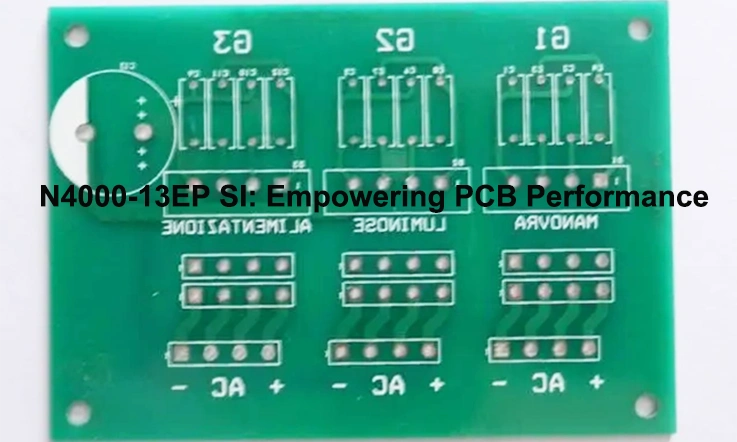
In the ever-evolving landscape of PCB manufacturing, staying at the forefront requires embracing innovative materials. Enter N4000-13EP SI, a game-changing solution that empowers circuit board manufacturers to push the boundaries of performance and efficiency. This article delves into the remarkable advantages offered by N4000-13EP SI from the perspective of PCB manufacturers, showcasing its transformative impact on product quality, manufacturing processes, and customer satisfaction.
N4000-13EP SI
N4000-13EP SI is a cutting-edge epoxy resin system specifically designed to meet the demanding lead-free requirements of modern electronics manufacturing. This advanced formulation offers superior thermal reliability along with excellent electrical performance and minimal signal loss. By incorporating SI® glass, it is particularly well-suited for applications that demand optimal signal integrity and precise impedance control. Furthermore, N4000-13EP SI exhibits exceptional resistance to Conductive Anodic Filamentation (CAF) and maintains its thermal reliability under challenging conditions. With a 94 V-0 UL rating and compliance with the IPC 4101/29 slash sheet, N4000-13EP SI ensures high-quality and reliable performance in PCB manufacturing.
Feature and Properties of N4000-13EP SI
1. Excellent Electrical Properties:
Precise thickness control for applications requiring tight tolerance impedance.
Low dielectric constant (DK) and dissipation factor (DF) for minimal signal distortion and faster signal propagation.
2. Thermal and Mechanical Properties:
Glass transition temperature (Tg) exceeding 210°C, ensuring high-temperature stability.
Low Z-axis coefficient of thermal expansion (Z-CTE) and proven resistance to Conductive Anodic Filamentation (CAF), ensuring long-term reliability for RF and digital applications.
Compatibility with lead-free assembly processes, with a maximum reflow temperature of 260°C.
Demonstrated long-term reliability.
3. Signal Integrity Option:
Incorporates SI® glass for enhanced performance in low-loss applications, ensuring optimum signal integrity.
4. Excellent CAF Performance:
Provides outstanding resistance to Conductive Anodic Filamentation (CAF), even after multiple lead-free assembly exposures.
5. High-Tg FR-4 Processing:
Utilizes the same processing parameters as N4000-13, similar to traditional high Tg FR-4 materials.
Requires a 90-minute press at 193°C and 275-350 psi for optimal performance.
What Benefits When Use N4000-13EP SI PCB Materials?
The N4000-13EP SI PCB material offers several significant benefits for PCB design and manufacturing:
1. Low Dissipation Factor (DF) and Dielectric Constant (DK):
The material exhibits low DF and DK, ensuring minimal signal distortion and improved signal integrity. This characteristic is crucial for high-frequency applications and advanced technology PCB designs.
2. Excellent Thickness Control:
The N4000-13EP SI material provides exceptional thickness control, allowing for tight tolerance requirements. This feature is essential for precise impedance matching and maintaining consistent performance across the PCB.
3. Support for Advanced Technology PWB Design:
With its superior electrical properties and signal integrity options, the N4000-13EP SI material supports the implementation of advanced technology Printed Wiring Board (PWB) designs. It enables engineers to develop high-performance PCBs capable of meeting the demands of modern electronic devices and applications.
Compare with Other Special PCB Materials
When comparing the N4000-13EP SI material with other special PCB materials, several factors should be considered:
1. Electrical Performance: Compare the electrical properties of different materials, such as dielectric constant (Dk), dissipation factor (Df), and signal loss characteristics. Higher Dk values can affect signal integrity, while lower Df values indicate better insulation properties.
2. Thermal Performance: Evaluate the thermal conductivity and coefficient of thermal expansion (CTE) of different materials. Higher thermal conductivity allows for better heat dissipation, while a similar CTE to other components reduces the risk of mechanical stress and reliability issues.
3. Mechanical Characteristics: Consider the mechanical strength, rigidity, and flexibility of the materials. Some applications require materials with high mechanical strength to withstand harsh environments or heavy components, while others may benefit from flexibility for bending or compact designs.
4. Manufacturing Compatibility: Assess the compatibility of different materials with standard PCB manufacturing processes, such as etching, plating, and soldering. Some materials may require specialized manufacturing techniques or equipment, which can impact cost and availability.
5. Cost: Compare the cost of different materials, including raw material costs, manufacturing expenses, and any additional processing requirements. Balancing performance requirements with budget constraints is crucial in material selection.
