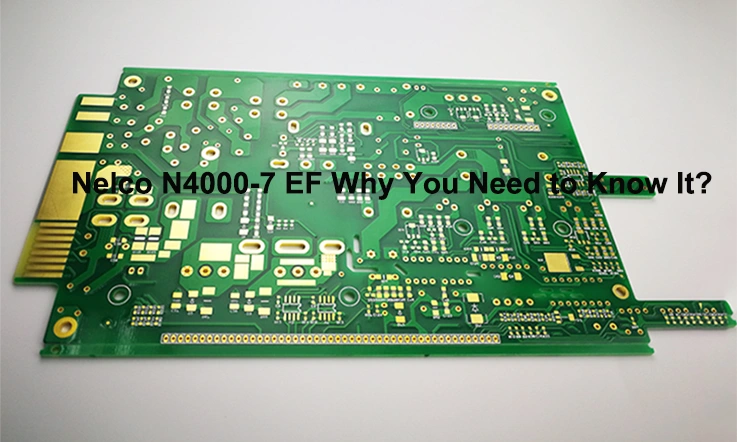
Electronic devices are pushing the limits of speed, efficiency, and reliability, and PCB materials need to keep up. Nelco N4000-7 EF, a halogen-free, low-loss epoxy laminate, has been widely adopted by manufacturers handling high-speed digital, RF, and microwave applications. Its strong thermal stability, controlled dielectric properties, and compatibility with lead-free soldering make it well-suited for industries such as telecommunications, medical electronics, and aerospace.
From multilayer stack-up optimization to ensuring EMI control, working with Nelco N4000-7 EF requires a deep understanding of material properties and processing techniques. This guide explores how this laminate compares to other high-performance options, best practices for PCB layout, and considerations for sourcing and manufacturing. Designing for 5G networks, advanced medical equipment, or aerospace applications starts with selecting the right materials and implementing effective engineering strategies.
Introduction to Nelco N4000-7 EF and Its Advantages
In PCB manufacturing, precision and reliability define success. Nelco N4000-7 EF stands out as a halogen-free epoxy laminate, designed to support high-speed signal transmission and stable performance under demanding conditions. Many industries, including 5G communications, aerospace, and medical electronics, require materials that maintain consistent electrical properties while complying with environmental regulations.
Unlike traditional laminates, Nelco N4000-7 EF offers a low dielectric constant (Dk) and low dissipation factor (Df), making it well-suited for applications that demand high-frequency operation with minimal signal loss. At the same time, its thermal stability and mechanical strength ensure long-term durability.
What is Nelco N4000-7 EF and Why Is It a Strong Option?
Nelco N4000-7 EF is a high-performance, halogen-free epoxy laminate engineered for advanced PCB applications. Built for high-frequency circuits, this material allows for low signal loss, making it suitable for telecommunications, automotive radar systems, and RF devices. Its high glass transition temperature (Tg) and excellent thermal stability help ensure reliability, even in environments with temperature fluctuations and high-power demands.
The laminate’s low Dk and Df properties allow us to design circuits with stable impedance control, reducing the risk of signal degradation. As a result, it supports high-speed data transfer, an essential feature in 5G networks, high-frequency RF applications, and next-generation computing hardware.
Beyond its electrical advantages, Nelco N4000-7 EF is also designed to comply with global environmental standards, offering a halogen-free composition that meets RoHS and REACH regulations. Some of manufacturers aiming to reduce hazardous material content while maintaining high-performance PCB fabrication often choose this material.
Key Benefits of Using Nelco N4000-7 EF in PCB Manufacturing
Selecting a PCB laminate requires careful consideration of electrical performance, thermal stability, and long-term reliability. Here’s a closer look at what Nelco N4000-7 EF brings to the table:
1. Superior Signal Transmission and Low Signal Loss-
PCB designs that operate at high frequencies demand materials with low dielectric constant and dissipation factor to maintain signal integrity. Nelco N4000-7 EF minimizes crosstalk and attenuation, ensuring precise data transmission across high-speed networks.
For instance, engineers working on 5G base stations and RF communication systems require a laminate that reduces signal loss while supporting fast data processing. Nelco N4000-7 EF fits these applications perfectly, helping to maintain consistent signal performance even as circuit complexity increases.
2. Strong Thermal and Mechanical Stability-
Applications in automotive electronics, aerospace, and industrial control systems expose PCBs to elevated temperatures and mechanical stress. Nelco N4000-7 EF, with its high Tg and low coefficient of thermal expansion (CTE), offers structural stability that prevents warping, delamination, or mechanical degradation.
