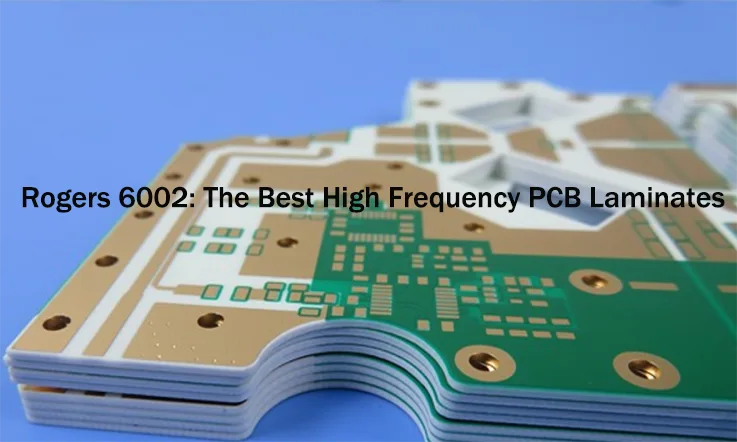
For buyers and manufacturers seeking to enhance the quality and durability of their electronics and electrical appliances, Rogers 6002 laminates present a compelling solution. These laminates are specifically designed to meet the rigorous demands of the industry. By familiarizing yourself with the characteristics and benefits of Rogers 6002 laminates, you can effectively fortify your products and ensure their long-term success. Let us delve into the realm of Rogers 6002 laminates and discover how they can significantly bolster your offerings.
What Is Rogers Ro6002 Laminates?
Rogers Corporation has earned a distinguished reputation for its production of premium circuit materials that cater to the demanding requirements of high-reliability designs prevalent in today’s world. Among its notable offerings, Rogers 6002 laminate stands out as the pioneering choice possessing a low dielectric constant (Dk) while delivering exceptional mechanical and electrical properties essential for constructing microwave structures.
RT/duroid 6002 laminate is reinforced with woven glass, thereby significantly enhancing its structural support by increasing the PTFE-to-glass ratio. This reinforcement ensures that microwave structures produced using RT/duroid 6002 exhibit both electrical stability and mechanical reliability. Since its introduction in the late 1980s, this laminate has revolutionized the selection of circuit board materials for microwave engineers. Prior to its advent, engineers had to choose between high or low Dk laminates based on polytetrafluoroethylene (PTFE).
However, it was recognized that these materials had substantial coefficients of thermal expansion, which could result in dimensional stability challenges. In this context, duroid 6002 laminate emerged as a game-changer by offering a solution that enables both mechanical and electrical stability across a wide range of temperatures.
The advent of Rogers 6002 laminates provided designers with the opportunity to develop multilayer boards that could be combined with FR4 to achieve the desired frequency coverage essential for high-reliability applications. These laminates were purposefully designed to offer superior advantages while mitigating the drawbacks associated with PTFE-based materials.
Rogers Corporation has meticulously crafted these laminates to ensure accuracy. Not only do they exhibit exceptional mechanical and electrical properties, but they also facilitate the production of high-frequency multilayer boards with impressive yields. With duroid 6002 laminate, designers can confidently rely on the long-term reliability of plated through holes (PTHs).
Properties of Rogers 6002
Rogers 6002 laminates possess a multitude of advantageous properties that render them highly suitable for various applications. These properties can be summarized as follows:
Dielectric Constant: Rogers 6002 laminates exhibit an exceptional dielectric constant of 2.94 ±40. This characteristic makes them highly desirable for utilization in multilayer constructions, where precise electrical performance is crucial.
Low Thermal Coefficient: The thermal coefficient of the dielectric constant (Dk) in Rogers 6002 laminates is remarkably low. This attribute empowers designers to achieve the necessary electrical balance required in modern applications, where thermal stability is paramount.
Low Z-Axis Coefficient of Thermal Expansion: Rogers 6002 laminates possess an impressively low coefficient of thermal expansion (CTE) in the Z-axis. This attribute significantly contributes to the reliability of plated-through holes (PTHs). Notably, rigorous temperature cycling tests, exceeding 5000 cycles, have been conducted on these materials without any recorded failures.
Low Tensile Modulus: The tensile modulus (X, Y) of Rogers 6002 laminates is notably low. This characteristic reduces the stress exerted on solder joints, allowing for controlled expansion of the laminate with minimal impact from the coefficient of thermal expansion (CTE) of the adjacent metal.
