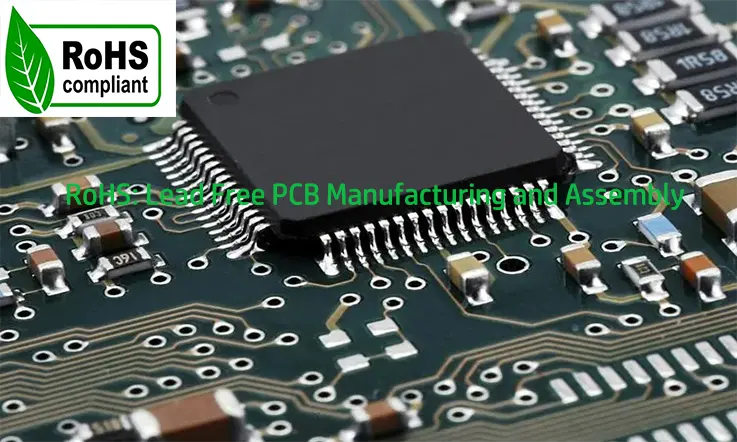
In recent years, there has been a growing concern for the environment and human health in the electronics industry. One of the major issues has been the widespread use of hazardous substances, such as lead, in the manufacturing of printed circuit boards (PCBs). To address this concern, the European Union introduced the Restriction of Hazardous Substances (RoHS) directive in 2006, which restricts the use of certain hazardous substances in electronic products, including lead. As a result, manufacturers have been under significant pressure to switch to RoHS-compliant lead-free PCBs.
This article will explore the manufacturing process of RoHS lead-free PCBs, which involves selecting RoHS-compliant materials and employing specific manufacturing techniques to ensure the absence of hazardous substances. We will also discuss the benefits of using RoHS lead-free PCBs, including environmental advantages, health benefits, and cost savings. Finally, we will examine the challenges associated with transitioning from traditional lead-containing PCBs to RoHS-compliant alternatives and provide best practices for successful implementation.
As the world becomes more aware of the harmful effects of hazardous substances, the use of RoHS lead-free PCBs is set to become the norm. By implementing RoHS-compliant practices, the electronics industry can take significant steps towards reducing its impact on the environment and human health.
Why RoHS Lead-free in PCB Manufacturing and Assembly So Important ?
● As a provider of PCB fabrication and assembly services, if you intend to conduct business within the European Union (EU), it is imperative that your assembly process is compliant with Restriction of Hazardous Substances (RoHS) regulations. Compliance ensures that every electronic or electrical device you import into the EU is compliant with RoHS and uses technology that aligns with the regulation. However, even if your business does not operate in the EU, it is essential that you plan to construct a preemptive RoHS-compliant, lead-free PCB assembly process. This is because many of the world’s major nations and states are planning legislations to limit the use of hazardous and environmentally damaging substances in industrial processes.
● RoHS implementation has played a significant role in reducing environmental waste, particularly in third world countries that bear the brunt of electronic garbage disposal. Additionally, concerns about lead’s health and liability risks have prompted regulatory authorities to limit its use in various industries. In the PCB assembly process, the health dangers associated with employees’ contact with solder paste have triggered a shift towards lead-free PCB assembly. A lead-free environment for PCB assembly reduces health risks for workers and responsibility for companies involved in the assembly process.
● By adopting lead-free soldering, PCB designers can simplify the board’s design, leading to significant advancements in miniaturization. Previously, PCB manufacturers found it challenging to fabricate small boards, but with a straightforward PCB layout, they can now produce smaller and more compact handheld devices, such as tablets and mobile phones. Lead-free soldering also enables the assembly of PCBs with fine, closely spaced components that the semiconductor industry demands.
● Lead-free soldering has made it possible to manufacturer printed circuit boards that are smaller, more tightly packed, and at a lower cost than in the past, leading to substantial cost reductions for businesses using RoHS-compliant and lead-free assembly methods. Although there is no unified standard controlling lead-free soldering, concerns about the reliability of lead-free assembly have been unfounded. Statistical data shows a decline in errors and customer complaints in the EU region since the implementation of RoHS rules.
● Moreover, businesses using lead-free and RoHS-compliant PCB assembly methods can market the feature as a vital selling advantage to prospective customers. Having a product that is both lead-free and RoHS-compliant puts you at an advantage in the international market.
What Is RoHS ?
RoHS, an acronym for Restrictions of Hazardous Substances, refers to a series of regulatory measures aimed at curbing the use of hazardous substances in electronic and electrical equipment. The six hazardous substances included in the RoHS guidelines are Lead (Pb), Mercury (Hg), Cadmium (Cd), Hexavalent Chromium (Cr VI), Polybrominated Biphenyls (PBB), and Polybrominated Diphenyl Ethers (PBDE).
