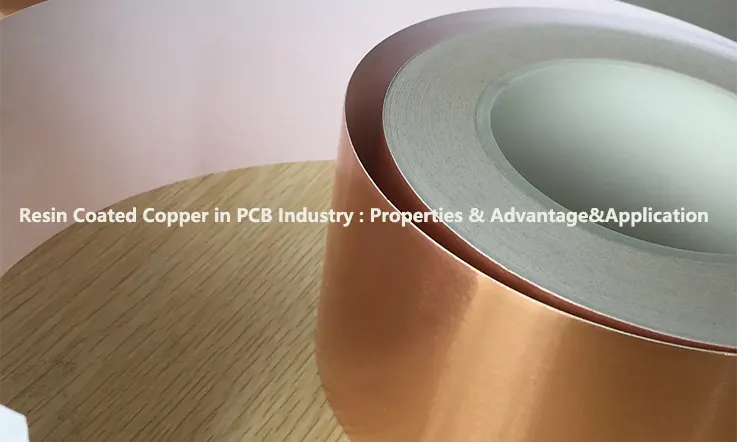
In current electronic assemblies, embedded passive components are prevalent, particularly in devices such as cellular phones, camcorders, computers, and defense equipment. This is largely driven by market pressures to produce compact products with greater functionality at lower costs. To address this, one strategy involves embedding passive components in the substrate to reduce the number of surface-mounted components required.
Interconnect technology for surface-mounted passive components can, however, limit board design and constrain the overall system speed. By using embedded passive components, the functional footprint can be minimized, and the system performance can be improved. As a result, embedding passive components is a viable technique for achieving these goals in the fabrication of printed circuit boards (PCBs).
This article explores the features, advantages, and applications of using resin-coated copper in PCB manufacture.
What Is Resin Coated Copper(RCC) in PCB Industry ?
The limitations of fiberglass-reinforced dielectrics have prompted many companies to seek alternative materials. These limitations include poor hole quality and lengthy drilling durations, as well as restrictions on how thin PCBs can be due to the thickness of woven fiberglass. To circumvent these difficulties, copper foil is used as a carrier for the dielectric in a novel material known as Resin Coated Copper (RCC). RCC is commonly used in the construction of multilayer circuitry, especially in High-Density Interconnect (HDI) PCBs.
RCC films are available in various configurations, each with a different copper thickness and dielectric thickness. These configurations offer trade-offs between filling underlying circuitry and maintaining the desired dielectric thickness. In the production process of HDI PCBs, RCC replaces standard bonding sheet and copper foil as the insulating medium and conducting layer.
A non-mechanical drilling method, such as a laser, is used to construct micro-via interconnect. RCC materials are compatible with typical PCB fabrication processes, such as layup, lamination, and DES, and are well-suited for mass blind microvia production techniques.
Manufacturing of Resin Coated Copper
Here are some possible steps involved in the manufacturing of resin coated copper:
● Cleaning: The copper substrate is cleaned thoroughly to remove any surface contaminants such as oils, dust, or grease.
● Coating Application: A resin coating is applied to the copper substrate using a variety of techniques, such as dip coating, spray coating, or electroplating.
● Curing: The resin-coated copper is then subjected to a curing process, which involves heating the material to a specific temperature for a set period of time. This process results in the cross-linking of the resin molecules, which improves the adhesion and mechanical properties of the coating.
● Post-Treatment: Once the curing process is complete, post-treatment steps may be necessary, such as surface smoothing and polishing, to ensure the final product meets the required specifications.
● Quality Control: The completed resin coated copper product is inspected thoroughly to ensure it meets the required standards for properties such as adhesion, thickness, and uniformity.
● Packaging and Shipping: The final resin coated copper product is then packaged and shipped to the end-user, often in reels, coils, or sheets, depending on the application and customer requirements.
Types of Resin Coated Copper
In the context of built-up multilayer circuitry, resin coated copper is a relatively unconventional choice of dielectric material. However, there are numerous options for resin coated foils that come in a range of designs with differing thicknesses of copper and dielectric materials. These foils offer trade-offs that balance the need to fill underlying circuitry with the requirement for a specific dielectric thickness.
