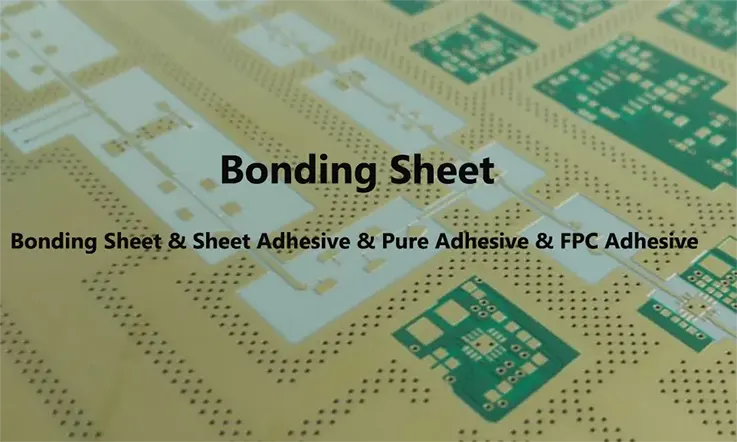
The miniaturization of printed circuit boards (PCBs) is an ongoing trend, and as a result, ensuring reliable functioning of components and contacts despite their reduced dimensions remains a significant challenge. In response, the use of adhesives is gradually replacing traditional soldered joints on PCBs due to their flexibility and ability to offer protection to delicate components. Adhesives are applied on PCBs in various forms, including glob toppings, coatings, or underfills for chips.
This paper seeks to enlighten us on the details of Bonding Sheet in the PCB industry, including Bond-ply and the adhesives used in Bonding Sheet, their types, characteristics, and applications.
As a PCB Manufacturer, our mission is to create high-quality, reliable PCBs despite the challenges, and understanding the nature of adhesives used in Bonding Sheet is crucial for accomplishing this goal. The Bonding Sheet plays a fundamental role in bonding layers of copper to end-products, and exploring the adhesives used in Bonding Sheet is imperative to achieve optimal performance in our PCB designs.
What Is Bonding Sheet in PCB Industry ?
Bonding Sheet, also referred to as Sheet Adhesive, Pure Adhesive, or Adhesive, is a type of glue applied to release paper. It is primarily used in multilayer lamination to bind flexible inner layers or rigid cap layers. In the manufacturing process of rigid-flex PCBs, it is often used to join flexible circuits to rigid-flex boards, as well as stiffeners and heat sinks. Its application provides a secure and durable bond between two components, ensuring the stability and durability of the end-product.
Types of Bonding Sheets
There are several types of bonding sheets used in PCB assembly, each with its properties and advantages. Some common types include:
Double-sided adhesive tape: made of a thin layer of adhesive material coated on both sides of a carrier film, commonly used for bonding components, displays, touch panels, and other flat structures. They can have different adhesive strengths, thermal conductivity, and electrical insulation properties, depending on the application.
Thermal interface material (TIM): designed to improve the heat dissipation and thermal conductivity between two surfaces, typically used for bonding semiconductor devices, LEDs, power modules, and heat sinks. They can be made of silicone, grease, thermally conductive adhesive, or other materials, depending on the required thermal resistance and operating temperature range.
Conductive adhesive tape: containing conductive particles or fibers in the adhesive material, used for bonding conductive traces, electrodes, and other components requiring electrical connectivity. They can have different conductance, adhesion strength, and resistance to environmental factors, such as temperature, moisture, and vibration.
Optical adhesive sheet: having a high refractive index and low light scattering properties, used for bonding optical components, lenses, and filters in display, imaging, and sensing applications. They can have different transmittance, refractive index, and curing properties, depending on the light wavelength and application requirements.
EMI/RFI shielding tape: containing metal or metal-coated particles in the adhesive material, used for bonding metal shields and enclosures to protect against electromagnetic interference (EMI) or radio-frequency interference (RFI). They can have different attenuation, conductivity, and adhesion properties, depending on the frequency range and shielding effectiveness required.
Bonding Sheet Properties
Using the properties of the adhesive on the DuPontTM Pyralux® FR sheet as an example. It has been brought to our attention that FR0100 is a flame retardant B-staged modified acrylic adhesive.
The adhesive’s capability to withstand flames makes it an ideal choice for use in applications where safety is of paramount importance. The Pyralux® FR sheet adhesive’s exceptional fire-retardant properties underscore its suitability for use in a broad range of environments, including those where stringent safety regulations must be upheld
By selecting the appropriate bonding sheet type and properties, PCB manufacturers and designers can achieve the desired mechanical, thermal, electrical, optical, and shielding performance for their products.
What’s the Adhesive Material in Bonding Sheet ?