Initially introduced for EU manufacturers in 2002, RoHS guidelines are now widely accepted across the entire electronics industry and a segment of electrical products. According to RoHS standards, the use of these prohibited materials should be limited to specific maximum concentration values that must not be exceeded during the production of electronic and electrical equipment.
There have been two distinct versions of the RoHS directive, including RoHS 2 and RoHS 3. RoHS 2, otherwise known as Directive 2011/65/EU, came into public view in 2011, while Directive (EU) 2015/863 was introduced in 2015. As part of Directive (EU) 2015/863, the original list of prohibited materials was expanded to include four additional components.
The Restriction of Hazardous Substances Directive (RoHS) regulates the use of ten substances in electrical and electronic equipment. The original six substances identified in 2011/65/EU and their maximum allowed concentration limits are:
● Lead (Pb) <1000ppm.
● Cadmium (Cd) <100ppm.
● Mercury (Hg) <1000ppm.
● Lexavalent chromium (Cr6+) <1000ppm.
● Polybrominated biphenyls (PBB) <1000ppm.
● Polybrominated diphenyl ethers (PBDE) <1000ppm.
The directive was expanded in 2015/863 (RoHS 3) to include four additional substances:
● Dibutyl phthalate (DBP) <1000ppm.
● Diisobutyl phthalate (DIBP) <1000ppm.
● Benzyl butyl phthalate (BBP) <1000ppm.
● Bis (2-ethylhexyl) phthalate (DEHP) <1000ppm.
Purpose of RoHS: The purpose of this regulation is to protect human health and the environment from the harmful effects of hazardous substances commonly used in EEE, such as lead, mercury, cadmium, hexavalent chromium, polybrominated biphenyls (PBBs), and polybrominated diphenyl ethers (PBDEs).
The RoHS Directive seeks to promote the design and production of eco-friendly products by limiting the use of hazardous substances in EEE. It also aims to address the growing problem of e-waste by encouraging the development of products that are less harmful to human health and the environment when they reach the end of their life cycle. By restricting the use of hazardous materials, the directive encourages manufacturers to develop new, safer materials and production processes and to reduce their environmental impact.
The RoHS Directive applies to a wide range of electrical and electronic equipment, including large household appliances, small household appliances, IT and telecommunications equipment, lighting equipment, electrical and electronic tools, toys, recreational and sports equipment, medical devices, monitoring and control instruments, and automatic dispensers. Compliance with the RoHS Directive is mandatory for manufacturers who wish to sell their products in the EU.
Will RoHS Impact the Quality of PCBs ?
RoHS (Restriction of Hazardous Substances) compliance alone does not improve the quality of printed circuit boards (PCBs). However, the switch to lead-free PCB manufacturing under RoHS regulations has significant implications for the PCB manufacturing and soldering processes. The higher temperatures required for lead-free soldering necessitate modifications to the PCB manufacturing process. As a result, newer FR-4 materials have been developed to withstand the increased temperatures without compromising the durability of the final product.
Testing and Certification of RoHS Lead Free PCB
To ensure compliance with RoHS (Restriction of Hazardous Substances) regulations for PCB (Printed Circuit Board) products, testing and certification are required. Here are some key steps involved in testing and certifying RoHS compliance for PCB products:
● Identify relevant regulations: The first step is to identify relevant RoHS regulations and requirements, which include identifying the substances in PCB products that are restricted under RoHS regulations.
● Determine which of the substances are present: The second step is to determine which of the substances are present in the product and at what levels through substance composition testing.
● Conduct materials tests: Material tests may include destructive and method-specific analyses to trace contaminants and ensure that there are no prohibited substance in the input materials.
● Analyze test results: PCB manufacturer following the testing will analyze the test results of both substance composition and material analyses conducted by third-party labs.
● File a declaration of compliance (DoC): Following the conclusion of testing and analysis, the PCB manufacturer issues a declaration of compliance, or DoC, which states that the product is fully compliant with RoHS regulations.
● Obtain certification: PCB manufacturers can obtain external certification from third-party labs/accreditations, to confirm the compliance of their product to RoHS regulations. This is useful for validating the result and gaining the trust of the customers and other stakeholders.
How to Modify Your PCB and Assembly to Meet RoHS and Lead-Free Standards ?
Prior to the implementation of RoHS directives, the electronic industry extensively employed tin-lead solder due to its exceptional bonding capabilities, as well as a surface finish (HASL with lead) to prevent copper corrosion. However, the implementation of RoHS regulations throughout the EU has prompted PCB makers and assemblers to modify their traditional manufacturing methods, raw materials, components, and equipment.