● Single Pass Resin Coated Copper( Single-stage): Single Pass Resin Coated Copper (SPRCC) is a type of copper foil material that features a specially engineered epoxy resin system that is applied once onto copper in a semi-cured (B-stage) state. During lamination, SPRCC exhibits the appropriate rheology to fill and encapsulate the underlying circuitry while leaving sufficient resin residue to function as a dielectric material.
The unique epoxy resin system used in SPRCC provides superior adhesion and thermal performance, making it an ideal choice for challenging PCB applications. The single-pass coating process not only enhances the efficiency of the manufacturing process but also enables greater design flexibility to adjust the resin thickness to meet specific dielectric thickness requirements.
Therefore, SPRCC is a reliable and cost-effective option in PCB manufacturing, offering excellent electrical, thermal, and chemical properties that meet the high demands of modern electronics design.
● Double Pass Resin Coated Copper (Dual-stage): Double Pass Resin Coated Copper (DRC) is a type of copper foil material that has been coated with two different types of high-temperature epoxy. The first coating is a fully cured C-stage epoxy, which acts as an electrically isolating dielectric barrier. The second coating is a semi-cured B-stage epoxy, which functions as an adhesive to bind the copper to the PCB’s inner layer and fill any existing gaps in the underlying circuitry.
Both coatings in DRC are high temperature epoxy, specifically designed to meet the demanding conditions of PCB manufacturing. This double-layered design allows for improved adhesion and a stronger bond between the copper and the inner layers of the PCB. Additionally, DRC offers a higher dielectric strength and thermal reliability, making it a preferred choice in many PCB applications.
● C-stage Coating: In the manufacturing of printed circuit boards (PCBs), various stages of coating are applied to the copper foil to provide functional attributes to the final product. The C-stage coating serves as the electrically isolating dielectric barrier, which separates the outer layer of copper from the underlying conductive copper layer. On the other hand, the B-stage coating acts as an adhesive that binds the resin-coated copper to the thin inner layer.
The B-stage coating is critical in that it fills the inner layer circuitry and any buried vias to ensure a robust connection of the layers. During PCB lamination, the B-stage resin promotes adhesion between the layers and also acts as a filler for the inner layer circuitry, while the C-stage coating ensures the necessary dielectric thickness between the layers. Together, these coatings, among other processing factors, play a crucial role in the performance and reliability of the final PCB product.
Resin Coated Copper Properties
Resin-coated copper (RCC) has a wide range of applications due to its exceptional electrical and mechanical properties, making it a versatile solution for PCB design. The polymer resin coating significantly enhances the copper wire’s properties such as abrasion resistance, flexibility, and corrosion resistance, which are critical factors in PCB design.
The resin coating on the copper acts as a barrier that helps prevent oxidation, thereby improving the wire’s lifespan and maintaining its electrical conductivity. Additionally, RCC exhibits excellent thermal conductivity and has a high melting point, enabling it to perform effectively and efficiently even under extreme heat.
Resin Coated Copper (RCC) is a highly versatile material widely utilized in numerous applications due to its impressive mechanical and electrical traits. The polymer resin coating applied to the copper enhances the wire’s flexibility, abrasion resistance, and corrosion resistance, resulting in a prolonged lifespan. Moreover, the resin-coated copper mitigates copper oxidation, improving the wire’s durability further. RCC boasts a high melting point and excellent thermal conductivity, enabling it to efficiently conduct electricity and withstand high temperatures.
As a result, RCC is a preferred choice in high-frequency applications, where minimizing energy loss and heat dissipation are critical considerations. RCC materials are ideal for use in various industrial sectors, including telecommunications, automotive, healthcare, aerospace, and many more. Our RCC materials offer reliability and performance, making them an excellent choice for PCB design engineers.
Microvias and Resin-Coated Copper
Microvias are an essential component of high-density printed circuit boards as they reduce layer count and improve processing speeds. The presence of resin-coated copper enhances this effect by reducing the time it takes for electrical signals to travel between devices as board density increases. Laser or plasma ablation techniques produce blind vias with a capacitance of about 0.05 picoFarad (pF), significantly lower than the capacitance of mechanically drilled through-holes of around 1 picoFarad (pF).