As a PCB manufacturer, we recognize that the adhesive used in Bonding Sheet has two primary applications. The first involves using the adhesive to bind metal foil to a base material, forming a laminate. Alternatively, the adhesive is applied to join layers of laminate material, producing multilayer flexible printed circuits (FPCs). Employing these adhesives facilitates the production of robust and reliable PCBs, particularly in multilayer lamination and rigid-flex PCBs. Therefore, understanding the different adhesive materials and their properties is crucial in creating high-quality PCBs that meet our customers’ specific needs.
In the production of flexible printed circuits (FPCs), the most commonly used adhesives include polyesters (PET), polyimides (PI), acrylics, and modified epoxies. Each of these different types of adhesives offers a unique set of advantages and disadvantages that must be considered, particularly in specific applications. A comparative analysis of these adhesives and their properties are described in the table below.
Polyester adhesives are the most cost-effective but are least effective at high temperatures and do not offer the strongest binding strength when compared to other adhesive types. To select the appropriate adhesive, it is essential to evaluate each type’s characteristics and how they align with the specific application requirements.
Polyester adhesives are commonly employed in situations where the substrate material is made of polyester, and where the circuit is not subjected to high temperature or pressure. In contrast, polyimide adhesives find broader applications in the defense, aerospace, and satellite industries, particularly in situations requiring high-demand multi-layer circuit applications. Polyimide adhesives, despite being more expensive than other alternatives, exhibit excellent performance at high temperatures and are thus favored in these industries. Understanding the various adhesives’ properties enables PCB manufacturers to determine which adhesive is most appropriate for a specific application, resulting in the delivery of reliable and high-quality PCBs.
Types of Electrically Conductive Adhesives in Bonding Sheet
● Electrically conductive adhesives can be classified into two categories – isotropic and anisotropic adhesives. Isotropic conductive adhesives (ICA) are capable of transmitting electricity in all directions. They are widely used for chip contacting and bonding electrically conductive SMDs.
● On the other hand, Anisotropic conductive adhesives (ACA) consist of specialized conductive particles in the range of micrometers that can only conduct electricity in a single direction. These adhesives are commonly employed in sensitive circuit board structures, such as LCD connectors or for contacting flexible printed circuits (FPCs). Due to their unique directional conductivity, ACA adhesives guarantee electrical connectivity while preserving the delicate nature of the electronic structures.
By choosing the right type of conductive adhesive, PCB manufacturers can create high-performance electronic products that meet and exceed the specific requirements of their customers.
Bonding Sheet: Adhesive Thicknesses
● 100μm (4mil).
● 75μm (3mil).
● 50μm (2mil).
● 25μm (1mil).
● 12μm (0.5mil).
In the selection of adhesive thickness for bonding materials, it is important to consider the trace thickness and remaining copper rate to ensure complete coverage and bonding of copper features. PCB manufacturers of flexible circuits generally adhere to the conventional unit conversion of 1mil to 25m (micron) for bonding sheet and coverlay applications. A thorough understanding of the unique properties of different adhesive types and their application requirements is necessary to produce high-quality flexible circuits that conform to specific industry standards.
Adhesives Applications
● Potting.
● Wire tackin.
● Encapsulation.
● Conformal coatings.
● Bonding of heat sinks.
● Bonding of exterior plastic housings.
● Bonding of Surface Mount Devices (SMD’s).
What Is Bond-ply of PCB Bonding Sheet ?
Bondply, or Bond-Ply, is a versatile material that can be either a flexible printed circuit (FPC) with an adhesive + Polyimide (PI) + adhesive structure or a printed circuit board (PCB) material. The latter contains an unreinforced, hydrocarbon-based thin film adhesive system. The structure of each of these materials reinforces their adhesive properties while providing the necessary robustness for their respective application. Regardless of their different applications, both types of materials share the same name – bondply. As a result, the material is widely used in various high-reliability electronic applications, such as defense, aerospace, telecommunications, and medical industries, where a critical balance of flexibility and durability is required.
In Rigid Boards
The 2929 bond-ply is an unreinforced, hydrocarbon-based thin film adhesive technology specifically designed for high-reliability multilayer constructions. The thin film adhesive system is ideal for bonding multi-layer boards (MLB) made using PTFE composite materials such as RT/duroid 6000 and RO3000 series laminates, filled hydrocarbon resin composites such as RO4000 cores, and specialty thin core laminates. The system has a low dielectric constant of 2.9 and a loss tangent of 0.003 at microwave frequencies, providing excellent microwave performance.
