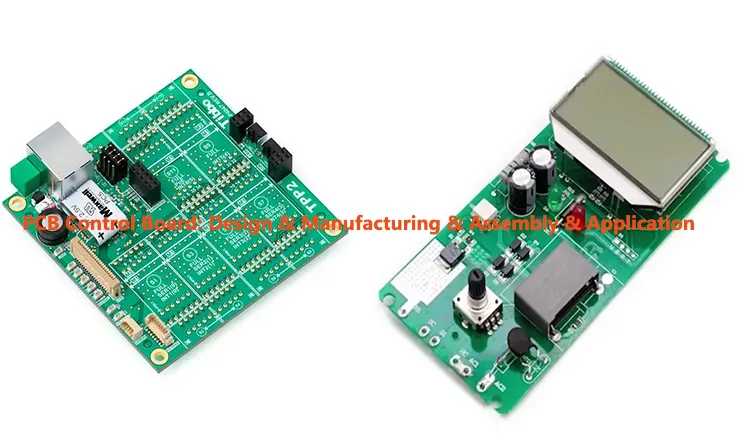
A PCB control board, also known as a printed circuit board control board, is a critical component in electronic devices that controls and manages the flow of signals and power between different components on the board. It is responsible for regulating the operation of the device and ensuring that it functions correctly.
The PCB control board provides a stable and reliable platform for electronic components to be mounted and connected, reducing the risk of loose connections or short circuits. It is an essential component in modern electronics, contributing to the efficiency and reliability of electronic devices.
The importance of the PCB control board lies in its ability to provide a standardized platform for electronic components and circuits. By using a PCB control board, manufacturers can streamline the design and production process, reduce costs, and improve the overall quality of their products. Additionally, the use of PCB control boards allows for easier repair and maintenance of electronic devices, as individual components can be easily replaced or upgraded.
PCB Control Board Basics
The PCB control board is a type of printed circuit board that contains electronic components and circuits that are designed to control and manage the flow of signals and power in electronic devices. It is an essential component in most modern electronic devices, from simple household appliances to complex industrial systems.
The basic structure of a PCB control board consists of a substrate material, typically made of fiberglass or plastic, with a thin layer of copper foil laminated onto it. The copper layer is etched to create a pattern of conductive traces that connect the various electronic components on the board. The conductive traces are arranged in a specific layout, called a circuit or circuitry, that enables the control board to perform its intended function.
The electronic components that are mounted on the PCB control board include resistors, capacitors, diodes, transistors, and integrated circuits, among others. These components are soldered onto the board to form the circuitry. The PCB control board may also include connectors, switches, and other components that allow it to interface with other electronic devices.
The design of a PCB control board is critical to its performance and reliability. The layout of the conductive traces must be optimized to minimize interference and signal loss, while the placement of components must be carefully considered to ensure that the board can operate within its specified temperature and power requirements.
Overall, understanding the basics of the PCB control board is essential for anyone involved in the design, manufacture, or repair of electronic devices. By mastering the principles of PCB control board design, engineers and technicians can create more efficient, reliable, and high-quality electronic products.
What are Materials used to manufacturing PCB Control Board ?
The materials used in the manufacturing of PCB control boards can vary depending on the specific requirements of the application, but typically include the following:
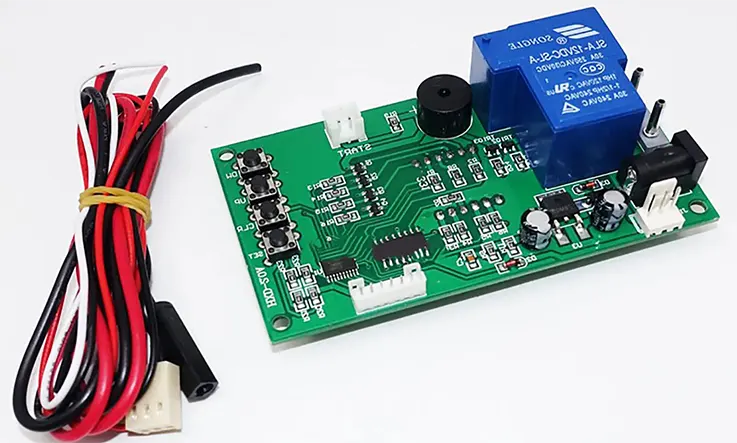
Substrate materials: The substrate material is the base material on which the conductive traces and pads are etched. Common substrate materials used in PCB manufacturing include fiberglass-reinforced epoxy (FR-4), polyimide, and Rogers.
Copper foil: Copper foil is used to create the conductive traces and pads on the substrate. The thickness of the copper foil can vary depending on the required current-carrying capacity and resistance.