Exceptional Dimensional Stability: Rogers 6002 laminates offer exceptional dimensional stability, with dimensional changes of approximately 0.5 mils per inch. This achievement is accomplished by aligning the coefficients of expansion in the X and Y directions with that of copper. As a result, double etching is eliminated, and tight positional tolerances can be consistently maintained.
Dissipation Factor: Rogers 6002 laminates exhibit a remarkably low dissipation factor of 0.0012 at 10GHz. The dissipation factor quantifies the rate at which energy is lost in a dissipative system, encompassing both mechanical and electrical properties. The minimal dissipation factor of Rogers 6002 laminates underscores their efficiency and effectiveness in preserving the integrity of electrical signals.
All in All, Rogers 6002 laminates encompass a comprehensive range of properties that position them as an ideal choice for various applications. These properties include exceptional dielectric constant, low thermal coefficient, low Z-axis coefficient of thermal expansion, low tensile modulus, exceptional dimensional stability, and a low dissipation factor at high frequencies.
Benefits and Advantages of Rogers 6002 Laminate
Excellent Electrical Performance: Rogers 6002 exhibits exceptional electrical properties, including low dielectric loss and high signal integrity. Its low loss tangent (Df) ensures minimal signal attenuation, making it suitable for high-frequency applications.
Stable and Consistent Performance: The 6002 series offers stable electrical performance across a wide frequency range, ensuring reliable signal transmission. It maintains its electrical characteristics over time and under varying environmental conditions.
Design Flexibility: Rogers 6002 is available in a range of thickness options, allowing for design flexibility to meet specific circuit requirements. It offers choices such as 0.002″, 0.004″, 0.006″, 0.008″, 0.010″, 0.012″, 0.015″, 0.020″, 0.030″, and 0.060″ (in inches).
High Mechanical Strength: The woven fiberglass reinforcement used in the manufacturing of Rogers 6002 provides excellent mechanical strength and dimensional stability. This makes it suitable for applications where robustness and reliability are crucial.
Chemical Compatibility: The 6002 series laminate exhibits good chemical resistance, making it compatible with various manufacturing processes and allowing for easy integration into the production line.
RoHS Compliance: Rogers 6002 laminates are compliant with the Restriction of Hazardous Substances (RoHS) directive, ensuring the materials used are environmentally friendly and free from hazardous substances.
Broad Application Range: Rogers 6002 is suitable for numerous high-frequency circuit applications, including RF amplifiers, power amplifiers, antennas, couplers, filters, and more. Its excellent electrical performance makes it suitable for demanding wireless communication systems and radar applications.
It’s important to note that the specific benefits and advantages of Rogers 6002 can vary depending on the application requirements and the overall design considerations. Consulting the datasheets and technical specifications provided by Rogers Corporation can provide more detailed information tailored to specific use cases.
Rogers 6002 laminates Application
Rogers 6002 laminates find extensive application in various industries where the demand for high-performance circuit materials is paramount. The exceptional properties of Rogers 6002 laminates make them suitable for a wide range of applications, including:
Microwave and RF Electronics: Rogers 6002 laminates are specifically designed for microwave and RF circuitry. They offer low dielectric constant (Dk) and excellent electrical properties, making them ideal for high-frequency applications such as antennas, power amplifiers, filters, couplers, and radar systems.
High-Frequency PCBs: The mechanical and electrical stability of Rogers 6002 laminates enable the production of high-frequency printed circuit boards (PCBs). These laminates allow for the design and fabrication of multilayer boards that can handle the frequencies required in high-reliability applications.
Aerospace and Defense: The reliability and performance of Rogers 6002 laminates make them well-suited for aerospace and defense applications. They can be used in radar systems, communication equipment, satellite technologies, and other critical electronic components where durability, signal integrity, and thermal management are crucial.
Automotive Electronics: Rogers 6002 laminates find application in automotive electronics, particularly in advanced driver-assistance systems (ADAS), radar modules, collision avoidance systems, and vehicle communication systems. These laminates provide the necessary reliability, signal integrity, and thermal properties required in the automotive industry.
Telecommunications: Rogers 6002 laminates are employed in telecommunications infrastructure, including base stations, antennas, and wireless communication systems. Their high-frequency capabilities and stable performance ensure efficient signal transmission and reception.
Industrial Electronics: In industrial settings, Rogers 6002 laminates are utilized in various applications such as power electronics, control systems, sensors, and instrumentation. The laminates’ mechanical strength and electrical reliability make them suitable for demanding industrial environments.