The use of a proprietary cross-linking resin system makes this thin film adhesive technology compatible with sequential bond processing. Controlled flow characteristics provide excellent blind via fill capability as well as predictable cutback ratios for designs that require blind and/or buried cavity filling. This makes 2929 bondply an excellent choice for high-reliability multilayer constructions in various electronic industries, including defense, aerospace, and telecommunications, where superior performance and high reliability are required.
2929 bondply is a versatile material that can be bonded using both conventional flat presses and autoclaves with successful results. The following is a list of the primary benefits and features of this material:
● Compatibility: The thin film adhesive system is compatible with various substrates, including PTFE composite materials and hydrocarbon resin composites.
● Excellent microwave performance: With a low dielectric constant of 2.9 and a loss tangent of 0.003 at microwave frequencies, this thin film adhesive system provides exceptional microwave performance.
● Controlled flow characteristics: The material’s controlled flow characteristics allow for excellent blind via fill capability and predictable cutback ratios for designs requiring blind and/or buried cavity filling.
● Suitable for high-reliability applications: The material is ideal for use in high-reliability electronic applications, such as the aerospace, defense, and telecommunications industries.
● Versatile bonding options: The material can be successfully bonded using both conventional flat presses and autoclaves.
So, the 2929 bond-ply offers exceptional performance and reliability in various electronic applications. Its versatility and compatibility with different substrates make it an excellent option for high-reliability multilayer constructions.
In flexible and Rigid-flex Circuits
Dupont bond-ply is used in the fabrication of flexible and rigid-flex circuits. It is a composite material consisting of a polyimide film that has been coated on both sides with a proprietary B-staged acrylic adhesive. When only one side is coated, it is commonly referred to as a coverlay. The bond-ply is used between two conductive layers with differing FCCL (Flexible Copper Clad Laminate) cores, to enclose etched features in multilayer structures.
During the actual PCB fabrication process, bond-ply is replaced by a coverlay layer and an adhesive layer. This material offers an array of features and benefits, including:
● Ease of use: Dupont bond-ply is a highly versatile material that is easy to use in the fabrication of flexible and rigid-flex circuits.
● Excellent adhesive properties: The proprietary B-staged acrylic adhesive coating on both sides ensures excellent adhesive properties that promote superior bonding strength.
● Enhanced dielectric strength: The polyimide film used in bond-ply provides excellent dielectric strength, making it suitable for sensitive electronic applications.
● Low thermal expansion: The use of bond-ply between two conductive layers provides low thermal expansion, ensuring consistent performance over a wide range of environmental temperatures.
● Wide range of applications: Dupont bond-ply is extensively used in a variety of applications, including telecommunications, commercial, and industrial electronic applications.
In a word, Dupont bond-ply is a high-performance composite material that offers superior adhesive strength, dielectric strength, and thermal stability, making it an ideal choice for a wide range of flexible and rigid-flex circuit applications.
At JarnisTech, bondply is mostly utilized for the fabrication of heavy copper flex and rigid-flex PCBs, particularly HDI boards with sharp copper features.
PCB Bonding Sheet: Adhesives Key Features
PCB bonding sheets come with several key features in terms of its adhesives, including:
● Strong Adhesion: PCB bonding sheets typically provide strong adhesion to the substrate material, ensuring long-lasting performance of the PCB.
● Thermal Conductivity: The adhesive used in the PCB bonding sheets is designed with a high level of thermal conductivity to enable better dissipation of heat from the electronic components.
● Flexibility: The adhesive in the bonding sheet is engineered with a degree of flexibility to accommodate the varying expansion and contraction rates between different materials that make up the PCB.
● Electrical Insulation: The adhesive used in PCB bonding sheets is electrically insulating, preventing short circuits and ensuring the protection of electronic components.
● High-Temperature Tolerance: PCB bonding sheet adhesives can withstand high-temperature conditions, making it suitable for use with advanced PCB manufacturing processes.
● Chemical Resistance: The adhesive used in PCB bonding sheets must be chemically resistant to withstand exposure to various chemicals, including solvents used in cleaning processes.
● Moisture Resistance: The adhesives in PCB bonding sheets must also be moisture-resistant to ensure the PCB’s overall reliability and prevent damage from moisture buildup.
PCB Bonding Sheet: Packaging and Storage Conditions
In the PCB manufacturing industry, bonding sheet is typically supplied as rolls that are 24 inches (610 millimeters) wide and 250 feet (76 meters) long, featuring nominal 3-inch (76 millimeters) cores. To meet specific requirements, narrower widths or cut sheets can also be made available upon prior request.
It is essential to handle FPC bonding sheet with care and store it in its original packaging. Suitable temperature conditions range between 4 and 29 degrees Celsius (40 and 85 degrees Fahrenheit), and the relative humidity must remain below 70%. It is not advisable to expose the product to freezing conditions, and it must be kept free from contaminants, dry, and adequately protected at all times.
