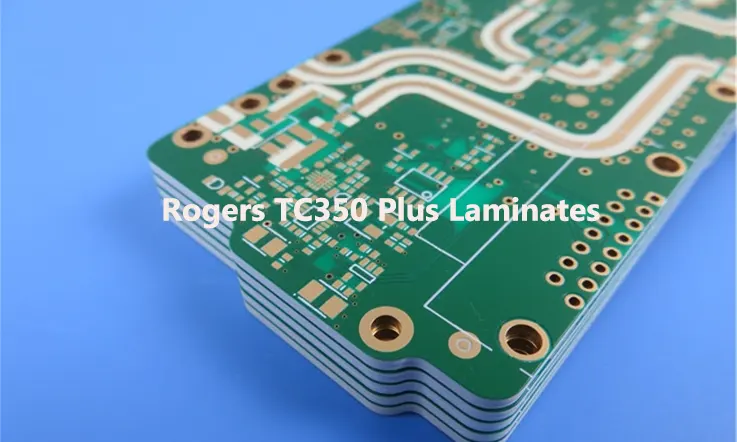
The following review will specifically highlight the distinctive qualities of Rogers TC350 Plus laminates. These laminates possess exceptional capabilities that make them suitable for various applications, including amplifiers, combiners, power dividers, couplers, filters, and more. Moreover, their utilization extends beyond the commercial and consumer sectors, encompassing aerospace and defense domains. Continue reading to explore the comparative advantages of this material when compared to similar alternatives.
What is Rogers TC350 Plus Laminates?
Rogers TC350 Plus laminates are a type of high-frequency circuit board material designed for applications that require excellent electrical performance at high frequencies. TC350 Plus laminates are manufactured by Rogers Corporation, a leading supplier of engineered materials for a wide range of industries.
TC350 Plus laminates are engineered with woven glass-reinforcement and low-loss thermoset materials, providing high electrical reliability and stability in various environmental conditions. These laminates exhibit low dielectric loss, low dispersion, and a stable dielectric constant (Dk) over a broad frequency range. This makes them suitable for applications involving high-speed digital and analog signals, including telecommunication systems, wireless devices, automotive radar, high-frequency test equipment, and more.
Rogers TC350 Plus laminates offer properties such as low insertion loss, excellent dimensional stability, and high thermal conductivity for effective heat management. These characteristics contribute to maintaining signal integrity, minimizing electrical losses, and improving overall performance in high-frequency electronic designs.
It’s worth noting that specific product specifications and available variants may be subject to change, so it’s recommended to refer to the official product documentation or contact Rogers Corporation for the most up-to-date and detailed information on TC350 Plus laminates.
Rogers TC350 Plus Product Specifications
The TC350, manufactured by Rogers Corporation, is a high-quality PCB laminate that offers excellent performance characteristics. It is characterized by a dielectric constant (Dk) of 3.5, providing stable signal transmission and minimizing signal loss. With a high glass transition temperature (Td) range of 520 to 567 degrees Celsius, this laminate offers exceptional thermal resistance, making it suitable for applications that involve elevated operating temperatures.
Product Details | |
Part Number | TC350 |
Manufacturer | Rogers Corporation |
General Parameters | |
Type | Copper |
Dk | 3.5 |
Td | 520 to 567 Degree C |
Frequency | 0.001 to 10 GHz |
Cte xy | 7, 7 ppm/Degree C |
Cte z | 23 ppm/Degree C |
Dielectric breakdown | 40 kV |
Electrical strength | 780 (31) Volts/mil (kV/mm) |
Flamibility | V0 class |
Flexural strength | 14/10 (97/69) kpsi (MPa) |
Industry application | Aerospace and defence |
Material | PTFE |
Peel strength | 7 (1.2), 9 (1.6) lb/in (N/mm) |
Surface resistivity | 3.2 x 10^7 Mohm |
Thermal coeffecient | -9 ppm/Degree C |
Thermal conductivity | 0.72 W/mK |
Volume resistivity | 7.4 x 106 Mohm-cm |
Water absorption | 0.0005 |
Z axis expansion | 0.012 |
The TC350 laminate exhibits a broad frequency range from 0.001 to 10 GHz, ensuring reliable signal integrity across a wide spectrum of frequencies. It is designed to meet the demanding requirements of advanced electronic systems and is commonly employed in various industries. From high-speed communication systems to RF and microwave applications, the TC350 laminate proves to be a reliable choice.