Solder mask: Solder mask is a protective coating applied over the copper traces to prevent solder from adhering to areas where it is not desired.
Silkscreen: Silkscreen is a labeling system that is printed onto the board to identify components, test points, and other important features.
Surface finish: The surface finish is a coating applied to the exposed copper on the board to prevent oxidation and improve solderability. Common surface finishes include HASL (hot air solder leveling), ENIG (electroless nickel immersion gold), and OSP (organic solderability preservative).
Adhesive: Adhesive is used to bond layers of the board together and to hold components in place during assembly.
Overall, the materials used in the manufacturing of PCB control boards must be carefully selected to ensure that they meet the required specifications for performance, reliability, and manufacturability. By choosing the right materials and following best practices in PCB design and manufacturing, manufacturers can ensure that their PCB control boards are of the highest quality and meet the needs of the intended application.
Design and Routing Considerations of PCB Control Board
The layout and routing of a PCB control board are critical steps in the design process that determine the performance, reliability, and manufacturability of the board. Here are some key factors to consider when laying out and routing a PCB control board:
Trace routing: Conductive traces should be routed in a way that minimizes signal loss, reduces noise, and maintains signal integrity. This can be achieved by using proper trace widths, spacing, and routing patterns, as well as by using ground planes and signal layers.
Power requirements: One of the most critical design considerations for a PCB control board is determining the power requirements of the circuitry and ensuring that the board can handle the required voltage and current levels. Designers must carefully select the appropriate power supply components, such as voltage regulators and capacitors, and ensure that they are placed correctly on the board.
Signal integrity: Another critical design consideration is ensuring that the conductive traces on the PCB control board have low impedance and minimal signal loss. This can be achieved by carefully selecting trace widths, spacing, and routing patterns, as well as using proper grounding techniques.
Component placement: The placement of electronic components on the PCB control board is also essential. Components must be arranged in a way that minimizes interference and signal crosstalk, while also allowing for efficient heat dissipation and easy access for maintenance and repair.
Thermal management: The PCB control board must be designed to handle the heat generated by electronic components during operation. This can be achieved by using adequate heat sinks, thermal vias, and other cooling components.
Manufacturing considerations: The design of the PCB control board must also take into account the limitations and capabilities of the manufacturing process. Designers must ensure that the board can be manufactured efficiently and cost-effectively, while also meeting all quality and reliability standards.
EMI/EMC compliance: The PCB control board must comply with electromagnetic interference (EMI) and electromagnetic compatibility (EMC) regulations to prevent interference with other electronic devices and ensure that the device operates reliably.
Design for manufacturability: The layout and routing of the board should be designed to facilitate the manufacturing process. This includes considerations such as panelization, fiducials, and proper spacing between components.
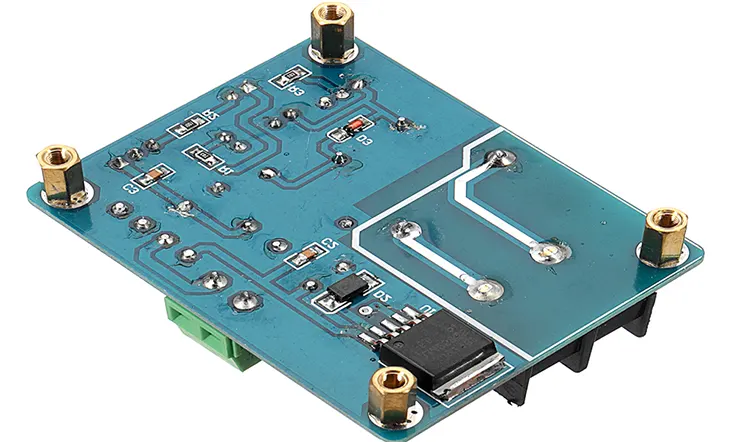
As a result, the design of the layout and routing of the PCB control board should take into account the specific requirements of the intended application, as well as the limitations of the manufacturing process. By carefully considering these factors, designers can create a highly efficient, reliable, and manufacturable PCB control board.
PCB Control Board: Manufacturing and Assembly
The manufacturing and assembly of a PCB control board involves several critical steps that determine the quality and reliability of the final product. Here are some of the key steps involved in manufacturing and assembling a PCB control board:
PCB fabrication: The first step in the manufacturing process is to fabricate the PCB itself. This involves several steps, including drilling, plating, and etching the board to create the conductive traces and pads.
Solder paste application: Once the board is fabricated, solder paste is applied to the pads on the board using a stencil. The paste is a mixture of solder and flux that helps to hold the components in place during assembly.
