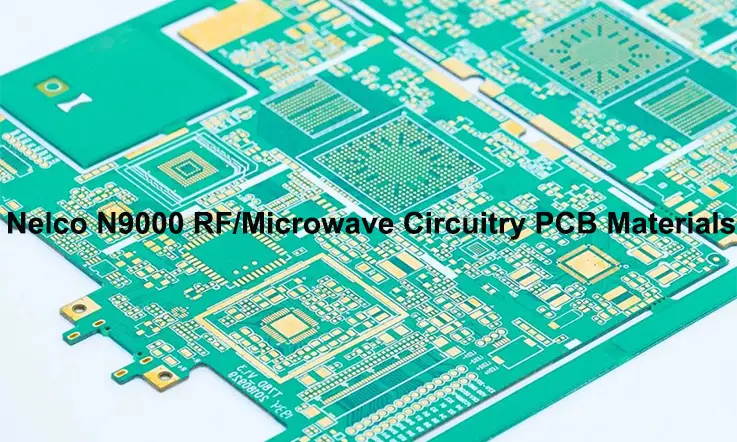
Nelco N9000 is a high-performance PCB material specifically designed for RF and microwave applications. Its exceptional electrical, thermal, and mechanical properties make it an ideal choice for demanding circuit designs. This article explores the unique characteristics of Nelco N9000 and its suitability for high-frequency applications, providing valuable insights for engineers and designers in the RF and microwave industry.
Definition of Nelco RF / Microwave Circuitry PCB Materials
Nelco RF/Microwave Circuitry PCB materials refer to a range of high-performance substrates designed for use in radio frequency (RF) and microwave circuitry applications. These materials offer superior electrical properties and are specifically engineered to meet the stringent requirements of high-frequency circuit designs, making them suitable for use in critical applications such as wireless communication systems, radar systems, and satellite communications.
What Is Nelco N9000 PTFE laminate?
The N9000 PTFE laminate system has been specifically engineered to meet the demanding requirements of critical microwave components, antennas, power amplifiers, and subassemblies. Its exceptional mechanical and electrical performance characteristics position the N9000 PTFE laminate system as the preferred material for high-frequency applications that demand minimal signal loss.
Key Features of Nelco N9000 PCB Laminate
Wide range of controlled dielectric constants: The N9000 PCB laminate offers a complete spectrum of dielectric constants, ranging from 2.08 to 4.50, providing flexibility for various high-frequency applications.
Low dielectric constant option: For very low loss antenna designs, a reinforced PTFE laminate with a dielectric constant of less than 2.17 is available. The PTFE/glass ratio is tightly controlled to ensure consistent performance.
Large sheet sizes: The N9000 laminate is available in sheets up to 80 inches long by 48 inches wide, providing ample material for large-scale PCB production.
Enhanced N9000 IM materials: These materials enable reduced passive intermodulation in antenna and high-power designs, offering up to 25% better performance compared to other PTFE laminates.
Excellent passive intermodulation performance: The N9000 laminate offers two-tone passive intermodulation performance of less than -155 dBc, significantly outperforming other PTFE materials.
Consistent quality: Statistical Process Control (SPC) methods ensure consistent dielectric values from sheet to sheet and lot to lot. Nelco facilities are ISO 9001:2000 quality certified and comply with ISO 14001:2004 environmental regulations. The material also meets UL 94V-0 specifications and is RoHS compliant.
Optimized PTFE processing: The N9000 laminate exhibits superior foil adhesion, offering 50-100% greater adhesion than competitive glass-reinforced PTFE laminates and 200-300% greater adhesion than other ceramic-loaded hydrocarbon laminates. It also demonstrates superior solvent absorption resistance and reduced dielectric constant changes, eliminating the need for additional baking cycles during processing.
Design Considerations and Best Practices for Using Nelco N9000
When designing and working with the Nelco N9000 PCB substrate, it is important to consider certain factors and follow best practices to ensure optimal performance and reliability. Here are some design considerations and best practices for using Nelco N9000:
1.Signal Integrity:
The Nelco N9000 substrate has excellent electrical properties, but it’s crucial to maintain good signal integrity. Proper impedance matching and controlled impedance routing techniques should be employed to minimize signal reflections and maintain signal integrity throughout the PCB.
2.Loss Budget:
The N9000 substrate is known for its low loss characteristics. However, it’s important to calculate the loss budget for your specific application and take into account factors such as trace length, frequency, and copper thickness. This will help ensure that the overall system performance meets the desired specifications.
3.Thermal Management:
The N9000 substrate has good thermal conductivity, which aids in heat dissipation. However, in designs with high-power components or in applications with elevated temperatures, proper thermal management techniques should be implemented. This may include using thermal vias or incorporating heat sinks to dissipate heat effectively.
4.Material Compatibility:
When selecting other materials for the PCB assembly, such as solder masks, adhesives, or surface finishes, ensure compatibility with the Nelco N9000 substrate. Some materials may have different coefficients of thermal expansion (CTE) or may not adhere well to the substrate, leading to reliability issues. Consult the manufacturer’s guidelines and recommendations for compatible materials.
