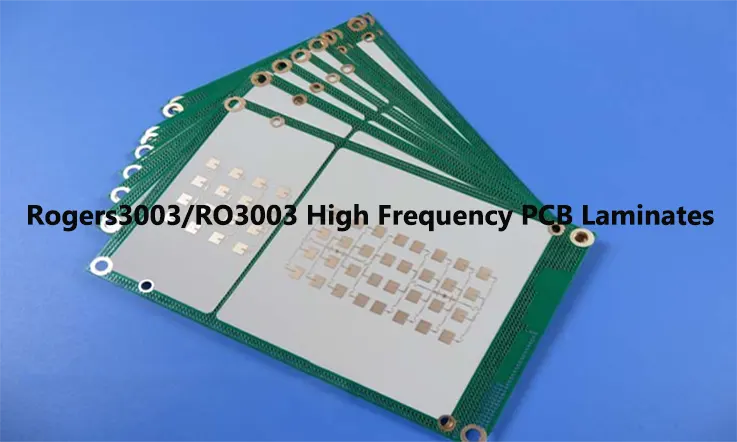
Rogers 3003 is a highly regarded laminate material used in the manufacturing of printed circuit boards (PCBs). It stands out as one of the top choices for PCB fabrication, offering exceptional performance and reliability. With its wide range of applications, including telecommunication services, radar systems, and space stations, Rogers 3003 has established itself as a versatile and valuable material in these industries.
For those seeking comprehensive information about Rogers 3003, this article serves as an ultimate FAQ guide, addressing all your inquiries and providing a comprehensive understanding of its features and benefits.
What is Rogers 3003?
Rogers 3003 is a popular choice for high-frequency printed circuit boards (PCBs) due to its durability and affordability. It is specifically designed for use in microwave and RF applications, offering excellent stability and a dielectric constant ranging from 3 to 40 GHz at room temperature. With a dissipation factor of no more than 0.0013 up to 10 GHz, it is well-suited for applications such as bandpass filters, microstrip antennas, and electron-controlled oscillators.
As part of the RO3000 series, Rogers 3003 is a high-frequency laminate that combines ceramic-filled polytetrafluoroethylene (PTFE) compounds. One of its key advantages is its consistent mechanical properties, regardless of the required dielectric constant. This makes it a reliable choice for various applications.
The unique characteristics of RO3003 include a dielectric constant of 3.00 and a low loss tangent of 0.0013. The substrate thickness typically measures 0.02 inches, ensuring a compact design. The copper density is typically 0.5 ounces, providing good balance and proportional stability to the components. The typical board thickness does not exceed 0.5 inches, and its Z-axis coefficient of thermal expansion (CTE) is approximately 24 ppm. This unique property contributes to reliable copper plating and hole reliability, even in demanding thermal environments.
As a result, Rogers 3003 is a high-frequency, ceramic-filled PTFE laminate that offers excellent electrical performance for RF and microwave applications. Its consistent mechanical properties, dielectric constant, and low loss tangent make it a reliable choice for a wide range of circuit designs.
Rogers3003/RO3003: Properties, Advantages and Application
RO3003 is a high-frequency laminate material developed by Rogers Corporation. It is widely used in the field of microwave and RF applications. The material is known for its excellent electrical and mechanical properties.
Properties
The key properties of RO3003 are:
Dielectric Constant (Dk): RO3003 has a consistent dielectric constant of 3.00 ± 0.04 which is maintained across a wide range of frequencies. This makes it suitable for applications that require precise control over impedance.
Low Loss Tangent: The material has a low loss tangent (typically 0.0010 at 10 GHz), which means it offers low signal loss during transmission.
Thermal Conductivity: RO3003 has a thermal conductivity of 0.55 W/m/K, which is higher than many standard PCB materials. This allows it to dissipate heat more effectively.
Low Moisture Absorption: RO3003 has a very low moisture absorption rate (<0.04%), which minimizes performance variation in humid conditions.
Advantages
The main advantages of RO3003 include:
High Frequency Performance: With its low dielectric loss, RO3003 is ideal for high-frequency applications where signal integrity is key.
Temperature Stability: The dielectric constant of RO3003 is stable across a range of temperatures, making it reliable in diverse operating environments.
