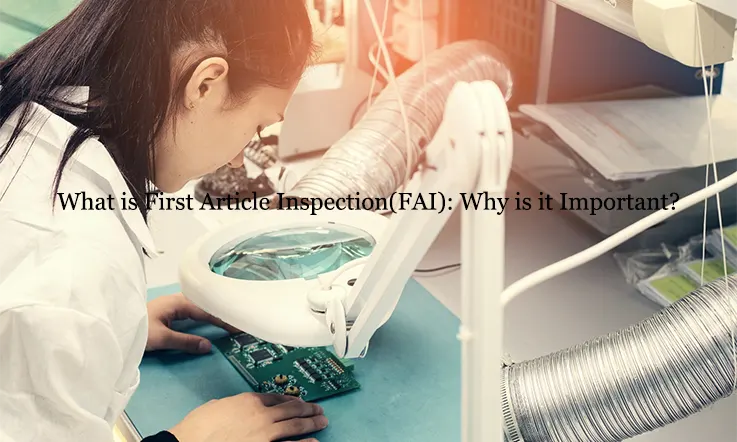
The scrutiny of printed circuit boards (PCBs) is a crucial step in detecting any potential defects that may have arisen during the manufacturing or assembly process. This process aids in the identification of design issues, if any, and allows for prompt remedial action. Conducting inspections at each stage of the process ensures timely identification of product flaws before proceeding to the next phase, thereby preventing unwarranted expenses and delays. Moreover, this practice facilitates the detection of isolated defects present on a single or multiple PCBs, ensuring consistency and quality of the end product.
As a PCB design professional, we recommend reviewing the information below for additional insights on PCBA first article inspection to improve your expertise in this important area.
Definition of First Article Inspection
The First Article Inspection (FAI) system is an essential method for preventing errors and minimizing batch mishaps in electronic manufacturing. It plays a critical role in enhancing overall manufacturing quality by reducing the likelihood of faulty components and errors. As the name implies, FAI is the initial inspection technique for manufactured items.
It is important to note that a “first article” is distinct from a sample or a pre-production prototype of a Printed Circuit Board Assembly (PCBA). This distinction is because both types of prototypes may utilize different methods or equipment for the fabrication process. In the case of PCBA, the first devices produced by a PCB assembly line may not be PCBAs. Instead, they may require an assessment of a representative sample of the initial manufacturing assembly.
Conducting an assessment at this early stage is crucial to ensuring that the production engineer or technician fully understands your requirements and incorporates them into the normal manufacturing process. By doing so, they can identify any potential issues that may arise during the manufacturing process and make any necessary adjustments to ensure that the final product meets your specifications.
The Importance of First Article Inspection
Conducting a first piece inspection is essential for achieving successful manufacturing outcomes. There are several key reasons why this inspection is critical:
● Product Quality: An FAI plays a critical role in determining the quality of the final product. If the inspection reveals issues, nonconformances, or deficiencies, it indicates that modifications are necessary to the manufacturing processes. The completion of an FAIR serves as verification that the specified conditions outlined by the customers have been met, thus ensuring that their expectations are satisfied.
● Process Quality: Performing a first article inspection not only determines product conformance, but also evaluates the manufacturing process to ensure the ability to replicate desired outcomes for your client. Conducting an FAI enables you to determine whether your manufacturing process is capable of generating desirable results and whether any modifications are necessary to improve product outcomes. The results from an FAI can guide the decision for engaging in more product runs, as well as provide insight into adjustments required for optimizing your manufacturing process.
● Documentation and Tooling: Furthermore, a first article inspection confirms material compliance and ensures the accuracy of special process documents and tooling used throughout the production process. This inspection provides objective evidence of product conformance, and certified FAI documentation serves as a reliable source of information about your process, particularly during postmortem reviews and evaluations. Having access to such documentation is advantageous not only to you, but also to your clients.