For example, in electric vehicles (EVs), where battery management systems generate continuous heat, a laminate with high thermal endurance ensures that electronic components remain intact over extended operational lifetimes.
3. Environmentally Friendly and Halogen-Free Composition-
Many industries are shifting toward sustainable manufacturing by reducing halogen-based materials in PCB production. Nelco N4000-7 EF meets strict environmental compliance requirements, making it a preferred option for companies looking to build eco-conscious products.
By integrating this material into consumer electronics, telecom equipment, and industrial automation systems, we can align with global environmental policies while maintaining PCB performance and longevity.
How Nelco N4000-7 EF Compares to Other PCB Laminate Materials?
Our engineers and procurement teams often evaluate PCB laminate options based on signal performance, heat resistance, and environmental impact. Here’s how Nelco N4000-7 EF stacks up against other industry-standard materials like FR-4 and other epoxy-based laminates:
1. High-Frequency Performance-
Standard FR-4 laminates work well for general-purpose PCB applications but fall short in high-speed data transmission. Nelco N4000-7 EF provides a low-loss dielectric material, reducing signal interference and delays in RF circuits, satellite communications, and 5G network components.
Material | Dielectric Constant (Dk) @ 10 GHz | Dissipation Factor (Df) @ 10 GHz |
FR-4 Standard | ~4.5 | 0.02 – 0.03 |
Nelco N4000-7 EF | ~3.7 | 0.005 – 0.009 |
The difference in Dk and Df values allows Nelco N4000-7 EF to support higher data rates, making it a better fit for modern, high-performance PCB designs.
2. Structural Durability and Heat Resistance-
Traditional laminates like FR-4 can struggle with thermal expansion in high-power applications. Nelco N4000-7 EF offers higher Tg values, meaning it remains stable under prolonged heat exposure.
For example, automotive radar modules that function in extreme weather conditions require laminates that can handle temperature shifts without cracking or degrading over time. This material provides a strong foundation for durable PCB structures.
3. Eco-Friendly Compliance and Manufacturing Benefits-
With global regulations pushing for halogen-free PCB materials, Nelco N4000-7 EF gives manufacturers an advantage by meeting RoHS and REACH directives. Compared to conventional epoxy laminates, this material eliminates concerns about toxic byproducts during PCB fabrication and disposal.
For companies focused on building next-generation electronic devices while keeping up with environmental compliance, Nelco N4000-7 EF remains a preferred option.
Nelco N4000-7 EF Material Properties and Performance
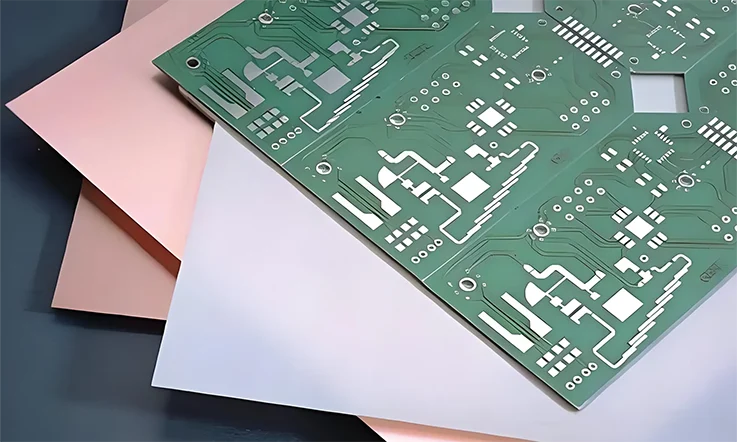
Choosing the right PCB laminate isn’t just about picking a material off the shelf—it’s about finding one that stands up to heat, electrical demands, mechanical stress, and environmental exposure. Nelco N4000-7 EF brings a halogen-free composition, stable electrical properties, and solid thermal management to the table.
Now, let’s break down its core properties and see how it performs where it matters.
Thermal and Mechanical Stability of Nelco N4000-7 EF
Circuit boards don’t live in a vacuum—they deal with temperature swings, vibrations, and mechanical loads daily. If a laminate can’t keep up, failures aren’t far behind. Nelco N4000-7 EF is designed to handle these challenges head-on.