Consistency: RO3003 shows excellent lot-to-lot repeatability, which is crucial for high-volume manufacturing.
Low Moisture Absorption: Its low moisture absorption rate lowers the risk of performance variation in humid conditions.
Applications
Because of its unique properties, RO3003 is used in a variety of applications:
Automotive Radar Systems: Its high-frequency performance and temperature stability make it ideal for use in automotive radar systems.
Microwave Applications: RO3003 is often used in microwave applications, including microwave circuits and antennas.
RF Applications: This includes diverse RF applications such as power amplifiers and filters.
Aerospace and Defense: In these sectors, RO3003 is used in applications like satellite communications systems and radar systems where high-frequency performance and reliability are crucial.
Overall, RO3003 is a versatile material that provides excellent performance in a wide range of high-frequency applications. Its consistent properties and reliability make it a popular choice in industries where performance cannot be compromised.
Material Composition of Rogers 3003 Laminate
Rogers 3003 is a composite material that typically consists of the following layers:
Copper Foil: The top and bottom layers of Rogers 3003 laminate usually include copper foils. The copper foils provide a conductive surface for circuitry and facilitate the connection of components.
Ceramic Filled PTFE (Polytetrafluoroethylene): The core layer of Rogers 3003 laminate is made up of a ceramic-filled PTFE material. PTFE is a high-performance polymer known for its excellent electrical properties, low loss tangent, and high temperature resistance. The addition of ceramic fillers helps to enhance the dielectric constant and improve the overall performance of the material at high frequencies.
Bonding Sheets: Between the copper foils and the core layer, there are bonding sheets that facilitate the lamination process and ensure adhesion between the layers.
The specific composition and thickness of each layer may vary depending on the desired electrical and mechanical properties of the final product. It’s always recommended to refer to the manufacturer’s datasheet or technical specifications for precise details on Rogers 3003 laminate.
How to Prevent Overheating in RO3003 Laminates?
To prevent Rogers RO3003 from overheating, you can follow these guidelines:
Adequate Thermal Management: Ensure proper thermal management within the system or application where RO3003 is used. This involves designing and implementing effective heat dissipation mechanisms such as heat sinks, thermal vias, or fans to maintain the temperature within acceptable limits.
Consider Operating Temperature Range: RO3003 has a specified operating temperature range. Make sure to operate the material within the recommended temperature limits provided by the manufacturer. Exceeding these limits can lead to thermal issues and potential overheating.
Optimize Circuit Design: Proper circuit design can help minimize heat generation and improve thermal performance. Consider factors such as trace width, copper thickness, and component placement to reduce resistive losses and hotspots. Efficient designs can help distribute heat more evenly and prevent localized overheating.
Adequate Ventilation: Ensure that the RO3003-based circuit boards or components have adequate ventilation, especially if they are enclosed in a housing or an environment with limited airflow. Proper ventilation allows heat to dissipate and prevents the buildup of excessive heat.
Thermal Analysis and Simulation: Utilize thermal analysis and simulation tools to evaluate and optimize the thermal performance of the system. These tools can help identify potential hotspots, optimize heat dissipation strategies, and ensure the RO3003 material operates within safe temperature limits.
Follow Manufacturer Guidelines: Always refer to the manufacturer’s datasheet, application notes, and guidelines for specific recommendations on thermal management and operation of RO3003. They may provide additional insights and best practices to prevent overheating.
By implementing these measures, you can help prevent RO3003 from overheating and ensure its reliable operation within the specified temperature range.
Key Differences Between Rogers 4003 and 3003 Laminates
Rogers 4003 and Rogers 3003 are both high-frequency laminates manufactured by Rogers Corporation, but they have some key differences in their composition and properties. Here are the main differences between Rogers 4003 and Rogers 3003:
Dielectric Constant (Dk): Dielectric constant refers to the material’s ability to store electrical energy in an electric field. Rogers 4003 has a higher dielectric constant, typically around 3.38, compared to Rogers 3003, which has a dielectric constant of approximately 3.00. The higher dielectric constant of Rogers 4003 makes it suitable for applications requiring higher impedance or tighter control over the electrical characteristics.
