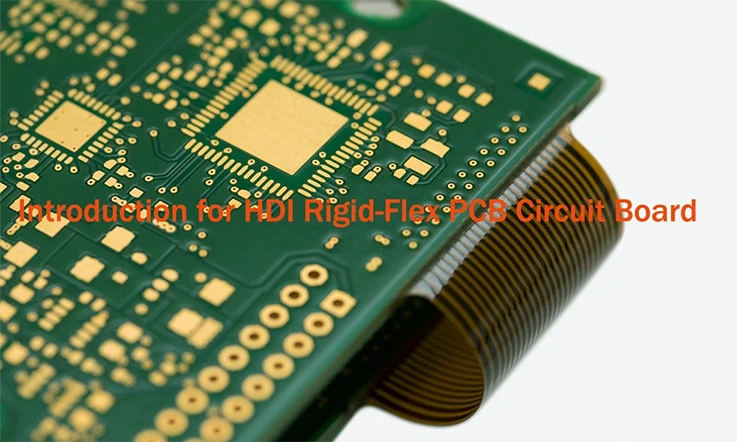
HDI (High-Density Interconnect) rigid-flex PCB denote a sophisticated types of printed circuit boards, combine the advantages of both rigid and flexible PCB techniques. Courtesy of HDI technology, these boards manage to provide intensified component density, enhanced design flexibility, improved reliability and optimized space utility.
In this post, we will discuss their key features, manufacturing considerations, and applications for HDI rigid-flex PCB. A thorough comprehension of the merits and factors related to HDI rigid-flex PCB enables engineers and designers can harness their potential for designing cutting-edge electronic devices.
What Materials used for HDI Rigid-flex PCB Manufacturing?
HDI Rigid-flex PCB are manufactured using a combination of materials to achieve the desired functionalities. Generally, rigid laminates, comprising FR-4 (a flame-resistant glass epoxy substance), or other high-performance substances such as polyimide or PTFE (polytetrafluoroethylene) are employed in the rigid domains. These materials extend rigidity, structural sustenance, and superior electrical efficacy.
Regarding the flexible sections, materials such as polyimide (PI) or flexible liquid crystal polymer (LCP) are frequently employed. These materials provide excellent pliability, robust thermal stability and electrical insulation characteristics.
In order to interconnect the rigid and flexible sections, a transitional material is put to use, such as adhesive-based bonding materials or coverlay films composed of polyimide. These materials ensure a dependable connection whilst sanctioning flexibility.
The selection of materials hinges on various factors such as the requisites of the application, operational circumstances, electrical potency, and considerations of cost. Diverse amalgamations of materials can be utilized to customize the HDI Rigid-flex PCB to cater to particular necessities.
Characteristics of HDI Rigid-flex PCB
Enhanced component concentration: HDI technology enables the downsizing of electronic devices by supporting an increased concentration of components and interconnections on the PCB. This is achieved through the use of advanced routing techniques, microvias, and smaller pad sizes.
Flexibility: Rigid-flex PCB provide flexibility and bending capabilities owing to their flexible sections. This allows them to be integrated into devices with complex geometries or those that require repeated bending or folding motions.
Space savings: The integration of rigid and flexible sections within a single PCB eliminates the requirement for additional connectors, cables, and interconnects, thereby achieving significant space savings in the overall device design.
Enhanced Reliability: HDI Rigid-flex PCB demonstrate superior reliability over traditional PCB. The presence of flexible sections mitigates the risk of mechanical stress and fatigue, which can lead to failures. Furthermore, the implementation of advanced materials and manufacturing techniques enhances signal integrity and minimizes the potential for electromagnetic interference (EMI).
Increased design flexibility: The combination of rigid and flexible portions in the PCB offers greater flexibility in designing complex layouts, particularly in devices constrained by limited space. It enables the placement of components and interconnections in multiple planes and allows for 3D configurations.
Cost Efficiency: Though the upfront expenditure for HDI Rigid-flex PCB can supersede that of standard rigid PCB, they frequently present long-term cost benefits. This is attributable to their capabilities for conserving space, mitigating the requirement for additional components, and capabilitie the assembly processes.
Types HDI Rigid-flex PCB
Single Sided Flex: This category of HDI rigid-flex PCB showcases a single flexible layer with components and traces on a single side. It ensures flexibility uni-directionally and is apt for applications confronting space constraints or simplistic bending requisites.
Double Sided Flex: The Double Sided Flex HDI rigid-flex PCB feature flexible layers with components and traces on both sides. This facilitates enhanced routing density and more sophisticated designs in comparison to single-sided flex PCB.
Multi-Layer Flex: The Multi-Layer Flex HDI rigid-flex PCB possess several stacked flexible strata, delivering enhanced flexibility and design alternatives. These can accommodate a greater density of components and intricate routing prerequisites.