Glass Transition Temperature (Tg) and Coefficient of Thermal Expansion (CTE)-
When temperatures rise, PCB materials soften and expand. Nelco N4000-7 EF features a Tg above 200°C, which keeps it from breaking down under high heat. This means it stays stable even in power-hungry applications like RF systems, satellite communications, and automotive electronics.
Expansion is another issue—too much of it and you’re looking at solder joint fractures or delamination. With a low CTE, Nelco N4000-7 EF reduces the risk of warping, keeping multilayer stacks and fine-pitch components firmly in place.
Durability Under Mechanical Stress-
Between flexing, shock, and constant vibration, PCBs in industrial and aerospace applications take a beating. Some laminates crack under pressure—this one doesn’t. It resists bending and holds its structure even when subjected to repeated mechanical strain.
If you’re designing for aerospace navigation systems, automotive control units, or ruggedized industrial equipment, this level of durability means fewer failures and longer-lasting performance.
For those handling high-layer-count boards, a material with low expansion rates keeps circuits where they need to be and helps solder joints hold up under thermal changes. No one wants a board warping mid-process—stability makes all the difference.
Electrical Performance: Dielectric Constant and Signal Integrity
High-speed signals don’t like surprises. When impedance shifts or signals lose strength, performance drops. Nelco N4000-7 EF is built to keep things steady across a range of frequencies, making it a reliable choice for us working on advanced electronics.
Low Dielectric Constant (Dk) for Consistent Impedance-
For RF and high-speed digital circuits, Dk dictates signal transmission speed. Nelco N4000-7 EF maintains a steady Dk, cutting down on signal distortion and keeping impedance calculations on point. That’s a solid win for 5G base stations, microwave circuits, and any setup where precise signal timing is a must.
Low Dissipation Factor (Df) for Minimal Signal Loss-
Signal loss translates to wasted power and poor performance. A low Df means signals maintain their strength instead of being converted into heat. Nelco N4000-7 EF keeps Df at a minimum, making sure signals reach their destination without unnecessary degradation.
Reliable Performance at High Frequencies-
Not all laminates handle GHz-level frequencies well—some start to drift, throwing off performance. This one holds steady, making it a strong fit for radar, satellite communications, and high-speed data transmission.
For engineers working on next-gen wireless systems, choosing a low-loss laminate can mean the difference between a circuit that performs and one that struggles under pressure.
Resistance to Moisture, Chemicals, and Harsh Environments
A PCB that can’t handle tough conditions won’t last long in real-world applications. Electronics used in aerospace, automotive, and industrial settings must deal with humidity, chemicals, and extreme temperatures. Nelco N4000-7 EF holds up where others fall short.
Low Moisture Absorption for Stable Operation-
Moisture can wreak havoc on PCB laminates, leading to electrical drift and physical degradation. This material absorbs very little moisture, keeping electrical properties steady even in humid environments. From outdoor telecom gear to industrial control systems, reliability holds strong.
Chemical Resistance for Longevity-
PCBs go through chemical baths during manufacturing and may later be exposed to harsh environments. If a material can’t withstand these conditions, degradation happens fast. Nelco N4000-7 EF resists chemical attacks, making it a solid choice for designs that require exposure to cleaning agents, flux removers, and industrial chemicals.
Handles Extreme Temperatures and Physical Stress-
Heat cycling, mechanical impact, and environmental exposure can wear down weaker materials. This laminate is built to withstand thermal shifts, vibrations, and shocks, making it well-suited for avionics, medical electronics, and heavy-duty automation.
For projects that demand a tough, long-lasting material, going with a laminate that resists moisture and chemicals is a no-brainer.
Why Nelco N4000-7 EF Stands Out for High-Speed and RF PCBs?
Designing printed circuit boards for high-frequency and high-speed applications demands materials that keep up with evolving technology. Engineers developing 5G infrastructure, IoT devices, satellite communications, and other high-performance electronics look for laminates that offer stability and reliability.
Nelco N4000-7 EF delivers consistent electrical performance, low signal loss, and well-maintained impedance, making it a preferred choice for those working on complex PCB circuit boards designs. Unlike general-purpose materials, this laminate is engineered to maintain performance under demanding conditions.
Let’s take a closer look at how Nelco N4000-7 EF meets the needs of modern high-speed applications.
Low-Loss Properties for 5G, IoT, and Telecommunications Applications
High-speed circuits require materials that support clean signal transmission without distortion. The right laminate can make a significant difference in performance, affecting everything from data rates to signal clarity.