Dissipation Factor (Df): Dissipation factor, also known as loss tangent, indicates the loss of electrical energy in the material. Rogers 4003 has a slightly higher dissipation factor compared to Rogers 3003. The Df of Rogers 4003 is typically around 0.0027, while Rogers 3003 has a lower Df of approximately 0.0013. A lower dissipation factor indicates lower signal loss and better electrical performance.
Thickness Options: Rogers 4003 is available in a wider range of thickness options compared to Rogers 3003. Rogers 4003 is commonly available in thicknesses ranging from 0.002″ to 0.125″, providing greater flexibility in design and specific application requirements. Rogers 3003 typically has a narrower range of thickness options.
Cost: Rogers 3003 is generally more affordable compared to Rogers 4003. The higher dielectric constant and wider range of thickness options in Rogers 4003 contribute to its relatively higher cost.
It’s important to note that both materials have excellent electrical properties and are commonly used in high-frequency applications. The choice between Rogers 4003 and Rogers 3003 depends on specific design requirements, such as the desired dielectric constant, loss tangent, and thickness options, as well as budget considerations. It’s recommended to consult the manufacturer’s datasheets and application guidelines to select the most suitable material for a particular application.
Difference between FR4 and Rogers 3003 Material
FR4 and Rogers 3003 are two different types of materials commonly used in the electronics industry, but they have distinct differences in composition and properties. Here are the main differences between FR4 and Rogers 3003:
Composition: FR4 is a type of fiberglass-reinforced epoxy laminate, while Rogers 3003 is a high-frequency ceramic-filled PTFE (polytetrafluoroethylene) laminate. FR4 consists of a woven fiberglass cloth impregnated with epoxy resin, which provides mechanical strength and insulation. Rogers 3003, on the other hand, combines PTFE with ceramic fillers to achieve high-frequency performance.
Electrical Performance: FR4 is a general-purpose material with moderate electrical properties. It typically has a relatively higher dielectric constant (around 4.4) and a higher dissipation factor compared to Rogers 3003. Rogers 3003, designed specifically for high-frequency applications, has a lower dielectric constant (around 3.00) and a lower dissipation factor, enabling better signal integrity at high frequencies.
Frequency Range: FR4 is suitable for a wide range of applications, including lower frequency circuits and general-purpose PCBs. It is commonly used in consumer electronics, industrial equipment, and low to moderate frequency RF applications. Rogers 3003 is specifically engineered for high-frequency applications, typically ranging from several GHz to tens of GHz. It is commonly used in RF/microwave circuits, antennas, and other high-frequency devices.
Mechanical Strength: FR4 offers good mechanical strength and is widely used for its durability and cost-effectiveness. It provides reasonable rigidity and can withstand typical environmental conditions. Rogers 3003, while offering good electrical performance, may not have the same level of mechanical strength as FR4. Care should be taken to ensure proper support and mechanical reinforcement when using Rogers 3003 in applications that require higher mechanical stability.
Cost: FR4 is generally more affordable compared to Rogers 3003. FR4 is a widely available and commonly used material, making it cost-effective for various applications. Rogers 3003, being a specialized high-frequency material, tends to have a higher cost due to its unique properties and manufacturing process.
The choice between FR4 and Rogers 3003 depends on the specific requirements of the application. FR4 is a versatile and cost-effective option for general-purpose PCBs and lower frequency applications. Rogers 3003 is chosen when high-frequency performance and signal integrity are critical, especially in RF and microwave applications. It’s important to consider factors such as frequency range, electrical performance, mechanical strength, and cost when selecting the appropriate material for a particular application.
Design Considerations and Best Practices
Design considerations and best practices play a crucial role in ensuring optimal performance and reliability when working with Rogers 3003. Here are some key design considerations and best practices to keep in mind:
Signal Integrity
● Impedance Control: Maintain consistent and controlled impedance throughout the design by carefully selecting trace widths, spacing, and layer stackup.
● Transmission Line Design: Use appropriate transmission line structures (such as microstrips or striplines) to minimize signal losses and reflections.
● Return Paths: Ensure proper return paths for signals to minimize electromagnetic interference (EMI) and maintain signal integrity.
Thermal Management
● Heat Dissipation: Consider the power dissipation of components and utilize proper thermal management techniques, such as heat sinks or thermal vias, to prevent excessive temperature rise.