Manufacturing and fabrication processes for Rogers TC350 Plus Laminates
Rogers TC350 Plus is a thermoset, rigid composite material made of woven fiberglass impregnated with a high performance, thermally conductive epoxy resin. It’s designed for use in high reliability, high power/heat applications where consistent electrical performance and high thermal conductivity are required. While the specific manufacturing and fabrication processes are proprietary to Rogers Corporation, here is a general overview of how such laminates are typically made and fabricated:
Impregnation: The fiberglass cloth is impregnated with a thermosetting epoxy resin. This resin is typically mixed with a hardener and a filler that enhances thermal conductivity.
Pre-Pregging: The impregnated cloth, also known as pre-preg, is partially cured to a “B-stage” where it is dry but can still bond to other layers.
Lamination: Multiple layers of pre-preg are stacked together and covered with copper foil on both sides. The stack is then placed into a lamination press where it is subjected to heat and pressure. This fully cures the epoxy, bonding the layers together into a rigid laminate.
When fabricating circuit boards from laminates like Rogers TC350 Plus, the following steps are generally involved:
Cutting: The laminate is cut to the desired size.
Drilling: Holes are drilled for through-hole components and vias.
Copper Plating: The drilled holes are electroplated with copper to create electrical connections between layers.
Etching: The copper on the surface of the laminate is etched away using chemicals to create the desired circuit pattern.
Solder Masking: A solder mask is applied to protect the circuitry and prevent solder bridging during assembly.
Silkscreening: Component references and other markings are printed onto the solder mask.
Assembly: Components are soldered onto the board, completing the fabrication process.
It’s important to note that due to the high thermal conductivity and specific characteristics of Rogers TC350 Plus material, attention must be paid to the heat management during fabrication, as overheating can lead to deformation or other defects.
Each manufacturing or fabrication step can have variations and nuances depending on the specific needs of the product being produced or the particular equipment being used. Therefore, it’s important to work closely with your laminate supplier and board manufacturer to ensure the best results.
Comparison of Rogers TC350 Plus laminates with other materials or laminates
Rogers TC350 Plus laminates are high-frequency laminates designed for use in advanced electronic applications. To compare them with other materials or laminates, let’s consider a few key factors:
Dielectric Constant (Dk): Rogers TC350 Plus laminates have a relatively low dielectric constant, typically around 3.50. This low Dk allows for better signal integrity and reduced signal loss compared to materials with higher Dk values. In comparison, some other popular laminates like FR-4 typically have higher Dk values ranging from 4 to 5.
Loss Tangent (Df): TC350 Plus laminates exhibit a low loss tangent (Df) of around 0.0015. The low Df indicates minimal signal loss and excellent electrical performance, especially at high frequencies. In contrast, FR-4 laminates generally have higher Df values of around 0.02 to 0.035.
Thermal Performance: Rogers TC350 Plus laminates offer good thermal stability and can handle higher operating temperatures compared to standard FR-4 materials. This makes them suitable for applications requiring high power and where heat dissipation is important.
Copper Clad Laminate (CCL) Options: Rogers TC350 Plus laminates are available with copper foil cladding on both sides, typically in thicknesses ranging from 0.5 oz to 2 oz. Other materials may offer similar copper cladding options, but it depends on the specific laminate chosen.
Cost: Rogers TC350 Plus laminates are generally more expensive than standard FR-4 laminates due to their specialized properties and high-frequency performance. If cost is a major consideration and the application does not require high-frequency performance, FR-4 laminates may be a more economical choice.
