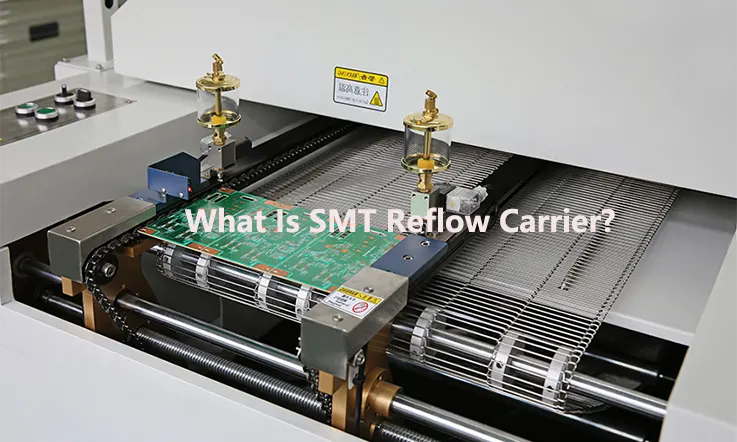
Solder paste printing, surface mount device installation, and reflow soldering are all processes that fall under the category of surface mount technology (SMT). These surface mount technology processes have requirements for SMT tooling, and the usage of these tools can maximize the efficiency of SMT. The terms “stencil,” “test jig,” and “reflow carrier” all refer to pieces of SMT tooling that are used frequently. In this article, we will discuss everything there is to know about the Reflow Carrier, which is also known as the SMT Carrier, the PCB Pallet, and the SMT Pallet. This component serves as a support and transport mechanism for printed circuit boards (PCBs) during all of these SMT operations.
If you are dealing with flex PCB assembly, however, reflow carrier is an absolute must for your SMT assembly. This is not the case when working with rigid board assembly, which may or may not require it at times. When it comes to new product introduction (NPI) or high-volume PCB assembly runs, reflow carrier is frequently an important component for attaining success that is consistent and of the highest quality.
This tool has been around for some time in the industry of electronic manufacturing, and it has been demonstrated to be an important component in the design of reliable PCB assembly procedures. When determining whether or not to utilize reflow carriers, it is common practice to take into account solely the mechanical support they provide; nonetheless, these carriers serve numerous purposes and offer various advantages.
What Is SMT Reflow Carrier ?
The printed circuit board (PCB) is placed on the so-called SMT reflow carrier and then transferred to the reflow oven. In most cases, the reflow carrier will have a positioning column that can be used to secure the PCB and prevent it from shifting out of position or distorting itself.
To better prevent the board from being deformed during the reflow process, certain high-end reflow carriers have a cover—typically for FPC—and magnets on the carrier, which are then downloaded as suction cups. Certain hard-board PCBs will also employ the cover plate to prevent certain components from slipping as they pass through the furnace.
Reflow Carrier Material: Durostone
When you go to a PCB assembly company, you might notice that the machines and conveyors in the SMT line all have dark grey smt carriers on them. What kind of material is used as the carrier? This topic is important to a lot of individuals. The carrier material in JarnisTech is always Nanometer Composite Stone, which is also known as Durostone. Occasionally, though, Aluminum is used instead. When it comes to reflow carrier fabrication, the most frequent material to employ is durostone.
Durostone is a high-strength glass fiber reinforced plastic that is designed for heavy-duty applications. It provides exceptional mechanical and thermal properties even when exposed to high temperatures, as well as dimensional stability and the preservation of carriers’ flatness through multiple reflowing cycles in the SMT manufacturing process.
The production of Durostone involves the utilization of Polyester (PET), Vinylester, Epoxid- and modified Epoxy resins, which are then mixed with carbon, glass, or basalt fiber reinforcements. Durostone carriers are designed to withstand extreme temperatures and can be continuously reused over 20,000 times. All PCB manufacturers and assembly factory can enjoy a great deal of competitive advantage by using SMT carriers made with durostone. You can think of the SMT carrier cost as an NRE fee, and you can regard it as an useful tooling alternative that will have a short return on investment term.
What Qualities Does the Perfect SMT Reflow Carrier Need ?