Sculptured flex: Sculptured flex HDI rigid-flex PCB have areas where the flexible material is thinned or etched away to reduce bulk and provide more flexibility in specific regions.This facilitates precision in bending or folding at pre-determined zones.
Stacked Rigid-Flex: The Stacked rigid-flex HDI PCB combine multiple tiers of rigid and flexible materials, permitting intricate 3D layouts. They provide significant design flexibility and are apt for applications entailing complex shapes or those demanding numerous rigid and flexible sections.
HDI Rigid-flex PCB Vs Standard PCB Board
HDI rigid-flex PCB and standard PCB contrast in their design, structure, capabilities and uses. Here are several crucial points distinguishing the two:
Design Flexibility: HDI rigid-flex PCB offer greater design flexibility compared to standard PCB. They allow for the integration of rigid and flexible sections on a single board, enabling 3D configurations and conforming to specific device shapes. Standard PCB are limited to rigid structures without the flexibility of bending or folding.
Space Efficiency: HDI rigid-flex PCB is inherently compact and optimal in space utilization in comparison to a standard PCB. The combination of rigid and flexible segments eradicates the necessity for supplementary interconnects, connectors, and wires in the apparatus, yielding a diminished overall footprint.
Component Density: HDI technology used in rigid-flex PCB allows for higher component density and more advanced routing techniques, such as microvias and smaller pad sizes. This enables the design of smaller and more compact electronic devices with increased functionality. Standard PCB generally have lower component density due to their limited routing capabilities.
Reliability: HDI rigid-flex PCB provides superior reliability when contrasted with standard PCB. The employment of flexible materials and cutting-edge production techniques diminishes the peril of mechanical stress, fatigue, and impairment instigated by heat expansion, making them fitting for applications with recurrent bending or oscillation.
Cost: The expenditure tied to HDI rigid-flex PCB typically surpasses that of standard PCB. The intricate fabrication procedures, specific materials utilized, and elevated design complexity all contribute to the heightened cost affiliated with HDI rigid-flex PCB. Standard PCB, with their relatively straightforward design and production, generally offer a more economical alternative.
Applications: HDI rigid-flex PCB are prevalently employed in circumstances demanding compactness, flexibility, and dependability. Their aptitude to adapt to spatially restricted environments, endure flexing, and provide high component density positions them as appropriate for sectors such as aerospace, medical apparatus, consumer electronics, and the automotive industry. Standard PCB, conversely, maintain extensive usage across a wider scope of applications where flexibility and compactness are not paramount factors.
HDI Multi-layer Rigid flex PCB Design Specifications
Design stipulations for HDI multi-layer rigid-flex PCB may shift based on the distinctive application and requirements. Nonetheless, here are some universal considerations and specifications to bear in mind:
Layer stack-up:
Ascertain the quantity of rigid and flexible layers needed for your design. Contemplate the distinct functions and components that necessitate positioning on each layer, along with the flexibility necessities of the flexible sections.
Routing techniques:
Utilize advanced routing techniques, such as microvias, blind and buried vias, to achieve high component density and efficient signal routing between layers. Microvias are particularly useful in HDI designs to enable interconnections in dense areas.
Pad and trace sizes:
Due to higher component density, HDI rigid-flex PCB often require smaller pad and trace sizes to accommodate more components and routing. Ensure that the selected pad and trace sizes comply with the manufacturing capabilities and the required electrical performance.
Damping materials:
Think about including damping materials, like adhesives or coverlay films, to manage vibrations, lessen stress, and enhance the reliability of the rigid-flex PCB.
Bending and folding requirements:
Set forth the flexing and folding stipulations based on the designated utilization of the rigid-flex PCB. Ascertain that the flexible sections along with the total design can endure the anticipated flexing and folding sequences without compromising efficiency or dependability.
Environmental considerations:
Take into account the operating milieu of the PCB and choose for materials, surface finishes, and compositions capable of sustaining temperature fluctuations, humidity, chemical substances, or other environmental factors encountered in the application.
Signal integrity:
Lend particular focus to factors influencing signal integrity, including controlled impedance, impedance matching, along with apt signal grounding, to assure steady signal transmission and reduce the magnitude of signal interference.
Design for manufacturability (DFM):
Maintain a tight-knit collaboration with your PCB manufacturer or engineer throughout the design procedure to guarantee that the design is feasible for manufacturing and aligns with the capabilities and limitations of their fabrication processes.
HDI Rigid-flex PCB Fabrication Process
1.Design: Initiate with the creating of the HDI rigid-flex PCB design, taking into account the layer stack up, component placement, routing and other design considerations. Employ CAD software for the design of the PCB layout and production of all essential files for manufacturing.
2.Material selection: Choose the materials for the rigid and flexible parts of the PCB. Commonly used materials for the rigid laminates such as FR 4 or high performance options like polyimide or PTFE. For the flexible sections materials, like polyimide or flexible liquid crystal polymer are often used.