Medical Devices: Rogers 6002 laminates are also used in medical devices where high-frequency performance and reliability are essential. They can be found in applications such as medical imaging equipment, monitoring systems, and diagnostic devices.
The versatility and superior characteristics of Rogers 6002 laminates make them a preferred choice for manufacturers and designers in industries that require robust and high-performance circuit materials.
Key Differences Between Rogers 6002 and RO3000 Laminate Series
Rogers Corporation offers a range of high-frequency laminates for RF and microwave applications, including the Rogers 6002 and RO3000 series. While both series are designed for similar applications, there are some key differences between them. Here are the main contrasting features:
Dielectric Constant (Dk):
Rogers 6002: The Rogers 6002 laminate series typically has a lower dielectric constant, typically around 2.94 to 3.02. It offers consistent and stable electrical performance across a wide frequency range.
RO3000: The RO3000 laminate series has a higher dielectric constant compared to Rogers 6002, typically ranging from 3.38 to 3.66. This higher Dk can provide advantages in certain applications where impedance matching or smaller dimensions are required.
Loss Tangent (Df):
Rogers 6002: The Rogers 6002 series has a relatively low loss tangent (Df), which means it exhibits lower signal loss and higher signal integrity. The Df values for Rogers 6002 are typically around 0.0015 to 0.0030.
RO3000: The RO3000 series has a slightly higher loss tangent compared to Rogers 6002. The Df values for RO3000 typically range from 0.0023 to 0.0031. However, it still provides excellent electrical performance for high-frequency applications.
Thickness Options:
Rogers 6002: The Rogers 6002 series is available in a wide range of thickness options, including 0.002″, 0.004″, 0.006″, 0.008″, 0.010″, 0.012″, 0.015″, 0.020″, 0.030″, and 0.060″ (in inches).
RO3000: The RO3000 series also offers various thickness options, but the available range might differ. Typical thickness options for the RO3000 series include 0.005″, 0.010″, 0.015″, 0.020″, 0.031″, 0.040″, and 0.060″ (in inches).
Manufacturing Process:
Rogers 6002: The Rogers 6002 series is manufactured using a woven fiberglass reinforcement, which provides good dimensional stability and mechanical strength.
RO3000: The RO3000 series utilizes a ceramic-filled PTFE (Polytetrafluoroethylene) composite material. This construction gives it a lower coefficient of thermal expansion (CTE) and improved dimensional stability.
It’s worth noting that both series offer excellent electrical performance and are suitable for high-frequency applications. The choice between Rogers 6002 and RO3000 would depend on specific application requirements, such as desired dielectric constant, loss tangent, and thickness options. Consulting the datasheets and technical specifications provided by Rogers Corporation would provide more detailed information and help in making an informed decision.
Rogers 6002 Vs RO4000 Laminate Series
In the realm of circuit applications, two viable options for laminates are the Rogers 6002 and RO 4000 series. However, these materials possess distinct characteristics that can impact circuit design.
The RO 4000 series laminates are composed of glass-reinforced hydrocarbon/ceramic, while the RO 6000 series consists solely of ceramic and PTFE composite. Unlike the RO 6000 series, the RO 4000 series does not require special surface treatments like sodium etching.
Another differentiating factor is rigidity. RO 4000 laminates are comparatively more flexible than the RO 6002 series, making them more prone to handling damages. Conversely, the RO 6002 series laminate exhibits substantially superior electrical properties compared to the RO 4000 series laminates.
Rogers 6002 High-Frequency Laminates Fabrication Guidelines
When working with Rogers 6002 high-frequency laminates, it is crucial to follow proper fabrication guidelines to ensure optimal performance and reliability. Here are some key guidelines to consider:
Material Handling: Prior to fabrication, it is essential to handle Rogers 6002 laminates with care to prevent any damage or contamination. Always store the laminates in a clean and controlled environment, protected from moisture, dust, and excessive heat.
Cutting and Drilling: When cutting or drilling the laminates, use sharp tools and appropriate cutting techniques to minimize delamination and ensure clean edges. Avoid excessive pressure or heat that could cause damage to the laminate.
Cleaning: Before any subsequent processing steps, ensure that the laminates are thoroughly cleaned to remove any contaminants, oils, or residues. Use compatible cleaning agents recommended by Rogers Corporation and follow their guidelines for cleaning procedures.