Application-specific Considerations: When comparing laminates, it’s essential to consider the specific requirements of your application. Factors like frequency range, power handling capabilities, dimensional stability, and environmental factors can significantly influence the choice of laminates. Other high-frequency laminates, such as Rogers RO4000 series or Taconic TLY series, may also be worth considering depending on the specific needs of your project.
Ultimately, the choice of laminates depends on the specific application requirements, budget, and trade-offs between performance and cost. It’s recommended to consult with materials suppliers or engineers experienced in high-frequency applications to determine the most suitable laminate for your project.
Applications and Industries where Rogers TC350 Plus Laminates are Commonly Used
Rogers TC350 Plus laminates find applications in various industries that require high-frequency performance and reliable signal integrity. Some common applications and industries where TC350 Plus laminates are commonly used include:
Telecommunications: TC350 Plus laminates are suitable for high-frequency communication systems, such as base stations, antennas, microwave links, and wireless infrastructure equipment.
Aerospace and Defense: These laminates are used in radar systems, satellite communication, avionics, radar-absorbing materials, and other applications that require high-frequency signal transmission and exceptional performance in harsh environmental conditions.
Automotive: TC350 Plus laminates are employed in automotive radar systems for collision avoidance, driver assistance, and autonomous driving applications. They offer low loss and stable electrical properties required for high-frequency automotive radar technology.
Test and Measurement Equipment: These laminates are used in high-frequency test fixtures, probes, and other test and measurement equipment where precise signal transmission, low loss, and stable characteristics are vital.
IoT and Wireless Devices: TC350 Plus laminates can be found in various wireless devices, such as routers, access points, IoT sensors, and smart home devices, where high-speed data transmission and signal integrity are critical.
Medical Electronics: TC350 Plus laminates are utilized in medical devices, such as imaging systems, wireless monitoring devices, and high-frequency surgical equipment, due to their high-performance electrical properties.
Industrial and Scientific Instruments: TC350 Plus laminates are suitable for high-frequency industrial and scientific instruments that require accurate signal transmission and measurement, such as spectroscopy equipment, high-frequency generators, and signal analyzers.
These are just a few examples, and the use of TC350 Plus laminates can extend to other industries and applications where high-frequency performance and reliable signal integrity are essential.
How Rogers TC350 Plus Laminates Reduce Insertion Loss?
Rogers TC350 Plus laminates are designed to reduce insertion loss primarily through their low dielectric constant (Dk) and low loss tangent (Df). Here’s how these properties contribute to the reduction of insertion loss:
Low Dielectric Constant (Dk): The dielectric constant of a material determines the speed at which electrical signals propagate through it. Lower Dk values result in faster signal propagation, which reduces the time it takes for signals to travel from one point to another. This faster signal speed helps to minimize phase delays and reduce insertion loss.
Low Loss Tangent (Df): The loss tangent, also known as the dissipation factor, measures the amount of energy that is lost as heat when a signal passes through a material. A low loss tangent indicates that the material has low signal attenuation and minimal energy loss. In high-frequency applications, low Df values are crucial for maintaining signal integrity and reducing insertion loss caused by signal absorption.
By combining a low dielectric constant and a low loss tangent, Rogers TC350 Plus laminates provide excellent electrical performance at high frequencies. These properties help to minimize signal loss, maintain signal integrity, and reduce the overall insertion loss within the circuit.
It’s important to note that other factors, such as the design of the circuit, trace geometry, and transmission line structures, also impact insertion loss. Proper circuit design practices, including controlled impedance routing and minimizing signal reflections, are essential to further optimize the performance and reduce insertion loss in high-frequency applications using TC350 Plus laminates.
How Rogers TC350 Plus Laminates Increase Thermal Conductivity?
Rogers TC350 Plus laminates are designed to have increased thermal conductivity compared to other standard PCB materials. The enhanced thermal conductivity of TC350 Plus laminates is primarily achieved through careful material selection and engineering.