3.Preparing the rigid layers: Begin the fabrication process with the rigid layers of the PCB. This involves preparing the chosen rigid laminate material by applying a copper layer to both sides, applying the required protective coatings, and drilling holes for vias and component mounting.
4.Preparing the flexible layers: Move on to the flexible layer of the PCB. The flexible substrate is readied by applying copper coatings to both facets, drilling microvias, and incorporating essential insulating layers.
5.Bonding the layers: The rigid and flexible layers are bonded utilizing a fitting bonding substance. This material fortifies the layers and safeguards trustworthy connections amidst them. Bonding materials based on adhesive or coverlay films crafted from polyimide are predominantly utilized in this step.
6.Etching and plating: The excess copper on the layers is then etched away, leaving the mandated circuit designs patterns. Plating processes are employed to bestow conductivity upon the circuit traces and vias, rendering them electrically operational.
7.Finishing processes: Diverse finishing procedures, like solder mask application, silkscreen imprinting, along with the surface finish (for instance, HASL, ENIG, OSP), are executed to safeguard the PCB and increase its functionality and aesthetics.
8.Testing and inspection: The fabricated HDI rigid-flex PCB undergoes thorough testing and inspection to ensure its electrical performance, functionality and adherence to quality standards. This includes electrical tests, visual inspections, and possibly specialized tests based on specific requirements.
9.Assembly: After fabrication, the HDI rigid-flex PCB is ready for component assembly. Surface mount technology or through hole technology can be used, depending on the design and application requirements.
Why HDI Rigid-flex PCB Cost Is Expensive?
Complex manufacturing process: Fabrication process of HDI rigid-flex PCB involves multiple intricate steps, including laser piercing of microvias, orderly laminating of rigid and pliable layers, precise alignment of layers, and advanced plating processes. These additional steps require specialized equipment, expertise, and more time, which increases the overall manufacturing cost.
Specialized materials: HDI rigid-flex PCB generally mandate specific material, such as high performance rigid laminates and flexible substrates like polyimide. These materials are more costly when compared to conventional FR-4 laminates employed in traditional PCB. Along with this, the application of progressive materials possessing peculiar properties such as improved malleability and thermal steadiness, adds to the all-encompassing cost.
Design complexity: HDI rigid-flex PCB are designed for elevated component density and complicated routing prerequisites. Attainment of such designs engages advanced routing methodologies, encompassing microvias, blind vias, and buried vias, which require additional processing steps and expertise. The increased complexity in design and fabrication further propels the escalation of cost.
Lower production volumes: HDI rigid-flex PCB are typically used in specialized applications with relatively lower production volumes compared to standard rigid PCB. The smaller production volumes result in reduced economies of scale, making it less cost-effective for PCB manufacturers to produce HDI rigid-flex PCB.
Testing and quality assurance: HDI rigid-flex PCB undergo thorough testing and inspection to ensure their high reliability and performance. The additional testing steps, including electrical tests and specialized tests (if required), contribute to the overall cost.
Expertise and labor costs: HDI rigid-flex PCB require specialized knowledge, skills, and equipment to design and manufacture successfully. The expertise and labor costs associated with HDI rigid-flex PCB fabrication can be higher compared to standard PCB.
While HDI rigid-flex PCB may have higher upfront costs, they can offer long-term benefits such as space savings, improved reliability, and enhanced functionality, which can offset the initial investment. It’s vital to thoughtfully evaluate the explicit demands of the application and juxtapose the advantages with the expenses while gauging the viability of HDI rigid-flex PCB.
Application of HDI Rigid-flex PCB
HDI rigid-flex PCB find applications in various industries where compactness, flexibility, high component density, and reliability are crucial. Here are some notable applications of HDI rigid-flex PCB:
●Industrial automation
●Internet of Things
●Communication systems
●Aerospace and defense devices
●Consumer electronics
●Automotive
The applications of HDI rigid-flex PCB continue to expand as technology advances and new design possibilities emerge. The unique combination of rigidity and flexibility, coupled with advanced manufacturing techniques, allows for innovation in various industries, enabling the development of smaller, more reliable, and technologically advanced electronic devices.
Final Thought
HDI rigid-flex PCB provide a versatile and powerful solution for modern electronic designs. Their ability to seamlessly integrate rigid and flexible sections allows for compact form factors, improved reliability, and enhanced functionality. HDI technology empowers these PCB with high component density, enabling sophisticated routing techniques and smaller footprint designs.
Even though HDI rigid-flex PCB involve elevated production expenses and intricate designs, their exclusive advantages deem them perfect for applications necessitating spatial optimization reliability and flexibility, such as in aerospace, medical apparatus, automotive and consumer electronics. With technological advances and design requirements evolve, HDI rigid-flex PCB are poised to play a pivotal role in shaping the future of electronics. By leveraging their capabilities and working closely with experienced PCB manufacturers and engineers, designers can unlock new possibilities and achieve innovative solutions.