5.Controlled Dielectric Constant:
The Nelco N9000 substrate offers a consistent dielectric constant, which is important for maintaining signal integrity. However, it’s essential to ensure that the fabrication process and handling of the material do not negatively impact its dielectric properties. Avoid excessive pressure, moisture ingress, or exposure to harsh chemicals that could affect the dielectric constant.
6.Design for Manufacturability:
Consider the capabilities and limitations of your PCB manufacturer when designing with the Nelco N9000 substrate. Ensure that the design adheres to their manufacturing guidelines and specifications. Consulting with the manufacturer during the design phase can help identify any potential manufacturing challenges and optimize the design for efficient and cost-effective fabrication.
7.Test and Validation:
Perform thorough testing and validation of the PCB design using the Nelco N9000 substrate. This includes electrical testing, such as signal integrity analysis, impedance measurements, and thermal testing to verify performance against the desired specifications.
8.Environmental Considerations:
Evaluate the operating environment of your application and ensure that the Nelco N9000 substrate meets the necessary requirements. Consider factors such as temperature range, humidity, chemical exposure, and vibration. The N9000 substrate is known for its stability in various environments, but it’s important to validate its suitability for your specific application.
By considering these design considerations and following best practices, you can maximize the benefits of using the Nelco N9000 PCB substrate, ensuring optimal performance, reliability, and manufacturability for your high-frequency and critical microwave applications.
Types of Nelco N9000 PCB laminate
The Nelco N9000 PCB laminate offers a variety of cladding options to suit different design requirements:
1.RTFoil: Available in 18, 35, and 70 µm (0.5, 1, and 2 oz) options.
2. Shiny Copper: Available in 18, 35, and 70 µm (0.5, 1, and 2 oz) options.
3. N Copper: Available in 18, 35, and 70 µm (0.5, 1, and 2 oz) options.
4.Heavy Backed Material: Aluminum and brass cladding options are available upon request, providing additional flexibility for specific applications.
Testing and Validation of Nelco N9000 Performance
Testing and validation are crucial steps to ensure the performance and reliability of PCB designs using the Nelco N9000 substrate. Here are some key aspects to consider when testing and validating the performance of the Nelco N9000:
1. Electrical Testing: Perform electrical tests to evaluate the signal integrity and electrical characteristics of the PCB design. This includes measuring impedance, insertion loss, return loss, and crosstalk. Use high-frequency test equipment specifically designed for measuring signals at the desired frequencies.
2. Signal Integrity Analysis: Conduct signal integrity simulations and analysis to verify that the design meets the desired electrical specifications. Use simulation tools to assess signal integrity metrics such as eye diagrams, bit error rates (BER), and jitter. This helps identify any potential signal integrity issues and allows for optimization of the design.
3. Thermal Testing: Evaluate the thermal performance of the PCB design using the Nelco N9000 substrate. Perform thermal testing to measure the temperature distribution across the board and identify hotspots. This is particularly important for designs with high-power components or applications with elevated temperatures. Use thermal imaging or thermocouples to assess thermal performance.
4. Environmental Testing: Subject the PCB design to environmental testing to ensure its performance under different conditions. This may include temperature cycling, humidity testing, thermal shock, vibration, and mechanical stress tests. These tests help validate the reliability and durability of the design when exposed to various environmental factors.
5. Mechanical Testing: Assess the mechanical strength and stability of the PCB design. Perform mechanical tests such as flexural testing, bend testing, and drop testing to ensure that the design can withstand mechanical stresses without failure or performance degradation. This is particularly important for applications that may experience physical stress or vibration.
6. Reliability Testing: Conduct reliability tests to assess the long-term performance and durability of the PCB design. This may include accelerated aging tests, such as temperature and humidity cycling, to simulate the effects of prolonged operation. Additionally, perform solderability testing and thermal cycling to evaluate the solder joint integrity and resistance to thermal stress.
7. Comparison and Compliance: Compare the measured results against the desired specifications and industry standards. Ensure that the performance of the Nelco N9000 substrate meets or exceeds the required parameters for the specific application. Compliance with relevant industry standards, such as IPC-6012 for PCB fabrication, is essential to ensure quality and reliability.
8. Design Iteration and Optimization: Analyze the test results and iterate the design if necessary. Address any performance deviations, reliability issues, or manufacturing challenges identified during testing. Optimize the design layout, stackup, or component placement to improve performance and manufacturability based on the test findings.
By conducting comprehensive testing and validation, you can verify the performance and reliability of PCB designs using the Nelco N9000 substrate. This helps ensure that the design meets the desired electrical specifications, environmental requirements, and long-term reliability expectations for high-frequency and critical microwave applications.