6. Application-Specific Considerations: Evaluate how each material performs in specific application scenarios. For example, high-frequency applications may require materials with low loss tangent and excellent signal integrity, while high-power applications may prioritize materials with high thermal conductivity.
7. Availability and Support: Consider the availability of the material from suppliers and the level of technical support provided. It is important to ensure a reliable supply chain and access to expertise when using specialized materials.
By considering these factors and conducting thorough research, designers can make informed decisions when comparing the N4000-13EP SI material with other special PCB materials for their specific applications.
Applications of N4000-13EP SI
The N4000-13EP SI PCB material finds extensive application in various electronic systems and infrastructure. Here are some notable applications:
1. High-Speed Storage Networks:
The exceptional electrical properties and low signal distortion of the N4000-13EP SI material make it well-suited for high-speed storage networks. It enables reliable data transmission and supports the demanding requirements of storage systems.
2. Internet Switches / Routing Systems:
N4000-13EP SI is an ideal choice for internet switches and routing systems where efficient signal propagation and minimal signal distortion are crucial. Its low dielectric constant and dissipation factor contribute to high-performance networking equipment.
3. Wireless Communication Infrastructure:
The material’s excellent electrical properties and signal integrity options make it highly suitable for wireless communication infrastructure. It enables the development of reliable and high-speed wireless communication systems, such as base stations and antennas.
4. Backplanes:
N4000-13EP SI is well-suited for backplane applications, where high-speed signal transmission and reliable performance are essential. Its low dielectric constant and dissipation factor, along with excellent thickness control, ensure optimal signal integrity and tight tolerance requirements in complex backplane designs.
In summary, the N4000-13EP SI material offers significant advantages for high-speed electronic systems, networking equipment, wireless communication infrastructure, and backplane applications, enabling reliable and efficient performance in these critical areas.
Manufacturing and Testing Considerations
Manufacturing and testing considerations play a crucial role in ensuring the successful production and reliable performance of PCBs using the N4000-13EP SI material.
Design for Manufacturing (DFM) Guidelines:
Designing a PCB with the N4000-13EP SI material requires careful consideration of manufacturing processes to ensure optimal performance and reliability. Here are some DFM guidelines to consider:
●Layer stackup: Optimize the layer arrangement to minimize signal interference and impedance mismatches. Follow industry-standard guidelines for signal, power, and ground plane allocations.
●Trace width and spacing: Design traces with appropriate width and spacing to accommodate the manufacturing capabilities and ensure consistent impedance control.
●Copper weight: Specify the appropriate copper weight for the desired current carrying capacity while considering the manufacturability and cost implications.
●Component placement: Optimize component placement to minimize signal distortion, reduce trace lengths, and facilitate efficient assembly processes.
●Vias and holes: Follow recommended via and hole sizes to ensure reliable plating and drilling processes. Consider the aspect ratio to avoid issues during fabrication.
Design for Testability (DFT) Considerations:
To facilitate efficient testing and debugging of PCBs using N4000-13EP SI, it is important to incorporate design elements that enhance testability. Consider the following DFT considerations:
●Test points: Include dedicated test points at critical nodes to enable easy access for probing and testing during manufacturing and debugging stages.
●Boundary scan: Implement boundary scan techniques (such as IEEE 1149.1) to simplify testing and diagnosis of complex circuits.
●Built-in self-test (BIST): Incorporate BIST circuitry to enable self-testing of critical components and subsystems, reducing reliance on external test equipment.
●Design for in-circuit testing (ICT): Ensure proper accessibility of test points for ICT probes to measure electrical characteristics and perform functional testing.
Manufacturing and Testing Methodologies:
Manufacturing and testing methodologies play a crucial role in ensuring the quality and reliability of PCBs using the N4000-13EP SI material. Consider the following methodologies:
●Controlled impedance testing: Perform impedance testing during manufacturing to verify the consistency and accuracy of signal traces, ensuring compliance with design specifications.
●Automated optical inspection (AOI): Utilize AOI systems to detect manufacturing defects, such as soldering issues, component misalignment, and trace discontinuities.
●Electrical testing: Conduct comprehensive electrical testing, including continuity checks, functional testing, and signal integrity analysis, to validate the performance of the PCB.
●Reliability testing: Subject the PCBs to rigorous reliability tests, such as thermal cycling, vibration, and humidity tests, to assess their durability and long-term performance.
●Statistical process control (SPC): Implement SPC techniques to monitor and control manufacturing processes, ensuring consistent quality and identifying any process variations.
By following these manufacturing and testing considerations, designers can enhance the manufacturability, testability, and overall quality of PCBs utilizing the N4000-13EP SI material, leading to reliable and high-performance electronic systems.
Conclusion
By harnessing the power of N4000-13EP SI, PCB manufacturers can unlock a new era of possibilities. Its exceptional electrical properties, thermal performance, and mechanical characteristics enable the creation of high-quality, reliable circuit boards that exceed industry standards. Embracing N4000-13EP SI empowers manufacturers to deliver superior products, optimize manufacturing processes, and forge strong partnerships with customers who demand excellence. Step into the future of PCB manufacturing with N4000-13EP SI and revolutionize your business.
I am text block. Click edit button to change this text. Lorem ipsum dolor sit amet, consectetur adipiscing elit. Ut elit tellus, luctus nec ullamcorper mattis, pulvinar dapibus leo.