Here are a few ways in which TC350 Plus laminates can increase thermal conductivity:
Filler Materials: TC350 Plus laminates utilize fillers with high thermal conductivity, such as ceramic fillers or specialized additives. These fillers are dispersed within the laminate matrix to enhance the overall thermal conductivity of the material.
Resin System: The resin system used in TC350 Plus laminates is formulated to have improved thermal conductivity properties. The selection of resin with higher thermal conductivity helps in efficient thermal dissipation.
Design and Construction: The specific design and construction of TC350 Plus laminates also contribute to increased thermal conductivity. The use of woven glass reinforcement and optimized layer stack-up helps in providing efficient heat flow across the laminate.
By increasing thermal conductivity, TC350 Plus laminates can effectively transfer heat away from heat-generating components on a PCB. This helps in reducing operating temperatures, mitigating hotspots, and enhancing the overall thermal management of electronic systems. Improved thermal conductivity is especially important in high-power, high-frequency, and thermally sensitive applications, where efficient heat dissipation is crucial to maintain optimal performance and prolong the lifespan of electronic components.
How Rogers TC350 Plus Laminates Reduce RF Heating?
Rogers TC350 Plus laminates are designed to minimize RF heating in high-frequency electronic systems. The reduced RF heating is achieved through several key factors:
Low Dielectric Loss: TC350 Plus laminates exhibit low dielectric loss, which means they have minimal energy dissipation as RF signals pass through the material. This reduces the conversion of RF energy into heat, thereby lowering RF heating.
Excellent Thermal Conductivity: TC350 Plus laminates are engineered to have enhanced thermal conductivity compared to standard PCB materials. This helps in efficient heat dissipation from components and minimizes localized hotspots that could contribute to RF heating.
Thermoset Material: The thermoset material used in TC350 Plus laminates offers superior dimensional stability and helps prevent expansion or warping of the PCB due to temperature changes. This stability ensures a consistent electrical performance, reducing the likelihood of heat buildup.
Effective Heat Management: TC350 Plus laminates can be designed with appropriate copper weight and vias to dissipate heat away from heat-generating components. The proper placement of thermal vias facilitates efficient thermal transfer to the PCB’s internal copper layers and external heatsinks.
Design Optimization: Careful PCB design techniques, such as proper component placement, optimized trace routing, and thermal relief patterns, can further mitigate RF heating in TC350 Plus laminates. These design practices aim to minimize impedance discontinuities, current crowding, and excessive copper loss, which can lead to RF heating.
By minimizing dielectric losses, enhancing thermal conductivity, and employing effective design and material properties, Rogers TC350 Plus laminates contribute to reducing RF heating in high-frequency electronic systems. This helps maintain the overall performance and reliability of the system under demanding RF operating conditions.
Future Trends and Developments in Rogers TC350 Plus Laminates
Higher Frequencies: Future developments may target even higher-frequency applications, considering the continuous advancement of communication technologies, wireless systems, and emerging 5G, 6G, and beyond networks. These developments could include improved electrical performance and lower losses at extremely high frequencies.
Miniaturization and Integration: There is an ongoing trend towards smaller and more compact electronic devices. Future TC350 Plus laminates might be designed to support miniaturization efforts by offering improved signal integrity, reduced form factors, and enhanced integration capabilities.
Thermal Management: As electronic systems become more powerful and generate more heat, effective thermal management becomes increasingly important. Future TC350 Plus laminates may focus on even better heat dissipation capabilities, possibly incorporating advanced heat-spreading technologies or innovative materials.
Reliability and Durability: The demand for high-reliability electronic systems continues to grow in industries like aerospace, automotive, and defense. Future developments in TC350 Plus laminates might prioritize enhanced reliability, long-term stability, and durability in harsh environments, including resistance to temperature extremes, humidity, and mechanical stresses.
Sustainable Materials: With the increasing emphasis on sustainability and environmental consciousness, future developments may explore the use of eco-friendly materials or manufacturing processes in TC350 Plus laminates to minimize their impact on the environment.
It’s important to note that these predictions are speculative, and actual developments may vary. For the latest information regarding future trends and developments in Rogers TC350 Plus laminates, it is recommended to refer to official product documentation, industry news, or directly contact Rogers Corporation for the most up-to-date insights.