Maintaining Signal Strength Across Long Distances-
Some PCB materials introduce losses that weaken signals as they travel, leading to distortions and delays. Nelco N4000-7 EF is designed with a low dissipation factor (Df), ensuring that high-frequency signals remain clear over extended paths.
Property | Nelco N4000-7 EF | Standard FR-4 |
Dissipation Factor (Df) | Low | High |
Signal Loss Over Distance | Minimal | Significant |
Frequency Stability | High | Inconsistent |
Supporting High-Speed Data Transmission-
As networks continue to push data rates higher, standard laminates often struggle to maintain performance. Nelco N4000-7 EF helps us design circuits capable of handling demanding data speeds without interference.
Minimizing Crosstalk in Multi-Layer Designs-
When multiple signal traces are packed into a PCB layout, interference between them can lead to performance issues. This material helps reduce unwanted coupling, keeping signal paths isolated and allowing for more predictable circuit behavior.
High-Frequency Performance Compared to FR-4 and Rogers Materials
Not all PCB laminates are engineered for high-frequency applications. FR-4 serves as an industry standard for general use, but it often introduces inconsistencies at higher frequencies. Rogers materials provide strong RF performance but come with additional costs and processing requirements.
Consistent Dielectric Properties Across Frequencies-
FR-4 is known for its variability in dielectric constant (Dk), which can lead to signal reflections and impedance mismatches. Nelco N4000-7 EF maintains stability across a wide frequency range.
Material | Dielectric Constant (Dk) | Frequency Stability | Processing Complexity |
Nelco N4000-7 EF | Stable | High | Standard |
FR-4 | Inconsistent | Low | Easy |
Rogers High-Frequency | Stable | High | Requires Adjustments |
Lower Loss Compared to Standard FR-4-
For high-frequency applications, FR-4 materials introduce higher signal loss due to their dissipation factor. Rogers laminates are often chosen to counteract this issue, but they can be costly. Nelco N4000-7 EF offers a balanced alternative, providing strong electrical performance while remaining accessible for various applications.
A Practical Option for RF Designs-
While Rogers materials have long been associated with RF performance, they often require special handling during manufacturing. Nelco N4000-7 EF offers similar advantages with better compatibility for standard PCB fabrication processes.
Ensuring Controlled Impedance with Nelco N4000-7 EF
Precision in impedance control directly affects circuit behavior, particularly in high-speed digital and RF applications. A mismatch in impedance can result in reflections, signal degradation, and reduced efficiency.
Maintaining Stable Electrical Properties-
Nelco N4000-7 EF is manufactured with strict quality controls, ensuring that its electrical characteristics remain consistent from batch to batch.
Property | Nelco N4000-7 EF | Standard FR-4 |
Impedance Variation | Low | High |
Consistency Across Batches | High | Low |
Supporting Transmission Line Designs-
Controlled impedance is a necessity for designs incorporating differential pairs, stripline, and microstrip transmission lines. This laminate provides the uniformity needed to support stable impedance levels.
Reliable Processing for Manufacturers-
When materials lack consistency, manufacturing yields can suffer. Nelco N4000-7 EF reduces these risks by providing repeatable results, allowing us to meet tight tolerances with fewer production challenges.
PCB Manufacturing Process Optimization with Nelco N4000-7 EF
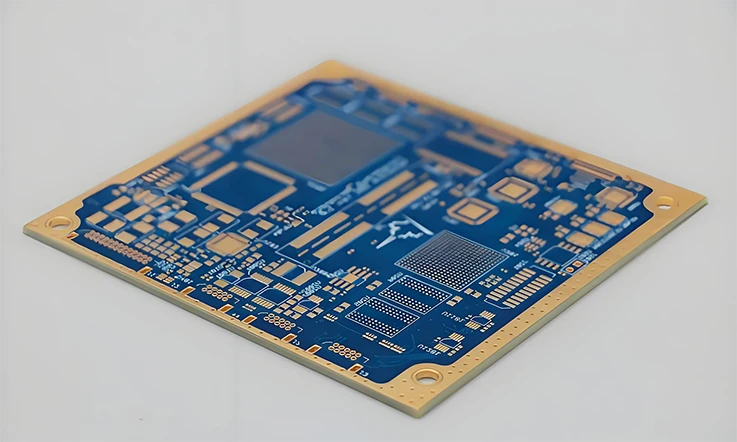
Creating high-performance printed circuit boards involves more than just selecting the right laminate—it requires fine-tuning every step of the manufacturing process. Nelco N4000-7 EF brings consistency in electrical properties, thermal stability, and environmental resistance, but achieving top-tier results depends on precise engineering choices.