● Buyer/Manufacturer Assurance: Assuring certainty for both you and your client throughout the transaction is crucial. Your client has the right to expect that the product will meet their specific criteria, while you must have confidence that your production process will generate the desired outcomes not only for the current run but also for subsequent ones. To gain the assurance required to proceed with the procedure, a first article inspection is essential. It provides conclusive evidence that the product meets the necessary requirements and establishes a foundation of trust between you and your client.
What Is PCB Assembly First Article Inspection ?
First Article Inspections (FAI), also known as first piece inspections, can be overlooked in the Printed Circuit Board (PCB) Assembly Manufacturing industry in favor of other types of inspections, such as Visual Inspection, Automated Optical Inspection (AOI), X-ray, and Solder Paste Inspection (SPI). Some PCB assembly or SMT assembly vendors may also be hesitant to provide FAI services, particularly if they are not familiar with the customer’s specifications and requirements.
If you require a first article inspection for your printed circuit board assembly, it is essential to clearly specify this requirement in your fabrication drawings and confirm that the PCB assembly manufacturer can provide FAI services. Clearly defining expectations for when and how the quality of the PCB assemblies will be evaluated in the fabrication drawing can prevent any pushback from the selected supplier. Additionally, it is advisable to communicate the significance of PCBA yield in high-volume PCB assembly projects by establishing a tolerable defect rate.
By emphasizing the importance of FAI and providing specific requirements, the PCB assembly manufacturer can better understand your needs and provide a higher level of service, resulting in a higher-quality end product.
So, the follow reason is Why us need to First Article Inspection for PCBA:
First Article Inspection (FAI) plays a crucial role in protecting products from being produced in batches of substandard quality, reworked items, and scrap. It is a method of controlling the product manufacturing process, serving as a key production process and quality control technique. FAI is a reliable method for ensuring product quality and enhancing economic efficiency.
The primary purpose of FAI is to detect factors that may impact product quality as early as possible in the production process to prevent the production of defective batches or scrap. FAI that occurs before beginning formal production serves to eliminate any possibility of producing unqualified items in batches.
Our long-term practical experience has shown that the FAI system detects problems early in the production process that can prevent defective batch production through the application of appropriate solutions. FAI can reveal issues such as excessive fixture deterioration, installation and placement mistakes, measuring instrument accuracy deterioration, incorrect drawings, feeding or formulation problems, and other systemic causes. These issues can be addressed through corrective or improvement steps during the production process to prevent batch rejects and ensure product quality.
PCBA First Article Inspection Process
Possible PCBA First Article Inspection Process:
● Preparing for inspection: The first step is to review the project’s specifications, design drawings, and any special requirements or instructions. Assemble all required measuring tools and inspection equipment.
● Inspection Checklists: Prepare an inspection checklist to identify all critical features of the PCBA that need verification and measurement. Checklists may include dimensions, tolerances, component placement, soldering quality, and electrical testing requirements.
● Performing the Inspection: Conduct an Eyes-On check of the PCBA. Use measuring tools to check critical dimensions, apply voltage and current as per the design, and verify the functioning of the PCBA. Inspect the PCBA for any physical defects, including scratches or dents, alignment, and cosmetic issues.
● Electrical Testing: Conduct electrical testing to check the circuits’ connectivity and functionality. Verify the DC voltage levels and measure the current flow across the different points.
● Result and Reporting: Record the results and observations of the inspection, including any non-conformances. If the results indicate a non-conformity or defect, document the issue and the corrective action taken to address it.
● Acceptance Criteria: Compare the results of the inspection and testing to the acceptance criteria specified in the project’s requirements. If the PCBA meets the required acceptance criteria, approve it for the production run. If not, take necessary corrective actions and recheck the PCBA.
Therefore, PCBA First Article Inspection aims to verify the conformity of the first manufactured item with the design specifications, drawing, and engineering requirements. It assures that the production process will produce the item consistently and ensure its quality. The inspection process follows industry-standard practices, including thorough documentation and verification of the assembly’s integrity.