Component placement: Electronic components are then placed on the board using automated pick-and-place machines. The components are aligned with the pads on the board and held in place by the solder paste.
Soldering: The board is then moved into a reflow oven, where the solder paste is heated and melted to create a permanent bond between the components and the board. This process is called surface mount technology (SMT) soldering.
Through-hole components: If the design includes through-hole components, they are inserted into the board and soldered using wave soldering or hand-soldering techniques.
Inspection and testing: After assembly, the board is inspected for defects, such as solder bridges, missing components, and misaligned components. The board is then tested to ensure that it meets the required specifications for performance and reliability.
Final packaging: Once the board has passed inspection and testing, it is packaged and prepared for shipment to the customer or for use in the final product assembly.
In a word, the manufacturing and assembly of a PCB control board require a high degree of precision and attention to detail. By following best practices for PCB assembly and testing, manufacturers can ensure that the final product is of the highest quality and meets the required specifications for performance and reliability.
Testing and Quality Control of Control Circuit Board
Testing and quality control are critical steps in the manufacturing process of a PCB control board. Here are some of the key steps involved in testing and quality control:
Visual inspection: The board is visually inspected to check for any defects, such as missing components, incorrect placement, or soldering defects.
Functional testing: The board is tested to ensure that it functions as intended. This can include testing for electrical continuity, signal quality, and power consumption.
Environmental testing: The board is tested under various environmental conditions, such as temperature and humidity, to ensure that it can withstand the conditions it will be exposed to in its intended application.
Electrical testing: The board is tested using specialized equipment to measure its electrical characteristics, such as impedance, capacitance, and resistance.
Reliability testing: The board is subjected to various stress tests to assess its reliability and durability. These tests can include thermal cycling, vibration, and shock testing.
Quality control documentation: All testing results and quality control procedures are documented to ensure traceability and accountability throughout the manufacturing process.
To sum up, testing and quality control are critical steps in ensuring that a PCB control board meets the required specifications for performance and reliability. By following rigorous testing procedures and documenting all results and procedures, manufacturers can ensure that the final product is of the highest quality and meets all required standards.
Control PCB Board Application
PCB control boards are used in a wide range of electronic devices and applications, including:
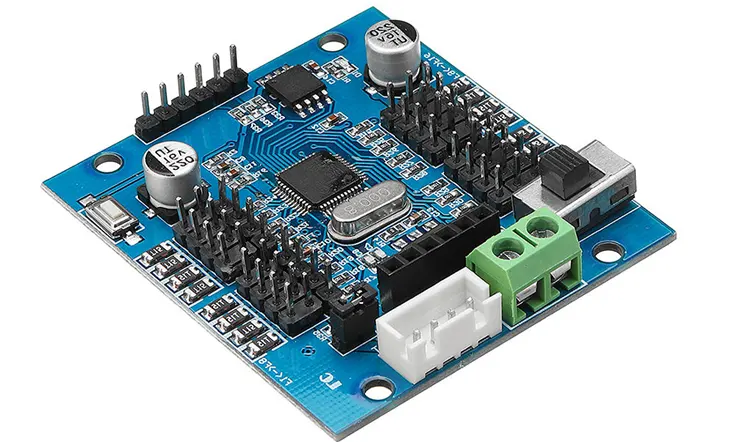
Consumer electronics
PCB control boards are used in a variety of consumer electronics, such as smartphones, laptops, televisions, and home appliances, to control the flow of signals and power between different components.
Industrial automation
PCB control boards are used in industrial automation systems to control and monitor the operation of machinery, equipment, and processes.
Automotive
PCB control boards are used in automotive applications to control the operation of various systems, such as the engine, transmission, and braking systems.
Aerospace
PCB control boards are used in aerospace applications to control the operation of various systems, such as flight control systems, navigation systems, and communication systems.
Medical devices
PCB control boards are used in medical devices, such as diagnostic equipment and monitoring systems, to control the flow of signals and power between different components.
Military and defense
PCB control boards are used in military and defense applications to control the operation of various systems, such as communication systems, radar systems, and weapon systems.
Overall, PCB control boards are an essential component in modern electronics, contributing to the efficiency, reliability, and functionality of electronic devices in a wide range of applications.
How to Choose a High Quality PCB Control Board Fabricator ?
Choosing a high-quality PCB control board fabricator is crucial to ensure that your electronic device operates efficiently and reliably. Here are some tips to help you choose a reputable and reliable PCB fabricator:
Look for experience: A PCB fabricator with years of experience in the industry is more likely to have a good understanding of the manufacturing process and can produce high-quality PCBs consistently.