From structuring multilayer stack-ups to refining drilling and plating methods, optimizing these steps ensures that circuit boards meet performance expectations. Let’s explore the factors that elevate PCB production when working with this advanced material.
Multilayer PCB Stack-Up Design for Nelco N4000-7 EF
A well-executed PCB stack-up enhances signal transmission, thermal management, and mechanical durability. We can leveraging Nelco N4000-7 EF can fine-tune dielectric placement, copper thickness, and prepreg layers to align with specific design goals.
Layer Configuration and Dielectric Precision-
The way layers are structured within a PCB influences impedance control and signal performance. Nelco N4000-7 EF provides a stable dielectric environment, ensuring predictable behavior in demanding applications.
Stack-Up Type | Dielectric Constant (Dk) | Typical Use Cases |
4-Layer (1-2-1) | Uniform across layers | Consumer Electronics |
6-Layer (1-4-1) | Maintains signal paths | Automotive Systems |
8+ Layers | Supports high-frequency routing | Telecommunications |
Copper Foil Considerations-
Copper foil selection affects conductivity, impedance control, and overall board efficiency. Using Nelco N4000-7 EF with low-profile copper reduces signal attenuation, making it a strong option for high-speed circuits.
Managing Thermal Expansion-
Materials expand and contract at different rates under heat, which can impact layer alignment during soldering. The coefficient of thermal expansion (CTE) should be carefully managed in high-layer-count PCBs to prevent warping or misalignment.
Drilling, Plating, and Etching Techniques for High-Performance PCBs
Nelco N4000-7 EF supports a range of advanced fabrication methods, but ensuring precision in drilling, plating, and etching improves both functionality and reliability.
Drilling Methods for Complex PCB Designs-
With higher layer counts and tighter tolerances, drilling precision is a major factor in maintaining connectivity across layers.
Drilling Method | Application | Benefits |
Mechanical Drilling | Standard PCBs | Cost-efficient for most applications |
Laser Drilling | Microvias, HDI | Enables smaller features and higher density |
Hybrid Drilling | Mixed designs | Balances cost and performance |
Plating for Enhanced Conductivity-
Ensuring even copper plating within vias strengthens electrical connections and improves long-term stability. The plating thickness must be carefully controlled to avoid resistance fluctuations.
Etching for Fine-Line Circuitry-
As designs become denser, controlling etching accuracy ensures that traces maintain their intended dimensions. Nelco N4000-7 EF’s material consistency supports fine-line features required for high-density layouts.
Lead-Free Soldering and Assembly Compatibility
Environmental regulations and industry trends have made lead-free soldering the standard. Nelco N4000-7 EF handles the higher temperatures required for lead-free assembly without compromising structural integrity.
Handling Higher Reflow Temperatures-
Lead-free alloys require processing temperatures that can exceed traditional tin-lead soldering. Some materials degrade under these conditions, leading to reliability concerns, but Nelco N4000-7 EF remains stable through multiple heating cycles.
Soldering Process | Peak Temperature | Effect on PCB Material |
Tin-Lead (SnPb) | ~220°C | Minimal stress |
Lead-Free SAC305 | ~245-260°C | Requires thermally stable laminate |
Minimizing Thermal Stress During Assembly-
Repeated heating and cooling cycles introduce mechanical stress within a PCB’s structure. By optimizing reflow profiles and selecting materials with compatible expansion properties, we can reduce the risk of layer separation or solder joint issues.
Ensuring Durability in Harsh Conditions-
In aerospace, automotive, and medical applications, circuit boards must endure exposure to temperature fluctuations, humidity, and harsh chemicals. Nelco N4000-7 EF, when paired with refined assembly techniques, supports designs that must withstand demanding environments.