The fabrication of densely packed circuit boards that require a significant number of blind and buried vias to achieve high electrical performance necessitates new materials such as resin-coated copper. The unique all-resin structure of this material allows for the production of ultra-small vias of less than 6 mils and reduced line and spacing features, permitting improved circuit density. Advanced formation techniques like laser and plasma ablation are being explored for cost-efficient mass-hole formation.
RCC finds numerous applications in various industries like automotive, aerospace, electronics, and telecommunications. Its excellent mechanical and electrical properties make it an ideal material for wire harnesses, printed circuit boards, electronic components, transformers, and motors. RCC is perfectly suited for harsh environments that expose it to heat, moisture, and harsh chemicals. It is an optimal choice for applications that require reliable and durable wires with high electrical conductivity and mechanical strength.
Microvia Forming Technique : Laser Ablation
Laser ablation is a highly effective microvia formation process that can be utilized with unreinforced dielectrics, resulting in small hole diameters for microvias of 6mil (0.15mm), 5mil (0.12mm), 4mil (0.1mm), and 3mil (0.08mm) or less (0.075mm). The presence of fiberglass can hinder the use of lasers for via creation. Laser drilling significantly reduces consumable costs, making it a more cost-effective and time-efficient option than conventional drilling. Guided laser beams are used on RCC to break down copper and dielectric into particulate and/or gaseous materials during microvia creation.
The dielectric layer, which may include low flow PP and polyimide, can be ablated alongside the outer layer copper. However, the ability to do so is dependent on the laser type utilized. While RCC is a desirable material for HDI board production, its high cost prompts many HDI PCB fabricators to replace it with 106PP and copper foil as a cost-effective alternative.
Applications of Resin Coated Copper
Here are some possible applications of resin coated copper:
● Printed Circuit Boards (PCBs): Resin coated copper is commonly used in the manufacture of PCBs, as the coating protects against oxidation and aids in etching processes.
● Electric Motors: Resin coated copper wires and windings are commonly used in electric motors, as the coating improves insulation and prevents short circuits.
● Transformers: Resin coated copper is used in transformers, as the coating can improve the thermal stability and electrical insulation of the material.
● Communication Cables: Some communication cables, such as Cat5 and Cat6 Ethernet cables, use resin coated copper wires to improve signal quality and reduce interference.
● Automotive Electronics: Resin coated copper is used in automotive electronics, such as ABS sensors and fuel injection systems, due to its ability to withstand harsh environments and reduce electromagnetic interference.
● Aerospace Industry: Resin coated copper is used in the aerospace industry due to its lightweight properties, high strength-to-weight ratio, and excellent corrosion resistance.
What’s the Best RCC Laser Microvia Diameter ?
As a PCB design engineer, it’s crucial to carefully consider microvia diameters when designing a circuit board with blind microvias that require the via-in-pad treatment process. To achieve optimal results with the laser drilling process, it’s essential to use the same diameter across all microvias. A small microvia diameter will result in low-quality copper deposition and plating on the microvia walls and copper cap, leading to larger dimples. Conversely, a large microvia diameter will yield good copper deposition and plating, leading to acceptable dimples for planarized pads.
After years of experience in laser drilling RCC and “copper + 106 PP,” we’ve found that microvias with a diameter of 4 mil are the optimal choice for HDI boards. This is the case even when the board requires ultra-fine pitch PoP component soldering. It’s imperative to maintain consistent microvia diameters across the board to ensure high-quality copper deposition and plating, resulting in adequate planarized pads.
Advantage of Resin Coated Copper
Before the advent of resin-coated copper, constructing boards compatible with blind vias often involved utilizing double-sided laminate-based structures, like Kapton film-based, nonwoven aramid reinforced, FR-4, even after the discovery of resin-coated copper. While such double-sided cores improved registration of conformal mask holes to layer 2 and (n-1), there were numerous issues with the designs, making them less appealing. These issues can be entirely avoided by using resin-coated copper, which simplifies the entire process.
