cost, compatibility, interference, data management, and privacy concerns, which need to be addressed, through proper planning and implementation.
As demonstrated by several successful case studies and success stories, implementing RFID technology in the PCB industry can lead to significant improvements in efficiency, productivity, and cost reductions. Hence, with continued advancements in RFID technology and increased awareness of its benefits, the adoption of RFID technology in the PCB industry is likely to continue to grow in the future.
Therefore, as technology advances, PCB manufacturers can anticipate further benefits, establishing RFID technology as a pivotal element in the industry’s progression and continued success. By embracing and implementing RFID technology, PCB manufacturers can maintain a competitive edge and spearhead innovation in this constantly evolving marketplace.
Related Posts:
1.Land Grid Array (LGA): Advantages, Challenges, Limitations, Applications
2.What is the Integrated Circuit (IC) Board?
4.What Is FPGA and Why Do You Need to Care?
5.Comprehensive Guide to IC Substrate Design and Manufacturing