Comparing Nelco N4000-7 EF with Other High-Performance PCB Materials
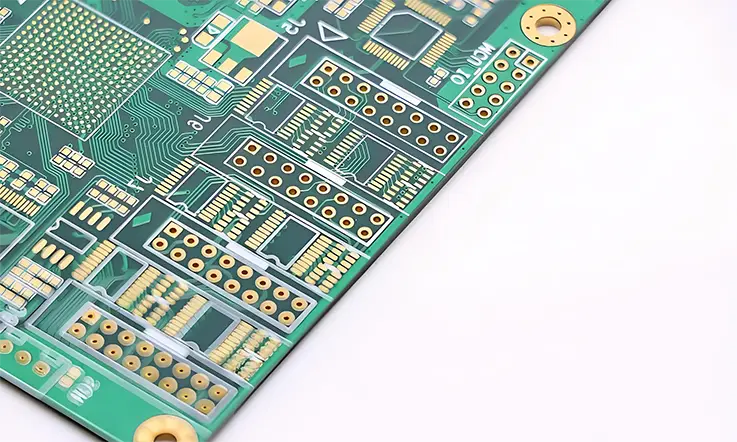
Selecting the right laminate for advanced PCB designs requires a deep dive into material properties, cost factors, and real-world application benefits. Nelco N4000-7 EF competes with well-established brands like Isola, Rogers, and Panasonic, each offering unique characteristics.
What makes Nelco N4000-7 EF a strong choice for electrical performance, streamlined manufacturing, and cost balance? Let’s dive in.
Nelco N4000-7 EF vs. Isola PCB Materials: Performance and Cost Benefits
Isola and Nelco both produce high-performance laminates, but their formulations and performance characteristics differ depending on the application.
Material Composition and Electrical Behavior-
Nelco N4000-7 EF is built on a halogen-free epoxy system with controlled dielectric properties, making it a strong option for high-speed and RF circuits. Isola, on the other hand, provides a variety of materials, including high-frequency PTFE-based substrates and epoxy blends designed for low-loss applications.
Feature | Nelco N4000-7 EF | Isola High-Speed Materials |
Dielectric Constant (Dk) | ~3.8 at 10 GHz | Varies by product (3.2-3.8) |
Dissipation Factor (Df) | ≤0.007 | Slightly higher for some epoxy-based models |
Halogen-Free | Yes | Not all products |
Processing Ease | Standard PCB fabrication | Some materials require specialized handling |
For projects that demand consistency in high-speed signal transmission without excessive cost, Nelco N4000-7 EF presents a strong alternative.
Manufacturing Flexibility-
One major advantage of Nelco N4000-7 EF is its ease of processing. Some Isola materials require unique drilling techniques or extended curing times, while Nelco laminates fit seamlessly into traditional manufacturing environments. This allows us to maintain production efficiency without investing in new processes.
Nelco N4000-7 EF vs. Rogers High-Frequency PCB Laminates
Rogers laminates dominate high-frequency applications, particularly in aerospace, satellite, and radar designs. But does that mean Nelco N4000-7 EF can’t hold its ground? Not quite.
High-Frequency Performance Breakdown-
Property | Nelco N4000-7 EF | Rogers RO4000 Series |
Dielectric Constant (Dk) | ~3.8 at 10 GHz | 3.3-3.7 (varies by model) |
Dissipation Factor (Df) | ≤0.007 | ≤0.0021 (lower loss) |
Thermal Stability | High | Excellent |
Processing Ease | Standard PCB techniques | Requires adjustments for PTFE materials |
Rogers materials offer ultra-low-loss performance for microwave and millimeter-wave designs, but Nelco N4000-7 EF provides a practical solution for engineers looking for a balance between cost and electrical performance.
Cost and Availability-
Nelco N4000-7 EF offers a more accessible price point than Rogers laminates, which are often used for niche applications. For telecommunications, high-speed networking, and computing, Nelco provides a capable solution without the additional costs associated with PTFE-based materials.
When to Choose Nelco N4000-7 EF Over Isola and Panasonic Materials?
Isola and Panasonic both offer competitive laminates, but Nelco N4000-7 EF brings unique advantages to specific applications.
Best Use Cases for Nelco N4000-7 EF-
1.High-Speed Digital and RF PCBs – The low-loss properties and controlled dielectric constant support applications such as 5G infrastructure, networking equipment, and advanced computing systems.
2.Consumer Electronics with Budget Considerations – When balancing electrical performance and cost, Nelco N4000-7 EF delivers strong results without pushing expenses too high.
3.Standard PCB Manufacturing Environments – Unlike some specialty materials that require unique processing techniques, this laminate works seamlessly within existing workflows.
4.Eco-Conscious Applications – Its halogen-free composition aligns with environmental regulations, making compliance easier.
For engineers working with ultra-high-frequency applications, Rogers laminates still lead the pack. Isola remains an option for those needing specific dielectric properties. However, for many high-speed digital and RF applications, Nelco N4000-7 EF serves as a dependable choice that balances performance, cost, and ease of fabrication.