How To Choose A Professional Rogers TC350 Plus PCB Manufacturer?
When choosing a professional Rogers TC350 Plus PCB manufacturer, consider the following factors:
Experience and Expertise: Look for a manufacturer with a proven track record of working with Rogers TC350 Plus laminates and other high-frequency materials. Check their experience in manufacturing PCBs for similar industries or applications that require high-frequency performance.
Certifications and Quality Standards: Ensure that the manufacturer follows industry standards and has certifications such as ISO 9001 or ISO 13485 (for medical applications) to ensure their manufacturing processes meet rigorous quality requirements.
Technical Capabilities: Evaluate the manufacturer’s technical capabilities, such as their ability to handle complex PCB designs, multi-layer boards, and high-frequency signal routing. Consider their expertise in addressing design challenges specific to Rogers TC350 Plus laminates.
Manufacturing Facilities and Equipment: Assess the manufacturer’s facilities and equipment. Look for modern manufacturing facilities with advanced equipment capable of producing high-quality PCBs. Ensure they have the necessary tools for precise material handling and manufacturing processes.
Prototyping and Testing Services: Check if the manufacturer offers prototyping services to validate your designs before mass production. Also, inquire about their testing capabilities to ensure that PCBs are thoroughly tested for electrical performance and quality control.
Supply Chain Management: Consider the manufacturer’s ability to efficiently manage the supply chain, including sourcing components and materials, to ensure a smooth manufacturing process and minimize lead times.
Customer Support and Communication: Good customer support is crucial. Choose a manufacturer that offers responsive communication, provides timely updates on the progress of your order, and is willing to offer technical advice or assistance when needed.
Cost and Pricing: Compare the pricing structure and cost-effectiveness of different manufacturers. However, be cautious of selecting a manufacturer solely based on the lowest price, as quality and reliability should also be prioritized.
References and Reviews: Seek references and reviews from other customers who have worked with the manufacturer to gain insights into their reliability, quality, and customer satisfaction.
By thoroughly assessing these factors, you can choose a professional Rogers TC350 Plus PCB manufacturer that aligns with your specific requirements and ensures the production of high-quality PCBs for your application.
Why Choose Us?
Producing First-Class and Remarkable TC350 is JarnisTech’s Forte
As a responsible producer and manufacturer of TC350 laminate, we prioritize strict adherence to environmental safety laws and international standards. Our commitment is to deliver a high-quality product that fully achieves its intended functionality.
With over 20 years of experience in the industry, we have established ourselves as one of the leading global sources of TC350. This extensive expertise enables us to offer a diverse range of exceptional deals and options tailored to meet your specific requirements and application needs.
At JarnisTech, we boast a team of skilled professionals dedicated to providing comprehensive solutions for our customers. Should any issues arise with your TC350, we are committed to offering detailed 8D reports to address and resolve any concerns you may have about our services and products.
For further information on how we can best cater to your needs, we encourage you to get in touch with us promptly.
Conclusion
Rogers TC350 Plus laminates provide exceptional thermal conductivity, making them highly suitable for demanding high-power microwave applications. They offer significant advantages in various electronic components such as filters, transformers, and power dividers. Additionally, these laminates exhibit excellent performance characteristics for military and aerospace applications. Moreover, their compatibility with automated equipment, including e-lam and other dry lamination machines, facilitates efficient manufacturing processes.
It’s worth noting that TC350 Plus laminates are not typically subjected to the traditional wetting process for fiberglass outside the dryer or integrated dryer drying and fiberglass fiber moving capabilities. However, they demonstrate superior thermal stability and do not suffer from thermal bridging issues, enabling their reliable operation even under direct sunlight exposure.
Overall, TC350 Plus laminates deliver a remarkable combination of thermal conductivity, high-frequency performance, and reliability, making them an ideal choice for advanced electronic circuits in a range of industries.
Our services
Rogers PCB Laminates & Series