Who Does the First Article Inspection for PCBA ?
FAI is crucial to the yield of high-volume PCB assembly production, but who will be responsible for doing the first article inspection ?
● At JarnisTech, we offer three alternative methods for conducting First Article Inspection (FAI) in our Shenzhen SMT assembly factory. The first option involves the customer performing the inspection at our factory, and if there are no flaws in the prototypes, mass production can begin promptly. In this scenario, we prioritize enhancing work efficiency while continuing with the production process.
● The second option involves online interaction between our respective teams, where we provide you with high-definition photographs of the inspection and testing results carried out in accordance with quality control procedures and standards. This method may require a longer stop in PCB assembly production, but it allows for more careful consideration and collaboration on both sides.
● The third preferable method is conducting the inspection and testing ourselves, following mutually agreed-upon standard procedures. However, if something has not been clearly specified, there is a risk that the PCB assembly manufacturer may overlook this during the inspection or testing process.
Regardless of who conducts the FAI, its primary objective is to determine whether the PCB assembly procedures and conditions are capable of producing high-quality and high-yield products. If faults are identified during the FAI, the PCB manufacturer can make necessary adjustments and optimize the machine program, adjust the convey speed of the bare printed circuit board, and/or take any other required steps. In the event that no issues are identified, mass production will proceed as planned, following the pre-production process.
FAI Mechanism and PCBA Processing: They Are interlinked
● Self-inspection: In PCB assembly manufacturing, self-inspections are typically carried out by engineers on the initial product they produce. Field engineers usually take the lead in this process. Through the use of validated data, engineers are able to conduct these inspections with a primary focus on the positioning of components as well as the impact of mounting.
● Mutual-inspection: Post completion of the engineer’s inspection, the mutual inspection stage involves the operator’s involvement. During this stage, the operator will undertake checking of the BOM and drawings, and will determine whether there is any deficit or shortage of materials, among other things. In the event of objects or issues arising, the operator shall promptly notify the production engineer.
● Full-inspection: Upon the successful completion of the qualification process, it is customary for the quality inspection staff to undergo a comprehensive inspection. This inspection is an important quality control measure that ensures all individuals responsible for examining and assessing the final product meet the established standards and criteria. During this inspection, the quality inspection personnel are subjected to a rigorous evaluation to assess their competence, skill level, and adherence to relevant safety regulations. The ultimate goal of this inspection is to maintain consistency and excellence in the PCB assembly manufacturing process, thereby ensuring customer satisfaction.
Electronics manufacturing commonly employs multimeters and ECR bridges for measurement purposes, with the latter being more prevalent in large-scale manufacturing settings. Accurately determining component values and identifying the direction of current flow are critical points of emphasis in such measurements. In instances where BGA components are involved, mandatory X-ray inspection is required in order to assess the impact of soldering on the internal solder balls.
In PCB Assembly manufacturing, the product is thoroughly examined in accordance with the original BOM and any special processing requirements or samples specified by the customer. The first piece of production is always inspected to ensure it meets the customer’s requirements. In addition, this step helps determine whether the production technical documents accurately represent the production needs and whether the production conditions and process parameters are suitable for mass production. If the PCBA sample passes the “three-inspection” process, it is saved for record-keeping until the end of batch production.
The “three-inspection” process builds on the foundation of the first piece of production and compares subsequent samples against the guidance materials and comparison standards agreed upon by the manufacturer and the customer prior to production.
In addition, The correctness of the sample is comprised of the correctness of both the material and the soldering.
In PCB Assembly manufacturing, the customer guide document takes precedence over the sample, but in the absence of such a document, the sample is given priority. This essential principle serves as a protective measure for the foundry while also being a responsibility of the client. Adherence to this principle is critical in ensuring and enhancing quality while preventing potential quality issues resulting from errors made by both parties.