Check certifications: Ensure that the PCB fabricator has the necessary certifications and meets industry standards such as ISO 9001, UL, and RoHS compliance.
Quality control processes: A reliable PCB fabricator should have strict quality control processes in place to ensure the PCBs are manufactured to the required specifications and standards.
Technical support: Look for a PCB fabricator that offers technical support and assistance during the design and manufacturing process to help identify and resolve any issues that may arise.
Production capacity: Consider the production capacity of the PCB fabricator. A fabricator with a large production capacity can handle large orders and can deliver the PCBs on time.
Cost: While cost is an important factor, it should not be the only consideration. Choosing a fabricator based solely on cost can result in lower quality PCBs that may not meet your requirements.
Reviews and referrals: Check online reviews and ask for referrals from other customers to get an idea of the fabricator’s reputation and the quality of their work.
By considering these factors, you can choose a high-quality PCB control board fabricator that meets your needs and produces reliable and efficient PCBs for your electronic devices.
Why Choose Us?
JarnisTech – 20 Years Experience PCB Control Board Manufacturer
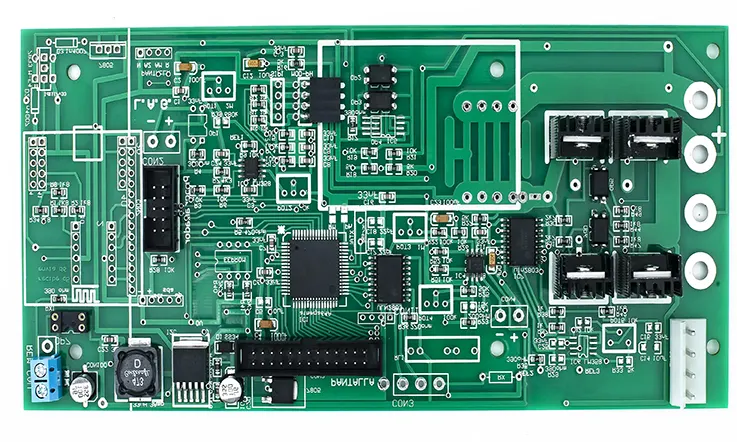
Jarnistech is a reputable manufacturer that specializes in the production of high-quality PCB control boards for over 20 years. We are committed to providing our clients with the best quality products that meet their business requirements.
Our PCB control boards are available in a wide range of designs and configurations. They are designed with advanced features that ensure high reliability in connecting multiple PCBs. We have a team of highly skilled and knowledgeable engineers who are experts in component sourcing, fabrication, assembly, and production of PCB control boards. Our engineers use advanced manufacturing technology to produce products that meet the highest quality standards.
Our PCB control boards are large printed circuit board formats that serve as a backbone for connecting various PCBs to form a computer bus. We also manufacture PCB control boards that function as a connection between active PCBs. Our products feature high mechanical stability and strength, high-signal integrity design, controlled impedance, buried vias, back drilling, and high speed.
At Jarnistech, we understand the importance of customer satisfaction, and we strive to provide our clients with the highest level of satisfaction. We offer competitive prices and low MOQ to support starting businesses. All our products have qualifications from ISO9001, ISO14000, UL, and more. We do not compromise on the quality of our products, and we guarantee high-quality PCB control boards.
Apart from PCB control boards, we also manufacture Rogers 3003, Rogers 5880, Rogers 4360, Rogers 3006, Rogers 3010, IC Substrate, Surface finish PCB, Flex PCB assembly, Power supply PCB, Inverter PCB, and more. Jarnistech is your one-stop solution for your PCB needs.
Choose Jarnistech as your number one supplier of high-quality PCB control boards. We are an expert in manufacturing authentic and genuine products that meet the highest quality standards. Our wide range of PCB control boards will surely meet your requirements.
Conclusion
PCB control boards are a critical component in modern electronic devices, providing the necessary control and signal routing to ensure their proper operation. Designing and manufacturing a high-quality PCB control board requires careful consideration of factors such as power requirements, signal integrity, component placement, thermal management, manufacturing considerations, and EMI/EMC compliance.
The layout and routing of the board must also be carefully designed to ensure efficient signal flow and minimal interference. Manufacturing and assembly involve several critical steps, including PCB fabrication, component placement, soldering, inspection and testing. Quality control procedures are essential to ensure that the final product meets the required specifications for performance and reliability.
PCB control boards have a wide range of applications in consumer electronics, industrial automation, automotive, aerospace, medical devices, military, and defense. By following best practices in PCB design, manufacturing, and testing, manufacturers can ensure that their PCB control boards are of the highest quality and contribute to the efficiency and reliability of electronic devices.