Today, RoHS-compliant lead-free solder alloys are commonly used in the electronic industry, along with lead-free components and PCB surface treatments. Even though some customers still request tin-lead PCBs and assembly procedures, many do not. These modifications have resulted in less e-waste and reduced contamination of groundwater.
It is recommended that electronic engineers verify with their PCB manufacturers and assembly service providers prior to initiating their next project to determine whether they can provide lead-free and RoHS-compliant manufacturing. RoHS compliance entails performing activities in accordance with RoHS regulations, allowing individuals to meet the RoHS requirements for their electronic products and potentially increase sales during subsequent marketing efforts.
RoHS Lead Free Regulations and Compliance Requirements for the PCB Industry
The RoHS (Restriction of Hazardous Substances) Directive is an EU regulation that restricts the use of certain hazardous substances in electrical and electronic equipment (EEE). The following are the RoHS regulations and compliance requirements for the PCB (Printed Circuit Board) industry:
● Restriction of Hazardous Substances: The RoHS Directive restricts the use of six hazardous substances in EEE, which include lead, mercury, cadmium, hexavalent chromium, polybrominated biphenyl (PBB) and polybrominated diphenyl ether (PBDE).
● Compliance with regulations: PCB manufacturers must comply with all applicable RoHS regulations, including those that are specific to their products as they may cover a considerable number of components and materials.
● Product categorization: PCBs must be categorized according to their level of compliance with RoHS regulations. The categories include Category 1 (appliances and machines), Category 2 (IT and telecommunications), and Category 3 (consumer electronics).
● Testing requirements: PCB manufacturers must test their products to ensure that they comply with RoHS regulations. These tests include substance composition testing, and materials tests from suppliers.
● Documentation: PCB manufacturers must keep documentation of their compliance with RoHS regulations. This includes manuals, procedures, records, and certificates of compliance.
● Third-party auditing: Some industries mandate third-party auditing to support and verify RoHS compliance. The audits may entail examining critical elements of the manufacturing process, conducting interviews, or reviewing reports and other documentation.
Challenges Faced by the PCB Industry in Implementing Lead-free RoHS Compliance
The transition to lead-free RoHS-compliant PCB (Printed Circuit Board) production can pose several challenges for the PCB industry. Some of these challenges include:
● High manufacturing costs: The shift to lead-free materials requires substantial investments in new manufacturing equipment, materials, and personnel training. This can result in increased production costs, which may be passed on to customers.
● Limited availability of lead-free materials: Finding reliable sources of lead-free materials compatible with PCB production processes can be challenging, especially for smaller manufacturers who may not have the same bargaining power as larger companies.
● Compatibility issues with existing manufacturing processes: Because lead-free materials have different properties from traditional lead-based materials, some manufacturing processes may need to be modified or new ones developed to accommodate these changes.
● Implementation timeline: RoHS regulations require all electronic products to be free of certain hazardous substances. In some cases, manufacturers may struggle to meet these requirements within the designated timeline, particularly if orders have already been placed or production processes are already underway.
● Quality control and testing: The use of new materials and manufacturing techniques required for lead-free RoHS compliance means that manufacturers must develop new quality control protocols and testing methods to ensure that products meet required standards.
Achieving lead-free RoHS compliance in the PCB industry requires a significant investment of time, money and resources, and may result in some initial challenges for manufacturers. However, the benefits of better environmental protection and worker safety, along with enhanced marketability, can outweigh these challenges in the long term.
Strategies for Successful RoHS Lead Free Compliance in the PCB Industry
Here are some strategies that can help PCB (Printed Circuit Board) manufacturers achieve successful RoHS (Restriction of Hazardous Substances) compliance:
● Conduct a thorough assessment of current manufacturing processes: This includes identifying the use of hazardous substances and evaluating current processes to ensure that they comply with RoHS regulations. This assessment can help manufacturers better understand the changes they need to make in their production process.
● Develop a comprehensive plan for transitioning to lead-free materials: This includes identifying reliable sources of lead-free materials, evaluating their compatibility with current production processes and making necessary changes to accommodate them.
● Enhance quality control and testing protocols: Testing for hazardous substances must be incorporated as part of the manufacturing process. To achieve this, a dedicated testing lab may need to be set up.
● Provide employee training: The adoption of new materials and manufacturing processes presents an opportunity to provide relevant training to employees, which will increase staff competency and accuracy of testing procedures.
● Develop positive relationships with suppliers: PCB manufacturers need to have a relationship with reliable suppliers. This can ensure the timely delivery of lead-free materials and can also help maintain the quality of the product.