Applications of Nelco N9000 PCB Substrate
The Nelco N9000 PCB substrate finds extensive application across various industries and technologies. Some notable applications of the Nelco N9000 PCB substrate include:
1.Cellular Base Station Antennas:
The N9000 substrate is well-suited for the construction of high-performance antennas used in cellular base stations. Its superior electrical properties ensure efficient signal transmission and reception.
2.Wireless Communications:
The N9000 substrate is widely utilized in wireless communication systems, such as Wi-Fi routers, Bluetooth devices, and satellite communication equipment. Its low loss characteristics enable reliable and high-speed data transmission.
3.Power Amplifiers:
The N9000 substrate is an ideal choice for power amplifier circuits that require high power handling capabilities. Its excellent thermal conductivity helps dissipate heat effectively, ensuring reliable amplifier performance.
4.Dual Band Hi Power Passive Circuits:
The N9000 substrate is employed in the fabrication of dual-band passive circuits, such as filters and diplexers. Its consistent dielectric properties enable precise frequency control for dual-band operation.
5.Automotive Applications:
The N9000 substrate is suitable for automotive electronics, including radar systems, advanced driver-assistance systems (ADAS), and communication modules. Its stability over a wide temperature range and resistance to environmental factors make it reliable in automotive environments.
6.Digital/Microwave Hybrid:
The N9000 substrate is utilized in digital/microwave hybrid circuits, which combine digital and microwave components on the same PCB. Its low loss and high-frequency performance are crucial for these hybrid applications.
7.Multilayer PCB Assemblies:
The N9000 substrate is commonly used in multilayer PCB assemblies, where multiple layers of circuits are stacked together. Its high mechanical strength and dimensional stability ensure reliable fabrication and assembly processes.
8.Millimeter Wave Components:
The N9000 substrate is employed in millimeter wave applications, such as high-frequency radar systems and wireless backhaul links. Its low loss and excellent electrical properties enable reliable signal transmission at these high frequencies.
9.Telecommunications:
The N9000 substrate is utilized in various telecommunications applications, including base station equipment, satellite communication systems, and high-speed data transmission. Its low loss and high-frequency performance contribute to efficient and reliable telecommunications infrastructure.
All in all, the Nelco N9000 PCB substrate offers exceptional performance and reliability in a wide range of applications, ranging from cellular base station antennas and wireless communications to automotive electronics and millimeter wave components. Its superior electrical and mechanical properties make it a preferred choice for high-frequency and critical microwave applications.
Comparison with Other PCB Materials in RF/Microwave Circuitry
When comparing the Nelco N9000 PCB substrate with other high-frequency PCB materials, it’s important to consider various factors such as electrical performance, mechanical properties, cost, availability, and manufacturing considerations. Here’s a general comparison of the Nelco N9000 substrate with some commonly used high-frequency PCB materials:
1. Nelco N9000: The Nelco N9000 substrate is known for its low loss characteristics, superior electrical performance, and stable dielectric properties. It offers excellent signal integrity and is suitable for high-frequency applications. It also has good thermal conductivity, making it suitable for designs with high-power components. The N9000 substrate is widely available and has a competitive cost compared to other high-frequency materials.
2. Rogers RO4000 Series: Rogers RO4000 series is another popular high-frequency PCB material. It offers low dielectric loss and good high-frequency performance. The RO4000 series is available in various versions with different dielectric constants to meet specific design requirements. It has good mechanical stability and thermal performance. However, it may have a higher cost compared to the Nelco N9000 substrate.
3. Isola FR408: The Isola FR408 is a high-performance laminate material designed for high-speed digital and high-frequency applications. It offers excellent electrical properties, low loss, and good signal integrity. The FR408 substrate has a lower dielectric constant compared to the Nelco N9000, making it suitable for specific design requirements. It is widely available and has competitive pricing.
4. Taconic RF-35: The Taconic RF-35 substrate is a high-frequency material known for its low loss and stable electrical properties. It offers good signal integrity and is suitable for high-frequency applications. The RF-35 substrate has good thermal stability and is available in various thicknesses and copper weights. However, it may have a higher cost compared to the Nelco N9000.
5. Arlon 85N: Arlon 85N is a high-frequency laminate material known for its low dielectric constant and low loss tangent. It offers good electrical performance and signal integrity. The 85N substrate has good thermal stability and can handle high-power applications. It is readily available in the market but may have a higher cost compared to the Nelco N9000.
It’s important to note that the suitability of a specific PCB material depends on the specific requirements of the application and the design considerations. Factors such as frequency range, power requirements, fabrication process, and cost constraints should be taken into account when selecting the most appropriate high-frequency PCB material. Consulting with PCB material manufacturers and considering specific application requirements will help determine the best choice for a given design.
Conclusion
With its superior dielectric properties, thermal conductivity, and manufacturing compatibility, Nelco N9000 emerges as a top-notch choice for RF and microwave circuitry. Its ability to meet stringent performance requirements and industry standards makes it a reliable and efficient substrate for next-generation high-frequency applications. Incorporating Nelco N9000 in PCB designs can significantly enhance the performance and reliability of RF and microwave circuits.