The utilization of the First Article Inspection (FAI) system has proved highly beneficial in detecting issues swiftly and preventing batch product destruction during prolonged periods of experience gained from processing PCBA.
Through the use of FAI, systemic issues such as fixture wear, improper installation and positioning, inadequate measuring tool precision, misinterpretation of drawings, incorrect materials or recipes, and more can be identified, enabling prompt implementation of corrective or improvement measures.
Ultimately, the primary goal is to identify elements that impact product quality during PCBA processing and production as soon as possible and to prevent batches of low-quality, discarded products from being produced.
The Significance of Pre-Production Samples and FAI Examples in PCB Design Engineering
In the field of PCB design engineering, both pre-production samples and first article inspection examples of a printed circuit board assembly (PCBA) play a vital role similar to the one described earlier. Interestingly, a first article inspection example can be viewed as a type of device sample in its own right. It is essential that both an approved PCBA pre-production sample and approved first article match the expected standards for the mass production of turnkey PCB assembly suppliers.
To ensure that your requirements are met, it may be beneficial to clarify expectations and evaluate the SMT assembly supplier’s understanding of your needs by approving a PCBA first article inspection sample before starting production. When these samples have been verified, pre-production samples can be considered “gold standards” and used as a reference point on the assembly production line and at quality control stations.
Typically, PCBA pre-production samples are custom-made by engineers who operate in the engineering team of the PCB assembly factory. Conversely, first articles are manufactured on the assembly production line, which can be located in the same assembly factory as the pre-production samples or the previous supplier’s factory.
Common Issues in PCBA First Article Inspection
Possible common issues in PCBA (Printed Circuit Board Assembly) First Article Inspection are:
● Component Issues: The quality of the components used in assembling the PCB can significantly impact its performance and reliability. Issues such as counterfeit, defective, or missing components can lead to non-functional circuits, reduced lifespan, or system failures.
● Soldering Issues: The soldering process is crucial in ensuring reliable and robust PCBAs. Issues such as poor soldering quality, insufficient or excess solder, voids, or shorts can result in circuit malfunctions, component damage, or reduced board reliability.
● Misalignment or Incorrect Placement: Incorrect placement or misalignment of components on the PCB can lead to critical issues such as incorrect circuit functioning, shorts, and damage to the board.
● Electrical Issues: The PCBA must undergo electrical testing to check the correctness of the connections among components or circuits. Electrical issues such as open circuits, shorts, incorrect voltages or currents, and poor grounding can result in non-functional circuits or system failures.
● Conformal Coating Issues: Conformal coatings are protective materials applied to the PCBA to provide environmental protection and prevent corrosion. Issues such as poor coating coverage, contamination, or incorrect application can impair the board’s integrity, leading to corrosion, electric leakage, or other electrical issues.
● Quality System Issues: Faulty production processes such as inadequate documentation, poor inspection procedures, and inadequate training, and lack of testing protocols can lead to significant issues in PCBA quality.
PCBA First Article Inspection aims to identify such common issues to detect their root causes and provide corrective action to prevent their occurrence in production runs, guaranteeing optimal product performance and reliability.
Summary
Choose First Article Inspection-Proficient CM
In the current landscape, it is common to face tight design schedules when developing printed circuit boards from start to market. Such high-pressure situations can lead to the problems we have previously discussed. As a preventive measure, it is crucial to ensure that the contracted manufacturer possesses the required knowledge, skills, and capabilities to conduct a comprehensive first article inspection and is knowledgeable of these potential issues. This approach provides the assurance that the subsequent production runs of the circuit board will be fabricated with 100% accuracy, while also giving you peace of mind.
At JarnisTech, we possess over two decades of expertise in the production and assembly of circuit boards, including first article inspection services. Our clients rely on us to recognize and address all concerns that may emerge during the FAI, thereby ensuring that their PCB and PCBA meets the stringent quality standards. If you are considering collaborating with us on your new venture and seeking additional information, please contact us without delay.