● To be able to be reused without deformation, the temperature at which softening deformation occurs must be higher than 300 degrees Celsius. This is the primary condition that must be met.
● Should have a low expansion rate when subjected to heat. The behavior of most materials can be categorized into two distinct categories: thermal expansion and cold contraction. If the thermal expansion of the reflow carrier is too great, it will ruin the printed circuit board (PCB).
● This material has the potential to be lightweight and processed. Heavy reflow carriers are not practical for everyday use in an electronics manufacturing because they require operators to physically move them from one location to another.
● The ideal material should be resistant to heat absorption or heat dispersion. Because the reflow carrier should be reusable, if the temperature cannot be decreased quickly enough to be reached by human hands after backsoldering, additional loads will need to be prepared, increasing the cost.
● The material must be as inexpensive as possible and capable of mass production.
● In most cases, an aluminum alloy will be used as the material for the carrier of the furnace. In addition, high carbon steel and magnesium alloy are utilized in the manufacturing process in order to create the reflow carrier. Despite the fact that aluminum alloy is lighter than standard iron metal, it nevertheless has a certain amount of weight.
And since aluminum alloy is a substance that readily absorbs heat, it is necessary to either wear heat-insulating gloves after removing it from the furnace or wait for a certain amount of time before picking it up. This makes the process a little less convenient than it otherwise would be. In addition, there is a specialized reflow carrier, which is made of a substance that is reasonably inexpensive but has a short service life. Recently, however, there have been some reactions that will be an allergic occurrence.
Why Would You Use an SMT Reflow Carrier ?
1. Reduce PCB Deformation
Warpage of stiff PCBs, rigid-flex boards, and flex circuits can drastically impair yields, however it can be reduced by providing mechanical support across the entirety of the SMT line (top and bottom assembly). SMT carriers are absolutely necessary when processing thin substrates, but they are frequently advantageous when working with thick substrates. The design characteristics selected for a particular SMT pallet are crucial for minimizing warpage. During the reflow process, threaded inserts may be used to secure the PCB board to the carrier.
During the processes of solder paste screen printing, pick and place, and reflow, a wedge effect is created by utilizing tapered tooling pins that are located in the tooling holes of the circuit board, regardless of whether the tooling holes are plated or non-plated. This effect is used to secure the printed board to the PCB pocket. By utilizing flush-mounted “pushers” with different spring K-factors (depending upon PCB board thickness and stack-up characteristics), tension or pressure is generated against these tapered pins. This helps to preserve printed board flatness throughout the entire process.
2. Prevent Heavy Parts From Falling
The reflow carrier can be designed to hold these parts that are likely to come off during the second weld after the first side of the piece has been welded. These are often certain hefty parts, such the mesh line connector, that are at risk of falling off during the second weld.
Both of the aforementioned issues are, in fact, connected to the region of the SMT reflow oven that experiences high temperatures. The process that does not use lead is now used in the majority of the products. The temperature at which lead-free SAC305 solder paste begins to melt is 217 degrees Celsius, while the melting point of SAC0307 solder paste is between 217 and 225 degrees Celsius. It is typically recommended that the highest temperature that can be reached during back welding is between 240 and 250 degrees Celsius.
However, because of the higher cost of Tg150 plates, we almost always go for FR4 plates instead. Also, the thickness of the printed circuit board is decreasing, going from 1.6 mm to 0.8 mm, and even 0.4 mm for PCB. When subjected to the high temperatures associated with SMT reflow, a PCB with such a low thickness has a greater propensity to have deformation issues.
SMT reflow carrier is used to get around the issue of PCB deformation and parts falling out. It typically employs the positioning column to fix the positioning hole of the PCB. This allows it to effectively maintain the shape of the PCB even when the plate deforms at high temperatures, which helps to reduce the deformation of the plate. However, there must be additional reinforcement to assist the middle position of the plate because the force of gravity can cause the plate to bend and sink.
In addition, by taking use of the non-deformable nature of the vehicle, it is feasible to provide support for the heavier section, so preventing the parts from coming loose and falling off. However, the design of the reflow carrier needs to be very cautious so as to avoid excessive support points lifting the part and producing inaccurate printing of solder paste on the second side.