● Establish clear lines of communication with customers: Establishing and maintaining open channels of communication with customers and stakeholders is crucial. Customers should be made aware of the changes in production processes and expected delivery timelines.
● Partner with third-party auditors: Partnering with third-party auditors can help PCB manufacturers identify areas of non-compliance in their production processes early. This can help companies remain compliant with regulatory requirements while avoiding penalties for non-compliance.
Why Choose Us ?
As a PCB manufacturing and assembly factory, we has the capability to provide customized printed circuit boards and assembly services with surface finishes that meet the RoHS criteria. Our selection of RoHS-compatible surface finishes includes lead-free HASL, ImAg, ENIG, and other similar options. Furthermore, we are equipped to provide RoHS-compatible laminate material that can endure high temperatures during the PCB assembly process. This meets the growing demand for environmentally-friendly products from our customers, ensuring their satisfaction with our services.
● PCB Laminates: JarnisTech is well-equipped to provide RoHS-compliant circuit boards using laminate materials that can withstand the high temperatures encountered during the assembly process. It is crucial to note that certain lead-free assembly procedures require the laminate base material to withstand temperatures above 260 degrees Celsius or 500 degrees Fahrenheit for extended periods. To address this challenge, we have expanded our collection of high-temperature laminates, allowing our clients to meet the more rigorous temperature cycling criteria associated with certain lead-free assembly applications.
JarnisTech has received UL approval to process high thermal capacity materials created by Nelco, Isola, and Polyclad. These materials have passed UL tests for maximum operating temperatures of 130 degrees Celsius, solder limitations of 288 degrees Celsius for twenty seconds, a 94-V0 flame rating, and direct support of current-carrying components. Each of these laminate systems fulfills the fundamental requirements for IPC 4101A standard sheets 24, 26, and 28.
The electrical, thermal, and physical properties of laminate materials can vary significantly across different manufacturers. For the most part, we maintain the products of a single manufacturer in stock and ready for use. If you have any specific questions, please contact the JarnisTech sales professional assigned to your account.
● Lead Free Solder For PCB Assembly: We has recently invested in and installed a new Penta 580 HASL machine for lead-free soldering. Following successful process trials, this equipment began production in the second week of September 2004. To produce RoHS compliant printed circuit boards (PCBs), we uses Nihon Superior SN100CL copper alloy solder for both prototype and production PCBs.
This specific solder composition includes 99.3 percent tin, 0.66 percent copper, and a trace amount of nickel. By using this lead-free alloy, we are capable of processing panels at a temperature comparable to that required for lead-based solder. We conducted several processing experiments to ensure comprehensive coverage and exceptional surface qualities, and the results were outstanding. Furthermore, the finish has demonstrated a remarkable co-planarity for a HASL process.
Trends and Future Outlook of Rohs Lead-Free PCB Industry
The adoption of RoHS lead-free PCBs has been increasing steadily, driven by regulatory requirements and consumer demand for more sustainable and eco-friendly electronic products. In the future, development of new, more efficient and cost-effective manufacturing processes for lead-free PCBs is likely to accelerate their adoption, making them more attractive to manufacturers. Technological advancements, such as the increasing use of advanced packaging technologies like fan-out wafer level packaging, are also expected to drive the market for lead-free PCBs.
Additionally, the ongoing development of the Internet of Things (IoT) and smart home technologies is expected to increase demand for smaller, energy-efficient devices, which are well-suited to the use of lead-free PCBs. Overall, the future outlook for lead-free PCBs is positive, and their adoption is likely to continue to increase as the emphasis on environmental sustainability grows.
Conclusion
Do You Find RoHS Lead-free PCB Manufacturing And Assembly ?
The use of lead-free PCBs is becoming increasingly important as we strive towards more sustainable and eco-friendly electronic products. The hazards of lead to human health and the environment make the use of RoHS lead-free PCBs a crucial step towards a more responsible approach to electronics manufacturing.
With the growing demand for eco-friendly products and regulatory requirements driving their adoption, RoHS lead-free PCBs are likely to become more prevalent in the electronics industry. As manufacturing processes continue to develop and new technologies emerge, lead-free PCBs are expected to offer even more benefits to manufacturers and consumers alike, paving the way for a greener and cleaner future.
At JarnisTech, we prioritize compliance when it comes to providing PCBs for your specific applications. We recommend searching for lead-free circuit boards that align with the relevant regulations. Our commitment to compliance is evident in all our products, as each one is equipped with a RoHS Certification of Compliance. Moreover, our products come in various surface treatments and materials that meet the RoHS standard.
If you require further information or pricing estimates on our lead-free printed circuit boards, please do not hesitate to contact us. We are always available to assist you with any inquiries you may have.