In a six-layer design using double-sided lamination, three thin laminations are required for circuitization, which means many layers of prepreg are employed to build the dielectric. Maintaining thickness consistency can be challenging, and changing dielectric properties of the prepreg concerning thickness can affect impedance. These issues are nonexistent when using resin-coated copper, which requires only two circuitizations on thick laminates, resulting in minimal changes to the overall dielectric layers. Moreover, the layup process is streamlined since no separate plies of prepreg and copper foil are needed. The utilization of resin-coated copper reduces the overall cost of materials compared to the use of double-sided lamination.
RCC has become a popular choice for various applications due to its numerous advantages, including high electrical conductivity, high mechanical strength, and exceptional durability. The resin-coated copper prevents wire breaking or cracking due to bending or stretching, making it reliable for use in high-stress environments. Additionally, it provides a barrier against moisture and other environmental factors, shielding the wire from harm.
Disadvantages of Resin Coated Copper
Here are some possible disadvantages of resin coated copper:
● Limited Processing Window: The resin coating process needs to be carried out under specific conditions, such as temperature and humidity, and any deviation from these conditions can result in poor adhesion and coating defects.
● Reduced Heat Dissipation: The coating layer reduces the thermal conductivity of the copper substrate, limiting the heat dissipation properties of the material.
● Environmental Concerns: Some resin coatings may contain harmful chemicals that can pose environmental risks during production or recycling.
● Higher Cost: The additional cost of the resin coating layer can increase the price of the copper-based products, making them more expensive than non-coated alternatives.
● Reduced Solderability: The resin coating can impact the solderability of the copper, making it more difficult to bond the material to other substrates.
● Fragility: The coating layer can be prone to cracking or abrasion, which can compromise the integrity of the material and lead to failure over time.
Future Trends and Developments in Resin Coated Copper
Here are some possible future trends and developments in resin coated copper:
● Increased use in high-speed and high-frequency applications, such as 5G networks, requiring highly conductive and low-loss materials.
● Development of new resin formulations that enhance the properties of resin coated copper, such as improved adhesion and mechanical strength, leading to longer product lifetimes.
● Commercialization of new applications incorporating resin coated copper, such as electric vehicles and renewable energy systems, due to the material’s low cost, lightweight, and high efficiency.
● Integration of resin coated copper with other materials, like composites and ceramics, to develop new functional materials with unique properties and applications.
● Research on the impact of resin coated copper on the environment and health, leading to the development of more sustainable alternatives and safer manufacturing processes.
Conclusion
Resin coated copper has become an increasingly important material in various industries due to its excellent properties and versatility. The material offers significant benefits such as improved insulation, protection from environmental factors, and enhanced electrical and mechanical properties. However, it also has some limitations such as higher costs and reduced heat dissipation.
As the demand for more efficient and durable materials increases, resin coated copper is likely to continue to be a vital material for various industries, including aerospace, automotive, and consumer electronics. Ongoing research and development may also lead to further advances in the formulation and processing of the material, expanding its range of applications while addressing potential drawbacks.
In addition, The increasing demand for high-density PWB substrates is rapidly expanding, and this trend is expected to continue in the foreseeable future. As a result, companies are under pressure to provide affordable technical solutions that meet minimum standards.
Microvias offer a solution for high-density connections, and coated coppers can be utilized to create microvias using techniques like plasma or laser ablation, allowing fabricators to offer cost-effective HDI alternatives. With advancements in these processes and materials, smaller, thinner, lighter, and faster boards will become increasingly prevalent.
JarnisTech, located in China, provides PCB manufacturing and PCB assembly services, including comprehensive PCB raw materials such as high-quality resin-coated copper to meet customers’ high-quality PCB circuit board requirements. We provide one-stop services from component purchase to Full and Partial Turnkey PCB Assembly. If you have any inquiries about resin-coated copper, please feel free to contact us, and we will offer the best service.
Related Posts:
1. Selecting PCB Laminate Materials: A Comprehensive Overview
2. PCB Copper Trace Width and Space: Everything You Need to Know About Them
3. Which Types are Most Commonly Used in PCB Substrates?
4. What Is Fiberglass PCB and Why Fiberglass Used in PCB Manufacturing?
5. Standard PCB Thickness-Choosing the Correct Thickness for PCB