Advantages of SMT Reflow Carrier
● Conveyance: Several “odd-shaped” PC board layouts are difficult to convey via the SMT process equipment, and carriers give robust edge step features that eliminate the need for smooth conveyance. While designing a carrier, ensure that the edge step thickness is given adequate consideration.
● Edge Clearance: During the processing of the first or second side of assembly, without an SMT carrier, there is a potential for parts that are too close to the edge of the PCB board to be damaged. Clearance for these components can be designed into SMT carriers from either side, and the carriers will still be able to support the rest of the printed circuit boards in a reliable manner.
Vision and Alignment: Reflow carriers can offer the necessary or additional fiducials for optimal stencil registration and SMD placement precision. Ask the provider of the tooling to describe how they design and construct carrier fiducials such that they are strong and easily seen by your process equipment.
Process Standardization: If all of the assemblies in your product range have the same carrier design—including width, thickness, and material—the changeover time for machines and/or lines can be shortened. In the case of processing on a single side, reflow carriers are frequently suitable for use in “downstream” operations such as AOI or electrical testing. With printing or placement equipment, the use of SMT tooling can also reduce the requirement for expensive vacuum or specialized support plates. Carriers offer the additional benefit of requiring no additional operator training, engineering assistance, or equipment maintenance support from their customers.
● Protection/Heat Shielding: During the secondary reflow process, it is frequently possible to insulate heat-sensitive components. A sturdy design will help ensure that temperatures are distributed evenly across the PCB board, hence decreasing the board’s thermal impact.
● Critical Alignment of Parts: During the reflow process, top cover alignment plates or incorporated carrier features can be utilized to assist in achieving the necessary alignment or spacing of components like edge connectors.
● De-paneling Improves Stencil Alignment: In the presence of fine pitch devices, yields can be increased by printing smaller pictures following de-paneling processes. The reflow carrier is often the only option for transporting and processing the SMT assembly when PCB boards are received in a de-paneled state. Use cautious while determining how many photos to load into a given carrier. Although output quality improves linearly with quantity, stencil-to-PCB alignment suffers exponentially as more and more images are included.
● Creating a Unique Reflow Carrier: The development of a custom SMT carrier for each unique circuit board assembly is an essential part of the project’s success. It is important to the success or failure of any carrier to have a comprehensive understanding of thermodynamics as well as the impacts that a composite carrier will have in the environment of reflow.
What Is Full Process Carrier ?
Common SMT reflow carriers are only used when the board is going through the welding furnace. This means that processes that take place before the welding furnace, such as applying solder paste or patching holes in the board, do not require the use of reflow carriers, which allows for a reduction in the number of reflow carriers.
However, If the circuit board has already been deformed prior to the solder paste printing, not only will the printing position of the solder paste be offset, but the thickness of the solder paste will also change, both of which are typically undesirable for the fine pitch parts because of the increasingly thin and dense PCBs and the higher requirements for precise solder paste printing. When any of the issues described above arise, the best approach to address them is by making modifications to the design.
If none of the designs are able to solve the problem, we will have no choice but to begin using the SMT full process carrier, which is indistinguishable from the reflow carrier. The only difference is that you have to take into account the process of printing solder paste, which means that the printed circuit board (PCB) needs to be elevated above the surface of the vehicle after it has been placed in the carrier. Even the positioning column has to be followed precisely, or else there would be an issue with the solder paste.
Depending on the length of the SMT manufacturing line, it is reasonable to anticipate that the number of full course SMT reflow carriers will increase by a factor of multiples. When it comes to things that are mass-produced, the overall cost may be just a tiny amount of money, but when it comes to products that are small and diverse, the total cost of these vehicles is practically enough to buy a car.
Conclusion
JarnisTech Provide PCB manufacturing and Turnkey Assembly Service
At JarnisTech, we provide high-quality PCB manufacturing and Assembly. This means that we can provide from component sources to printed circuit board fabrication and PCB assembly services for clients.
At the same time, in the PCBA assembly process, we also provide many kinds of SMT tools. For example, SMT reflow carrier, and if you want to use an SMT reflow carrier, you need to calculate the cost of loading and unloading the product and keep in mind the idea of the total cost and make contact with us. We provide a much better service for your PCB and PCBA projects.