Performance and Reliability Evaluation of Bonding Sheets in PCBs
The performance and reliability evaluation of bonding sheets in PCBs typically involves various tests and analyses, including:
● Adhesion strength test: measuring the force required to separate the bonding sheet from the substrate or component.
● Shear strength test: measuring the force required to break the bond between two surfaces bonded by the sheet.
● Peel strength test: measuring the force required to peel the sheet from the substrate or component.
● Thermal cycling test: subjecting the bonded assembly to alternating high and low temperature conditions to evaluate its resistance to thermal stress and fatigue.
● Environmental testing: subjecting the bonded assembly to humidity, salt spray, and other environmental conditions to evaluate its resistance to corrosion and degradation.
● Electrical testing: measuring the electrical conductivity, insulation resistance, and dielectric properties of the bonded assembly.
● Failure analysis: identifying the mode and cause of failure, such as adhesive failure, cohesive failure, interfacial failure, or material degradation.
● Statistical process control: monitoring and analyzing the bonding process parameters and quality characteristics to ensure consistent and reliable bonding performance.
By conducting these tests and analyses, manufacturers and users of bonding sheets for PCB applications can assess their suitability, performance, and reliability under different conditions and requirements.
Bonding Technologies and Their applications in PCB Assembly
There are several bonding technologies used in PCB assembly, depending on the application and requirements. Some common bonding technologies include:
● Soldering: using metallic alloys with a low melting point to form a mechanical and electrical bond between two metals. It is widely used for bonding components, connectors, and other metal structures in PCB assembly processes, such as reflow soldering, wave soldering, and selective soldering.
● Conductive adhesive bonding: using conductive adhesives to form a bond between two structures with electrical conductivity. It is suitable for applications requiring high electrical conductivity, flexibility, and low-temperature operation, such as flexible circuits, RFID tags, and sensors.
● Anisotropic conductive film (ACF): using a thermoplastic adhesive film with conductive particles to form a mechanical and electrical connection between two contact pads. It is used for bonding fine pitch, high-density components, such as LCDs, OLEDs, and IC chips.
● Non-conductive adhesive bonding: using non-conductive adhesives to form a mechanical bond between two structures with insulating properties. It is suitable for applications requiring high mechanical strength, chemical resistance, and environmental stability, such as conformal coatings, encapsulants, and gaskets.
● Thermal compression bonding: using heat and pressure to form a mechanical and electrical bond between two surfaces through intermolecular forces. It is suitable for applications requiring high reliability, accuracy, and low resistance, such as micro-electromechanical systems (MEMS), wireless modules, and medical devices.
By selecting the appropriate bonding technology and process parameters, PCB manufacturers and assemblers can achieve the desired performance, reliability, and cost-effectiveness for their products.
Future Trends and Challenges in Bonding Sheet Technology
Some potential future trends and challenges in bonding sheet technology for PCBs could include:
● Integration with emerging materials and manufacturing processes, such as flexible and stretchable electronics, additive manufacturing, and 3D printing.
● Development of new bonding sheet materials with enhanced mechanical, thermal, and electrical properties, as well as compatibility with different substrate materials.
● Implementation of advanced bonding techniques, such as laser bonding, ultrasonic bonding, and thermo-compression bonding.
● Improvement of bonding sheet reliability and durability in harsh environments, such as high temperature, humidity, vibration, and corrosion.
● Optimization of bonding sheet design and assembly parameters for high-density and complex PCBs, such as multi-layer, fine-pitch, and mixed signal designs.
● Compliance with environmental regulations and sustainability standards, such as RoHS, REACH, and circular economy principles.
Summary
As a premium PCB manufacturing and PCB Assembly factory, we take pride in using only the highest quality adhesives in our manufacturing process. This commitment to quality enables us to offer our customers the most superior PCB manufacturing and assembly services possible. Moreover, we are proud to be an ISO 9001 certified company, which ensures that we uphold high-quality standards across all our products, regardless of project specifications.
At JarnisTech, we offer a diverse range of rigid and flexible printed circuit board (PCB) solutions that will suit your project needs. If you have any inquiries or require further information, please do not hesitate to reach out to us or submit a quote request. We are happy to provide additional details and pricing information to help you find the ideal solution for your project.
Related Posts:
1. Selecting PCB Laminate Materials: A Comprehensive Overview
2. PCB Copper Trace Width and Space: Everything You Need to Know About Them
3. Which Types are Most Commonly Used in PCB Substrates?
4. What Is Fiberglass PCB and Why Fiberglass Used in PCB Manufacturing?
5. Standard PCB Thickness-Choosing the Correct Thickness for PCB