● Copper Pour and Pad Size: Optimize copper pour and pad sizes to enhance heat dissipation and minimize thermal hotspots.
RF Grounding and Shielding
● Ground Plane Design: Utilize a solid ground plane to provide a low impedance return path for RF signals and minimize ground noise.
● Shielding: Implement appropriate shielding techniques, such as adding grounded copper fills or using RF shielding cans, to reduce EMI and maintain signal integrity.
PCB Layout Considerations
● Component Placement: Strategically place components to minimize trace lengths, reduce parasitic effects, and optimize signal paths.
● Trace Routing: Follow best practices for trace routing, such as avoiding sharp bends, maintaining consistent trace widths, and minimizing crosstalk between traces.
● Via Placement: Optimize via placement to minimize stubs and maintain controlled impedance.
Manufacturing Considerations
● Material Selection: Ensure compatibility between Rogers 3003 and other materials used in the PCB assembly process, including soldering temperatures and techniques.
● Design for Manufacturability (DFM): Follow DFM guidelines to ensure ease of manufacturing, such as adhering to minimum feature sizes and clearance requirements.
● Design for Testability (DFT): Incorporate test points and access for test probes to facilitate testing and debugging during production.
Simulation and Validation
● Electromagnetic Simulation: Utilize electromagnetic simulation tools to verify signal integrity, impedance control, and EMI performance.
● Prototyping and Testing: Validate the design through prototyping and comprehensive testing, including high-frequency measurements, to ensure it meets the desired specifications.
Documentation and Collaboration
● Detailed Documentation: Maintain thorough documentation of the design, including layer stackup, impedance calculations, and manufacturing specifications, for future reference and collaboration with manufacturers.
● Collaboration with Fabricators: Engage in open communication with PCB fabricators and manufacturers to ensure proper understanding of design requirements and address any manufacturing-related concerns.
By considering these design considerations and following best practices, you can enhance the performance, reliability, and manufacturability of your Rogers 3003-based PCB designs in high-frequency applications.
Manufacturing and Handling Considerations
When it comes to manufacturing and handling Rogers 3003 PCB material, there are certain considerations to keep in mind to ensure successful production and reliable performance. Here are some manufacturing and handling considerations:
Material Selection and Procurement
● Choose a reliable supplier or manufacturer that provides genuine Rogers 3003 material to ensure consistent quality and performance.
● Verify the material specifications, such as dielectric constant (Dk), dissipation factor (Df), and thickness, to match the desired design requirements.
● Storage and Handling
● Store the Rogers 3003 material in a controlled environment to prevent exposure to moisture, extreme temperatures, or contaminants that could affect its properties.
● Handle the material with clean, dry gloves to avoid any potential contamination or damage.
PCB Fabrication
● Consult with the PCB manufacturer to ensure they have experience working with high-frequency materials like Rogers 3003.
● Provide detailed documentation, including layer stackup, material specifications, and impedance requirements, to the manufacturer to ensure accurate fabrication.
● Follow the manufacturer’s guidelines for specific fabrication processes, such as drilling, etching, plating, and lamination, to minimize any potential issues.
Copper Clad Laminate (CCL) Preparation
● Ensure proper surface preparation of the CCL before lamination, including cleaning and roughening the copper surface for better adhesion.
● Follow the recommended cleaning agents and techniques to remove any contaminants or oxidation from the copper surface.
Lamination Process
● Follow the recommended lamination process parameters, including temperature, pressure, and time, specified by the Rogers 3003 manufacturer.
● Ensure proper alignment and registration of the layers during lamination to maintain the desired impedance control and signal integrity.
Drilling and Routing
● Use appropriately sized drill bits and routing tools to minimize any mechanical stress or damage to the Rogers 3003 material during the drilling and routing process.
● Follow the manufacturer’s guidelines for recommended drill speeds, feed rates, and tooling to prevent delamination or burring.
Surface Finish and Soldering
● Choose surface finishes compatible with Rogers 3003, such as gold immersion (ENIG) or organic solderability preservative (OSP), to ensure good solderability and prevent surface oxidation.
● Follow the recommended soldering techniques, temperatures, and dwell times to prevent excessive heat exposure that could damage the material.
Quality Control and Testing
● Implement thorough quality control measures throughout the manufacturing process, including inspection of raw materials, in-process checks, and final testing, to ensure adherence to specifications.