Signal Integrity and EMI Control with Nelco N4000-7 EF
High-frequency PCB designs require more than just a well-planned layout—material selection plays a massive role in keeping signals clean and interference at bay. Poor choices can lead to signal degradation, unintended crosstalk, and electromagnetic interference (EMI) that disrupts system performance.
Nelco N4000-7 EF provides a solution for us aiming to enhance signal transmission while minimizing unwanted electrical noise. Its stable dielectric properties and low-loss characteristics make it a reliable choice for high-speed digital and RF applications. Let’s explore how this material helps tackle signal integrity and EMI challenges.
How Nelco N4000-7 EF Reduces Signal Loss and Crosstalk?
Signal degradation and crosstalk can wreak havoc on high-speed PCB designs, leading to timing errors, data corruption, and reduced system efficiency. These issues often arise from material properties, poor trace routing, and inadequate isolation between signal paths.
One of the main contributors to signal loss is excessive attenuation caused by the PCB laminate itself. Nelco N4000-7 EF is designed with a low dissipation factor, meaning that signals travel through traces with minimal energy loss. This allows for cleaner transmission over longer distances, which is especially useful in applications like 5G infrastructure and high-performance computing.
Crosstalk, the unwanted coupling of signals between adjacent traces, is another issue that can compromise data integrity. With a well-controlled dielectric constant and predictable electrical properties, Nelco N4000-7 EF helps maintain proper impedance, reducing the chances of unwanted interference. We can further minimize crosstalk by optimizing trace spacing, incorporating ground planes, and using differential pair routing where necessary.
Designing PCBs with Nelco N4000-7 EF for High-Speed Digital Applications
For high-speed digital circuits, maintaining signal quality from the source to the destination is a top priority. Even slight impedance mismatches or variations in material properties can introduce reflections and distortions, affecting overall performance.
Nelco N4000-7 EF provides a consistent dielectric constant, allowing us to design transmission lines with predictable impedance. This stability makes it easier to match trace widths, layer thicknesses, and spacing to achieve controlled impedance, reducing signal reflections and ensuring cleaner waveforms.
A carefully structured PCB stack-up directly affects performance. Designers using Nelco N4000-7 EF should consider approaches such as:
●Placing signal layers adjacent to ground planes to control impedance and reduce noise
●Using symmetrical stack-ups to maintain consistency across the board
●Selecting appropriate core and prepreg combinations to fine-tune electrical behavior
These techniques, combined with the material’s low-loss characteristics, help high-speed signals travel with greater accuracy and less distortion.
The Role of Dielectric Constant Stability in EMI Reduction
Electromagnetic interference (EMI) can lead to unpredictable system behavior, signal corruption, and compliance failures. Managing EMI requires careful material selection and design optimization to minimize unwanted radiation and external noise coupling.
Nelco N4000-7 EF maintains a stable dielectric constant across frequency ranges, which helps prevent signal reflections that contribute to EMI. Sudden shifts in dielectric properties can create impedance mismatches, leading to unintended emissions that cause interference with nearby circuits. The material’s ability to provide consistent electrical performance allows us to control emissions more effectively.
To further reduce EMI, engineers can:
●Route high-speed signals on internal layers to shield them with surrounding ground planes
●Keep return paths short and direct to avoid large current loops
●Optimize via transitions to prevent impedance discontinuities
By combining these design strategies with a material that offers stable electrical behavior, we can build systems that meet electromagnetic compliance standards while maintaining signal integrity.
How to Design for Optimizing Nelco N4000-7 EF in PCB Layout?
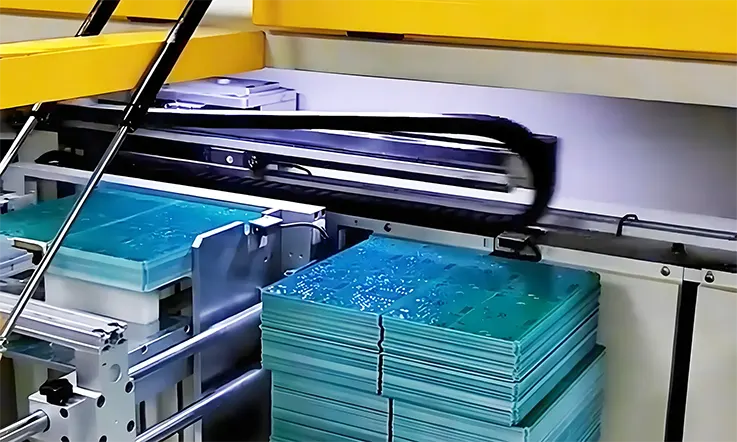
Designing a PCB with Nelco N4000-7 EF requires careful planning to make the most of its electrical properties and mechanical stability. The overall performance of the board depends on how well routing strategies, stack-up configurations, and thermal management techniques are applied.