Surface Preparation: Prior to any surface treatment or metallization, it is crucial to prepare the laminate surfaces adequately. Follow the recommended surface preparation techniques, such as mechanical abrasion or chemical treatments, to enhance adhesion and promote proper bonding.
Copper Cladding: When applying copper cladding to Rogers 6002 laminates, ensure that the copper foil is compatible with the laminate material and the desired application. Follow the recommended lamination methods and parameters to achieve a reliable bond between the copper and the laminate.
Etching: If etching is required for circuit formation, use compatible etchants and follow the recommended etching processes. Take care to control the etching time and temperature to achieve precise circuit patterns without compromising the laminate’s integrity.
Plating: When plating conductive materials on Rogers 6002 laminates, use compatible plating solutions and adhere to the recommended plating parameters. Properly prepare the laminate surfaces, including appropriate activation and pre-treatment steps, to ensure optimal plating adhesion and quality.
Soldering: If soldering components to the laminate, use compatible soldering techniques and materials. Pay attention to the recommended soldering temperatures and dwell times to prevent excessive heat exposure that could potentially damage the laminate.
Testing and Quality Control: Throughout the fabrication process, implement rigorous testing and quality control measures to ensure the final product meets the desired specifications. Perform electrical testing, impedance measurements, and other relevant tests to validate the performance of the PCB laminates.
It is essential to consult the specific fabrication guidelines provided by Rogers Corporation for Rogers 6002 laminates. These guidelines may include detailed instructions, recommended processes, and specific parameters to achieve optimal results during fabrication. Adhering to these guidelines will help maximize the performance, reliability, and longevity of circuits fabricated using Rogers 6002 laminates.
How to Choose the Best Rogers 6002 PCB Manufacturer?
In the global market, a wide range of manufacturers specializes in the production of Rogers 6002 laminates. These reputable manufacturers typically maintain official websites that can be easily accessed through popular search engines such as “Google” or “Bing.”
To compile a comprehensive list of these manufacturers, conducting a search using relevant keywords will yield numerous results. Once the list is compiled, it is advisable to thoroughly evaluate each manufacturer’s website and initiate contact with their representatives to gather further information.
During the evaluation process, certain criteria should be considered to select the most suitable manufacturer:
Product Range and Competitive Pricing: A reliable manufacturer will offer a diverse range of Rogers 6002 laminate products, accompanied by competitive pricing that aligns with market standards.
Compliance with Standards: It is crucial to ensure that the manufacturer possesses all the necessary manufacturing licenses and adheres to international and national quality and safety standards. This guarantees the reliability and quality of their products.
Well-Equipped Manufacturing Facility: A reputable manufacturer will boast a well-equipped manufacturing facility, equipped with modern machinery and staffed by highly skilled and experienced professionals. This ensures efficient production processes and high-quality output.
After-Sales Service and Payment Methods: Look for a manufacturer that provides reliable after-sales service, including technical support and assistance. Additionally, consider their offered payment methods, ensuring they are secure and convenient for your business needs.
Research and Development Capabilities: A manufacturer with a well-established research and development department demonstrates their commitment to product improvement. They invest in enhancing the quality, lifespan, and safety of their Rogers 6002 laminates.
Manufacturing Experience and Customer Satisfaction: Consider manufacturers with a proven track record of at least ten years in the industry. Additionally, seek feedback from their existing customers to gauge their level of satisfaction with the manufacturer’s products and services.
Sales and Technical Support: Opt for a manufacturer that offers round-the-clock sales and technical support. This ensures prompt assistance whenever required, facilitating smooth communication and addressing any concerns efficiently.
Bulk Order Management and Timely Delivery: Evaluate the manufacturer’s ability to handle and fulfill bulk orders efficiently. Timely delivery is crucial for smooth project execution, so prioritize manufacturers with a reputation for meeting deadlines.
By meticulously evaluating manufacturers based on these criteria, you can confidently select the most suitable one to fulfill your specific requirements for Rogers 6002 laminates.
Conclusion
Rogers 6002 laminates have found applications in various configurations, including non-planar and flat structures, such as microwave circuits, complex multilayer circuits, and antennas. These laminates have demonstrated suitability for deployment in space and multilayer constructions due to the reliable performance of plated-through holes (PTH).
In the realm of laminates, numerous options are available; however, opting for high-frequency laminates like Rogers 6002 enables the attainment of a harmonious balance between electrical and mechanical characteristics. This balance is crucial in achieving optimal performance for high-frequency applications.
Our services
Rogers PCB Laminates & Series