● Conduct high-frequency testing, such as impedance measurements, signal loss characterization, and return loss measurements, to validate the electrical performance of the fabricated PCBs.
By considering these manufacturing and handling considerations, you can minimize potential issues, ensure the integrity of the Rogers 3003 material, and achieve reliable and high-performance PCBs in high-frequency applications. It is advisable to consult the Rogers Corporation’s guidelines and recommendations for specific manufacturing and handling practices related to Rogers 3003.
Why Choose JarnisTech for Your Rogers 3003
When searching for a reliable source of high-quality Rogers 3003 laminate material, JarnisTech emerges as the ideal choice. As a trusted producer and manufacturer based in China, we possess a strong reputation for delivering exceptional products with excellent customization capabilities.
At JarnisTech, we offer a diverse range of Rogers 3003 options, catering to various PCB applications. Our Rogers 3003 is a ceramic-filled composite that exhibits remarkable mechanical and electrical stability, making it particularly well-suited for high-frequency applications, including two-layer boards and 3.0DK. We provide flexibility in dielectric thickness, allowing you to choose options such as 0.75mm, as well as finished thicknesses like 0.9mm. Additionally, our Rogers 3003 boasts excellent thermal conductivity and other desirable properties.
To ensure top-notch production quality, we meticulously prepare certified raw materials and employ advanced processing machines. JarnisTech manufactures Rogers 3003 with immersion gold surface treatment, enhancing its performance and durability. Our Rogers 3003 finds extensive application in automobile radar systems, where longevity and reliability are paramount. It is also suitable for aerospace PCBs, RF coupler PCBs, GPS antenna PCBs, and various other project applications.
Notably, JarnisTech’s Rogers 3003 excels in high-temperature environments, capable of withstanding temperatures ranging from -10 to 150 degrees Celsius. Furthermore, our Rogers 3003 is specifically designed for radio frequency applications, offering competitive prices without compromising on quality.
We specialize in developing two-layer boards and are fully committed to supporting your specific customization requirements. Our manufacturing process utilizes high-grade materials, ensuring excellent supplies and practical applications.
JarnisTech PCB Capabilities | |
PCB Material: | Ceramic-filled PTFE composite |
Designator: | RO3003 |
Dielectric constant: | 3.0 ±0.04 (process) |
3.0 (design) | |
Layer count: | 1 Layer, 2 Layer, Multilayer, Hybrid PCB |
Copper weight: | 0.5oz (17 µm), 1oz (35µm), 2oz (70µm),etc. |
PCB thickness: | 10mil (0.254mm), 20mil (0.508mm),etc. |
30mil (0.762mm), 60mil (1.524mm),etc. | |
PCB size: | ≤400mm X 500mm,etc |
Solder mask: | Green, Black, Blue, Yellow, Red etc. |
Surface finish: | Bare copper, HASL, ENIG, OSP etc.. |
PCB Material: | Ceramic-filled PTFE composite |
At JarnisTech, we strive to be your trusted partner, dedicated to building long-term relationships. Whether you require Rogers 3003 for your business in wholesale quantities or for specific project needs, we are the number one choice. Our efficient and professional staff will expedite your order process, so please don’t hesitate to contact us directly.
For urgent inquiries and requirements, JarnisTech guarantees comprehensive guidance throughout your Rogers 3003 processing journey. We are here to support the establishment of your new business ventures or the expansion of your existing successful operations.
Reach out to us with your inquiries for further information and let us assist you in achieving your goals with Rogers 3003.
Conclusion
Rogers 3003 PCB laminates have revolutionized the electronics industry by offering a host of advantages that address the evolving needs of modern technology. Their exceptional electrical properties, thermal stability, and mechanical strength have made them an indispensable component in the design and manufacturing of high-performance electronic devices.
In summary, Rogers 3003 PCB laminates have set new standards in terms of performance, reliability, and versatility. Their advantages have propelled the electronics industry to new heights, enabling the development of increasingly sophisticated and efficient electronic devices. By harnessing the potential of Rogers 3003 laminates while embracing sustainability, we can pave the way for a future where technology meets both performance and environmental responsibility.
Our services
Rogers PCB Laminates & Series