Nelco N4000-7 EF has been widely adopted for high-speed digital and RF applications due to its low-loss characteristics and high-frequency stability. To fully harness these benefits, we must refine signal routing, select appropriate layer arrangements, and implement effective thermal control methods.
Best Practices for Routing High-Speed Signals on Nelco N4000-7 EF PCBs
The way signals are routed across a PCB determines how efficiently they travel without interference or distortion. Even minor layout missteps can introduce noise, reflections, and losses that negatively affect performance.
To enhance signal integrity, consider the following techniques:
●Keeping traces as short as possible: Reducing the distance a signal must travel helps minimize resistive losses and propagation delays.
●Maintaining consistent impedance: Uniform trace width, spacing, and reference plane configurations ensure that signals move predictably through the board.
●Using differential pairs when applicable: Many high-speed signals benefit from differential routing, which helps counteract noise and maintain clean waveforms. Proper spacing between these traces prevents phase shifts.
●Avoiding abrupt transitions: Sharp bends and sudden changes in trace width create impedance mismatches, leading to signal reflections. Smooth routing and properly tuned vias improve signal flow.
●Shielding sensitive traces: Placing high-speed signals next to solid ground planes or using guard traces helps reduce electromagnetic interference (EMI) and crosstalk.
A well-routed PCB prevents unnecessary signal degradation and allows high-frequency designs to function as intended.
Stack-Up Configurations to Maximize Nelco N4000-7 EF Performance
Choosing the right stack-up arrangement directly impacts impedance control, EMI shielding, and overall electrical stability. A well-balanced layer structure helps maintain consistency across the entire board while improving manufacturability.
For best results, consider these principles when designing the stack-up:
●Keeping the stack symmetrical: A balanced arrangement minimizes stress during fabrication, reducing the risk of board warping.
●Placing signal layers next to ground or power planes: This setup enhances return path integrity and lowers electromagnetic emissions.
●Adjusting dielectric thickness carefully: The spacing between layers must be optimized to maintain controlled impedance and minimize insertion loss.
●Avoiding signal layers that cross gaps in reference planes: Disruptions in the return path can cause noise issues and degrade signal quality.
Managing Thermal Dissipation for Reliable Operation
Heat buildup is a common challenge in high-performance electronics, especially in RF and high-speed digital applications. While Nelco N4000-7 EF is designed to handle elevated temperatures, proper PCB layout strategies help distribute heat efficiently and prevent localized hotspots.
Effective thermal management methods include:
●Incorporating thermal vias: Placing vias near heat-generating components allows heat to transfer through multiple layers, preventing excessive buildup in one area.
●Using copper pours and heat spreaders: Large copper areas in power and ground layers help distribute heat more evenly.
●Positioning components for better airflow: Keeping high-power parts spaced out and aligned with airflow paths improves heat dissipation.
●Avoiding excessive component clustering: When multiple heat-generating elements are placed too close together, it becomes harder to manage temperature effectively.
By addressing thermal concerns in the design phase, operational stability can be improved, and the lifespan of the board and its components can be extended.
FAQ: Nelco N4000-7 EF
1.Is Nelco N4000-7 EF compatible with high-density interconnect (HDI) PCBs?
Yes, its low dielectric loss and thermal stability make it suitable for HDI designs with fine-pitch components.
2.Does Nelco N4000-7 EF require special storage conditions?
It should be stored in a controlled environment with low humidity to maintain material integrity before processing.
3.What are the recommended lamination cycles for Nelco N4000-7 EF?
It follows a standard multi-stage lamination process with controlled heat and pressure to prevent resin voids.
4.How does Nelco N4000-7 EF perform under extreme mechanical stress?
It offers high flexural strength and impact resistance, making it reliable for applications that face mechanical strain.
5.Can Nelco N4000-7 EF be used for mixed-material stack-ups?
It can be integrated with other laminates, but dielectric compatibility should be considered for signal integrity.